Recycled roofing shingles can make an ideal ingredient in hot mix asphalt pavements.
Unless you have been living in a cave for the last 20 years, you are aware that the U.S. has a significant landfill overfill problem. It’s hard to believe, but the statistics show that as a nation, we generate more than four billion tons of solid waste per year – that’s about 14 tons per capita.
It doesn’t seem to me that I carry that much to the curb each year. Few of us really appreciate the magnitude of the overall problem, as we see so little of the non-household waste. About 90 percent of the total waste stream is from the agricultural and mining/mineral industries, with the remaining 10 percent from domestic and industrial sources.
With landfills reaching and exceeding capacity in many areas, tipping fees have become very high, particularly in urban areas. In addition, many waste materials are found to be unacceptable in landfills. So other disposal and re-use options are being considered for many materials.
PAVEMENT AS A MARKET
The hot mix asphalt industry has been a long supporter of recycling. Recycling began on a large scale in the 1970s with the use of reclaimed asphalt pavement (RAP) and has grown ever since. From the beginning, the issues for the hot mix asphalt (HMA) industry have been to ensure the engineering, economic and environmental viability of the finished product. The National Asphalt Pavement Association (NAPA), Lanham, Md., outlined these issues in detail in a special report prepared in 1993.
Clearly, the asphalt pavement industry does not want its product to become a linear landfill. However, there certainly are synergies from which advantage can be derived that do not in any way minimize the quality and performance of the HMA pavement. Based on performance to date, the use of asphalt roofing shingles appears to fit into that category. This paper will review the use of these waste shingles in HMA.
About 90 million squares of asphalt shingles are manufactured each year – about two-thirds goes to re-roofing and the other third to new construction, according to NAPA.
The re-roofing generates six to seven million tons of waste that needs to find a home. Add this to the five percent to 10 percent manufacturing waste that the shingle producers have, and you quickly see that there is a very large supply of waste shingles that potentially could be available. Like any other material that is used in a manufacturing process, the prevalent issues are quality, quantity, consistency and price.
Manufacturing Waste vs. Tear-Offs
Let’s start with a discussion of the supply of materials. The two main supply sources are manufacturing wastes and tear-offs (from the re-roofing process). In both cases, the HMA producer should expect to receive a tipping fee to defray handling costs.
Manufacturing wastes generally have less contamination and a relatively stable supply history. Clearly, the location for use of the shingle waste must be fairly close to the manufacturing facility to make the application economically attractive. HMA producers work with the supplier to develop a mutually beneficial relationship.
Tear-off shingles present some interesting issues that need to be addressed by the HMA contractor. Often the company tearing off the shingles does not segregate the shingles from other construction waste, and the supply of shingles becomes "guts, feathers and all." This is an entirely unacceptable situation for the HMA producer. There is, however, a huge supply opportunity for tear-offs in any reasonably sized urban area. The use of tear-offs also can be used as positive public relations by the HMA producer, by noting that the industry is helping to solve society’s solid waste management problem.
It’s interesting to note that many companies using manufacturing wastes don’t understand why anyone would use tear-offs and vice versa. Both types of material can and do work well.
References and Background |
The following reports were used as background references by the author, and in some cases can be obtained by the publishing organizations: • “A Study of the Use of Recycled Paving Material – Report to Congress,” joint report FHWA-RD-93-147 and EPA/600/R-93/095, June 1993. • Decker, Dale S., “Evaluating the Use of Waste Materials in Hot Mix Asphalt,” Special Report 165, National Asphalt Pavement Association, 1993. • “Uses of Waste Asphalt Shingles in HMA: State-of-the-Practice,” Special Report 179, National Asphalt Pavement Association, 1997. |
COMPOSITION AND HMA DESIGN
Shingles are composed of asphalt, sand and fiber, all products that are routinely added to HMA. The asphalt content of the shingle ranges from about 25 percent to 40 percent of an asphalt material much harder than is normally used in HMA.
Just like any other material that is added to HMA, it is important to know the physical properties of the shingles that are to be added. In order to be acceptable to the HMA producer, the shingles must in no way reduce the quality of the final product.
Shingles are typically added to the HMA at five percent to 10 percent by weight. The shingles are reduced to minus one half-inch particle size and the physical properties of the shingles are determined. Typically the asphalt content, specific gravity and gradation of the sand are determined.
The asphalt content of the shingle can be determined using the asphalt ignition oven developed by the National Center for Asphalt Technology, Auburn, Ala. In order to maintain a safe oven operation, it probably will be necessary to reduce the sample size because of the high asphalt content in the shingles.
