Of the metals that result from the automobile shredding process, which category is the more profitable, the ferrous or nonferrous?
While they represent a smaller portion of the total input material, the commodities derived from the nonferrous segment are more profitable, even in the current marketplace.
As we work through today’s economic challenges, the ability to produce more material and to generate more revenue is paramount. A variety of technologies currently are available that, when implemented downstream from an automobile shredder, allow shredder operators to derive more revenue from the nonferrous stream.
By definition, optical sorting is the ability to identify and separate materials based on physical properties or visible characteristics. In the automobile recycling industry, a variety of optical technologies are available, from the basic to the advanced, including sensor, X-ray, color and near-infrared technologies.
SENSING A DIFFERENCE
Sensor based technology is the oldest and most commonly found sorting technology employed downstream of the auto shredder. It has been estimated that more than 70 percent of the auto shredding facilities in North America have a sensor sorting unit.
These units include multiple rows of electromagnetic sensors positioned beneath a conveyor belt. The sensors can "see" the nonferrous metals within the ASR (auto shredder residue) stream. The technology was originally introduced in 2000 to recover stainless steel, the most valuable commodity found at the time, from the eddy current waste stream. CommoDaS/SSE GmbH of Germany was among the first companies to develop this technology, which was introduced to the U.S. market by Wendt Corp. of North Tonawanda, N.Y., in 2001. Steinert, SGM Magnetics and Eriez and MTD/Metaltek have introduced their respective offerings.
However, as the market value of nonferrous metals has changed, so have the needs of auto shredder operators. Today, sensor sorting equipment is used to recover as much nonferrous metal as possible from the eddy current waste stream and to minimize the volume of nonferrous metals that are lost to the landfill.
ADVANCING WITH X-RAYS
X-ray technology represents the next advance in optical sorting downstream of the auto shredder. There are two types of X-ray technology: X-ray fluorescence (XRF) and X-ray transmission (XRT).
XRF technology is commonly used in handheld metal analyzers. It performs a surface analysis of the material and is useful in identifying alloy composition.
XRT technology operates very differently from XRF technology. An XRT sorter is a stationary unit that features an X-ray generating source that transmits X-ray energy through the metal particles traveling below the unit on a high-speed conveyor belt. The X-ray energy is absorbed by the material’s particles based on their atomic density, creating an image that is captured by the unit. Using the captured image, the equipment can then identify, or "see," the targeted metal and perform a successful separation.
JOINT EFFORT |
The global nature of the economy and the scrap recycling industry in particular can be seen in the multi-national effort by Spain’s Toratec Recycling Solutions to devise a sorting and separating system for a scrap recycler in Japan. Toratec, based in Igualada, Spain, represents U.S.-based Innov-X QXR Sorting Systems in Japan and played a major role in installing what it calls the first high-volume XRF sorting system in that country using equipment from many manufacturers. In January of 2009, a six-track QXR sorting system was installed at Kanemura, an auto shredding plant near the Japanese city of Fukuoka. A critical part of the system at Kanemura is a QXR sorting system built by Innov-X Systems and developed and licensed by Austin AI. The QXR Series is a high-volume technology designed to rapidly and accurately sort by what Toratec calls highly specific material chemistry. Kanemura runs a 4,000-horsepower shredder and has a downstream system that includes eddy current sorters, induction sorters and optical sorters to recover nonferrous metals. A heavy media plant separates nonferrous metals. The QXR system installed at Kanemura primarily separates zorba with a size range of between .4 and 2.4 (sometimes up to 3.2) inches. The 24-inch wide QXR system uses 12 pairs of 2-inch airless paddles from Eriez, Erie, Pa., to divert the heavy metals from the aluminum. The purity of the aluminum ranges from 93 percent to 96 percent in one sorting step. To achieve a quality of greater than 99 percent, a second online sorting step uses optical sorting technology. – Submitted by Eva-Maria Gerosch on behalf of |
At a shredding facility, XRT equipment is used to process the zorba fraction, or the shredded nonferrous scrap that is comprised primarily of aluminum, created by an eddy current. Now, rather than sending the zorba product to a dense media plant for processing, a shredding facility can implement XRT technology to produce an iron-free, furnace-ready aluminum commodity as well as a heavy metal package.
It was only a few years ago that the market value of copper was well below that of aluminum. However, as the value of copper increased, the need for a new optical technology to sort the nonferrous metals within the heavy metal package based on color was born.
A COLORFUL VIEW
High-resolution CCD (charge-coupled device) technology was introduced to specifically perform separation based on color. The heavy metals package created by either a dense media plant or XRT sorting equipment serves as the input material. The material travels on a high-speed conveyor and passes through a scanning field. As the metal particles leave the conveyor and travel through the air, an image is taken, a decision is made and the targeted color material is separated from the stream. A mixed feedstock can be separated into red metal, yellow metal and white metal piles.
LOOKING MORE DEEPLY
The newest technology to be developed for the auto shredding industry is near-infrared, or NIR, technology. NIR technology sorts the different plastics within the ASR stream based on polymer composition and characteristics.
ASR is placed on a high-speed conveyor belt and passed through an NIR scanning field. Based on predetermined programmed criteria, targeted particles, such as PE (polyethylene), PPE (polyphenylene ether), HDPE (high-density polyethylene), PET (polyethylene terephthalate) and PVC (polyvinyl chloride) can be separated from the ASR.
On their own, each of these optical technologies offers shredding facilities the opportunity to extract more revenue from their ASR. When implemented within an existing plant, each offers an incremental revenue benefit. Recently available equipment offers a combination of these technologies and is designed for improved results. For instance, Wendt/TiTech has recently introduced equipment that incorporates two of these technologies to create a solution for insulated copper wire processing.
Through the efforts of companies such as Wendt/TiTech, Steinert, SGM Magnetics, Eriez and MTD/Metaltek, shredder operators have more optical technology options and equipment choices than ever before to assist in generating more revenue from ASR.
The author is sales and marketing manager of Wendt Corp., Tonawanda, N.Y. He can be reached at ridall@wendtcorp.com.
WANT MORE?
Enter your email to receive our newsletters.
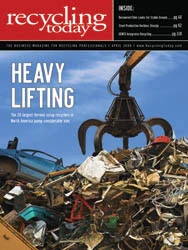
Explore the April 2009 Issue
Check out more from this issue and find your next story to read.
Latest from Recycling Today
- WM to debut 4 recycling, RNG projects
- Celsa Group welcomes new Spanish investor
- Ferrous price hikes could be poised to pause
- BIR prepares for Spanish exhibition
- Copper exempted from latest round of tariffs
- Interchange Recycling's EPR stewardship plan approved in Yukon
- Making the case for polycoated paper recovery
- Novolex, Pactiv Evergreen finalize merger