"We used to be a large paving company doing a small amount of recycling," says Marshall "Jack" Gibson. "Now it has turned around. We are a large recycler doing a small amount of paving."
While he might be overstating the swing a bit, Gibson ought to know, as he is CEO and owner of Commercial Paving Co, Inc., Scarborough, Maine, and its sister company Commercial Recycling Systems.
He oversaw the changeover for the simplest of business reasons—recycling is profitable and is the future, he says.
CHANGING DIRECTIONS
Gibson has been in the paving business for 57 years, and Commercial Paving was a typical paver, going after large paving projects where it could utilize its hot mix plant and expertise. Indeed, its introduction to recycling was on a state highway project in the early 1990s, when a district engineer approached Gibson about taking some oil-containing soil, screening and processing it and putting it into the hot mix Commercial Paving was applying.
Gibson agreed to try it, but after the first day of using the new mix, it was obvious something was wrong. The paving crew, which knew nothing of the new additive, complained about the mix’s odor and the headaches they got from it. "I knew we were solving a soil problem," he says, "but we were creating a pulmonary one for our personnel." Gibson immediately suspended using the material.
For many contractors, narrow-mindedness would have made that the end of it, as they would not put any more of that problem material in the mix.
But Gibson took a different tack. He was intrigued because he had heard that disposing of the oil-containing soil—he doesn’t call it contaminated because it is a useful product—cost as much a $100 per ton. "That sounded like an awfully high number," he says. So the company did some research and lab work and developed a process that would allow safe reuse of the material.
|
The Maine Department of Environmental Protection approved the process, and Commercial Paving has been doing similar projects all over the state ever since.
But that was only the start, according to Douglass Gleason, vice president of recycling and general manager of the company’s recycling facility. Besides oil-containing soils, the company accepts and recycles sand blast grit; catch basin grit; bottom and fly ash; commercial and residential roofing; gypsum wallboard (non-painted or papered); concrete; porcelain and glass materials, including windshields; street sweepings; asphalt pavement; bricks; ledge (blasted rock from highway construction); any used gravel material; stone screenings; and wood, including painted, but not treated, wood.
Commercial Recycling Systems is the division that provides a larger percentage of the company’s revenues. More than 250,000 tons were handled last year, with but a few roll-offs going to the landfill. The rest is recycled, says Gleason. In addition and perhaps as importantly, "10 percent of the mixes Commercial paving sends out have some level of recycled material in them, without adverse effects on our paving personnel," Gibson reports. "Our crews are very fussy, and if anything is not right, they will let us know."
So how did a paving company get so deep into recycling? "About eight years ago, when municipal and state budgets were tight, the numbers (revenue from paving) began to drop," says Gibson. "We were looking at the paving operation ending up every year in the red, and I said, ‘This is crazy.’"
The company decided not to pursue the largest paving projects anymore, focusing instead on the more profitable recycling sector—a sector that has grown even more profitable every year since, says Gleason.
But it wasn’t easy. "When we started recycling, it was not popular," says Gibson. "We had a difficult time convincing contractors and municipalities that these were good products and that we were willing to prove it. We wound up giving some of our material for projects to contractors and told them that if they didn’t like the material, don’t bother paying us. That’s how we built the recycled materials business."
MATERIAL MIX
First up was aggregate recycling, a natural extension of the paving business. Commercial uses a Pioneer 3042 jaw crusher as a primary and a Thunderbird horizontal impact crusher with a 36-inch infeed as a secondary. A triple-deck screen (58 inches by 16 feet) and three magnets also are a part of the system, which is fed by a Caterpillar 950G loader.
"We had to modify most equipment to manufacture quality recycled products," says Gibson. "They now produce a quality product daily."
Next was wood, because the chips could be used for soil stabilization and erosion barriers on paving projects. The amount has risen over the years to the point where the company now has four grinders—two Maxigrinds and a Biogrind from CMI and a Peterson Pacific, which can work in concert with a ReTech Model 620R trommel screen.
