
Carbon emissions reduction has taken center stage for steel and aluminum producers over the past few years as countries around the world look to reduce their carbon footprints throughout the next two to three decades to combat climate change.
Aluminum companies, particularly, are looking for ways to increase their production of low-carbon aluminum (LCA) in their quest to reduce their emissions. For example, Norwegian aluminum producer Norsk Hydro recently decided to sell its rolling business worth $1.64 billion to divert funds toward its long-term sustainability goals, which are outlaid in its LCA strategy.
Like Hydro, many companies are investing in low-carbon technology to recalibrate their production methods, with some of the bigger companies already finding success with their rollouts of LCA products. The question arises, therefore, why now?
The answer perhaps can be found in a study titled “The Quest for Low Carbon Aluminum: Developing a Sustainability Index” by Subodh Das, Ph.D., founder and CEO of Phinix LLC, Clayton, Missouri, which is summarized in this article.
Das notes that in 1995, the global aluminum industry produced roughly 364 million short tons (363.2 million metric tons) of carbon-dioxide equivalent emissions (CO2Eq) at a rate of 16.5 tons of CO2Eq per ton of primary aluminum produced. This figure represented about 1 percent of global emissions that year. At that time, actual aluminum production stood at roughly 22 million metric tons, or 24.25 million short tons.
By 2018, aluminum production increased to 64.4 million metric tons per year (nearly 71 million short tons) with a footprint of roughly 12 tons of CO2Eq per ton. The global benchmark for LCA is 4 tons of CO2Eq per ton of aluminum produced. Das says the Aluminum Stewardship Initiative (ASI) certifies LCA at less than 8 tons of CO2Eq per ton of aluminum. Still, experts consider this as too inclusive a benchmark for LCA.

Finding solutions
Smelting is viewed as the biggest culprit for adding to CO2 emissions in the aluminum-making process since it requires the most power, which often is fueled by coal/fossil fuels. A popular solution in the industry is using hydropower stations to provide electricity to smelters, effectively lowering the carbon footprint. Solar or wind farms also are being considered as replacements for fossil fuel-based electricity.
Another vital step in lowering CO2 emissions is recycling. By producing secondary aluminum from scrap, the process to mine and refine bauxite to alumina is shortened, thereby cutting emissions. Because aluminum is infinitely recyclable, it is fundamentally possible to achieve a 100 percent recycling rate.
Secondary production requires significantly less energy and can offset the carbon footprint of primary production. However, this benefit is lost when end-of-life aluminum products do not find their way back into the recycling loop. Aluminum dross, a popular secondary grade used for recycling, has been heading to landfills for years. It is only recently that the industry realized the significance of dross as a source of secondary production. According to estimates, dross makes up around 5 percent of total production and can yield almost 80 percent aluminum. However, the challenge in recycling dross lies in its production of salt slag as waste.
Building LCA capacities
The North American aluminum industry successfully cut down emissions by 85 percent after it shut smelters built from 1940 to 1960.
In Asia, China Hongqiao Group, one of the largest producers of the metal, has moved one-third of its capacity out of China’s Shandong province to Yunnan, which is filled with hydropower stations, to produce green aluminum. India’s Hindalco also is planning to set up a 24-megawatt solar power plant at its smelter in Odisha, India, to replace its coal-captive power plant to achieve a lower carbon footprint.
Other companies are aggressively pursuing LCA initiatives:
- Rio Tinto launched the industry’s first certified LCA product in 2016, Renewal, which is produced at 4 tons CO2Eq per ton or lower using hydropower at its Canadian smelters. In 2018, Rio Tinto and Alcoa formed a joint venture named Elysis, touted as a zero-carbon aluminum company. In 2019, Elysis produced its first commercial batch of aluminum to supply Apple. It is currently setting up a technology center in Quebec to industrialize the technology by 2024. The zero-carbon concept is based on using a substitute for the carbon blocks used to separate aluminum chemically. The company has not disclosed which material it is using, but it is essentially an inert anode and cathode used in the smelting process.
- UC Rusal launched its own LCA brand, Allow, in 2017, that features a carbon footprint of less than 4 tons of CO2Eq per ton for the smelting process’ direct and indirect emissions, while the full-scope footprint of Allow from ore to casting is less than 8 tons of CO2Eq per ton of aluminum produced. Rusal has been testing electrolytic cells with inert anodes since 2019 and plans to commercially launch a carbon-free product in 2021 using this technology. It is expected to reduce the product’s footprint to a level of less than 2 tons of CO2Eq per ton as well as significantly reduce the cost of production. The technology and timeline for launch put Rusal in direct competition with Elysis.
- Norsk Hydro has been focusing on LCA over the past two years and has launched two such products— Hydro Reduxa and Circal. Reduxa is produced using hydropower at the company’s plants in Norway and is available as extrusion ingots, sheet ingots, foundry alloys and wire rod, with a carbon footprint of less than 4 tons CO2Eq per ton. Circal, or Hydro 75R, uses a minimum of 75 percent recycled content, which is usually postconsumer scrap. In March, the company also spoke of using recycled aluminum during the primary production process at its smelters in Norway. It is currently testing the concept at its Hoyanger plant.
