Maximizing a baler’s productivity and life span often comes down to doing the
little things. Putting into place a consistent maintenance program is one of those
little things that can help ensure maximum production.
Machinery manufacturers of every variety endorse proper maintenance as one of the best, least expensive and easiest ways to guarantee value from their products. The philosophy is no different for manufacturers of balers.
It is essential that regular, routine maintenance be performed on balers to ensure that they operate at peak performance.
CLOCK WATCHING. Because of the initial cost of a baler, owners of the equipment often seek to run the machines long enough to make sure they receive an immediate return on their investment. Many owners and operators opt to run these machines constantly. Routine downtime, to many of these operators, is tantamount to throwing money away.
However, baler manufacturing company personnel say that taking time to spot check the baler and to perform routine maintenance and general housekeeping can extend the life of the baler and boost the productivity of the machine.
Baler manufacturers say that while these procedures can save significant repair costs down the road, many baler owners do not adequately conduct the simple steps that can spell the difference between a few hundred dollars spent now or tens of thousands of dollars spent later if the problem is not handled when it first appears.
Albert Gould, vice president of Enterprise Co., a Santa Ana, Calif.-based baler and recycling equipment manufacturer, says most companies that purchase balers do not follow up with a maintenance plan. And that, he adds, is a big mistake.
Buddy Himes, president of Himes Service, a Waco, Texas-based equipment services company, echoes Gould’s opinion. "Operators don’t perform the maintenance that is needed." Failure to follow many of simple maintenance and repair procedures could result in sharply higher repair costs.
Roger Williams with American Baler Co., Bellevue, Ohio, says one problem is that "some operators only worry about maintenance when the baler goes down. Most operators just want to keep the plant running."
Although offered only anecdotally, several of the baler manufacturers say that it is more likely that inadequate baler maintenance occurs at a satellite plant of a company with multiple locations rather than at a company with just one central recycling facility.
Also, while having an employee dedicated to maintenance procedures can result in a more efficient baler operation, often a maintenance supervisor can be stretched too thin, spending more time ensuring that trucks are repaired rather than attending to the baler.
PART OF THE ROUTINE. While all baler manufacturers have very explicit directions on what to check, when to check, and how to repair any problems, many baler owners neglect to follow the check list carefully.
What exactly is considered routine maintenance? A quick walk around the machine to look for leaks, clear any extemporaneous material from around the baler and to check oil levels is considered a very good start.
Joe Szany, director of Horizontal Baling Systems Sales for Marathon Equipment Co., Vernon, Ala., points out that many of the steps he recommends operators take "are not labor intensive." If these simple steps are taken, Szany continues, they can mean the difference between a few thousand dollars in preventive care and tens of thousands of dollars to overhaul the equipment.
According to the baler manufacturers contacted for this story, one of the most important maintenance steps is checking the level and the quality of the oil. "Oil quality is big, but it is often neglected. Most manufacturers say you should check the oil once a year. I don’t think it is done enough by the operators," Szany adds.
Another simple step that should be taken is checking to make sure the bolts are fastened properly, he adds. While this procedure may seem like an obvious, simple step, failure to keep the bolts tight can create greater problems such as causing the shear blades to not be aligned properly, creating a larger gap in the baler.
American Baler’s Williams is even more succinct, saying that many of these problems could be remedied by simple "housekeeping" every day.
This might mean having the operator make a visual check of the equipment the first thing in the morning, clean out the baler and make sure debris and residual material is not clogging the various parts of the baler.
For example, keeping the area and the baler clean will allow an operator to see any problems with leaks, to keep dirt and other grit from damaging some of the equipment and to prevent bigger problems like tangled and damaged hoses.
"Taking these simple steps," Williams notes, "will eliminate many of the minor problems."
Problem areas. While recycling has long been considered a harsh environment for equipment, it appears that the environment is becoming even rougher. As municipalities look to improve their recycling rates, more material is being handled. While glass is a big concern, the growth in the number of single-stream collection operations is causing greater amount of glass to be mixed in with other recyclables. Along with glass, greater amounts of grit, dirt and other abrasive materials are finding their way into the baler.
Gould says that material coming from a single-stream system may take in a much larger amount of glass fragments. When mixed in with the load, enough of the glass shards can act like a sandblaster. Over time this can cause damage to many different parts of the baler, including the shears and the floors.
To reduce the amount of glass reaching the baler, a sorting system should be included in front of the baler to pull out as much glass as possible.
In addition to glass, Williams remarks that plastics and flattened used beverage cans can create problems for balers. These materials can get caught up in some of the different parts of the baler, resulting in the equipment running less efficiently.
Single-stream processing calls for operators to be even more vigilant with their maintenance schedules.
A host of maintenance steps should be taken. One thing to remember, Gould says, is that an operator should base the maintenance on how much the equipment is being used.
Himes says that several metals, such as titanium and stainless steeel, are also very punishing on the balers. He says that the titanium could quickly damage an essential part of the baler.
While a host of components and parts of a baler should be checked, particular components might merit greater attention.
Gould, for one, says that the wire-tying system is an area that should be closely watched and serviced. Constant cleaning, oiling and blowing out of any extemporaneous material will prevent any slowdown in the operation.
Failing to adequately maintain the wire-tying system could cause the bale wires to improperly band material, potentially resulting in bales breaking apart.
"It is the number one problem area," Williams says. "It is an area that is doing a lot of the work. Some balers use it every minute to minute and a half." He adds that operators should look to see if knots are forming.
CALLING ATTENTION. While acknowledging that many operators fail to adequately provide the maintenance to keep the balers running at peak performance, companies are offering balers with additional programs or services that could make the maintenance tasks easier to remember.
From alarms and lights that notify the user when a repair or check needs to be performed, many baler manufacturers recognize the importance of helping users keep their balers operating efficiently.
While these programs can help, it still falls to the user to ensure that the small problem is fixed before it snowballs into a much larger problem.
For example, Williams says that one of its customers knew it had a preventive maintenance task scheduled. However, the company wanted to see how long it could go without performing the maintenance. "All of a sudden they lost a main cylinder. The shear gap widened. The result was a baler that was down for longer than a week."
Often, when a baler needs to be repaired, the downtime could extend from several days to as long as a month or even longer, depending on the availability of parts, etc.
In comparison, the time needed to perform many of the routine maintenance tasks could take less than a day. At the same time, it would likely allow the baler to last for much longer before needing to purchase a new baler.
And, as the old bromide goes, "Time is money."
The author is senior editor and Internet editor of Recycling Today. He can be contacted via e-mail at dsandoval@RecyclingToday.com.
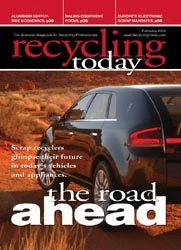
Explore the February 2004 Issue
Check out more from this issue and find your next story to read.
Latest from Recycling Today
- PCA reports profitable Q1
- British Steel mill subject of UK government intervention
- NRC seeks speakers for October event
- LME identifies Hong Kong warehouses
- Greenville, Mississippi, launches aluminum can recycling program
- Cotton Lives On kicks off 2025 recycling activities
- Georgia-Pacific names president of corrugated business
- Sev.en Global Investments completes acquisitions of Celsa Steel UK, Celsa Nordic