With consumers demanding ever-increasing levels of quality from the scrap metal industry, there is an increasing need for accurate and fast metals analysis. There is a wide range of requirements for chemical analysis, from the need to measure chromium and nickel at concentrations which can be in excess of 20 percent, to very low levels of sulfur, phosphorus and other elements.
In addition to the need for the high accuracy and precision of systems designed for quantitative analysis, there is also a need for analysis of a different type – an ever-present need to rapidly identify what material is present at any particular place. This is referred to as on-site semi-quantitative identification.
There are many methods of semi-quantitative and qualitative analysis that have been tried over the years.
NON-INSTRUMENTAL METHODS
One of the simplest methods is the spark test in which the composition of the metal can be deduced by looking at the color and shape of sparks produced when the sample is ground with an abrasive wheel. This can be very useful for steels, but is of limited use on other alloys. It also requires a highly experienced operator to interpret the results.
Another method that has found favor in some organizations is the use of chemical spot test kits. In this system a chemical or series of chemicals is dropped onto the surface of an alloy. The color change resulting from the chemical reaction between the alloy and the reagent can indicate the presence or absence of certain elements in the alloy. Again, the type of alloy that can be tested is rather limited, but the cost of this type of test is extremely low and can give good results in the right circumstances.
SPECTROMETRY
It is generally agreed that the most useful type of on-site identification instrument is one that uses some form of spectrometry. There are two basic methods to choose from:
Optical emission (OE) spectrometers, which make an arc or spark to the sample and analyze the light given off, and X-ray fluorescence (XRF) spectrometers that bombard the sample with X rays and analyze the X-rays that are re-emitted.
Both methods have been and are used in the on-site role. Both have their particular advantages. XRF analyzers can give very high precision results and are especially good at the high level alloying elements such as chromium and nickel. They are not as good at the light elements such as carbon and silicon. They also have the drawback that most of them use a radioactive isotope as the source of X-rays, and so they require particular safety precautions.
Optical emission spectrometers can cope well with the light elements and have no radioactive hazard. The precision of the results they give on higher-level element concentration is not usually as good as XRF, but the results are achieved more rapidly.
To tackle the on-site identification job, any instrument must meet the following requirements:
• It must be portable and come to the sample, not the other way around.
• It must be simple to operate by
non-technical personnel.
• It must be rapid (a few seconds
per test).
• It must be readily available and not require lengthy setting up or
calibration.
• It must be able to operate on a wide range of sample surface conditions.
• It must cover a wide range of
elements and concentration ranges. Accuracy and precision must be sufficient to identify the materials encountered on-site.
TRADITIONAL METHODS
Two methods of on-site identification have been available for many years, the spark test and the visual spectroscope. These have been used successfully but both suffer from serious drawbacks: although easy to operate they require the user to have an immense amount of experience to get good results, and they are severely limited as to the range of materials they can cover.
The first development in on-site spectrometry was to employ the technology of the laboratory spectrometer and repackage it into a mobile form.
Many attempts have been made to use optical emission spectrometers on-site, with varying degrees of success. In a typical laboratory OE spectrometer, an electric arc or spark is struck between the sample and an electrode. Light from this spark is directed into the spectrometer through a fine slit. It then falls on a diffraction grating which splits the light into its constituent wavelengths and at the same time reflects it. This reflected spectrum is then directed onto a series of photomultiplier tubes placed so that they pick up an individual wavelength produced by one of the elements in question. To measure ten elements, at least ten detectors are needed.
The current produced by each photomultiplier tube detector is proportional to the amount of light falling on it, and so a measure the intensity of each different wavelength in the spectrum measured can be obtained. A computer is used to convert the currents produced by each of the detectors into element concentration readings, which are then displayed on a monitor or printer.
The breakthrough in using these instruments on-site came with the advent of optical fibers. In a laboratory instrument the sample needs to be brought to the instrument so that the light from the arc or spark can be directed into the spectrometer. By using optical fibers, the arc or spark can be produced remotely from the spectrometer, and the light can be channeled along the fibers into the instrument.
By using this technology, along with the smaller computers that became available, manufacturers were able to package spectrometers into a size that could be put on wheels and used as a mobile spectrometer.
This type of instrument has become very popular because it represents a great advance over the traditional visual methods, but they cannot meet all the requirements of portability and robustness desirable for on-site spectrometers.
The problem with these types of instruments is threefold. For one, the technology they use is rather fragile. The large number of components in the spectrometer means that there is the possibility of mechanical shock causing misalignment of the optics. Also, the fiber optic is fragile and prone to breakage by bending or by crushing (e.g., with a forklift truck).
Secondly, because of the size of the optics, the instruments are rather large and heavy (around 440 pounds). This means they are mobile but not portable.
The third problem they face is that they are not easy to operate. They require frequent re-calibrations because of shifts in the optics.
THE CCD REVOLUTION
In recent years there have become available a number of solid-state, light sensitive semi-conductor devices. These Charge-Coupled Devices (CCD) have, so far, been primarily used to capture the image in such devices as fax machines and video cameras. They are stable, compact, robust and relatively low cost. They offer an ideal solution to the measurement of a spectrum in an on-site spectrometer.
In a typical CCD based spectrometer, the array of photomultiplier tubes is replaced by a single device a little more than an inch long, which can capture the spectrum projected onto it and produce a video image that can be digitized and processed by a computer.
The spectrometer using this technology is much more compact, enabling the optical system to be housed in the hand-held portion of the instrument. In this way, the spectrometer is brought to the sample without the need for fragile fiber optics. Also, since the spectrometer is measuring the complete spectrum, the unit does not need to have constant re-calibrations. Another benefit of measuring the complete spectrum is that the instrument can recognize what type of material is being tested and can select the appropriate calibration from its memory.
All of this means that a CCD based spectrometer meets the requirements of the on-site application in almost every respect: it is very portable, it is very simple to use and it is always available without complicated setting up. Instruments using this technology have only been available for a few years, but they are already capturing about 25 percent of the world market.
THE FUTURE
The technology that has enabled the production of very compact spectrometers has so far only really been used in the identification role. Future developments will focus on improving the analytical performance of these instruments, and the time is not far away when they will perform at least as well as conventional laboratory spectrometers.
Work is also proceeding on light sources other than arc or spark. For instance, the use of lasers has already shown promising results. Coupled with the new spectrometers, this will make it possible to quantitatively analyze metals on-site, without having to take samples, transport them to a laboratory, prepare them for analysis, and finally produce the analytical result. This process will be replaced by a rapid test produced in-situ using an extremely small spectrometer mounted at the processing stage where the analysis is required. Samples will no longer have to be solid, flat and clean, but may be liquid metal, unprepared ingots, rolled bar, or taken from any location where an analysis is required.
The author is president of Arun Technology Inc., Dearborn, Mich.
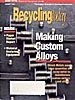
Explore the August 1997 Issue
Check out more from this issue and find your next story to read.
Latest from Recycling Today
- Sortera Technologies ‘owning and operating’ aluminum sorting solutions
- IDTechEx sees electric-powered construction equipment growth
- Global steel output recedes in November
- Fitch Ratings sees reasons for steel optimism in 2025
- P+PB adds new board members
- BlueScope, BHP & Rio Tinto select site for electric smelting furnace pilot plant
- Magnomer joins Canada Plastics Pact
- Out of touch with reality