The Berea, Ky., facility of Alcan Aluminum Corp. is the final destination for a large percentage of America's used beverage cans.
Berea, Ky., is a hotbed of recycling. It’s a town of 10,000 people that recycles more than ten billion aluminum cans each year.
No, the residents of this college town don’t subsist on a diet of soft drinks and beer. Rather, Berea is the place where the recycling loop is closed for as many as 11 billion of the used beverage cans (UBCs) recycled in America.
A Berea manufacturing facility constructed and operated by Alcan Aluminum Corp., Cleveland, melts down 11 billion used aluminum cans each year. It is one of five of the company’s global recycling facilities, which combine to melt a total of 24 billion UBCs each year—a number equivalent to roughly 40 percent of all UBCs recycled in the U.S.
The receiving dock in Berea accepts cans from most of America’s 50 states, where recyclers have collected, sorted and baled UBCs at county material recovery facilities, rural collection centers, small retail yards and large scrap facilities. The cans provide a steady stream of metal to be processed and recycled.
True recycling, of course, doesn’t occur until a collected item is made into a new product. So while UBCs are, in one sense, recycled in curbside bins and across scrap yard scales throughout the country, in another sense they aren’t recycled until they reach the place where they will be melted down and turned into raw aluminum ingot or billet.
For many of these UBCs, that recycling loop is completed in Berea.
Specializing in UBCs
The Alcan Berea plant has been operational since 1989, and from the beginning the facility was designed to specialize in the production of ingots made from UBCs as melting stock.
Throughout the 1990s, the plant’s workforce of more than 100 people has increased its annual production of aluminum ingot each year. The current production rate results in 200,000 tons of aluminum ingot from melting 11 billion cans—or roughly 18 percent of all UBCs recycled in America.
Alcan is currently investing millions of dollars in the facility to increase the plant’s production capacity to 300,000 tons of ingot, as well as to guarantee that strict environmental controls remain in place.
The Berea plant is one of several facilities Alcan operates in the state of Kentucky, but it is one of only two Alcan-owned melting facilities in North America dedicated exclusively to the recycling of UBCs and process scrap from can plants.
According to Alcan’s Dan Duclos, plant manager at the Berea facility, the Berea plant is "the world’s largest dedicated UBC recycling plant."
Many of the ingots produced in Berea are shipped to Russellville, Ky., to the Logan Aluminum Inc. plant co-owned by Alcan. That plant makes beverage can sheet and other aluminum products.
Duclos says that for eight of the last nine years, the Berea plant has been the Supplier of the Year to Logan, an achievement he credits to all of the plant’s 114 employees. "We have basically the same equipment as the other [supplier] plants. It’s the people who make the difference," he comments.
With both an impressive output by volume and an admirable track record for quality, Alcan’s Berea facility is a key factor in the company’s plans to be a market leader in both aluminum can sheet production and in UBC recycling.
Step By Step
Alcan’s Berea plant is divided into three main areas, according to Duclos:
• Cold Metal operations, which includes UBC receiving, de-baling, contaminant removal and shredding
• Hot Metal operations, which involves a first heating step of "de-coating" (removing paint), followed by melting and alloying
• The Casting Center, where hot metal is put into holders, purified, cast, analyzed and shipped out as ingots.
For the most part, recyclers who make shipments to Berea do not want to hear from the plant’s receiving area, at least not on an emergency basis. It is here where incoming bales are inspected.
Areas of concern, according to Berea business unit leader Donnie Northern, include the presence of contaminants (most notably lead and plastic) and the presence of too much moisture. Both lead and plastics are unwelcome in the hot metal processes used by the plant. Alcan addresses this problem by removing the moisture and plastics in the de-coating process.
Unfortunately, it is the nature of UBCs and the millions of sources from which they come (virtually every American who drinks cola or beer) that some contaminants will make it past a visual inspection. For this reason, Alcan puts all of its melting stock through a multi-step process in the Cold Metal Area.
After passing through receiving, where moisture sampling is performed, bales are conveyed inside by a moving floor to a large de-baling machine that breaks the flattened cans away from each other (as well as from the baling wire wrapped around the bale).
Just in Time, All the Time |
This stream of crushed UBCs passes under a drum magnet that picks up any steel cans mixed into loads, as well as the baling wire fragments that emerge from the de-baler. A screening conveyor removes dirt and fines and air knives are used to remove heavy contaminants. The air knives carry cans from one conveyor to another using an air stream, while denser material falls into a reject hopper. The stream of UBCs then moves toward a surge hopper that controls how the stream is fed to two awaiting shredders.
The shredders are completely enclosed, keeping the decibel level low and helping to ensure that any dust produced in the process stays away from the rest of the plant.
