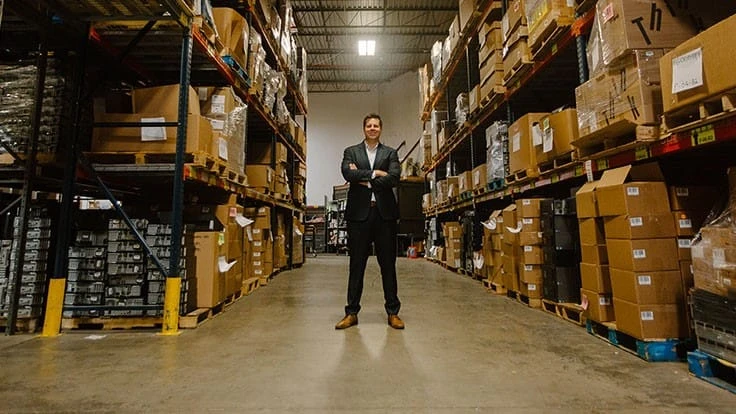
Photos by Connor Barber Photography

Singapore is a tiny island nation of 5.3 million people that is known for punching above its weight class as a global shipping, logistics and financial hub. Therefore, it might come as no surprise that perhaps the world’s single-largest electronic scrap recycling and information technology asset disposition (ITAD) firm used Singapore as a springboard for its worldwide ambitions.
TES (at one time known as TES-AMM, which stood for Total Environmental Solutions – Asset Material Management) started in 2005 as an e-scrap recycler based in Singapore, says Eric Ingebretsen, TES’ U.S.-based chief commercial officer.
The company’s 16-year story is a chronicle of growth by volume handled and geographically, as well as by the size of its customer base and depth of its service menu. “That growth was materially based on [Forbes] Global 2000 relationships and TES’ entrepreneurial approach to expanding to support them,” Ingebretsen says.
Always more to do
Obtaining a full grasp of TES’ operations can be difficult for reasons beyond that it now has 42 owned and operated processing facilities around the world. The company handles a wide variety of technology devices and pursues refurbishing, recycling and other processing methods based on client requirements, economic factors and sustainability-based outcomes.
TES CEO Gary Steele says, “In the early 2010s, TES recognized the opportunity to also service the refurbishing and reuse space within the same or similar client set and, thus, started offering ITAD services.”
Remarkably, after spending from 2005 to 2010 becoming “the dominant player” in the Asia-Pacific region in e-scrap recycling, TES accomplished the same thing in the global ITAD space in the following five or six years, Steele says.


The company’s successful strategy in Asia has been introduced to the rest of the world in part because of TES’ 2013 acquisition by Malaysia-based Navis Capital Partners. Ingebretsen describes Navis as “a large private equity firm with $6 billion in investments under management.”
In conjunction with Navis, “TES aligned on a global strategy [and] acquired a large ITAD player in Europe named Dataserv in 2016,” Steele says. Several other small acquisitions in Europe followed, he says, helping TES build to its current scale in Europe.
In North America, TES has pursued more of a greenfield strategy. Over a five-year period, the company has developed three ITAD and recycling locations with nearly 100 combined employees.
The decade and a half of rapid but targeted growth has led to more than 40 processing facilities on three continents and about 2,000 employees globally. In early 2021, Connecticut-based IT market analysis firm Gartner identified TES as the largest and one of just three companies in the world with the ability to deliver comprehensive ITAD services globally.
However, far more than just buildings are needed to provide global service, Steele says. “Our 2,000 employees worldwide deliver our services directly, which allows TES to offer a global service that really feels like a global service. What does this mean? It means a lot more than lower logistics costs. It means that we have local compliance experts in the region and in-country and a deep understanding of transboundary movement globally. It means that we can offer support in local time zones and languages (critical in global programs); consistency in service, pricing and values; billing in local currency and more.”
With global responsibility comes global risk. Therefore, Steele continues to help find growth avenues for TES while also helping the company manage a range of issues affecting electronic scrap recycling and ITAD service providers.
Respecting boundaries

