
Tim Horkay, Rob Taylor and Jeff Nella surmised they have more than 100 combined material recovery facilities (MRFs) among their respective companies—and balers are vital in each one.
Taylor, senior manager of recycling operations for Phoenix-based Republic Services, oversees capital allocated to its 70-plus MRFs, ensuring facilities get the equipment they need to run efficiently. Horkay, director of recycling operations at The Woodlands, Texas-based Waste Connections, supports 33 MRFs, while Nella, area recycling director-U.S., at Vaughan, Ontario-based GFL Environmental Inc., said his company operates nearly 30 MRFs in North America.
“When we talk about the number of balers that the three of us have within our facilities, it’s almost like a number that’s too hard to count,” Nella said during a panel discussion at the MRF Operations Forum, hosted by the Recycling Today Media Group last October in Chicago.
Nella moderated the session, which focused on baler redundancy, and noted all three speakers have been directly involved in purchasing balers at their MRFs.
Each speaker also noted that baler purchases should be tailored to a MRF’s needs, and those needs will vary.
Single- or two-ram?
When searching for the right baler, the panel said the choice between a single- or two-ram model comes down to a numbers game.
Taylor said MRF operators should start by looking at the composition of their inbound material to figure out if its primarily fiber or a combination of fiber and single-use beverage containers. “Then you figure out the overall tonnage coming through the stream, if you’re looking at a 25 ton-per-hour system up to a 70-ton, [for example],” he said. “Then you’ve got to just go back into the math and know that you can have baling capacity that’s going to be able to keep your plant operational for a dual shift, typically, throughout the day where you can get everything [baled] that’s going to be separated and bunkered by the end of the shift.”
He added that if a facility primarily is processing fiber, a single-ram baler makes the most sense.
Horkay agreed, adding that a single-ram baler “is all about throughput and consistency on fiber and can really knock it out of the park.”
When it comes to two-ram models, Horkay said they offer the flexibility to process different materials, allowing operators to quickly switch between commodities, such as moving from fiber to aluminum cans to plastic bottles.
Switching between commodities with a single-ram baler often involves adding or subtracting wires to tie the bale, he said, which reduces throughput by adding time to modify the baler ties. “That’s one of the things we look at” when selecting a baler, Horkay said.
Along with changing material, facility upgrades affect what baler fits best.
In the case of a 10-ton-per-hour system with bunkers that align with that tonnage being upgraded to a 25-ton-per-hour MRF, “I’ve got 2 ½ more times the number of grade swap-outs,” Nella said. “That’s something we generally start looking at as well.
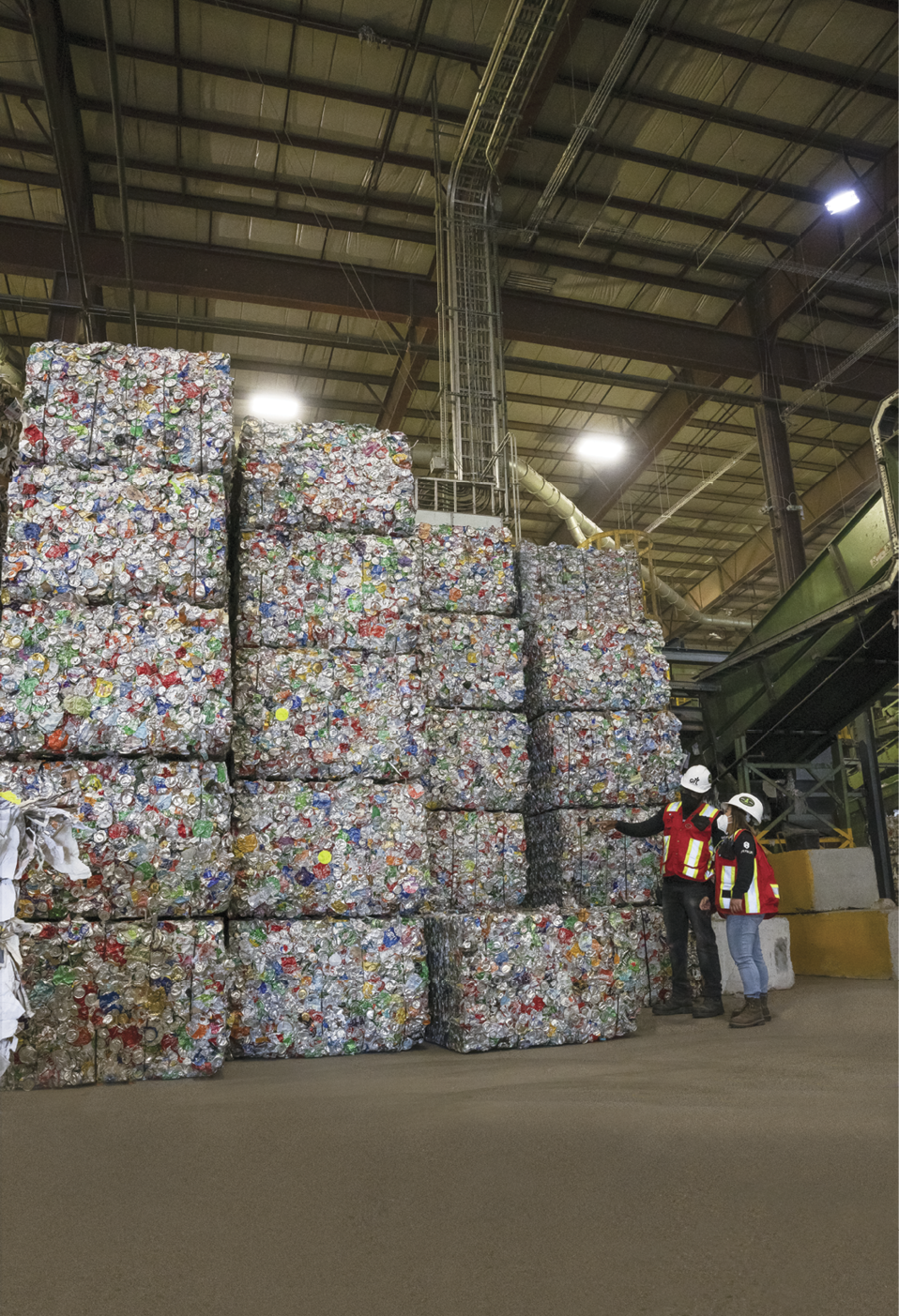
Adding on
The panel agreed tipping floor capacity also matters when deciding to add balers to an operation.
“You can look at how much [material] you have on your tip floor,” Taylor said. “If you have a tip floor with a lot of capacity, then you want to have that redundancy built in.”
