
Electric arc furnace- (EAF-) based steel production in the United States could increase from 70 percent of overall production as of late 2020 to 85 percent by 2025, according to estimates from the Steel Manufacturers Association, Washington. This growing EAF output would increase ferrous scrap demand and competition for volumes throughout the U.S. This, in turn, will change domestic scrap flows and scrap import and export trends.
Texas is becoming an increasingly attractive destination for steelmakers looking to set up EAFs. Over the past few years, three new EAF mills—Big River Steel (BRS), JSW Baytown and Steel Dynamics Inc. (SDI)—have announced expansion plans in the state, thereby increasing the need for scrap in the region. How will these EAFs meet their raw material needs?
A general market consensus points toward inflows through all modes of transportation, including barge or vessels, rail and trucks. Moreover, new scrap demand in the South could distort flows all the way to the Mississippi.
Freight costs are an essential factor in scrap procurement, and market participants note that water and rail access are preferred delivery forms mill consider when they select a site for making steel. Texas, because of its location, ticks most of these boxes. Market participants also say that transporting via rail over longer distances, imports of prime grades from Europe and barge loads of scrap sourced from along the East Coast also could be more economical for steelmakers in the region compared with truckloads sourced from closer suppliers.
Koch Metallics, BRS’ exclusive procurement agent, says it expects some of the additional scrap to come from material reshuffled from the basic oxygen furnace closures in the region. Companies like OmniSource, SDI’s scrap processing division, and Koch are proceeding with strategic scrap sourcing arrangements. Lynn White, commercial development manager at Koch, says her company is “leveraging its extensive experience in materials handling and transportation to reduce raw materials costs while seeking alternative supplies of raw materials.”
Koch Metallics also plans to maximize access to other Koch Group entities and their vast contact base to access scrap sources that include demolition projects and end-of-life assets.
Ore-based metallic scrap alternatives, such as hot briquetted iron (HBI), direct-reduced iron and merchant pig iron, also could be part of the raw materials mix for new EAFs, easing reliance on scrap. As a result, Voestalpine’s HBI plant in Texas and Cleveland-Cliffs’ HBI facility in Ohio could play larger roles in satisfying the raw material needs of EAF mills.
Greater metal recovery yields will add to total scrap supplies with ongoing technology investments at scrap processors. Portland, Oregon-headquartered Schnitzer Steel Industries, for example, is making capital investments to achieve greater metal recovery yields. The steelmaker’s export customers accounted for 65 percent of its total ferrous sales volumes in the fourth quarter of 2020, thereby, making Schnitzer a potential source for domestic feedstock.
Continued emphasis on recycling programs and landfill diversion also could increase national scrap supplies.
But the question remains: How will these trends affect the need for scrap in Texas and its surrounding areas?
SDI: An immediate impact
Of the three EAF mills planned for Texas, SDI has the closest start date at mid-2021. Regional dealers are hearing of small purchases starting in December 2020 to test logistics and a buildup of inventories in the spring. The upcoming 3-million-ton SDI mill in Sinton, Texas, will focus on flat-rolled products for the automotive industry. Market participants anticipate an average monthly scrap buy of 100,000 gross tons. Given the magnitude, present scrap flows could be interrupted.
In August 2020, SDI completed the purchase of Mexico’s Zimmer Recycling under its OmniSource metals division in anticipation of scrap feed needs in Texas. Zimmer has six recycling facilities with strong industrial relationships with northern Mexico mills that will ensure a continuous feedstock of busheling to the Texas mill. The purchase gave SDI access to an annual capacity of 2 million tons of scrap. Domestically, OmniSource does not have facilities in Texas but has facilities in nearby states like Oklahoma, Missouri and Alabama.
BRS: Looking beyond the U.S. border
In April 2018, BRS announced an option agreement with the board of commissioners of the Port of Brownsville for a 1.6-million-ton steel mill and distribution facility in south Texas. (As of early December 2020, U.S. Steel announced its intention to purchase BRS.)
