
Balers are the foundation of many recycling operations, enabling the efficient handling and transportation of materials ranging from old corrugated containers (OCC) to plastic bottles to light metals. These workhorses, even when properly maintained, will require relines to keep them operating efficiently for years to come.
SIGNS TO MIND
Baler operators will know it’s time for a reline when they begin to witness gaps between the shear knives, exacerbated floor wear at the shear point and leaking cylinders, says Mike McChrystal, president of Cleveland-based OBC.
OBC sells and services many of the recycling industry’s most recognized baling equipment brands, including Harris, Max-Pak, American Baler and IPS.
“Most balers are built with adjustability in mind,” says Jim Kuhns, operations manager for B.E. Equipment, Quakertown, Pennsylvania. “As floors and ram liners wear, the knives and ram guide bars can be lowered so cutting and running tolerances can be maintained. Once you are forced to drop the stationary knives below the guide bars, it is time to replace (at the very least) ram bottom and floor liners.”
B.E. Equipment offers a variety of new, reconditioned and used recycling equipment, including balers. Baling equipment brands the company represents include International Baler, BACE, Max-Pak, Excel and Imabe Ibérica.
Kuhns says floor strip liners will begin to break loose under the shear beam as the leading edges of the strip liners wear in machines with strip-lined floors.
“Depending on the manufacturer, just replacing the floor and ram bottom strips is acceptable in certain situations,” he adds.
Recyclers also should be on the lookout for consistent jamming under the shear beam. “If the baler continues to jam, and there is no adjustment remaining, the additional force required to push the material under the shear beam may in some cases cause the rear cylinder mount to break, causing catastrophic frame damage,” Kuhns says.
When recycling operations begin seeing these signs of wear will vary depending on the volume and type of material being processed and the type of baler, McChrystal says. “If it’s relatively glass-free material being processed, the material will not make much of a difference,” he says. “Lighter materials, such as PET (polyethylene terephthalate) and HDPE (high-density polyethylene) bottles, tend to rise up above the shear point as the ram gathers, so more strokes are required.”
“A baler with a precompression lid keeps material below the shear point, which means the ram will cycle less often to make a bale,” McChrystal adds. “The lid greatly reduces the air volume in the charge box.”
He adds that OBC generally tells its customers they can expect to have to reline their balers every five to 10 years. “Most probably happen within a seven-year period,” McChrystal says.
Adhering to a preventive maintenance schedule will help recyclers to extend the time required between baler relines, Kuhns says. “A baler that is properly maintained will always require less liner replacement than a unit that is not. The simple act of adjusting the knives, hold-down liners and/or hold-up liners will force the main ram to always run as straight and true as possible,” he advises.
EXPERT ATTENTION
While recycling operations with properly trained maintenance crews often can perform relines, some balers require special tools and hydraulic wrenches, Kuhns says. “A crew that is specifically trained to perform a reline will always achieve better results than one that is doing it for the first time,” he suggests.
McChrystal says the work can be tedious, and, while most recycling companies have maintenance crews who could do the job, time can be a factor. “If those resources can better be used in other areas when markets and/or opportunities are hot, they will have it outsourced to a company like us,” he says. “If commodities are in a down cycle, more than likely they will do it themselves, unless they don’t have qualified welders.
“Often times we send a supervising technician/welder with the help of their own maintenance people, which helps keep the cost down,” McChrystal adds.
When selecting among service providers, recyclers will want to consider how long they’ve been in business, whether they offer emergency service and the warranties offered. Recyclers also should ask for references, Kuhns says.
COST CONSIDERATIONS
Recyclers can chose between OEM (original equipment manufacturer) parts or having steel cut to match the replaced parts’ size and thickness.
“If the reline work being done is with OEM parts, the end result will be a baler that is back to its original spec,” according to McChrystal.
“Some companies look to save money by cutting steel matched to the original size and thickness,” he continues. “If this is the case, they should make sure the steel is the same quality as what was originally installed, which in most cases is an abrasion-resistant (AR) 400 or 500.”
Kuhn advises purchasing machined liners directly from the manufacturer, as they will be milled to the required dimensions.
“For older units with nonmachined boxes and right-angle liners, AR plate can be purchased from local suppliers and cut on-site to fit the baler,” he says.
