
Bano Recycling, headquartered in Padua, Italy, has been developing advanced solutions for aluminum and nonferrous scrap processing for the last 20 years.
Leading its lineup is the PREMAC HYDRO single- shaft primary shredder, which offers a revolutionary way to process aluminum scrap with its high-torque, slow-speed operation that results in high recovery with minimal dust creation. The shredder produces a high-quality product that is very much in demand by smelters and refiners. It is available in sizes with rotor lengths ranging from 1.8 to 3.5 meters, or nearly 6 to 11.5 feet, and with power requirements that range from 200 to 700 kilowatts.
Bano’s MAC-S HYDRO single-shaft secondary shredder series ensures precise cutting with low maintenance costs. With rotor size that range from 1.6 to 4.8 meters, or 5.25 to nearly 16 feet, it processes light metal scrap, such as UBCs (used beverage cans), aluminum briquettes, copper wires, brass bullets and turnings.
Laura Minotto, sales project manager at Bano Recycling, says certain aluminum scrap applications also employ the company’s vertical mill with specific rotor configurations. “And we do have refining line to recover fine aluminum particles from secondary products of other processes.”
In addition to these technologies, Bano can provide a complete plant that includes magnets and eddy current separators, she says.
Counting the benefits

Bano’s size-reduction technologies offer a range of benefits, Minotto says, including downstream processing efficiencies related to the precise, flat cut that is produced and the homogeneous sizing through their integrated screens. Fines and dust are kept to a minimum, as is noise, while safety is increased because the machines eliminate the risk of projectiles, explosions and fires, which cannot be said of hammer mill shredders. The machines’ hydraulically operated rotors are controlled with programmable logic controllers (PLCs) that level out their energy demands for economical operation.
Profilglass S.p.a., an Italian manufacturer of aluminum laminates, uses Bano’s equipment for the cold treatment of aluminum scrap and for processing internally generated manufacturing scrap prior to smelting. The company’s Denis Ricciatti says Profilglass turned to Bano’s single-shaft shredders to process 5000-series alloy packs that Profilglass found double-shaft and hammer mill shredders ill-equipped to handle.
He adds that double-shaft, hammer mill and single-shaft shredders are very different and the characteristics of the input material and the objectives to be achieved in terms of productivity and the density of the output material affect machine selection. “Surely the single-shaft is the one that accepts a wider range of materials in input,” he says, noting that it also excels in productivity.
Minotto says that compared with the twin- and four-shaft shredders and hammer mills that traditionally are used to process aluminum scrap, “Bano has developed technology that is more efficient and responsive to customer needs.”
She says Bano’s equipment has excelled in processing UBCs and extrusions, taint and tabor. The flat particles produced by the technology allow contamination to be spotted easily, Minotto adds, particularly when compared to the output of hammer mill shredders.
Maintaining the cutters is fast and easy, she adds “We have interchangeable cutters that can be changed within six hours without removing the rotor.” She says maintenance can be performed from a platform in front of the rotor using a remote control to move the rotor.

Ricciatti says that while the cutters need to be replaced more often on the single-shaft shredders, “extremely invasive maintenance” is very rare, unlike with hammer mill shredders.
Profilglass also operates a vertical mill from Bano. Ricciatti says, “I think that the advantage of Bano Recycling’s vertical mills is versatility. In fact, by changing the type of rotor and armor, it is possible to process different types of material and obtain different types of output material.”
Regarding the addition of Bano’s equipment, Ricciatti says, “We have certainly been able to optimize the production process by having a range of products that we did not have before.”
He adds, “I think that Profilglass has found in Bano Recycling a serious and reliable supplier.”
From recyclers to smelters
Aluminum scrap recovered using Bano’s technology offers advantages to smelters, as well, she says, and the company has seen increasing interest in its technology from this sector. The homogeneous material produced using Bano’s single-shaft shredders offers very little space for air and melts quickly, improving the energy efficiency of their furnaces. The purity of the material also is improved, reducing the need for additives.
Bano’s aluminum size-reduction equipment has been installed across the world, Minotto says, including in Japan, Europe, the USA, Mexico and South America, at public and private companies. Its latest installations have been at companies in the U.S. and Mexico, with the U.S. company having installed two identical lines to process UBCs at a rate of 18 tons per hour each, or 36 tons total. The company in Mexico is a smelter that also installed twin lines, which are processing aluminum extrusions, primarily, at a rate of 15 tons per hour on each line.
Get curated news on YOUR industry.
