
Photo courtesy of Machinex

Historically, when it came to designing a material recovery facility (MRF), recyclers had to make sacrifices, and an important consideration used to be the decision between recovery and purity. In the world of MRF system design, market demands for cleaner end products typically required the MRF operator to sacrifice recovery.
As recycling has evolved and markets continue to evolve, how can MRFs and their suppliers deliver both purity and recovery?
The sum of its parts
When building or upgrading a MRF, it’s important to remember the best equipment does not always deliver the best MRF. Customers do, however, need to consider using various technologies that interconnect, data-share and are supplied by a trusted adviser that will provide long-term support.
It is key to have technical support that listens first and has a full understanding of your goals. You will want to work with people who consider all aspects of your operation and maintenance for the long term. Plant accessibility and safety also should be top concerns. Find an adviser or supplier who can help you achieve the vision of your MRF now and into the future and select the supplier who can understand the evolution of your material composition to provide a system that meets your requirements for purity and recovery. Choose a partner who can provide the technologies and is willing to participate in a collaborative effort that takes a great deal of time and patience. The most successful MRFs are the projects where the engineers and the customer’s development team work together from the beginning.
Before designing
To ensure a new or upgraded MRF meets your goals, as much information as possible is required upfront in the process. Typical items MRF designers should look for are building information, material composition, required throughput, required recovery/purity goals, operating hours and the approximate overall project budget. Knowing and providing this information to your adviser will get your project off to the right start and shorten the system design curve. These items also will help set clear expectations for what your final goals are.
It is important for operators to understand there is no one-size-fits-all approach. Many variables must be considered when working through a system design, so using an off-the-shelf system might not be the right option for your project.
Each MRF has different goals (tons per hour, recovery rates, purity, manpower, etc.), and you want a system that can be customized to your needs when making such an investment. While another system could have similar pieces of equipment, are they in the right position for your process?
Sitting down with a designer early in the process is recommended because some of the best MRF designs have been accomplished when a customer is willing to spend time with the designers and challenge one another with ideas. The customer needs to be ready to share and have an open mind. It is important not to go into a project with a preconceived idea but to be open to hearing all the technologies and ideas your potential suppliers can offer. An instrumental part of a successful MRF is its design, engineering and the experience of the MRF designer.
A key issue to discuss upfront with your designer is whether your MRF will be in an existing building or greenfield construction. An existing building can lead to many challenges that will need to be addressed upfront, such as ceiling height, traffic flow, building columns and any other challenges that are relevant to your property constraints and project. Do you have to sacrifice anything due to the limitations of the existing building?
Technology and design considerations
When beginning the design process, it is important to remember you are not only designing for today’s environment but also to accommodate future changes.
“When planning and designing a new MRF, it is important to consider your [MRF’s] particular stream,” says Jeff Snyder, director of recycling at Cincinnati-based Rumpke Waste & Recycling. “Each MRF stream is different around the country and the globe, and different equipment choices will be needed based on your particular service area’s needs and end-market availability.
“Additionally, you have to anticipate your future needs in the design so you have the ability to adapt machinery or add new machinery when new end markets emerge, and you can pull more commodities from the waste stream,” he adds.
Keep potential changes in commodity markets, inbound material composition and staffing challenges in mind when working through a new or upgraded MRF design.
To address potential changes, select equipment that is more adaptable to material changes, save space for additional equipment within the building footprint and include extra material storage bunkers for commodities that could need to be recovered.
Two of the most overlooked issues when designing a MRF are how separated commodities and system residue will be handled. This challenge begins with material bunkers and how you plan to manage the commodities. Building flexibility within the commodity storage and baling system is key to making sure you are designing a successful MRF.

Most of today’s higher-capacity MRFs are being designed with at least two balers. Ensuring all commodities can go to either baler will help with everyday operations.
For residue, understanding where you are going with that material and how you want to transport it to its final location are important factors. Do you want to have smaller compactors with boxes that need to be changed out more frequently or large, transfer-style compactors that load into transfer trailers? Discuss these points during the design phase to determine the best route for your project.
Additional considerations should include but are not limited to flexibility with optical sorters ejections, equipment bypass options in case a machine is down and commodity sorting options by position.
As commodity markets change, one of the ways many customers stay flexible is by including more advanced technologies, such as optical sorters and robots. Within reason, both technologies easily can be modified to sort different materials. For example, with optical sorters, it could be as simple as changing the ejection pattern or changing the parameters inside the unit. Robots can be reprogrammed or can learn to go after a different commodity or new product that appears in the inbound material stream.
Flexibility is critical as MRF adjustments usually need to be made every six months.
In the era of equipment interconnectivity through artificial intelligence- (AI-) supported software, technology integration cannot be overlooked, and the efficiency a technologically advanced, data-driven MRF can provide should be part of the business analysis of your project. Consider the ease of integrating all technologies and ease of data sharing when designing a new MRF. Using a single manufacturer that can integrate high-technology equipment with other system operations could be beneficial.
Along with overall system design features, consider how the system will be operated and maintained over the years. For example, overall traffic flow around the MRF, on-site trailer parking, scale house location and maintenance accessibility to processing equipment via platforms are critical items to examine in the design phase to help extend system life and uptime. If you make equipment harder to service, it will not get serviced. Try to stay away from multiple platform levels and ladders to help give your key personnel better access to the equipment and make their lives less challenging.
