
The idea was to transform scrap automobile bumpers into artificial slate roofing tiles. But the process for actually doing so was not straightforward.
For help, the recycler turned to plastic additives—which are becoming increasingly sophisticated as more companies try to reuse commingled plastics. With additives and compatibilizers, recyclers can blend multiple materials without degrading their properties.
“People are looking for outlets for recycle streams that are very difficult to work with,” according to Mike Fulmer, product manager for plastic additives at Struktol Co. of America, Stow, Ohio, which has worked with the recycler.
For the recycler, residues left on the original parts created problems in the remanufacturing process, he says.
“In many cases, they still have paint on them,” says Fulmer, who could not disclose the name of the recycling company. “The ability to mix and disperse that residual paint … is a real issue for the compounder because it can clog filter screens in extruders. It can cause disruptions in physical properties. It can cause surface defects.”
A combination of lubricant technology and a homogenizing agent provided a remedy.
Such situations are often the reason why recyclers turn to Struktol. “It’s a very common type of project that we work on, where a customer is trying to find a use for a widely available feed stream,” Fulmer says. “People are looking for outlets for recycle streams that are very difficult to work with.”
A growing field
The challenges of recycling—particularly postconsumer recycling—have enhanced the demand for compatibilizers.

The role of a compatibilizer is to interact with the two polymers being blended to improve their interfacial adhesion. Compatibilizers operate using three general principles: molecular diffusion at the interface allowing for the polymer chains to become entangled, polar interactions between the two polymers or chemical reactions between chemical groups in the polymers.
Plastics compatibilizers have been used for decades, but demand for these products is growing.
“Most of the polymers or plastics we know were invented in the ’40s, ’50s and ’60s in the last century,” says Jose Torradas, a senior technical consultant with the DuPont Performance Materials division of DuPont, Wilmington, Delaware.
In the early 1970s, manufacturers started looking for plastics with unique characteristics that could meet specific challenges.
In the absence of new polymers, the industry looked at other ways to create materials. This included modifying, blending and reclaiming existing polymers.
Compatibilizers operate using three general principles: molecular diffusion at the interface allowing for the polymer chains to become entangled, polar interactions between the two polymers or chemical reactions between chemical groups in the polymers.
Most polymer blends are incompatible, Torradas says. As an example, polyethylene terephthalate (PET) and high-density polyethylene (HDPE)—two of the most commonly used plastics—don’t interact well if blended. The resulting product has poor properties and limited use. Other polymers, acting as compatibilizers, can solve the problem.
“In the recycling world, let’s say you’re recycling polyester [PET] bottles,” Torradas says. “That PET may have some contamination that comes from caps and closures. The closures of soda bottles are made from polypropylene (PP) or polyethylene [HDPE]. So, even though they sort them and separate them in the recycling process, sometimes the PET stream may end up with small amounts of contamination you have to worry about,” he explains.
If a company recycles that plastic without a compatibilizer, the contamination will create problems, and the final product won’t have good properties.
_no_words_fmt.png)
“So, what is done is to add a small amount of compatibilizers to make the two more compatible,” he says, “and then you’re able to make a final product that will have more acceptable properties for something else.”
Torradas acknowledges one of the challenges of developing compatibilizers for the recycling market is added cost. If a manufacturer wants to develop a unique blend of polymers for a high-performance car part, it typically can afford to pay more money to make those plastics compatible than a recycler who wants to reclaim old soda bottles.
Fortunately for recyclers, compatibilizers have been developed to blend unique combinations of polymers.
Kenrich Petrochemicals Inc.
Salvatore Monte, president of Kenrich Petrochemicals Inc., Bayonne, New Jersey, is involved in developing and marketing compatibilizers. He says the plastics recycling market is creating demand.

“Compatibilizers are needed because there is just so much you can do with mechanical cleaning and separating,” Monte says. “Many polymers just hate each other, and small amounts of fillers are considered contaminants and can destroy mechanical properties.”
Economics and sustainability are two major factors driving not only recycling but also the market for additional research into compatibilizers, Monte says.
“As the economic gap between the cost of virgin polymer versus recycled polymer narrows … recycling based on polymer cost alone is often not feasible, unless you move away from postconsumer recycling into postindustrial recycling, where higher-cost specialty polymers are used and where compounds containing combinations of conventional recycled polymers can produce better results,” he explains.
Other factors, such as regulatory and waste removal costs, also can make recycling a more viable option, he says.
