
In 2018 Metalico set out to significantly upgrade its nonferrous processing capabilities at its Buffalo, New York, shredding facility. Joe McGough, VP of Engineering & Shredder Operations for Metalico, says, “Market conditions had changed, and we needed to change the metal packages we were making. It required us to invest in a new plant.”
Following a comprehensive tendering process for the 45 tons-per-hour plant that would produce zorba, zurik and insulated copper wire (ICW), Metalico selected SGM Magnetics to supply the plant. SGM in turn partnered with U.S. Conveyor to supply the conveyors, structural work and mezzanines.
“In going through the process, we were introduced to U.S. Conveyor’s Modular Hybrid Conveyors,” McGough says. “I was impressed with what I learned and saw. These things are extremely well-engineered, and everything was top-shelf. They were not the cheapest option, but they were certainly the best.”
He adds, “Years of experience has taught me that anyone can put a nice paint job on conveyors, and they look great. Trouble is, six months later in this severe-duty application, they begin failing. These units had PPI rollers, SKL bearings, Dodge motors and gear boxes. We knew they would last, and that’s been the case.”
Plant changes made easy
Since 2018, Metalico has made several modifications to its plant. “We’ve added some equipment and reconfigured the plant to meet changing market demands,” says McGough.

“What’s outstanding about the modular configuration of these conveyors is you just take them apart and put them back together. It’s literally unbolting, reconfiguring and rebolting. No need for journeyman welders to cut the system and then try to get it back together,” he adds.
“When we installed the plant, I’m not sure we fully appreciated the time and money we’d save each time we made a change. The modular conveyor design has made making tweaks or major adaptations much easier.”
Engineered for success
U.S. Conveyor’s Modular Hybrid Conveyors incorporate the benefits of a troughing conveyor and combine them with the benefits of a fully sealed slider pan conveyor. They have a flat roller carriage that carries most of the payload with sealed side skirts on the edges of the belt.
“U.S. Conveyor uses first-rate components and have very high-quality fabrication.” – Joe McGough, VP of Engineering & Shredder Operations
The bottom edge of the belt slides along an angled abrasion-resistant (AR) wear plate to aid in sealing the bottom edge of the belt. The skirting material in contact with the belt is replaceable, high-wear UHMW (ultra-high molecular weight polymer). Safety pull cords, nip guards and tail covers are included below 7 feet or when conveyors are in arm’s reach.
The units are available in straight, banana-bend and z-bend configurations.
“U.S. Conveyor uses first-rate components and have very high-quality fabrication,” states McGough. “They cost a little more upfront, but they deliver loads of value and cost a lot less in the end. They are straightforward, honest guys to deal with,” McGough concludes.
Get curated news on YOUR industry.
Enter your email to receive our newsletters.
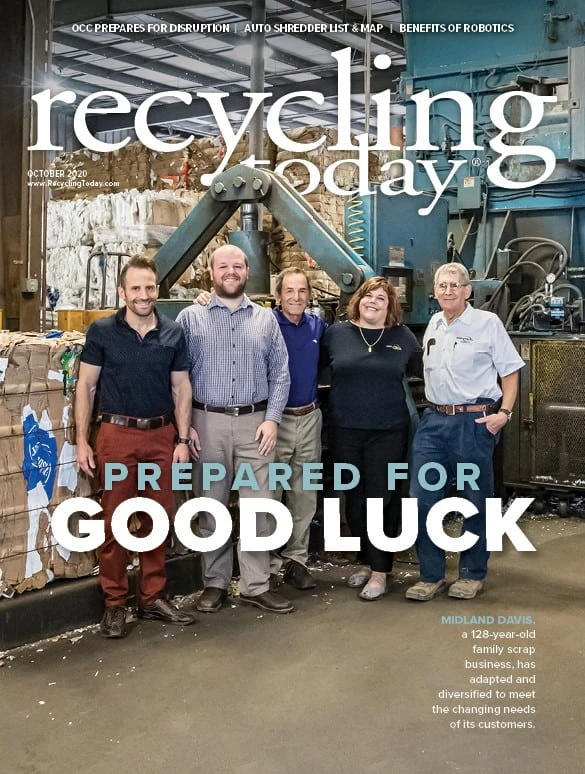
Explore the October 2020 Issue
Check out more from this issue and find your next story to read.
Latest from Recycling Today
- Toppoint Holdings expands chassis fleet
- Lego creates miniature tire recycling market
- Lux Research webinar examines chemical recycling timetables
- Plastics producer tracks pulse of wire recycling market
- Republic Services, Blue Polymers open Indianapolis recycling complex
- Altilium produces EV battery cells using recycled materials
- Brightmark enters subsidiaries of Indiana recycling facility into Chapter 11
- Freepoint Eco-Systems receives $50M loan for plastics recycling facility