Enter your email to receive our newsletters.
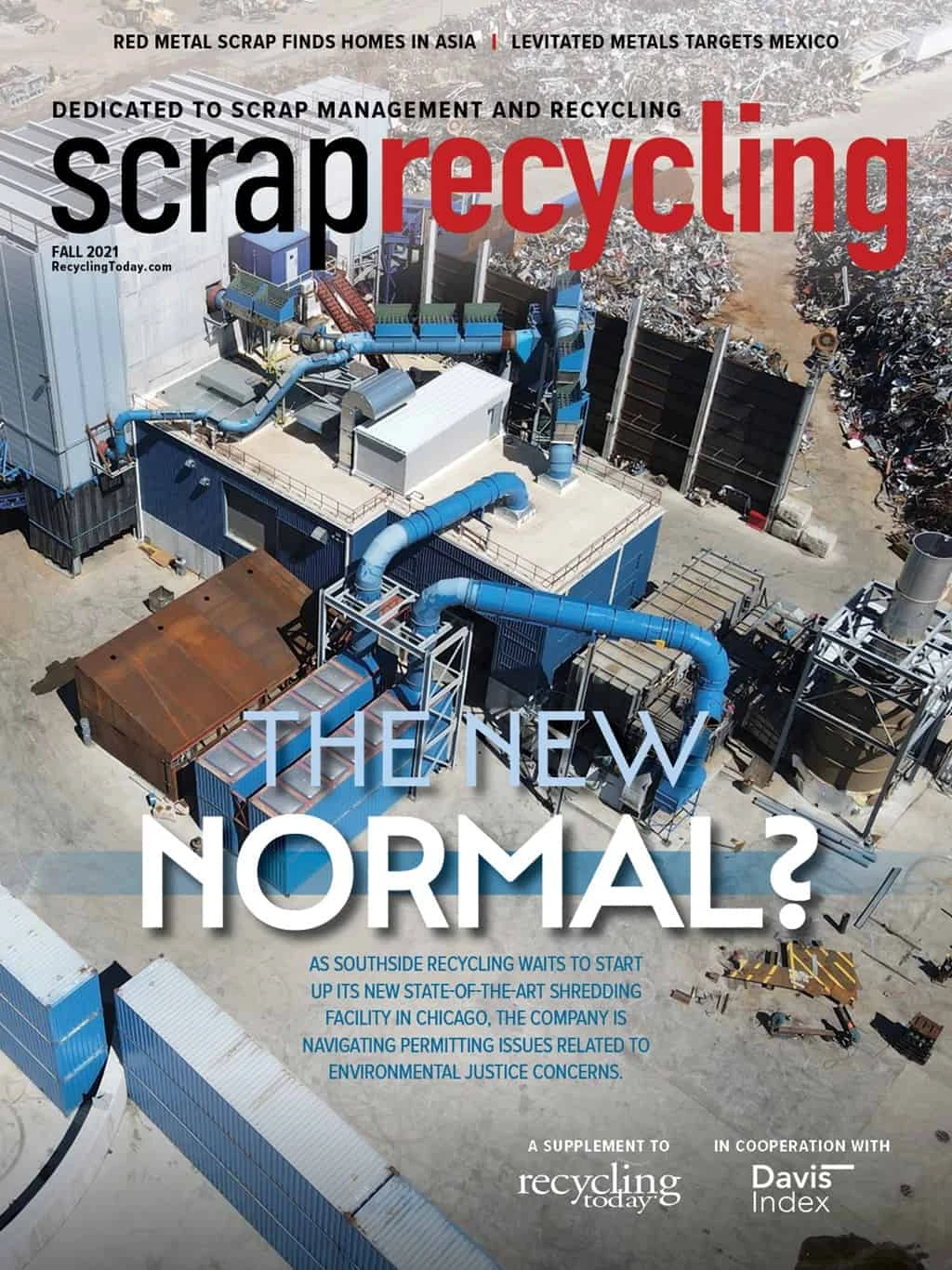
Explore the Fall 2021 Scrap Recycling Issue
Check out more from this issue and find your next story to read.
Latest from Recycling Today
- Green Cubes unveils forklift battery line
- Rebar association points to trade turmoil
- LumiCup offers single-use plastic alternative
- European project yields recycled-content ABS
- ICM to host colocated events in Shanghai
- Astera runs into NIMBY concerns in Colorado
- ReMA opposes European efforts seeking export restrictions for recyclables
- Fresh Perspective: Raj Bagaria