While the size and brand of baler dictate reline costs, McChrystal says, full relines typically range from $60,000 to $100,000 and can take from seven to 10 working days to complete.
Kuhns adds that half of the cost of a reline typically is labor.
“Balers that are conveyor-fed will have a fixed hopper that needs to be removed in order to remove the ram,” he says, noting that removal of the hopper, including removal of conduit, wiring and other devices, can take two days. Reinstallation of these items would take two days as well.
“The typical amount of time required to perform a full reline on a two-ram baler with a trained crew working 12-hour days is 10 to 11 days on a standard baler and six to seven days on a hinged-wall unit,” according to Kuhns.
Sponsored Content
Labor that Works
With 25 years of experience, Leadpoint delivers cost-effective workforce solutions tailored to your needs. We handle the recruiting, hiring, training, and onboarding to deliver stable, productive, and safety-focused teams. Our commitment to safety and quality ensures peace of mind with a reliable workforce that helps you achieve your goals.
He adds that companies such as International Baler offer balers with a hinged rear wall that allows the mine and side rams to be removed and reinstalled in a matter of hours rather than days.
Recyclers also may consider rebuilding cylinders and pumps, McChrystal says, and replacing warn parts in the wire tier.
Kuhns adds that rebuilds of remaining components should be necessary only as they fail.
RELINE OR BUY?
Recyclers eventually may find that a reline doesn’t make sense and that a replacement baler is warranted.
McChrystal says damage to the baler’s subflooring, cracks in the baler or its frame or bowing of the shear beam can be signs that a recycler is better off replacing a baler.
Kuhns agrees, saying, “Once the frame of the baler begins to fatigue, stress cracks begin to appear and/or the main system components become obsolete, it is time to consider replacement.”
To help ensure the longevity of a recycling operation’s baling equipment, he advises, “The best thing a customer can do is to regularly test the hydraulic oil for contamination and change it when necessary. Dirty hydraulic oil will cause cylinder, pump and valve damage. A typical cylinder for a two-ram baler can cost as much as $70,000 and will require six weeks to build. The cost of changing oil is a very good insurance policy.”
Get curated news on YOUR industry.
Enter your email to receive our newsletters.
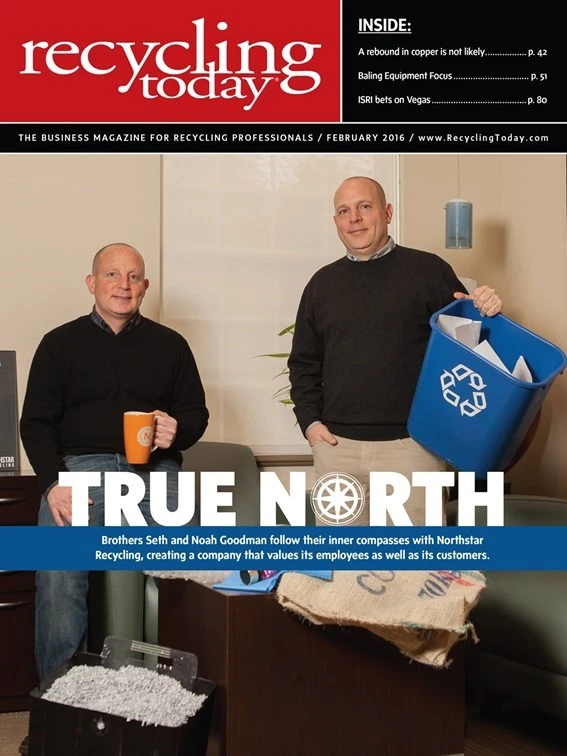
Explore the February 2016 Issue
Check out more from this issue and find your next story to read.
Latest from Recycling Today
- Toppoint Holdings expands chassis fleet
- Lego creates miniature tire recycling market
- Lux Research webinar examines chemical recycling timetables
- Plastics producer tracks pulse of wire recycling market
- Republic Services, Blue Polymers open Indianapolis recycling complex
- Altilium produces EV battery cells using recycled materials
- Brightmark enters subsidiaries of Indiana recycling facility into Chapter 11
- Freepoint Eco-Systems receives $50M loan for plastics recycling facility