Those machines often travel to customers’ sites to grind wood for a variety of markets, but the largest is the New England standby: the boiler fuel market. Says Gleason: "The wood market depends on what they are getting paid for the electricity. The big use is in the middle of the summer and the middle of the winter. Fortunately, the alternative energy facilities have great stockpiling capabilities, which allows us to keep shipping to them."
That is helpful, because the paving company, hot mix plant and recycling facility all share a 14-acre site in the Portland suburb.
Another recyclable material Commercial has been working with for several years is asphalt shingles. The company adds the processed shingles into road pavement base, binder hot mix and a cold mix. Recently Commercial received an MTI grant to continue development of a product for gravel roads that will substantially reduce erosion, dust and grading maintenance. The product also may be used in the reconstruction of secondary roads. It currently has a beneficial use license in Maine and Massachusetts (it’s pending in New Hampshire) to process shingles with natural base material, making a product that can stay unpaved for a time without required grading. But the largest shingle market is a road base product.
Commercial Recycling accepts gypsum wallboard in limited amounts, because, like so many other recyclers, it has limited market opportunities.
Most of the material comes from within a three-hour haul from the company headquarters. Commercial does have its own fleet of trucks that it sends out to collect material from municipal partners in its material exchange program. Those partners and nearly 500 contractors and state and federal agencies are taking advantage of low recycled material rates. Tipping fees vary by material type, though generally provide substantial savings over landfill cost.
The municipal partners and the contractors are the largest customers of the finished products. Gibson says, "We felt that we were taking in material from many sources to recycle, why would they object to taking some recycled material back?" It worked, he adds, as the program has really grown.
Commercial Recycling makes several products out of the incoming materials, some with national trademarks. Besides those mentioned above, some include Bind-Tite, a drying agent for wet soils and aggregates; Hot De-Icer, a winter road maintenance and stockpile cover manufactured from aggregates and asphaltic binders; and Jack’s Patch, a blend of crushed stone and recycled shingles for asphalt road repair.
COOPERATION AND OPTIMISM
Both Gibson and Gleason agree the company has been fortunate in its dealings with the Maine DEP, in sharp contrast to the often-adversarial relationship many other C&D recyclers have with their own states’ equivalent agencies.
"The reason we have advanced substantially is because of a mutual respect for one another. This has provided our company with a good working relationship with our regulators," says Gleason.
Gibson adds, "The state regulators have been very helpful. They have their job to do," he continues. "I am the type of person who if I think of something today, I want to do it tomorrow. But it doesn’t work that way, and we have had to cool our heels many times. However, we are well aware the department is protecting everyone’s interests, including ours. We do have a very cooperative relationship."
Gibson is bullish on the future of the C&D recycling industry. From the time Gibson has spent promoting the franchise concept for sharing Commercial’s expertise with others, he expects many other smaller companies to jump into the business in the coming years. "There are many firms throughout the U.S. and Canada that have expressed an interest in purchasing our technology" says Gibson. "However, it seems most prudent to us at this time to develop further operations throughout New England as our priority."
New England is home to one of the most sophisticated C&D recycling markets in North America. And it is one Commercial has a large stake in, for now and in the future.
The author is associate publisher of C&D Recycler and executive director of the Construction Materials Recycling Association. He can be contacted at turley@cdrecycling.org.
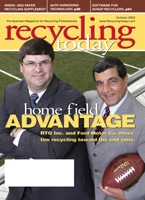
Explore the October 2003 Issue
Check out more from this issue and find your next story to read.
Latest from Recycling Today
- Steel Dynamics cites favorable conditions in Q1
- Hydro starts up construction in Spain
- Green Cubes unveils forklift battery line
- Rebar association points to trade turmoil
- LumiCup offers single-use plastic alternative
- European project yields recycled-content ABS
- ICM to host colocated events in Shanghai
- Astera runs into NIMBY concerns in Colorado