
The English clergyman William Pollard once said, “Without change, there is no innovation, creativity or incentive for improvement. Those who initiate change will have a better opportunity to manage the change that is inevitable.”
Pollard, who died in 1893, could not have foreseen the factors that are forcing change in today’s plastics recycling industry and the plastics supply chain, but his words certainly apply.
The plastics industry has been the subject of growing scrutiny because of the issues of ocean-bound plastics and the collapse of markets for some secondary plastics caused by scrap import bans introduced by China. A growing number of countries in the developing world are adopting similar policies toward plastic scrap imports. This scrutiny is helping to force changes within the industry.
We’ve seen an increasing number of virgin plastics producers become involved in recycling in the last year, including Americas Styrenics LLC (AmSty), BP and Indorama Ventures PLC. Many of these ventures involve chemical recycling, which had not been pursued as a realistic option until recently. AmSty has partnered with Agilyx to chemically recycle polystyrene. BP plans to purchase the diesel fuel and naphtha blend stocks produced by RES Polyflow to distribute in the regional petroleum market. Indorama Ventures has formed a joint venture with Loop Industries to become what it describes as a world leader in the circular economy for 100 percent sustainable and recycled polyethylene terephthalate (rPET) resin and polyester fiber.
Other recyclers, such as the subject of this issue’s cover story, rPlanet Earth, Vernon, California, are looking for ways to streamline and cut costs from the plastics recycling process.
rPlanet Earth is producing polyethylene terephthalate (PET) packaging with as much as 100 percent recycled content using a vertically integrated approach that cuts out the pelletizing process. The company is going from Grade B PET bottle bales that it purchases from material recovery facilities throughout California to bottle preforms and sheet, and even thermoform packaging. While it will make a number of stock products that are suitable for food contact, rPlanet Earth also will produce rPET packaging to its customers’ specifications.
The company’s process allows it to avoid the heat history that pelletizing would impart. “It saves a lot of greenhouse gases, and you don’t get the degradation from heat exposure” during pelletizing, rPlanet Earth co-CEO Bob Daviduk says. As a result, rPlanet Earth can avoid degrading its products’ appearance because it is eliminating a melting step that can negatively affect color. Read more about rPlanet Earth’s approach to rPET packaging and its expansion plans in this month’s cover story.
Daviduk says now is the time for innovations such as this given brand-owner demand for rPET content.
Change is inevitable. Will you be helping to drive it or responding to it?
Get curated news on YOUR industry.
Enter your email to receive our newsletters.
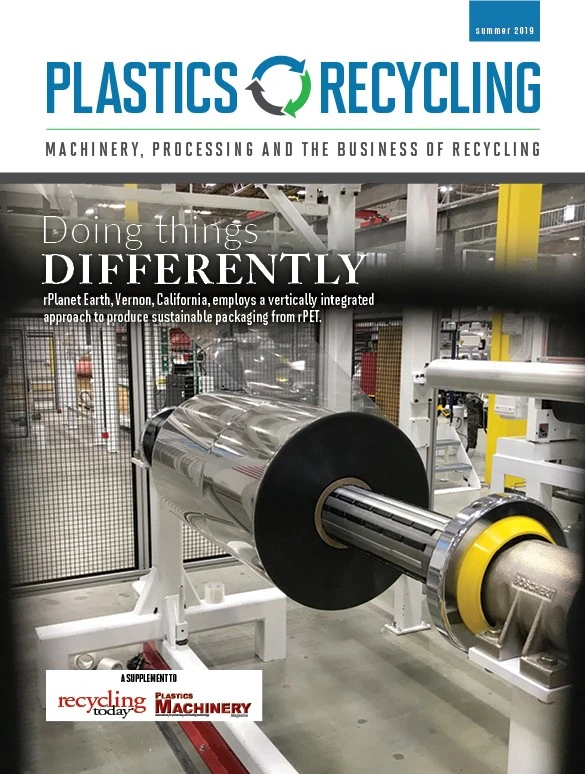
Explore the June 2019 Plastics Recycling Issue
Check out more from this issue and find your next story to read.
Latest from Recycling Today
- Circular by Shapiro releases "5 for Five" sustainability series
- Graphic Packaging set to close Ohio CRB facility
- Ameripen voices support for Maryland EPR bill
- Matalco to close Canton, Ohio, plant
- Maryland county expands curbside recycling to include electronics
- California EPS ban will be enforced
- YKK AP America introduces BetterBillet
- Fresh Perspective: Cameron Keefe