During 2007 and the first half of 2008 as commodity markets hit their peaks, recyclers were struggling to find ways to ship affordably as the high demand for trucks and railcars drove freight prices upward. That scenario has changed radically, as have costs for transportation.
One potential lesson to take away from the peaks and valleys of 2008, however, is that recyclers who have flexibility in their transportation methods are at an advantage in any market.
Adding a rail spur can provide recycling facilities with an alternative mode of transportation when commodity markets rebound and demand for trucks tightens. Additionally, for recyclers who have seen a nearby consumer idle or shut down, adding a rail spur might provide a cost-conscious means of serving markets outside of their traditional shipping radius.
GAINING AN EDGE
According to the Association for American Railroads’ Web site, www.aar.org, major freight railroads can move a ton of freight an average of 436 miles on each gallon of fuel. Additionally, the typical rail car can hold four times as much freight as the average truck. As a result, as the distance between recycling facilities and consumers increases, the incentive to ship freight via rail also increases because it is a more cost-effective solution than trucking.
"You can move one rail car a lot further at a cheaper freight rate than you can trying to move four trucks that same distance," says Phil Bedwell, corporate manager of rail and barge transportation for OmniSource Corp., Fort Wayne, Ind. "So you have that competitive edge in cost of transportation."
Having an on-site rail spur at a recycling facility can help further reduce costs by eliminating the middleman needed to transport freight from the facility to the rail cars.
"If we had to load material on trucks to transport it to a remote rail loading site, the handling cost would become too great, so having our own spur is critical to our marketing strategy," says Michael Potash, engineer for Sioux City Compressed Steel, Sioux City, Iowa.
Administrative advantages can be gained by adding and maintaining a rail spur, some of which can be overlooked. As Bedwell notes, some customers prefer to receive freight by truck, while others prefer rail, and being versatile is critical to being successful. Additionally, transporting freight using a rail spur vs. trucking can cut the amount of administrative paperwork by up to 25 percent.
"If you’re loading four trucks, you’ve got four scales in, four scales out, four invoices, four freight bills; it multiplies," says Bedwell. "Versus one rail car, one way in, one way out and one invoice; it’s just simpler," he says.
For scrap metal recyclers trying to stay ahead of the curve, having a rail spur on site may be even more critical in the future as fuel concerns rise. Steel mills are relying on rail as a foremost method of transportation at an increasing rate. Bedwell says that 95 percent of the large steel mills in the United States use rail as their primary method of receiving freight.
Finally, installing a rail spur is by some calculations more environmentally friendly than moving freight by truck, a significant factor considering the companies are in the recycling business.
"There are environmental advantages to shipping by rail: less fuel consumption and fewer emissions of greenhouse gases and other pollutants, including nitrogen oxide and particulate matter," says Tom White, spokesman for the Association of American Railroads, Washington, D.C.
While installing a rail spur may be a good investment for scrap companies (ferrous scrap yards in particular), it may not be as cost effective for other commodities, even in the same region where using rail is beneficial to scrap metal recyclers.
Scott Rogers, president of Cedar Poly LLC, Stanwood, Iowa, says plastic and paper recyclers cannot achieve the same savings shipping via rail that metal recyclers in his region can because scrap metal is a heavier and rougher material than the commodities his facility ships.
Rogers says a rail spur will most benefit companies that are hauling relatively heavy loads long distances. "Really, here in Iowa, the railroad has not been that effective for us because we’re close to Wisconsin, and there are a lot of paper mills up there."
Rogers adds that the rail spur has been more effective for shipping heavier commodities, such as coated book. Despite having a rail spur, his facility leans heavily on trucking as its primary method of moving freight, he notes.
While long-term benefits can be achieved by installing a rail spur, business owners would be wise to evaluate whether the potential payoffs justify the costs of installation and maintenance.
JUSTIFYING THE COST
Start-up costs for installing a rail spur can be rather expensive, and it is pivotal for recyclers to calculate the time line for any return on their investments.
One key factor for recyclers to consider when estimating the installation costs is whether the rail workers installing the track are unionized. Unionized railroad workers may charge up to $110 per foot, while non-unionized rates can dip as low as $80 per foot, according to Bedwell, who notes that the average installation of a rail spur at his 52 facilities nationwide is in the mid- to upper $80-per-foot range.
"Those figures are all inclusive. That includes the ground prep, stone, ties, rail and labor," says Bedwell. He adds that installing a switch or turnout may cost an additional $45,000 to $80,000.
In contrast, Potash reports that Sioux City Compressed Steel installed its rail spur in 1998 when the company was building its scrap yard, at an all-inclusive cost-per-foot rate. Sioux City’s spur cost $140 per foot for a siding of approximately 1,100 feet of rail, which included a switch and turnout, a derail section, two crossings and the labor to install a rail scale, according to Potash.
Time frames to install a rail spur may vary drastically depending on the weather, landscape and gaining approval from the railroads, local governments and utility companies. Potash says Sioux City’s spur was installed in about a month after nearly a year of planning and securing approvals, while Bedwell has seen the installation process extend anywhere from three weeks to eight or nine months, depending upon the approval process.
