
Sustainability: The ability to be maintained at a given rate or level; avoidance of the depletion of natural resources to maintain an ecological balance.
By definition, sustainable plastics should be managed within a sustainable materials management system or circular economy that avoids creating waste, toxins and pollutants. Unlike a linear economy that takes resources, makes products, uses these products and disposes of them, creating waste, material in the circular economy is collected and reused after each use.
Plastic producers place heavy emphasis on a product’s ability to be reused at the end of its life as they transition toward a more sustainable, eco-friendly position within the broader circular economy. However, an often-overlooked opportunity for reuse comes within the production of the product itself via in-plant recycling or reclamation of production scrap. Creating and implementing a reclamation program can help a producer become more sustainable and often can be a cost-effective, profitable endeavor.
But an in-plant recycling or reclamation operation is a large undertaking that requires significant analysis to determine if it is a fit for the organization and production process. Producers must understand the type of scrap produced and the economics behind such a program. They also must identify and form an implementation plan for the reclamation of production scrap and its reintroduction into the production process.
Understanding, defining production scrap
Production scrap comes in all forms, shapes and sizes. Some can be reclaimed online, offline or not at all.
In the cases of blown or cast film and sheet, startup purge, trims, bad rolls and loose products should be reclaimed. Blow- and injection-molded scrap, such as flash, sprues, runners and whole or cut-down parts, should be reprocessed. Other processes, such as compounding and fiber extrusion, also produce considerable production scrap.

Producers often can reclaim production scrap directly online, known as direct scrap reclaim. For film and sheet, edge trim can be processed and fed directly back to the extrusion line. In blow and injection molding, scrap such as flash, trimmings and runners can be granulated beside the machine and fed directly back to the process. Producers must handle production scrap offline for all other processes, such as pipe and profile, compounding and fiber extrusion.
Processors that still need to develop their internal recycling capabilities typically are left with three choices when dealing with their scrap: disposal, resale or toll processing. Disposal is the last resort before incineration, where the scrap can be used as fuel to recover its British thermal unit, or Btu, value. Disposal is the only option for scrap that cannot be reused or converted to energy. Often, size reduction and compaction are used to prepare the material for efficient transport and disposal, which can be critical for cost-effective operations.
Economics and decision-making for in-house scrap reprocessing
The first step is to evaluate the economics of the current production scrap handling process. You then can calculate the potential savings per year to substitute the current handling methods, including disposal, resale or toll processing. After calculating potential savings, you can compare them against the costs associated with an internal scrap reclamation operation, including any process modifications.
To understand the true economics and cost of disposal, you must calculate real and ecological factors. The cost calculation should consider factors such as the carbon footprint from transporting the waste as well as landfill tipping fees. If you plan to sell the scrap, you must calculate the net profit from the resale, considering costs such as marketing, administration, storage and logistics. These costs can offset a considerable amount of the price per pound received from selling the scrap. When determining an accurate cost analysis for toll processing, producers also must consider additional factors, such as the implications of quality control and material loss.
Once a complete cost profile is established for the current methods used to handle your production scrap, you can calculate potential cost savings per year to substitute your scrap’s disposal, resale or toll processing with in-house processing.
It’s important to evaluate the production process to determine the potential reuse of reclaimed materials. You can collect much of the necessary information by running trials on your processing line using reclaimed materials. Identify any detrimental effects that reclaimed materials have in the process, such as reduced output or automation and product quality issues, and study the impact of different reclamation forms, such as regrind, densified particles or repelletized material. Process modifications needed to optimize reclaim use need to be determined, as well as the costs associated with their implementation.
After identifying the ideal form or forms of the reclaimed material for reintroduction and any process changes needed to accommodate them, you can begin looking at different processes to recover the material.
Once you have decided on the correct processes to convert scrap into the desired form for reprocessing, you can determine the associated costs. Calculate the potential savings per pound of material recovered. Based on the process limitations of your production lines, the maximum percentage of reclaimed material introduction should be established, thereby indicating the potential material savings per year.