Taylor used Republic’s Las Vegas MRF as an example. The facility has three balers, in part because it receives additional tonnage such as Amazon packaging that otherwise would cut into baling time for the rest of the operation.
The breakdown of commodities also is important when considering redundancy. “If you’re container rich, then maybe you look at a double-ram,” Horkay said. “But, if you’re a typical MRF, I would look at the speed and efficiency of the single-ram and then the backup where you run the containers could be the dual-ram, and it’s going to do a lot better of a job for you over there.”
Another number to consider is the MRF’s square footage. While installing multiple balers and bunkers might not be feasible for some operations, the panelists said new or expanding MRFs should take potential tonnage increases into account during the design phase.
In the new MRFs Republic is constructing, if incoming tonnage has the opportunity to increase, Taylor said, “let’s build [redundancy] in now and not wait for the capacity to show up.”
Nella said GFL considers future changes for all its new MRF builds. “We’re thinking about what a second baler would look like if it’s a small facility, what a third or even what a fourth baler potentially could look like, and making sure that the design would allow for an easy flip-over, or at least a faster upgrade, rather than blowing a facility up to try and realize you’ve just outgrown your storage facility even though everything else has got capacity,” he said.

Maximum return
Taylor said 12 to 15 years is the ideal lifespan for a baler, though that can depend on wear and tear.
“Baler linings are hard to measure sometimes, and they’re strong machines,” he said. “They tear themselves apart and you don’t see it coming. But, ideally, you should be looking at 12 to 15 years.”
Horkay said preventive maintenance, such as checking the oil, oil filters and hydraulics, can help keep balers healthy.
“We always look at sampling the oil on a quarterly basis or, at the very worst, when we change filters out,” Nella added.

Not so simple
The conversation around which balers to use in a MRF is anything but simple, Nella said. “It’s a case-by-case basis, and what’s good for your friend who has a MRF 50 miles away or down the street may not work for your own operation.
“Even within Republic or Waste Connections or GFL, we have wildly different parameters within our own network of facilities, and what’s right in Missouri at one site may not be right at one in Illinois or Wisconsin,” he added.
For companies that operate multiple MRFs, Horkay recommended working with individual operators to evaluate baler needs.
“It’s constant coaching,” he said. “It’s an opportunity to sit with operators and walk through the numbers behind the decision. It’s understanding their operations and seeing where you can help and give a little bit of guidance. Operators know what’s going on most of the time.”
Taylor said it could be beneficial to visit a facility to see how the system is being fed. “You may have a 35-ton-an-hour baler that you’re putting 20 tons through because they’re not feeding it right,” he said. “So, look at those kinds of day-to-day operations. See if there’s any efficiencies you can help build on.”
