
Steel prices have risen steadily in the first four months of 2021, and CEO Lourenco Goncalves of Cleveland-Cliffs said it is about time that “a ton of steel is worth more than a ton of bananas.”
In a presentation made for the mid-April online Fastmarkets AMM Scrap, DRI & Minimills Conference, Goncalves outlined the major investments the Cleveland-based company has made in the past few years and looked at the global steelmaking metallics market. On the latter front, he portrayed a steel, iron ore and ferrous scrap landscape that is undergoing major changes.
Transformational change
Since Goncalves was hired as CEO in 2014, he has transformed Cleveland-Cliffs beyond its roots as a provider of Upper Great Lakes-iron-range products to North American steelmakers. In 2017, the Cleveland-based firm announced plans to build a 2.09-million-tons-per-year hot-briquetted iron (HBI) plant in Toledo, Ohio. That plant ramped up production in November and December of last year.
In an even higher profile set of moves, Goncalves brought Cleveland-Cliffs into the steelmaking industry with the acquisition of AK Steel, formerly based in Middletown, Ohio, in March 2020. Just eight months later, Cleveland-Cliffs added to its steel holdings by buying nearly all Luxembourg-based ArcelorMittal’s steel mills in the United States.
Subsequently, Goncalves is the CEO of a company that operates five integrated (blast furnace and basic oxygen furnace, or BOF) mills and four electric arc furnace (EAF) mills, all in the U.S.
The CEO said the initial purpose of the Toledo HBI plant was to offer a merchant direct-reduced iron (DRI) product to steelmakers in North America, but now that Cleveland-Cliffs has four EAF mills of its own, “We expect to use half of that in-house and sell half, as we have been doing, to our outside clients.”
The four Cleveland-Cliffs EAF mills are in Mansfield, Ohio, and in Butler, Coatesville and Steelton, Pennsylvania. The Mansfield mill produces stainless steel, the Butler mill makes stainless and specialty electrical-grade steels, the Coatesville plant produces steel plate, while the Steelton mill makes steel rail.
Goncalves said the large-volume Toledo plant made sense from the merchant DRI perspective because of the 10 million tons per year of EAF capacity being added by companies including Nucor Corp., Steel Dynamics Inc., ArcelorMittal (in Alabama), BlueScope Steel (in Ohio) and by the U.S. Steel-Big River Steel combination.
“We’re talking about more than 10 million metric tons being added to our market, without the corresponding support of feedstock,” he said. “There is no more [prime] scrap generation to support this 10 million tons, [and] the only concrete move that was made with explicit intention to support this new [capacity] was our plant in Toledo.”
As of 2020, Goncalves said 71 percent of steel output in the United States already was being produced at EAF mills. Much of this capacity was added following the 1989 installation in Crawfordsville, Indiana, of the first thin-slab caster at an EAF mill owned by Charlotte, North Carolina-based Nucor, which put EAF steelmakers in the flat-rolled steel game.
Carbon reduction
Thanks in part to this scrap-fed EAF steel output, the U.S. produces less carbon dioxide and other greenhouse gas (GHG) emissions per ton of steel made compared with output in China, India and many other nations. Goncalves said the steel sector in the U.S. is responsible for 2 percent of global steel industry GHG output compared with 64 percent for China. Concern surrounding global warming in the steel sector “doesn’t reside in the United States, it resides in China,” he added.
China not only uses more emissions-heavy BOF technology, it also uses sinter-based iron ore imported largely from Australia. Cleveland-Cliffs has been making iron pellets that lead to less than half of the GHG impact compared with the sintering process, Goncalves said.
“China feeds off Australia, which has lots of iron ore, but Australia does not have a lot of water [needed to produce pellets],” he said. “In the U.S., our taconite mines are located on the edge of the Great Lakes, so we can produce pellets, and we do produce pellets.”
Goncalves said operators of EAF and BOF mills can produce steel with lower emissions methods—he added that Cleveland-Cliffs is already doing so—even while using mined materials instead of scrap. “There is no such thing as blast furnaces versus EAFs, one against the other,” he said. “We operate both, [and with] our four EAF plants and five integrated plants, we’re on both sides of the process.”