The final step is to calculate the cost for an internal scrap reclamation operation; this includes the capital equipment and operational cost per pound for the reprocessing line. With this information, you can compare the estimated cost savings per pound and factor in the amount of scrap that can be reprocessed for a projected payback.
Armed with this information, you can prepare the business plan for upper management to evaluate and make a tentative decision on whether to move forward with the project.
Detailed evaluation for introducing reclaimed material
With the initial cost analysis and justification completed and management’s OK to move forward, you are ready to dive into the implementation details. Transportation and storage of reprocessed material is the first consideration, knowing regrind materials and densified scrap handle differently than pellets.
All standard options—gaylord boxes, super sacks, hoppers/bins and silos—are available. Your material conveying systems, however, must be analyzed for these reprocessed material forms, including material line sizes, dust collection systems and material holding bins. If you repelletize material, storage and transportation equipment typically can be used as is.


Blending and feeding systems need to be evaluated. While you can use existing systems to introduce reclaimed material in most circumstances, blending and feeding equipment might need to be added or modified to accept the new material stream.
The most complicated step is identifying and implementing any modifications needed to the production process for making your end products. The extruder and/or extruder screw might need modification to accept higher levels of reclaimed material. Nonpelletized reclaimed materials could require a larger feed section, deeper metering flights and improved venting. Melt pumps also can be incorporated into the process. Mixing sections or static mixers can be added to the extruder to improve melt homogenization. Upgraded melt filtration could be required to handle increased material contamination arising from using reclaimed materials. Gauge measurement and control could need to be upgraded or added to better monitor the product’s overall dimensions.
Despite best efforts, reprocessed material can negatively impact end products. Viscosity loss, gel formation and color degradation can result, as well as loss of mechanical properties. Process output and stability issues can lead to loss of production and gauge control. Contamination and visual imperfections also could be unavoidable. Though the market insists on products manufactured with reclaimed content, the producer also must maintain the highest possible level of aesthetics and performance, so, identifying potential adverse effects on the final product early on and implementing solutions to offset them are critical.
Processes for reclaiming production scrap
A critical first step in any reclamation process is size reduction. A preshredder might be required for proper sortation, inspection and separation of foreign materials. A second size-reduction step, or reshred, might be needed for further material processing for either densification or repelletizing. Further size reduction also could be required to granulate the product to a processable size or even to pulverize it to return materials to their original powdered or granulated form.
Complex material streams, even postconsumer streams, could require sorting for color and polymer type. Contamination removal is a critical last step and often includes ferrous and nonferrous metal removal and soft contamination removal by wash systems, including wet and dry-cleaning operations.
If the recovered material cannot be used in a simple regrind form, either densification or pelletizing must be incorporated. The extrusion process can include traditional single-screw extruders, twin-screw compounding extruders or specialized recycling extruders.
Pelletizing can be done either by “strand,” using a bath or water slide, or “die face,” either air- or water-cooled. Techniques are available to help preserve polymer properties during the recovery process, including viscosity recovery, to boost color, remove odor and improve mechanical properties.
Future considerations
There’s a lot to think about when you want to go green and move toward a more sustainable, circular production process, considering ecological and economic factors must be addressed. Consider hiring a sustainability manager responsible for looking into all aspects of production to minimize waste. As your internal recycling capabilities grow, you also can consider bringing in other producers’ production scrap as well as postconsumer scrap to supplement your own.
Grow your sustainability program into a profitable business unit your competitors will admire and lead the way toward the ultimate goal of zero waste.
Get curated news on YOUR industry.