Nexam Chemical
Lars Öhrn, chief marketing officer for Nexam Chemical, Lund, Sweden, which makes plastic additives, says his company makes products that can improve the properties of multiple kinds of polymers, including polyesters and PE.
“When polymers are processed, used and recycled, they lose functionality due to deterioration. The polymer breaks down into smaller parts,” says Öhrn, who describes some of his company’s offerings as chain extenders that reconnect the polymers.
As part of its Nexamite line, Nexam Chemical offers compounds in masterbatch form that help with the recycling of polyesters. Among the company’s newest products is Nexamite M921001 for PET.
“With Nexamite, we can rebuild the polymer and regain properties and quality. Nexamite connects the plastic parts and, with that, you improve processability, melt strength and mechanical properties.” – Lars Öhrn, Nexam Chemical
“With Nexamite, we can rebuild the polymer and regain properties and quality,” Öhrn says. “Nexamite connects the plastic parts and, with that, you improve processability, melt strength and mechanical properties.”
Struktol Co. of America
Fulmer says recyclers are increasingly turning to the plastic additives market.
Rather than simply offering compatibilizers, Struktol has taken a different approach toward addressing blending of different polymers. The company combines lubricants with homogenizing agents.
The addition of lubricants reduces viscosity, improves mold-release characteristics by lessening the likelihood of plastic sticking to a mold and creates better surface appearance when the recycled plastic is made into a new product, Fulmer says.
While some compounders have been separately adding lubricants to their processes, Struktol’s products eliminate that need because the lubricant already is added, making the process easier, he says.
Struktol’s homogenizers work like a “super glue” that bonds two or more incompatible plastics together, Fulmer says.
Development of improved homogenizing agents or compatibilizers is helping expand the ability to cost-effectively recycle plastic that used to go to waste.
The ability to use less-expensive raw materials helps overcome the added cost of using compatibilizers or homogenizers, he says.
“These types of lubricants and compatibilizers … really do open up the window of opportunity for these recyclers to use materials they might not have been able to use in the past,” Fulmer says.
For more information: DuPont, 302-774-1000, www.dupont.com, Kenrich Petrochemicals Inc., 201-823-9000, www.4kenrich.com, Nexam Chemical, 46-703-47-9700, www.nexamchemical.com, Struktol Co. of America, 330-928-5188, www.struktol.com
Get curated news on YOUR industry.
Enter your email to receive our newsletters.
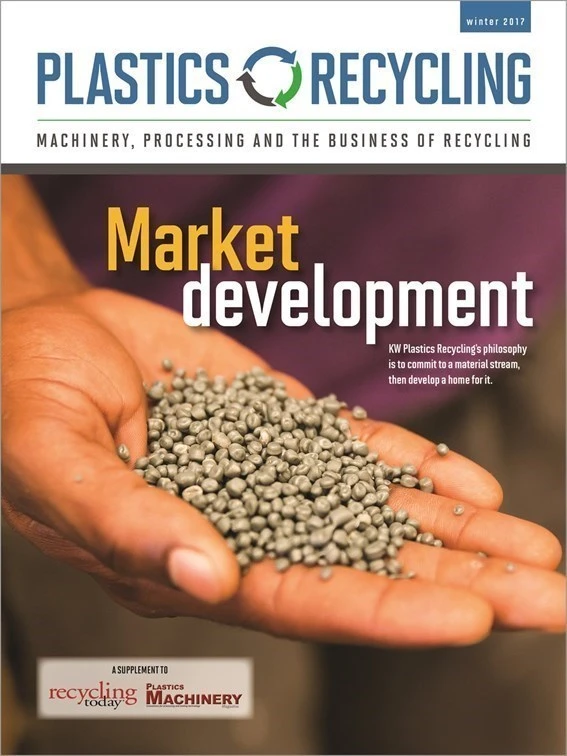
Explore the February 2017 Plastics Recycling Issue
Check out more from this issue and find your next story to read.
Latest from Recycling Today
- Toppoint Holdings expands chassis fleet
- Lego creates miniature tire recycling market
- Lux Research webinar examines chemical recycling timetables
- Plastics producer tracks pulse of wire recycling market
- Republic Services, Blue Polymers open Indianapolis recycling complex
- Altilium produces EV battery cells using recycled materials
- Brightmark enters subsidiaries of Indiana recycling facility into Chapter 11
- Freepoint Eco-Systems receives $50M loan for plastics recycling facility