Scrap scarcity
The CEO said the nonscrap-dependent methods will be necessary because of what he calls the “new reality” of higher scrap and, subsequently, higher steel prices. “I believe we are in for a very consistent appreciation in scrap prices,” Goncalves said. While pricing will fluctuate from $20 to $40 per month, he continued, “in the long run, for the next several years, we should expect scrap prices to appreciate in the international market.”
Regarding supply, Goncalves said prompt grade generation in the U.S. cannot rebound much unless more manufacturing returns from offshore. Even obsolete supply has seen some of the existing reservoir consumed steadily by the EAF boom of the past 30 years.
Demand for ferrous scrap will come not just from the 10 million tons of added capacity in the U.S. but also from a hungry export market likely to get even hungrier because of changes afoot in China. The leaders of that nation, Goncalves said, “recognize pollution as their Achilles’ heel. The Chinese Communist Party knows that is the problem they are exposed for, and they will be criticized and penalized” for high GHG emissions.
He continued, “So, the last five-year plan put in place talks about doubling EAF production in China from 100 million tons per year in 2019 to 200 million tons per year by 2025.” In what he called “typical Chinese fashion, this number will be achieved by the end of 2021, actually. It means China is ahead of their plans, but it does not have a fully developed scrap collection infrastructure to support 200 million tons of EAF capacity. In the meantime, they will fight for scrap in the international market.”
Goncalves said this means “we should expect scrap prices to appreciate in the international market. That’s motivated by demand and by the environmental push toward less generation of GHGs throughout the entire world. Australia cannot help because Australia cannot produce pellets.”
For Cleveland-Cliffs, the scenario paints a potentially bright picture for its Toledo HBI facility, its comparatively emissions-friendly iron pellets produced in the U.S. and its flexible steelmaking capacity in the U.S., Goncalves said.
“I believe the scarcity of scrap has just started to show,” he said. “Scrap prices in the long run will be extremely expensive. That is what we have prepared for. So having our own iron ore and [the ability] to produce environmentally friendly pellets and environmentally friendly HBI puts Cleveland-Cliffs in a unique position, not just from a cost standpoint but also from an environmental standpoint,” Goncalves concluded.
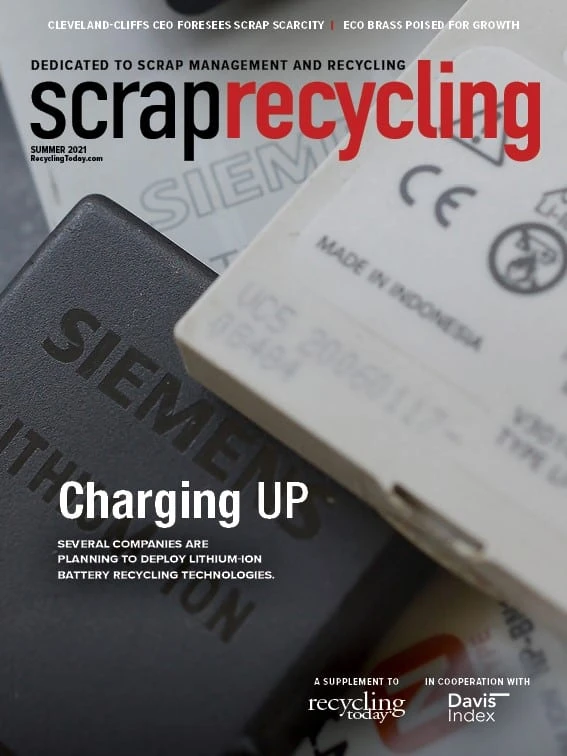
Explore the Summer 2021 Scrap Recycling Issue
Check out more from this issue and find your next story to read.
Latest from Recycling Today
- Steel Dynamics nets $217 million on record shipments
- Massive Chinese steelmaking rebound recorded in March
- LME looks into sustainable metal pricing
- OnePlanet Solar Recycling closes $7M seed financing round
- AMCS launches AMCS Platform Spring 2025 update
- Cyclic Materials to build rare earth recycling facility in Mesa, Arizona
- Ecobat’s Seculene product earns recognition for flame-retardant properties
- IWS’ newest MRF is part of its broader strategy to modernize waste management infrastructure