Design review
As important as drafting and developing project goals are, it is equally important to ensure those goals are met with a design that has been put together by the equipment vendor, and having a list of your goals can help in that process.
It is important to review the proposed design many times, in detail, with the equipment vendor to ensure you have a complete understanding of all the features built into the system.
Operational costs are another major part of the selection process, so reviewing the information with each potential supplier is crucial. These costs can be in the form of overall system recovery, maintenance and required staffing levels, as well as a number of other costs. If you are reviewing multiple proposals, it is important to understand how the designer came to this cost to ensure your known costs were considered.
Lastly, you also are selecting a partner that will be working with you throughout the life of your processing equipment. It is not only important to consider the proposed processing system, but also the vendor. Select one you can see yourself working with throughout all phases of the project.
You are not just buying equipment; you are buying a long-term relationship. Many vendors will try to sell you a system. Do not be sold, rather, choose to buy. Ensure you have established trust with your vendor to understand what you are buying and why.
Get curated news on YOUR industry.
Enter your email to receive our newsletters.
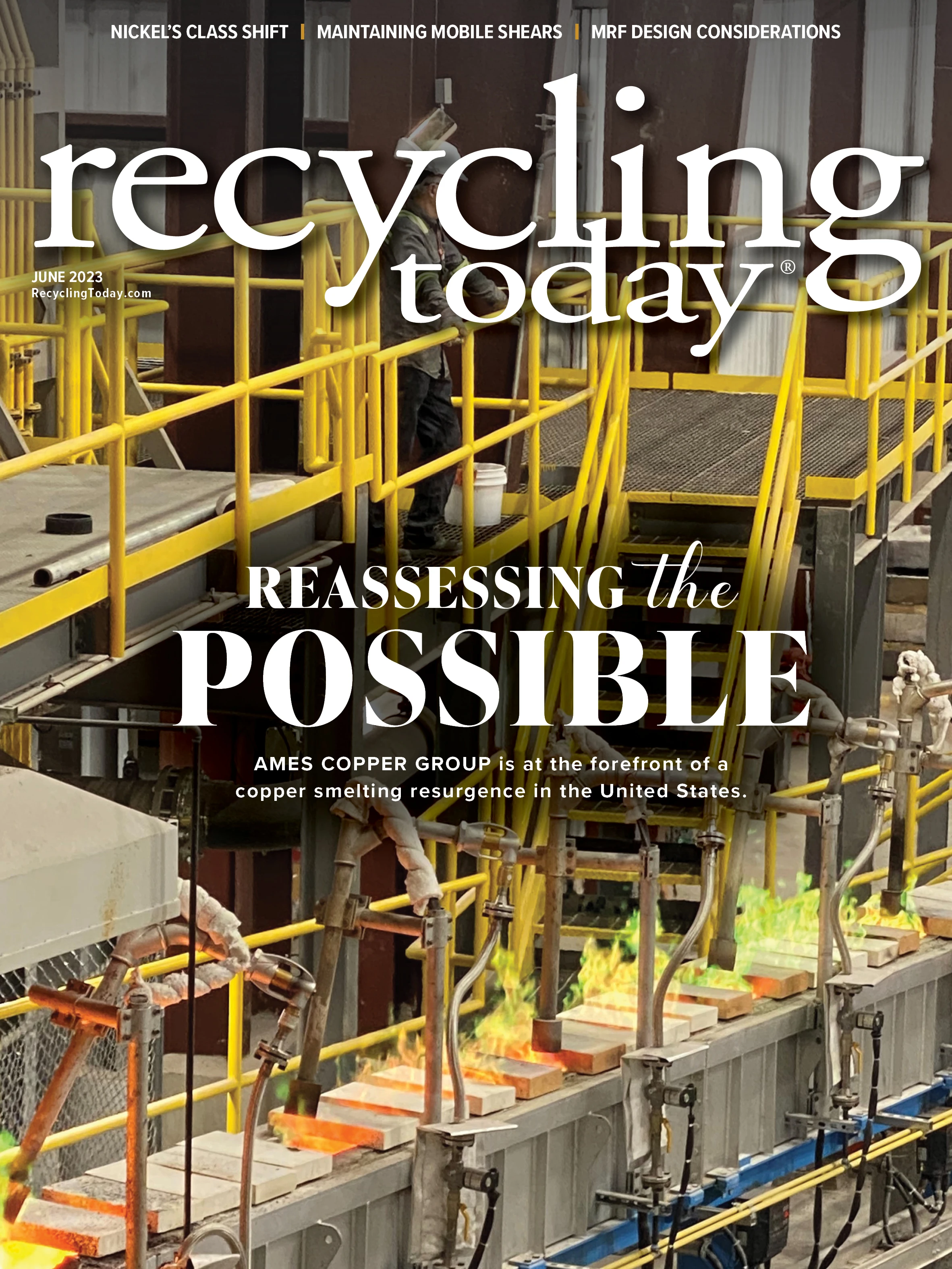
Explore the June 2023 Issue
Check out more from this issue and find your next story to read.
Latest from Recycling Today
- Athens Services terminates contract with San Marino, California
- Partners develop specialty response vehicles for LIB fires
- Sonoco cites OCC shortage for price hike in Europe
- British Steel mill’s future up in the air
- Tomra applies GAINnext AI technology to upgrade wrought aluminum scrap
- Redwood Materials partners with Isuzu Commercial Truck
- The push for more supply
- ReMA PSI Chapter adds 7 members