
More than 80 percent of all materials, some 20 million-plus tons, that flow into the curbside recycling system are recovered from an increasingly complex inbound stream.
To say that material recovery facility (MRF) technology has failed is inaccurate. What has failed is MRF operators’ overreliance on commodities to provide the revenue needed for investment and innovation while the current system ages. We will not break this cycle without significant investment in innovation.
It is ironic to write about the state of MRF technology just off the bottom of a prolonged and historic six-year down market. When new technology is most required, burnt investors, whether private or public, who counted on the sale of recovered commodities, are in no rush to invest.
Dismantling the illusion
According to a Pew Charitable Trust report issued earlier this year, MRF operators “offered low- or no-cost contracts to municipalities and other customers because they wanted to sell the recycled material at what were (then six years ago) high prices.” Additionally, and uniformly in the “up” market, recycling companies—whether venture capital startups, large integrated waste companies, local family-owned businesses or regional firms—went on large capital spending sprees at the top of that market, developing convenient household single-stream programs with willing and inviting local governments, that required (the then) high revenues to prosper. As a result, more than 65 percent of the U.S. population enjoys curbside recycling in more than 3,000 programs nationwide.
The same Pew report from this March also points out that local governments got used to the illusion that MRFs were a low- or no-cost processing component of the service. Then the bottom fell out, beginning in 2010. The result has been a gradual weakening of MRF infrastructure in the U.S. Investment at poorly funded companies stopped first, and then even the well heeled pivoted away from MRF investment and current system maintenance. Take the largest MRF operator in North America: Waste Management (WM) CEO David Steiner—a regular on the CNBC program “Squawk Box”—said on that program May 28 that “… we all know what happens when [recycling] becomes unprofitable: People don’t invest … we generally invest $100 million to $200 million a year in recycling assets. The last two years we haven’t invested any.”
According to “Recycling in America: In the Bin,” which was posted to The Economist website April 22, 2015, “$1.25 billion is needed to fully modernise America’s recycling infrastructure.”
That figure is not far-fetched and might be more pronounced now, given investment in MRFs is a “trickle” when compared with 2010’s high commodity markets.
Investing in processing
According to conversations with all of the large equipment suppliers, only small to nonexistent efforts have been undertaken at retrofitting, unless required to keep a facility operational or demanded by key large public customers. And the new MRFs that are starting up have been long in the pipeline, such as Republic’s new Las Vegas showplace, the Pratt Conyers, Georgia, facility and the Rumpke central Ohio facility—these being the exceptions to the rule.
As current commodity pricing inches up and needed repairs hopefully get funded, demand for equipment should grow, but that is a big “if” and likely will not cover the needed changes to infrastructure to accommodate today’s dynamic materials.
Estimates of the number of operating MRFs vary widely. Some notable estimates from the last five years say approximately 270 multimaterial MRFs are operating, while the Environmental Research & Education Foundation reported at WasteExpo in early June of this year that some 350 MRFs are in operation nationwide. RRS and other sources estimate more than 450 multimaterial MRFs are operating. Averaging these numbers, each MRF must spend roughly $3 million to modernize based on The Economist’s $1.25 billion estimate.
However, $3 million does not buy what it used to. The current generation of MRFs is bigger. National studies have confirmed that MRFs coming online in the last decade increasingly were regional, with higher incoming tonnages and throughput, commonly serving between 200,000 to more than 1 million households. These MRFs typically require a processing rate of more than 20 tons per hour. Some 10 to 15 pounds of material gets sorted per second into saleable commodities at these MRFs.
But the complexity of these systems requires more maintenance. This phenomenon is well-documented, and MRF maintenance costs have doubled to more than $8 per ton for such systems after five years of operation. For a 10,000-ton-per-month MRF, this represents a bill in excess of $1 million in ongoing maintenance per year. Simple replacement and repair costs for worn screen components, conveyors, optical sorters and balers and building wear costs (tip floors, HVAC, scales, etc.) are 3 percent to 7 percent of total capital per year. For example, a 20-plus-ton-per-hour system and building may cost $14 million. The money to keep it going in good repair, without any kind of upgrade, is between $400,000 and $900,000 per year. If MRFs put off making these relatively minor repairs for several years, millions of dollars of pent up maintenance must be spent before real process changes can occur.
Most MRFs are stuffed with equipment already, and space is at a premium. The snug design makes change expensive. Changes beyond the component level to the process level—adding an optical sorter on the paper line after screening out containers—may require motor control changes, platform load design changes, maintenance access modifications, conveyor belt changes, new storage, reintegration with the entire system and demolition of existing equipment. Such an effort can be well more than $1 million. If the process design change has multiple components, the cost is even higher. Also, major aftermarket replacement components have risen in cost and complexity. Replacing a baler at a typical MRF can cost from $450,000 for a two-ram baler to $1.5 million for a high-speed, energy-efficient single-ram machine—about 40 percent more than 10 years ago.
The inbound packaging and waste paper stream also has undergone a well-documented diversification and lightweighting. Shapes, densities/weight, blurring of the physical lines between 2-D objects (paper) and 3-D containers (bottles, cans and cartons) and the chemistry of the inbound material all are different than what the original design of a typical MRF considered—namely, cleaning and separating newspapers (ONP) and OCC (old corrugated containers) and further separating metal containers from plastic bottles and metals and plastics from glass.
The custom nature of new materials for consumer packaging changes the overall flow of materials through the plant—the speed of the system, the productivity levels (lightweighting means more units per ton) and the need for identification, capture, storage and markets for each additional material. These changes are not completely accounted for in 95 percent of MRFs today.