Enter your email to receive our newsletters.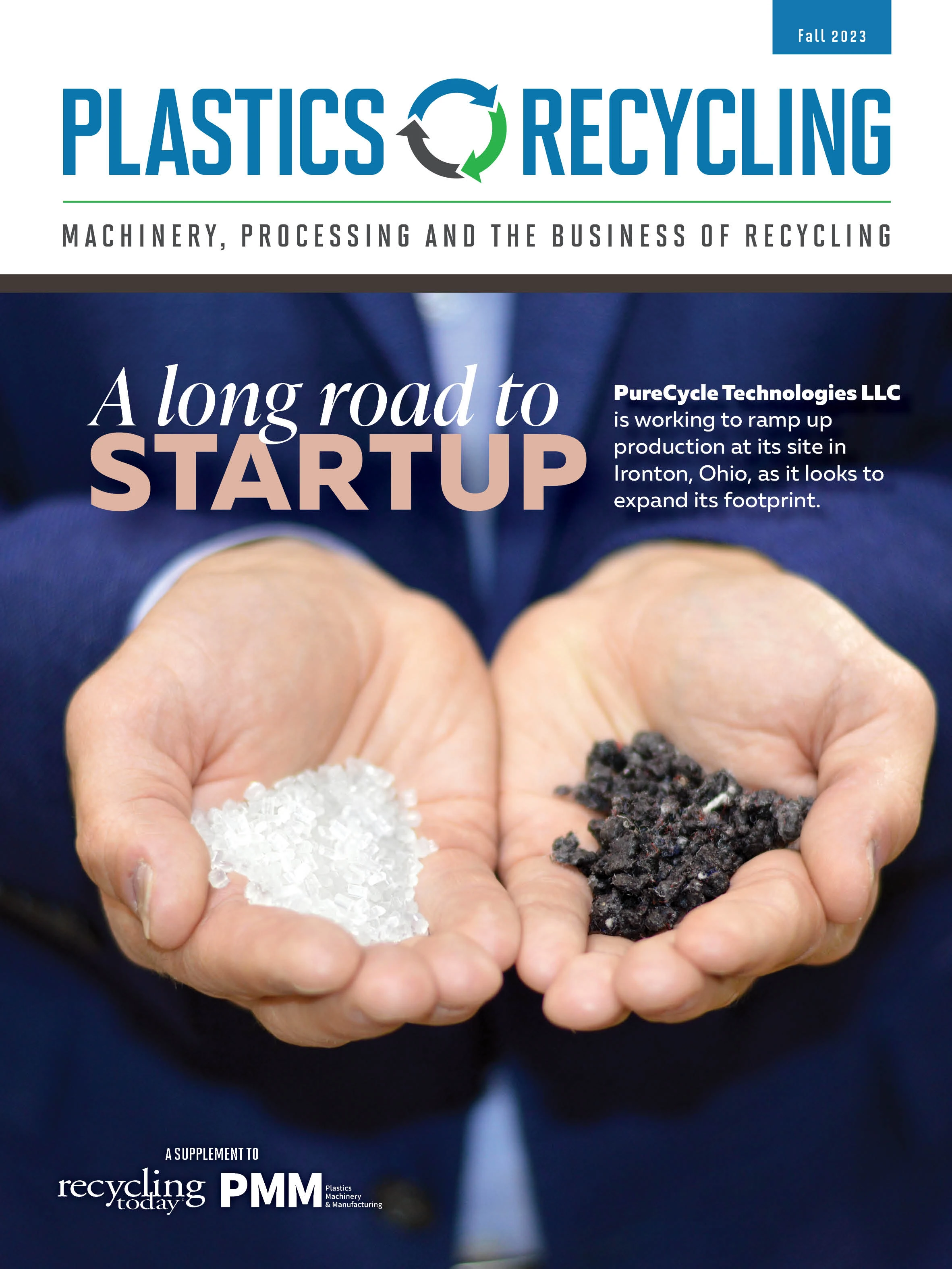
Explore the Fall 2023 Plastics Recycling Issue
Check out more from this issue and find your next story to read.
Latest from Recycling Today
- Copper exempted from latest round of tariffs
- Interchange Recycling's EPR stewardship plan approved in Yukon
- Making the case for polycoated paper recovery
- Novolex, Pactiv Evergreen finalize merger
- In memoriam: Danny Rifkin
- BIR adds to communications team
- Greenwave asks for SEC filing extension
- EU levies ELV recycling fines against 15 automakers