Nucor Steel is the second largest steel company in the U.S. Since forming, the company has led the charge of the electric arc furnace (EAF) steel mini-mill sector as it gains market share from integrated steel mills.
However, acute problems in the steel industry have hammered both mini-mills as well as the integrated steel industries. In an exclusive interview, Dan DiMicco, president and CEO of Nucor, Charlotte, N.C., talks about the dynamics of the steel industry, and steps Nucor is taking to grow during these difficult times.
Q: With steel industry capacity going off line, do you see some of these shuttered facilities restarting when steel markets improve?
A: That is literally the $100 million question. I believe you will see a mix. I believe you will see some facilities remain shuttered, and I believe you will see some restarted. What will determine that will obviously be the marketplace number one. And number two will be the equipment available in those facilities. How recent and up to date is the technology? What is the cost to get it updated? Really, we have a major issue in our industry globally.
Worldwide, we have global overcapacity that is forcing situations to exist where really there are no highly profitable steel companies. And when I mean no highly profitable steel companies, I mean companies consistently earning their cost of capital at a minimum. Nucor may be one of the few. There may be one or two more. It is a major issue worldwide, not just in the United States.
Should some of this capacity stay off line? Absolutely. The more the better. But there will be some facilities out there that have been constructed the last five to 10 years that have the latest technology that probably should be restarted at some time at the expense of operations that have not proven themselves to have the best technology. Sometimes facilities shut down not because of technologies but because of the business acumen of the management—how they ran their business; how their labor and management relations were. Did they take care of their customers? And so on.
There are a variety of reasons for the shut down. I believe the facilities with the latest technologies will come back on stream at least in the United States.
Q: Do you see significant consolidation coming to the United States?
A: Bigger isn’t always better. Corus (a combination of British Steel and Dutch steelmaker Hoogovens) would tell you that right now. They are going through a lot of pains associated with being bigger, although it seems like they are getting a handle on things.
As far as consolidation, what we are seeing is worldwide there is an overcapacity of, depending on whom you listen to, 150 million to 300 million tons. And all that overcapacity is outside North America. North American steel producers cannot at the present time produce all the steel that is needed in our marketplace. The reason why is that quite honestly the bulk of the industry has not been able to earn its cost of capital to justify our reinvestment.
We have 30 to 40 million tons of dumped steel coming into the United States from overseas because of the overcapacity that exists. At current prices you can’t justify making further investments, which is really sad because it ought to be a great opportunity for companies like Nucor to continue to grow with the latest technologies, to be the most environmentally friendly, the most energy efficient, the most productive. But because of market conditions you aren’t able to now.
The consolidation globally is taking place ahead of the United States, only in the sense that there are these mergers going on. There are some rationalizations coming from that. But they have situations over there that have allowed them to do that.
Principally the anti-trust laws overseas, whether in Europe or Asia, are nowhere near as stringent as in the United States. The United States has the most stringent anti-trust laws by far. And so bringing companies together to form these large steel companies it’s very difficult for those things to happen in the United States. It would take very special circumstances to allow that to happen. Worldwide the industry is extremely fragmented.
I support 110% what people in other parts of the world are doing to consolidate and hopefully to rationalize permanently because there is this excess capacity, all outside the United States. Be it Russia or Eastern Europe, or Brazil or Japan. All these places have much more capacity than they can consume internally. And the technology they utilize and the productivity and efficiencies they run at are no better than what we have in the United States at most of our best operations, whether they are at Nucor or even at the integrated plants that have modernized over the years.
Q: With the present administration, is more consolidation possible?
A: We are hopeful that the administration will work to allow that to happen because this is a global issue. Our anti-trust laws are important for domestic issues. But when you have a global marketplace, you need to allow the U.S. producers to be able to compete, and consolidation will be an important part of that process. But also what our government needs to do is create a fair and level playing field for steel. I won’t comment on other products, but it is way out of whack for steel, as evidenced by the fact that virtually every time we file a trade suit we win.
Q: Nucor was a party to a suit just recently for hot rolled steel.