The demand to add new materials has been constant and, for a variety of reasons, these demands were accommodated by all players in the MRF business—from municipality to MRF owner. MRFs more than doubled the types of containers they took, and all household papers were accommodated, not just ONP and brown grades. Rarely was the real marginal cost determined for each new material by analytically weighing the impacts, and the assumption that each new material only had a marginal increased cost was unrealistic in this environment. Consequently, MRF costs increased 25 percent in eight years as they struggled to keep up with the realities of the stream and the demands to recycle a wider variety of paper and packaging.
Considering components
To fully accommodate a wide range of materials, more components must be added. Instead of long-applied screens, magnets, eddy currents and near-infrared optical sorters, MRFs require advanced air separation, dimensionality screens and separators, nonwrapping debris screens and other more advanced equipment to truly separate and clean. Entirely new processes will be needed rather than just components. MRFs also will have to wrestle with capturing more film and other two-dimensional materials.
How do we bring needed innovation to MRFs today in a poor U.S. investment environment? By treating the MRF as part of the service.”
How do we bring needed innovation to MRFs today in a poor U.S. investment environment? By treating the MRF as part of the service. Where recycling infrastructure’s return on investment (ROI) is supported, as in Europe, innovative products, better design and advanced processes are invented to accommodate a more and more complex household recycling system, even the rarer single-stream programs there. Europe can do so explicitly because of reliable funding that can support research and investment. As a result, recent innovations, such as air knives, paper magnets, robotics and multiwall 3D trommels, have been brought over from there to here. Several new approaches to optical recognition technologies also are available that help in the identification of the new plastic and fiber materials, either as a quality control device or as a positive sort for the material. These include near infrared, other infrared and visible light and lasers to identify resins; X-rays to detect outlier elements, such as chlorine in PVC (polyvinyl chloride) and bromine fire retardants in cardinal plastics; and optical recognition cameras with higher sensitivity in the lenses to identify shape and sometimes color.
Technology and processes that were innovative in Europe 20 years ago are spread throughout the U.S. today, and European-derived equipment makes up a significant share of MRF infrastructure. MRF operators and engineers here, whenever possible, incorporated it readily. Borrowed innovation is better than none. But U.S. MRFs lack the funds to borrow anew and take advantage of these innovations.
This is not to say that equipment providers here are not competent. They are, and their engineering competes well. But, the lack of steady ROI-driven development hampers their progress. The grassroots policy and research Jobenomics blog, www. jobenomics.com, has said government funding mandates may be important if we want to have similar MRF investment and innovation here in the U.S. Where such support exists, as in California, the greatest investment in recycling is made.
Realizing their function
All the way back in 1993, David Biddle of the Harvard Business Review, during a shorter but still highly painful recycled paper and metal downturn, commented that MRFs were “… capital intensive and (were designed for) filtering materials into ‘cleaner’ commodities,” where “the end product should be a raw material that can be injected into existing industrial processes.”
A MRF’s function is cleaning, in other words. Even then the U.S. MRF system faced similar, though simpler, barriers to investment. The MRF evolved from this era to a successful component in the most convenient and highly popular recycling system in the world—single stream—during the boom years earlier in this new century. Until we pay for that convenience on the processing side that funds modernization in a systematic way, innovation and technology will not develop here in the states, and MRFs will struggle to keep up with the need to clean a more diverse waste stream.
MRFs have been shown to be the least costly component of a typical municipal collection service—collection and disposal of garbage as well as collection of recyclables cost much more per household. It’s time to make MRFs part of the system without taking the fall for commodities, which help offset costs but are unreliable for investment.
![]() | The Garden Center Conference & Expo, presented by Garden Center magazine, is the leading event where garden retailers come together to learn from each other, get inspired and move the industry forward. Be sure to register by April 17 to get the lowest rates for the 2025 show in Kansas City, Missouri, Aug. 5-7.
|
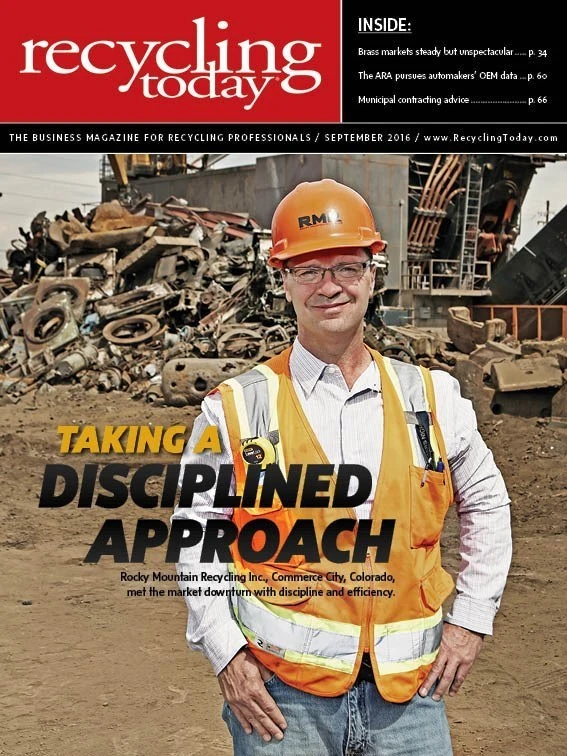
Explore the September 2016 Issue
Check out more from this issue and find your next story to read.
Latest from Recycling Today
- ReMA board to consider changes to residential dual-, single-stream MRF specifications
- Trump’s ‘liberation day’ results in retaliatory tariffs
- Commentary: Waste, CPG industries must lean into data to make sustainable packaging a reality
- DPI acquires Concept Plastics Co.
- Stadler develops second Republic Services Polymer Center
- Japanese scrap can feed its EAF sector, study finds
- IRG cancels plans for Pennsylvania PRF
- WIH Resource Group celebrates 20th anniversary