Because of the hardness of the asphalt in the shingles, generally a softer grade of asphalt cement is used in a mix with shingles than would be used in a mix with all virgin materials.
PROCESSING CONSIDERATIONS
While there may be other approaches, the author has been exposed to two different approaches to shredding shingles. The first involves the use of a conventional milling hea, and the second uses "anvils." Both approaches will produce a shredded shingle product that can be used in HMA. Both systems also have significant wear issues. Neither the milling heads nor the anvils like stones in the product. They are not intended to be crushers.
The anvil system appears to minimize oversized material better than the milling head, so a lower percentage of reject material may be created with the anvil system. The shredder production is dependent on the type of shredder and the logistics of the operation but will range from about 25 to 100 tons per hour.
It is very important that no rock product becomes intermingled with the waste shingles. This is true regardless of the type of shredder. Getting stone products into the system will decrease shredder life and efficiency, increase cost of operations, decrease efficiency of operations and reduce the consistency of the final product. It can’t be said enough: Keep the stockpiles clean!
Many contractors have found it helpful to build a working platform. This would begin by blading the surface to solid material. Then a bed of either shingles or RAP is placed on which to build the shingle stockpile. This working platform will assist to minimize contamination of shingles into the shredder.
Grapple hooks appear to be the best method of feeding the shingles into the shredder. This approach minimizes contamination because the operator can physically see what he’s feeding into the shredder. The grapple hook also offers good feed control to the shredder.
Generally, a small amount of water is sprayed onto the shingles just prior to the shredder head. The purpose is for both cooling and dust control. Clearly, this moisture content needs to be kept to a minimum as it adds to drying cost for the HMA producer. A one percent increase in moisture content will increase the drying cost by approximately 10 percent! Like RAP, the product needs to be kept as dry as possible.
It is generally advisable to shred no more than a two-week supply of shingles to avoid the possibility of agglomeration of the stockpile. This short storage time will also minimize moisture in the shredded shingles.
Often, shredded shingles are blended with either RAP or crusher fines. The objective of the blending is to keep the shingles from sticking together and has proven to be very effective. If a blend is produced, the HMA mix design should be based on the blend properties, not the shingles alone.
For peace of mind, it is advisable to regularly check tear-offs for presence of asbestos. Although asbestos is almost never found, one data point is better than ten thousand expert opinions.
The shingles need to be in the plant long enough to melt the hard asphalt. The HMA producer refers to this as dwell time. The length of dwell time will depend on the plant operation and efficiency. Plant trials will have to be done to determine the appropriate time. The mix temperature may need to be raised slightly to perhaps the 310 to 315 degrees Fahrenheit range.
The use of shingles in the HMA plant does have an impact on the plant operations. There is usually an increase in the frequency at which the plant needs to be cleaned out. This is an expense that must be included in the economic evaluation of using shingles.
An economic evaluation of the use of shingles will need to be developed for each location that is interested in the process. Issues that need to be included in the evaluation are: shingle transportation and handling costs, shredder costs, tipping fees, additional plant operational expenses and the value of the asphalt in the shingle.
WIN-WIN
HMA produced using waste asphalt shingles has been shown to have good performance. Several state agencies have successfully used the product. Perhaps the biggest challenge with many agencies is to have a specification that allows the flexibility to use shingles if the opportunity is available. In many cases, this requires some effort on the contractor’s part to demonstrate that the shingles will produce a HMA with good performance.
Use of waste asphalt shingles in HMA is truly a "win-win" scenario. The consumer wins with lower construction and rehabilitation costs without compromising quality, thereby stretching tax dollars and allowing more roads to be kept in better driving condition than if all virgin materials are used. The public also wins by reduced volume of construction rubble in landfills and reduced use of petroleum products. The construction industry wins because higher volumes of production from the same fixed investment lowers business risk and keeps more people employed.
The author is an engineer based in Columbia, Md. He can be contacted via e-mail at dsdecker@comcast.net.
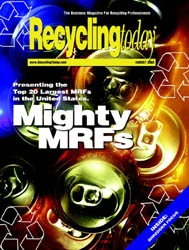
Explore the August 2002 Issue
Check out more from this issue and find your next story to read.
Latest from Recycling Today
- Athens Services terminates contract with San Marino, California
- Partners develop specialty response vehicles for LIB fires
- Sonoco cites OCC shortage for price hike in Europe
- British Steel mill’s future up in the air
- Tomra applies GAINnext AI technology to upgrade wrought aluminum scrap
- Redwood Materials partners with Isuzu Commercial Truck
- The push for more supply
- ReMA PSI Chapter adds 7 members