The Port of Brownsville has been in confidential discussions with BRS for some time on using the port for trade. BRS selected the site not only because it is the only U.S. deepwater seaport directly on the U.S.-Mexico border, but it also is a major source of steel scrap. The port’s recycling facility also handles offshore drilling platforms, automobiles, rail cars, white goods and more apart from shipbreaking and recycling. BRS estimates that Brownsville recyclers could supply 500,000 tons of the 2.2 million tons required by its EAF annually. The port also provides access to additional scrap by barge and rail.
BRS has yet to announce a final plan and financing sources. Inadequate power infrastructure has influenced the EAF’s launch. Once fully approved, the project is four years out.
JSW: Leaning on domestic production
In March 2018, JSW announced a $500 million planned expansion in Baytown, Texas, that included steelmaking capacity of 1.1 million tons. The mill’s melting capacity would eliminate the need to transport slabs as raw material. Companies reliant on imported scrap have been affected by Section 232 import quotas and tariffs, providing an incentive for domestic production.
JSW has shifted strategies and recently hired Mark Bush as its chief executive officer. Bush is overseeing the upgrades at its Ohio Mingo Junction mill and strategic integration with the company’s Texas plate and mill pipe production site.
Focus was placed on upgrading the Ohio mill by the first quarter of 2021 to supply Baytown with raw materials by late Q1 to early Q2 of 2021. In the process, the Baytown facility was temporarily idled until Ohio can ship slab supplies.
Purchasing contracts for the furnaces at Baytown have not been signed as of early December 2020. Bush had said in August 2020 that the melting plan for the mill remains on the table but on an extended timeline depending on demand and pricing trends. According to some scrap dealers, JSW has its work cut out to manage a U.S.-based steelmaking asset as the entity has not fared well compared with other mills when steel faces downturns and rapidly resorts to closures.
Others in the fray
With the growing number of EAFs in Texas, competition for scrap will increase. Commercial Metals Co. is scheduled to begin operations at its 500,000-ton merchant bar quality micromill near its existing 400,000-ton micromill in Mesa, Arizona—a potential hub for scrap to Texas.
Nucor’s new 1.2-million-ton plate mill in Kentucky will allow for less volume to be available to the south. On the eastern region, Nucor also is expanding its footprint in Florida with its 350,000-ton annual capacity Frostproof rebar micromill. Evraz is proceeding with its $500 million mill expansion in Colorado.
The growing Mexican steel production market currently is facing diminished feedstock because of the pandemic, and Mexican mills are aggressively pursuing U.S. scrap. While Mexico is a net importer of scrap, the phenomena of lower scrap generation because of the country’s economic deceleration has placed added pressure on Mexican mills, with the situation expected to continue into the second half of 2021.
Scrap dealers and buyers are somewhat concerned about the effect that new mills in Texas will have on export flows. Prime grades produced in Mexico historically have been imported into the U.S. as Mexico’s EAF production of wire rod and rebar does not require the higher quality scrap, while secondary grades are imported. A Mexican dealer says, “Any incremental demand will provoke pressure on scrap prices, flows and tonnage access, and I doubt these new mills will be the exception.”
China’s shift to EAF production will increase short-term demand for ferrous scrap globally. In the long term, as China generates more scrap, its domestic supplies are expected to satisfy its mills with the possibility that China could become a net scrap exporter.