"You may have to gain approval for the operation from serving railroads, local and state governments, electrical companies, water companies and neighborhoods," says Bedwell. "It’s not just one-stop shopping anymore; you have to put some time and effort into it."
Once installed, aside from start-up costs, rail spur expenses are minimal. Recyclers report that there are no fees for the facilities to maintain access to the railroad and that maintenance costs are low.
"It requires very little maintenance really. We might just have to repair a railroad tie here and there," says Roland Fisher, general manager for R J Recycling, which has a rail spur at each of its three West Virginia facilities.
Sponsored Content
Labor that Works
With 25 years of experience, Leadpoint delivers cost-effective workforce solutions tailored to your needs. We handle the recruiting, hiring, training, and onboarding to deliver stable, productive, and safety-focused teams. Our commitment to safety and quality ensures peace of mind with a reliable workforce that helps you achieve your goals.
Sponsored Content
Labor that Works
With 25 years of experience, Leadpoint delivers cost-effective workforce solutions tailored to your needs. We handle the recruiting, hiring, training, and onboarding to deliver stable, productive, and safety-focused teams. Our commitment to safety and quality ensures peace of mind with a reliable workforce that helps you achieve your goals.
Sponsored Content
Labor that Works
With 25 years of experience, Leadpoint delivers cost-effective workforce solutions tailored to your needs. We handle the recruiting, hiring, training, and onboarding to deliver stable, productive, and safety-focused teams. Our commitment to safety and quality ensures peace of mind with a reliable workforce that helps you achieve your goals.
Sponsored Content
Labor that Works
With 25 years of experience, Leadpoint delivers cost-effective workforce solutions tailored to your needs. We handle the recruiting, hiring, training, and onboarding to deliver stable, productive, and safety-focused teams. Our commitment to safety and quality ensures peace of mind with a reliable workforce that helps you achieve your goals.
Sponsored Content
Labor that Works
With 25 years of experience, Leadpoint delivers cost-effective workforce solutions tailored to your needs. We handle the recruiting, hiring, training, and onboarding to deliver stable, productive, and safety-focused teams. Our commitment to safety and quality ensures peace of mind with a reliable workforce that helps you achieve your goals.
Additionally, recyclers need not invest in expensive equipment to spot and move rail cars after installing a spur, as tools they already have at their disposal are usually adequate. Cedar Poly uses a tractor to move cars, while loaders and material handlers do the job for R J Recycling. Sioux City Compressed Steel used to have a Trackmobile, but determined a loader was sufficient for the minor shifting of cars for loading and scaling purposes, says Potash. He adds that the railroad enters the yard for all of the switching and placement of the cars.
Because his facilities are so dependent on the railroad system, Bedwell says OmniSource invests more money in the equipment needed to move rail cars.
"Most people just run up and put a bucket against it, but then you’re slicing into the sides or posts," he says. "We’ve got Trackmobiles and locomotives to move our cars around."
With low maintenance and equipment costs after installation, car availability is among the chief concerns for facilities using rail spurs. For recyclers, this issue often serves as a Catch-22. As the prices for commodities were soaring during much of the past year, the demand for containers was also soaring, causing rail car shortages across the board. Now that the market has taken a downward shift, recyclers still find themselves in a tricky situation.
"When the demand for containers is down, you could probably get a better freight rate by rail, but there’s no place to go with your paper. If the paper market was still hot and containers were down, it would be excellent. It’s unfortunate because it goes hand-in-hand with the economy," says Rogers.
SEEING A RETURN
Even with the fluctuating demand for rail cars, because of low maintenance and equipment costs after installation, most recyclers using rail spurs immediately see a return on their investments. Potash says his facility handles between five and 20 rail cars during a typical week, depending on the market, while Bedwell says OmniSource’s facilities transport 70 percent of the company’s total freight on the tracks. OmniSource’s facilities have a broad range of rail spur utilization, with some facilities handling 30 to 40 cars per day, and others handling only two or three per week.
Given that rail spurs provide transportation options when the demand for commodities is high and enable their facilities to expand their market reach, Bedwell and Potash say they consider their rail spurs valuable additions to their facilities.
"Without installing the track, we would have eliminated markets for about one-fourth to one-half of our sales," Potash says. "We need the railroads to sustain our level of business."
The author is an editorial intern for the Recycling Today Media Group.
Get curated news on YOUR industry.
Enter your email to receive our newsletters.
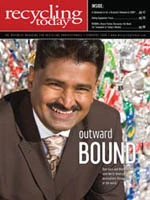
Explore the February 2009 Issue
Check out more from this issue and find your next story to read.
Latest from Recycling Today
- AF&PA report shows decrease in packaging paper shipments
- GreenMantra names new CEO
- Agilyx says Styrenyx technology reduces carbon footprint in styrene production
- SABIC’s Trucircle PE used for greenhouse roofing
- Hydro to add wire rod casthouse in Norway
- Hindalco to invest in copper, aluminum business in India
- Recycled steel price crosses $500 per ton threshold
- Smithers report looks at PCR plastic’s near-term prospects