A: Preliminary findings on a variety of steel products. Nucor is a relative newcomer into this trade issue. But we did it first on beams at our Nucor Yamato joint venture, working with Chaparral and Northwestern, and won handily. The duties were assessed against Japan and Korea. Now we are joining with other mini-mills and integrated mills with a hot-banded sheet suit, in which the preliminary findings are very much in our favor. My point here is that every time we say, “Hey they are breaking our trade laws,” [it turns out] they are dumping illegally in our country.
We go to the courts; we put the facts on the table. Forget about the rhetoric you hear from the EU and Japan. Of course they are going to say the things that they do about marketplace. They survive by shipping their own incremental tonnage into our country and North America. They would be foolish not to fight. We understand it. It doesn’t make them right.
We find that when we have the facts presented and work through legal challenges with the ITC (International Trade Commission) and the Department of Commerce, we are proven to be right and they are proven to be dumping illegally into our country and North America.
What we need our government to do is put in place a trade law system that is proactive and not reactive. We know the process when it starts. We know what it looks like. You don’t necessarily need to have it stare you in the face. This is the process that is initiating. The prices are going down, the volumes are going up, based upon imported numbers. Hey, we are headed toward the same direction. Our government needs to put in place an early warning system and needs to allow the process to happen more rapidly. All this is WTO (World Trade Organization) consistent.
Canada has a system now. They have an early warning system through import licenses they issue. Also, it doesn’t take them more than six months for a ruling. It takes us a year and a half, sometimes two years before things are taken care of. If our government would do that . . . we aren’t asking for subsidies, we aren’t asking for handouts, we aren’t asking for loan guarantees. You put together a level playing field for us and take away their ability to dump their countries’ products, we will be able to compete worldwide and it will force the consolidation and rationalization (the shutting down of capacity) of facilities worldwide, to get rid of the excess capacity because they won’t have anywhere to send it. Right now the Europeans and Japanese have these under-the-table agreements that in this country would be illegal, not to dump in each other’s backyard. We are fearful that if we would do something like that . . .
Excess capacity is coming in from Russia, Korea and [other parts of] Europe. Russia would have nowhere to move their material except their own markets, and they don’t want to do that. So they fight like hell. It’s understandable but it doesn’t make it right. And it doesn’t make it fair, and it doesn’t make it legal. So this is a major issue for our government. This is where they should step in. This is a proper role of government—to create a fair and level playing field. We aren’t asking for any handouts, even though the Europeans have all the legacy costs forgiven by the government and paid for by the taxpayers where these consolidations take place. They have that advantage. We can still deal with that if we have a level playing field. We are the most efficient market in the world.
Q. Are there positive signs out there in the North American industry?
A: I think there are signs. You have to say the industry and the manufacturing sector are in a recession. Take a look at profits of manufacturing, including high-tech manufacturing, not just basic industries like steel. Earnings are terrible. [But] there are some improvements in the economy. We see construction has picked up a little bit. We see consumer confidence and we see the index of purchasing managers starting to turn a little bit. We have the Federal Reserve doing things to turn the economy around. But make no doubt about it, we are in a recession in manufacturing. We are hopeful there will be a turnaround in the second half. How much better? I was reading the Conference Board on the GDP and they are predicting 2.6 for the first quarter and we came in at 2. They are showing 5%, 3% to 5% for the year. So I certainly hope their predictions are accurate.
Q: Do you see ferrous scrap processors being able to continue providing the scrap needed as a raw material?
A: Absolutely, there is no shortage of scrap. There is no shortage of quality scrap. Not only here, but worldwide. What is happening is other areas of the world are becoming exporters. There is no shortage of prime grades. You can’t exclude the fact that people are using HBI and pig iron to supplement. And that will continue. There is plenty out there. I don’t see the usage increasing dramatically.
Q: As far as energy costs, what can Nucor do to offset the significant increases there?
A: Firstly, it isn’t just the mini-mills that are being impacted. Integrated mills also have been hurt. They are big consumers of natural gas and they have been hit hard.
