_fmt.png)
Plastics recycling is on the mind of nearly everyone, everywhere, it seems, and getting better at it is the collective goal. The various parts of the supply chain are finding innovative ways to work together to close the loop.
Several technologies that are included in this issue were introduced at the triennial plastics industry trade event the K show, held in October in Düsseldorf, Germany. These are only some examples of how plastics recycling seemed to be gaining more significance during the show’s eight-day run. The undisputable centerpiece was the Careformance Recycling Center, where Erema recycled more than 30 tons of plastic scrap live. This was a recycling plant set up in the center of the fairgrounds, separate from Erema’s own booth. Using its Intarema TVEplus 1108 recycling system, it also presented an Industry 4.0 package. Machine, quality and recycling process data were relayed in real time from the recycling center to Erema’s booth.
The show also was the premiere of 100-percent-recycled-plastic packaging, accomplished through the collaboration of Borealis, Hosokawa Alpine, Bobst, GEA and Erema. The end product was recyclable stand-up pouches with a material combination exclusively based on polyethylene. “I like to compare the plastic loop to a relay race,” says Manfred Hackl, CEO of Erema. “It is not enough if a part of the value chain thinks only in terms of their processing step. Every manufacturer of plastics has to think one step further to reach the finish line successfully together.”
*****
In the spirit of getting better at what we do, this is the first of three issues that we have planned for 2017. Our editorial teams have collaborated to bring you compelling features that now include articles on equipment technologies and how they’re being used by processors; or, processors in search of technology. We also now cover materials science. Starting on Page 40, correspondent Bruce Geiselman reports on “The Expanding Role of Compatibilizers,” profiling several companies involved in the production of these materials. In layman’s terms, these are the additives that make it possible for plastics that do not agree with each other to get along. Demand is growing for compatibilizers because “there is only so much that can be done with mechanical cleaning and separating,” says Kenrich Petrochemicals’ Sal Monte. Here is an example he provided about how the use of a compatibilizer improves possibilities. “No. 2 high-density polyethylene (HDPE), No. 4 low-density polyethylene (LDPE) and No. 5 polypropylene (PP) are all considered to be polyolefins and are made by similar addition catalysts. However, when you try to recycle more than 5 percent PP into HDPE to injection mold utilitarian flower pots, you will run into severe delamination problems. Therefore, a small amount of an organometallic compatibilizer will allow a 50-50 blend with good properties.”
How are you finding ways to be innovative? We would love to hear about it. Please contact one of our editors with your interesting story: DeAnne Toto at dtoto@gie.net, Ron Shinn at rshinn@plasticsmachinerymagazine.com or me at aderosa@plasticsmachinerymagazine.com.
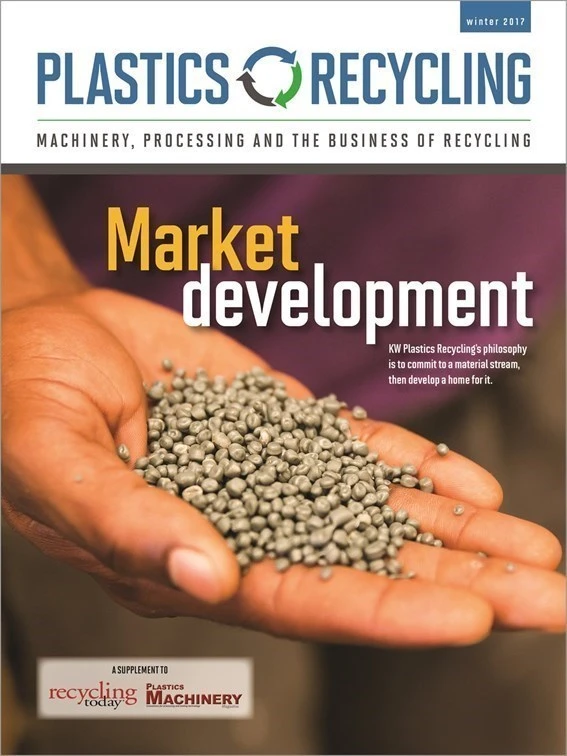
Explore the February 2017 Plastics Recycling Issue
Check out more from this issue and find your next story to read.
Latest from Recycling Today
- Green Cubes unveils forklift battery line
- Rebar association points to trade turmoil
- LumiCup offers single-use plastic alternative
- European project yields recycled-content ABS
- ICM to host colocated events in Shanghai
- Astera runs into NIMBY concerns in Colorado
- ReMA opposes European efforts seeking export restrictions for recyclables
- Fresh Perspective: Raj Bagaria