Shredded aluminum leaving the shredder is conveyed into the Hot Metal Area of the plant, where the product is first sent through a de-coater that removes the paint. (Like the shredder dust, this byproduct is captured by a baghouse system that keeps emissions to well below state and federal limits.)
From the de-coater, the shredded aluminum heads into four melting furnaces that reach 1400 degrees Fahrenheit. The UBC shred is mixed with some primary aluminum and some remelt secondary ingot (RSI) before it is cast. The shredded UBCs make up more than two-thirds of the volume of most melts.
The molten aluminum flows down troughs into holding furnaces. From there it will be sent through a filtered purifying area and then cast. The direct chill casting area is configured to allow ingots of several different sizes to be made.
An Eye On Quality
Alcan is known to most people as a primary aluminum company, and a chart displaying activities at Alcan’s plants throughout the world shows a greater number of facilities with primary operations as opposed to recycling.
But the company is aware of the benefits that can be gained when recycled aluminum is used, with the most dramatic being a 95 percent reduction in the amount of energy needed to melt scrap aluminum versus producing primary aluminum from bauxite.
In terms of greenhouse gas emissions produced, minimizing emissions at recycling plants is also far less costly than what must be put in place at primary plants. The operation of recycling plants fits in with an "Alcan initiative relative to the reduction of greenhouse gas emissions," says Jeff Cruse, who is safety, health and environmental coordinator of the Berea facility.
The one detriment to the use of scrap aluminum is the potential for contaminants and imprecise metallurgy to enter the equation. On the positive side, unlike a secondary smelter melting many types of aluminum scrap, the Berea facility is accepting only UBCs and process scrap from can plants, so the chemistry stays within a narrow range.
But this UBC scrap enters the Berea facility from a number of sources from all over the continent, and quality must be monitored carefully.
Even with Alcan’s screening air knife system in place, contaminants can still cause problems if they are hidden within cans. Among the items that have been removed from the UBC stream are bullets, lead fishing sinkers, household batteries and hypodermic needles.
"The biggest issue is heavy metals," says Duclos. "And there can be no lead in can stock," he adds.
Should recyclers ever question how they fit into this quality picture—as well as the health and safety picture—they are welcome to come to Berea and see where the cans they collect are heading. "We have a program where suppliers come in to see our process and they can see why we ask for what we ask for," says Northern.
Similarly, Alcan managers have an audit process that allows them to visit some of their supplier scrap yards. The visits help the Alcan managers better understand the work recyclers perform to put together a clean shipment. "You see what they have to start with, and you can see that a lot of work has gone into it at their end," says Northern.
The Berea facility monitors its incoming scrap shipments, and the company has a system in place that provides both positive and negative feedback to UBC suppliers. "Moisture sampling is done, and a supplier will be penalized if the percentage is too high," says Duclos. He notes that water mixed with dirt can clog up the air knives at the plant, resulting in contaminants designated as "heavies" getting through to the shredder.
"Certain suppliers have been disqualified" after having repeat quality problems, Duclos notes, although there is a requalification program to give them another chance once corrective measures have been put in place.
Alcan’s multi-million dollar upgrade to its Berea facility should mean that the company will stay in the UBC purchasing game for some time to come, remaining an important end market for this key recyclable.
"The aluminum can is the only recycled package to more than cover its cost of collection and processing," says Duclos. In its promotional material, Alcan notes that the aluminum industry pays nearly $1 billion annually to recyclers for UBCs.
Often, the cost paid for a ton of aluminum cans is more than ten times what is paid for a ton of steel cans, with similar or greater ratios in place for glass and PET bottle plastic.
Duclos praises the Berea plant’s performance and the recognition it has received within Alcan for the quality of its ingots, including being supplier of the year to the Russellville plant and having enviable environmental and safety records. "There’s a lot of automation at a plant like this, but the human factor is critical. Our employees are the ones making the key decisions," he remarks.
As long as demand for aluminum cans is steady and the plant’s performance is enviable, the Alcan Berea facility should remain a key destination for UBCs for some time to come.
The author is editor of Recycling Today and can be contacted via e-mail at btaylor@RecyclingToday.com.
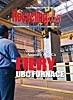
Explore the December 2001 Issue
Check out more from this issue and find your next story to read.
Latest from Recycling Today
- Green Cubes unveils forklift battery line
- Rebar association points to trade turmoil
- LumiCup offers single-use plastic alternative
- European project yields recycled-content ABS
- ICM to host colocated events in Shanghai
- Astera runs into NIMBY concerns in Colorado
- ReMA opposes European efforts seeking export restrictions for recyclables
- Fresh Perspective: Raj Bagaria