There are a number of main drivers for the problem, including market manipulations by utilities and powerbrokers and screw-ups by the politicians. Further, California is sucking power from neighboring states, dragging the whole West Coast into the problem. If you take a look at really the main drivers, it has been natural gas.
Our company is very energy efficient compared to other types of integrated processes, although we still consume a lot of power. Our flat rolled operations consume a lot less gas than an integrated plant because we use a thin slab caster to put into a tunnel furnace. We don’t use the same volumes of gas. Our operations are inherently more efficient. But we still have seen an $8 to $10 per ton average hit because of natural gas and natural gas affecting electricity prices.
That will be cut in half probably with the pricing we see now for natural gas. As far as conservation goes we are constantly working to minimize our energy consumption in our furnaces, in our electric furnaces, in our reheat furnaces.
One of the biggest things people can do in our industry is hot charging, where you take the material right off the casting machine while it is still red hot and put it right into the reheat furnace and then roll it. We do it at our sheet mills because they come right off the caster into a tunnel furnace into the mill. And a lot of our bar mills and beam mills do as much hot charging as the scheduling allows. The more that you can do you can save two or three dollars a ton in energy consumption.
But other than that we are pretty much stuck with the fact that we consume electricity in our arc furnaces. The good news for Nucor plants is we have long-term contracts in place for electricity, so our impact there is minimal.
Q: Is your company still using David J. Joseph as your exclusive buying agent?
A: David Joseph is basically our exclusive buying agent. We do buy pig iron on the open market. We have a reverse auction that we run. And many times David Joseph will be the supplier of pig iron, but also other people will. Occasionally, the general managers will do some buying on their own to keep their fingers on the market. We don’t discourage that.
But, when you are consuming more than 11 or 12 million tons of scrap a year, you would have to have a tremendous increase in the number of people involved. And, we would have to bring the people in the buying side and the logistics side. We have a 30-year relationship with David Joseph. And they have done a great job for us.
Where they really benefit us is on two fronts. One way they benefit us is by buying the volume that we need for all of our operations around the country. You couldn’t do it more efficiently than they do. You could always have one plant buying a little bit lower. Their commission is very low on a per ton basis.
The other thing they do is manage logistics. The logistics of moving scrap from overseas or anywhere to the United States to our operations is huge. They have their own rail cars, and they have a very good system to manage logistics. Those two things are obviously the two most important things. Getting it at the best price and getting it delivered in a timely fashion. They do an excellent job for us. It couldn’t be done better.
Q: Do you see Nucor going more directly into the scrap business?
A: Absolutely not.
Q: What can you say about the company’s future plans?
A: Nucor’s growth strategy going forward is three fold. One, focusing on our existing business and maximizing the profit margins by maximizing the revenues per ton by getting it to highest value product that we are capable of and then stretching to go even further. Even in the record year we had last year we were quite frankly running on five of eight cylinders. Nucor’s potential from an existing operations standpoint is tremendous.
Our second strategy is to grow through acquisitions, which is new. We have already acquired our first steel company, from Sumitomo. It is up in Auburn, N.Y. It produces about 430,000 tons a year of bar product. The mill produces a similar mix to what we do with our four bar mills. It gives us an excellent geographic position in the Northeast.
The third growth strategy involves the implementation of new technologies, particularly disruptive and leapfrog technologies. The one we are working with now is called cast strip. We are constructing a direct sheet casting from liquid directly to sheet.
That process is known as cast strip. That will allow us to get back into greenfield opportunities in flat rolled where we have major cost advantages, and even some quality and technologies advantages over existing production techniques for producing cold rolled quality or cold rolled equivalent material.
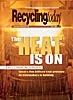
Explore the July 2001 Issue
Check out more from this issue and find your next story to read.
Latest from Recycling Today
- Steel Dynamics cites favorable conditions in Q1
- Hydro starts up construction in Spain
- Green Cubes unveils forklift battery line
- Rebar association points to trade turmoil
- LumiCup offers single-use plastic alternative
- European project yields recycled-content ABS
- ICM to host colocated events in Shanghai
- Astera runs into NIMBY concerns in Colorado