- Alcoa has introduced a new product line, Sustana, that includes three products: Ecolum, EcoDura and EcoSource. Ecolum is a primary aluminum brand produced at the company’s largely hydropowered smelters. The product’s total carbon footprint, including bauxite mining and refining, is less than 4 tons of CO2Eq per ton produced, making it a top contender. EcoDura aluminum is made with a minimum of 50 percent recycled content with a footprint of less than 2.5 tons of CO2Eq per ton. EcoSource is the company’s low-carbon alumina brand, with less than 0.5 tons CO2Eq per ton produced.
- Emirates Global Aluminium (EGA) confirmed in January of this year that it will use solar energy sourced from Dubai Electricity and Water Authority’s solar farm, which can supply roughly 560,000 megawatts of power, to produce aluminum. EGA plans to sell this product under the name CelestiAl.
- Century Aluminum announced the launch of its LCA products under the line Natur-Al in 2020. These products are processed at the company’s plant in Iceland, which is ASI certified and uses renewable energy to source its power. This range of aluminum is produced at less than 4 tons of CO2Eq per ton as verified by external inspections.
LCA also has caught the attention of several traders:
- The London Metal Exchange (LME) has put sustainability at the forefront of its metal trading platform. It initially planned to roll out a second aluminum contract and trading platform for green/low-carbon production, apart from the LME primary aluminum contract. However, this notion was met with opposition from companies like Hydro and Hindalco, which said a second contract would weaken the LME’s efforts to promote sustainable production by commoditizing LCA. They believe that this would lead to a generalized method of representing carbon footprint. Instead, LME plans to roll out LMEpassport, a digital register that will store certification and other carbon metrics related to specific batches of aluminum. This would be the first step to labeling green aluminum in an LME-approved market. Both LME and non-LME listed brands will be given access to the passport data to ease trading.
- Considering the growing demand for LCA from the automotive and packaging industries in the EU, commodities trader Trafigura Group Pte. Ltd., Singapore, launched a $500 million financing platform for LCA production, which is touted to be an industry first. The funds will be provided by Natixis and Rabobank at a preferential interest rate to Trafigura, which will be used to pay premiums for green aluminum. Trading houses expect LCA to trade at a premium within the next two years, especially in the European Union and U.S. However, with most global production still being powered by coal, these premiums are expected to be confined initially to these two regions, alongside the standard primary aluminum premiums.
- Harbor Aluminum, Austin, Texas, announced the launch of the world’s first green aluminum premium, the US MW P1020 Green Aluminum Spot Premium, in October 2019. According to the company, low-carbon P1020 in the form of ingot, T-bar and sow is expected to be around 4.7 million metric tons in 2020, which makes up around 43 percent of global P1020 production ex-China. The specification for the product is 99.7 percent high-grade aluminum with 4.5 tons or less CO2Eq per ton of aluminum produced. Carbon calculations are done according to standards prescribed in IAI Scope 1 and 2 on products traceable to a single smelter.
Many industry experts say they believe switching to renewable sources for electric power is not the only change that the aluminum industry must undergo for sustainability. Rather, a more holistic approach is prescribed, which accounts for factors such as mining and refining of bauxite and alumina as well as byproducts, such as spent pot lining and carbon anodes and cathodes from the electrolysis process and salt slag from recycling dross. A new approach of recycling bauxite residue in cement mixtures has been adopted by Rio Tinto and Hindalco.
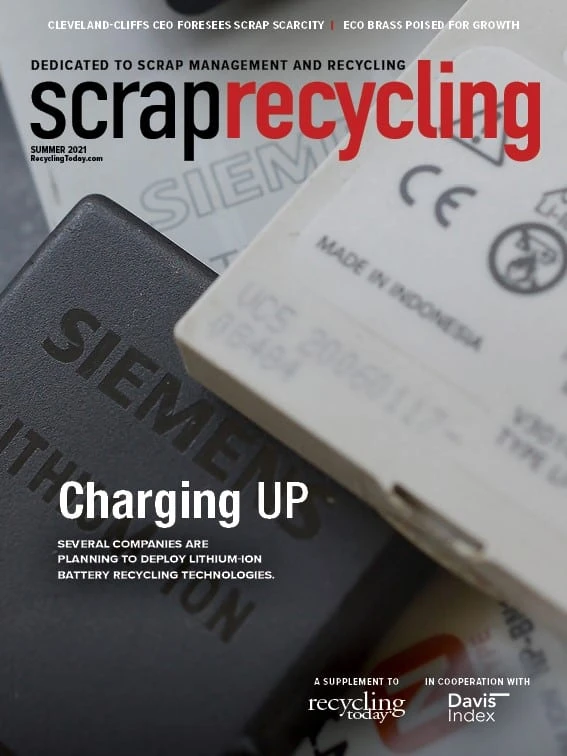
Explore the Summer 2021 Scrap Recycling Issue
Check out more from this issue and find your next story to read.
Latest from Recycling Today
- New recycling grant program launches in Massachusetts
- Tire Recycling Foundation names executive director
- Dock 7 named 2025 Exporter of the Year at New Jersey International Trade Awards
- Waste Connections reports ‘better than expected’ Q1 results
- Commentary: How EPR is transforming the packaging industry
- Acerinox names new North American Stainless CEO
- Greenwave closes 2024 books with red ink
- Steel Dynamics nets $217M on record shipments