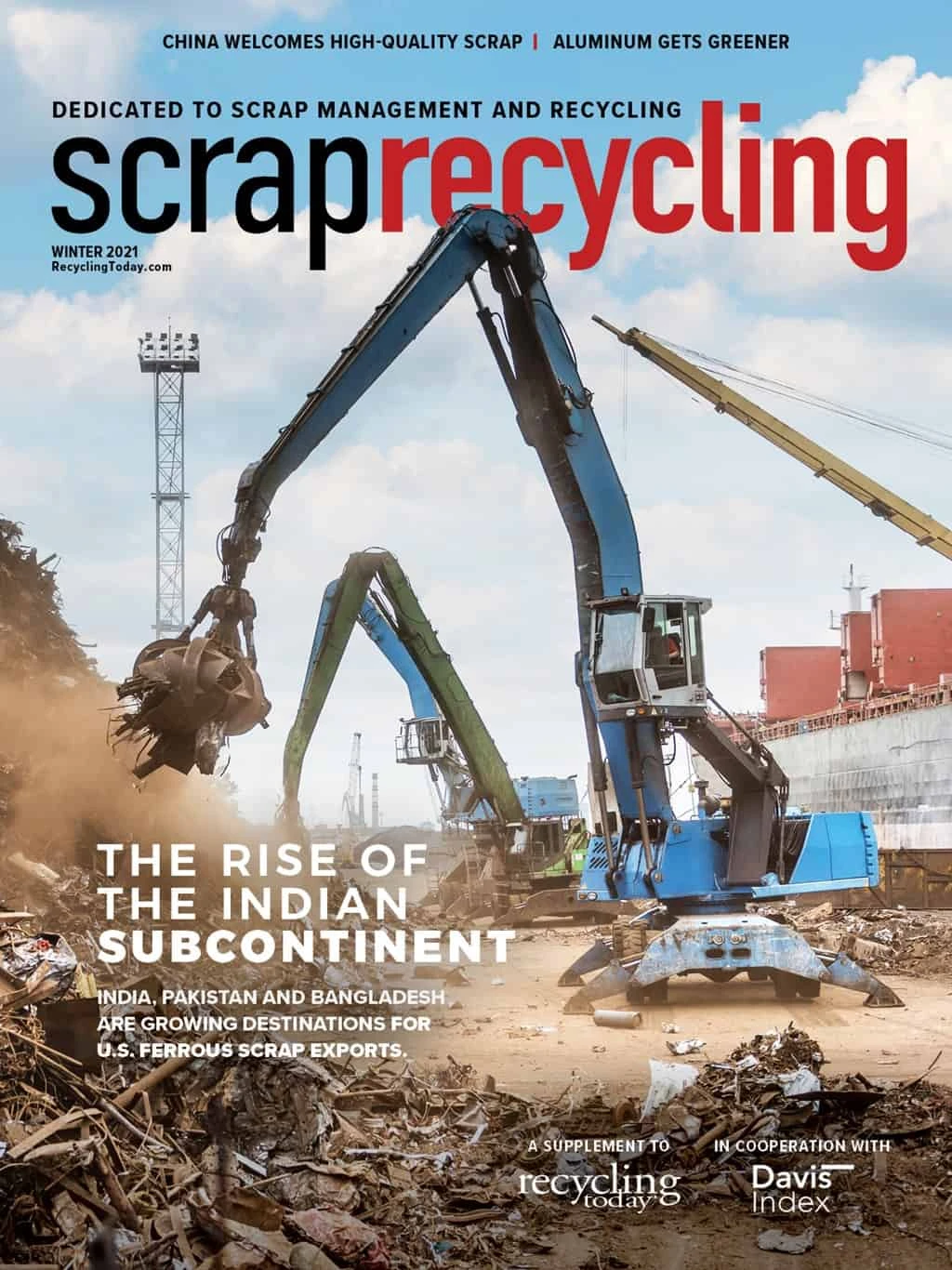
Explore the Winter 2021 Scrap Recycling Issue
Check out more from this issue and find your next story to read.
Latest from Recycling Today
- ReMA PSI Chapter adds 7 members
- Joe Ursuy elected to NWRA Hall of Fame
- RRS adds to ownership team
- S3 Recycling Solutions acquires Electronics Recycling Solutions
- Nextek, Coveris to recycle food-grade plastic film
- Recyclekaro expands recycling capacity
- USTR hears comments on port fee proposal
- C&D World 2025 hits record attendance and exhibitor numbers