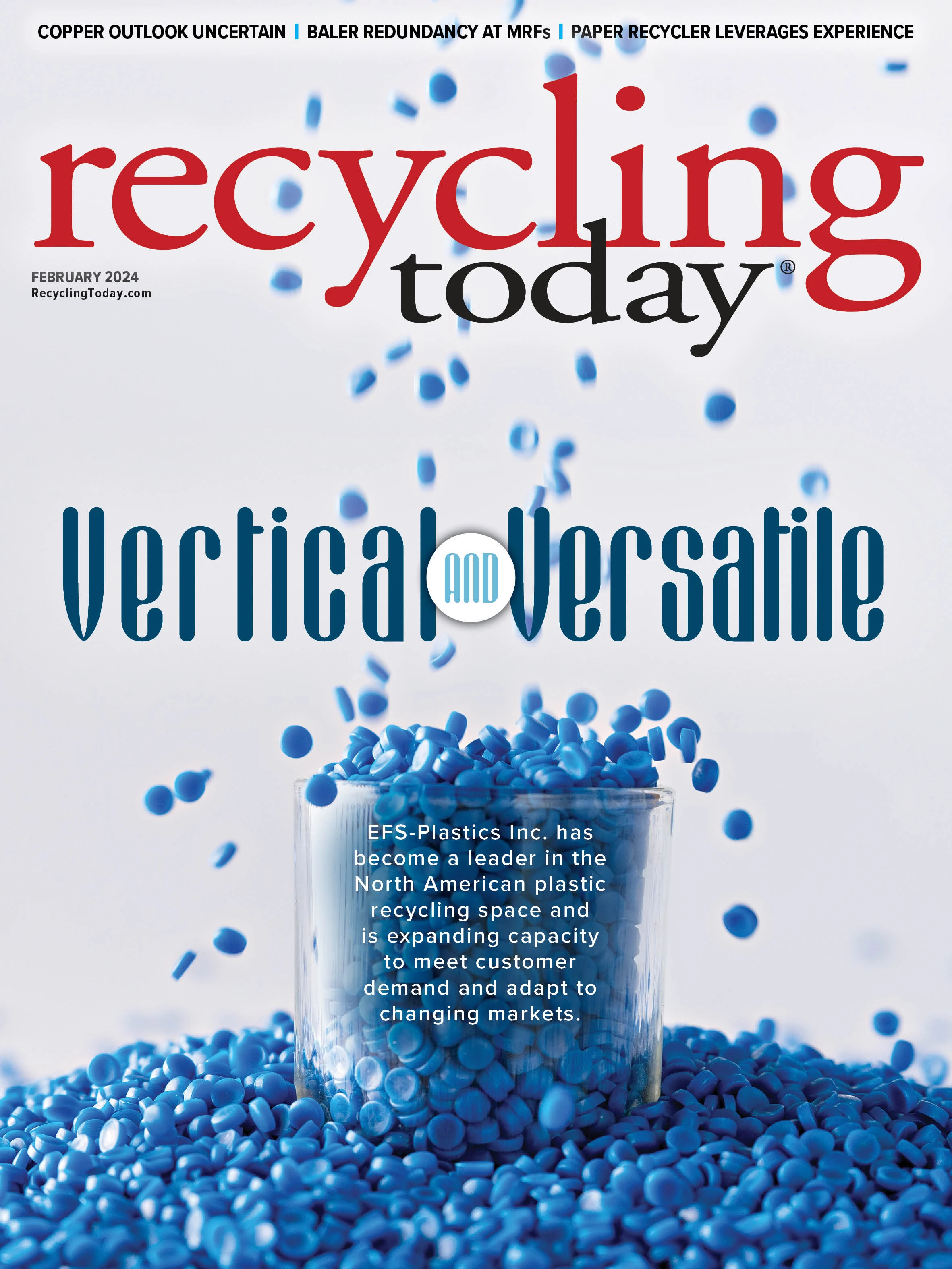
Explore the February 2024 Issue
Check out more from this issue and find your next story to read.
Latest from Recycling Today
- EU levies ELV recycling fines against 15 automakers
- Call2Recycle Canada launches program in Alberta
- The history of SAS Forks: Celebrating 50 years
- SAS Forks partners with NED at Green Recycling in Houston, Texas
- DRKhorse’s RCC series at Gorick Construction in Endicott, New York
- Balar Equipment to operate under Enviro-Clean Equipment name
- Li-Cycle reports 2024 financials
- Wisconsin Aluminum Foundry acquires Anderson Global