TES has built its business in part because its more than 40 globally situated processing facilities “give our customers a consistent experience no matter where their assets are,” Ingebretsen says.
The company’s global model also involves moving retired assets, components and secondary raw materials to the most suitable market, but the e-scrap aspect of the business is under increasing pressure, he adds.
“Transboundary movement of material is likely going to get more challenging; we’ve seen this changing in Asia over the last three to four years as things have tightened up significantly in China, Malaysia, Thailand and other countries,” Ingebretsen says.
The reasons for some of the restrictions make sense, he says, and TES has and will continue to create closed loops how and where it needs to do so. “We see this as a positive for those countries and the industry in general to help ensure e-scrap is going to receiving facilities that can appropriately process it.”
Ingebretsen adds, “TES was already well-positioned with a network of permits that allows us to compliantly move material into a variety of countries where we have facilities that can process this material.”
That circumstance could change in the U.S. “In the U.S., there is legislation being considered that would significantly restrict material flow outside the country,” he says. “There are potential positives and negatives that could come out of that, depending on the final language in any bill that passes.”
Provided such legislation and regulations are uniformly enforced, change doesn’t have to be bad for TES. “Transboundary movement of material has always been foundational to recycling, particularly in the U.S., and this legislation could introduce a step change to both the e-scrap recycling and ITAD industries,” Ingebretsen adds.
Understanding the regulatory minefield means “there is more of a need than ever for the services we provide,” he says. “While cost and value remain important, commercials take a back seat with our customers versus how we can raise the bar in data security and sustainability, which is great for the industry. Customers are educated on their requirements and needs, which elevates the strata of providers like TES who can meet them.”
While changes to laws and regulations provide reasons to keep Ingebretsen and other TES executives busy, the pursuit of new revenue streams provides others.
A charged-up future
Despite potential regulatory change, TES continues to invest in new opportunities. One of the most intriguing opportunities at the start of the 2020s involves optimal handling of end-of-life batteries.
Starting in 2019 with a facility in Grenoble, France, TES has invested in research, processing equipment and new plants with the goal of repurposing and recycling the growing stream of batteries found in excess and retired technology assets in addition to batteries from electric vehicles.
This spring, in its headquarters city of Singapore, TES officially opened its multimillion-dollar, highly automated facility to recycle lithium batteries.
The facility, known as TES B, has the capacity to recycle up to 14 metric tons, or the equivalent of 280,000 lithium-ion smartphone batteries, daily. TES B deploys a combination of mechanical equipment and hydrometallurgical processes to recover nickel, lithium and cobalt.
True to its global nature, this July, TES announced it had agreed to a deal to equip a 110,000-square-foot facility at the Port of Rotterdam in the Netherlands to recycle end-of-life batteries.

The facility “already has a basic waste license to receive, store and forward lithium batteries and to manage electric vehicle batteries and battery production scrap, as well as a license to shred alkaline batteries,” according to the company.
Batteries are not the sole focus of recent investments or expansion plans at TES. Ingebretsen points to an “innovative recycling process that transforms PCB (printed circuit board) manufacturing waste in China into a valuable polymer.”
The company has acquired the patent for a nanotechnology that “produces carbon nanotubes (CNT) from recycled plastics,” he says.
“CNT are cylindrical molecules that consist of rolled-up carbon atoms that develop ultra-high-strength, low-weight materials that possess highly conductive electrical and thermal properties,” Ingebretsen says. “This makes them highly attractive for numerous applications.
“In my opinion, the industry is at an inflection point—innovation in terms of process, tools and reporting have been relatively static for the last 10 to 15 years.” – Eric Ingebretsen, TES chief commercial officer
“We will start building a plant in Singapore in late 2021 to transform all types of used plastic, offering an innovative solution to the growing problem of waste plastics,” he continues.
The company’s investments are funding services that Ingebretsen says are designed to be comprehensive. “By using TES’ integrated services stack, organizations can remove complexity from their reverse supply chain and take advantage of the synergies that come with it.”
Continued growth will require innovation, Ingebretsen says, which is a quality that helps define his role with the company and the overall TES philosophy.
“In my opinion, the industry is at an inflection point—innovation in terms of process, tools and reporting have been relatively static for the last 10 to 15 years. Providers who will win in the long run will be the ones who have the appetite and means to invest in innovations like better material refinement, automation, sustainability programs and more.”
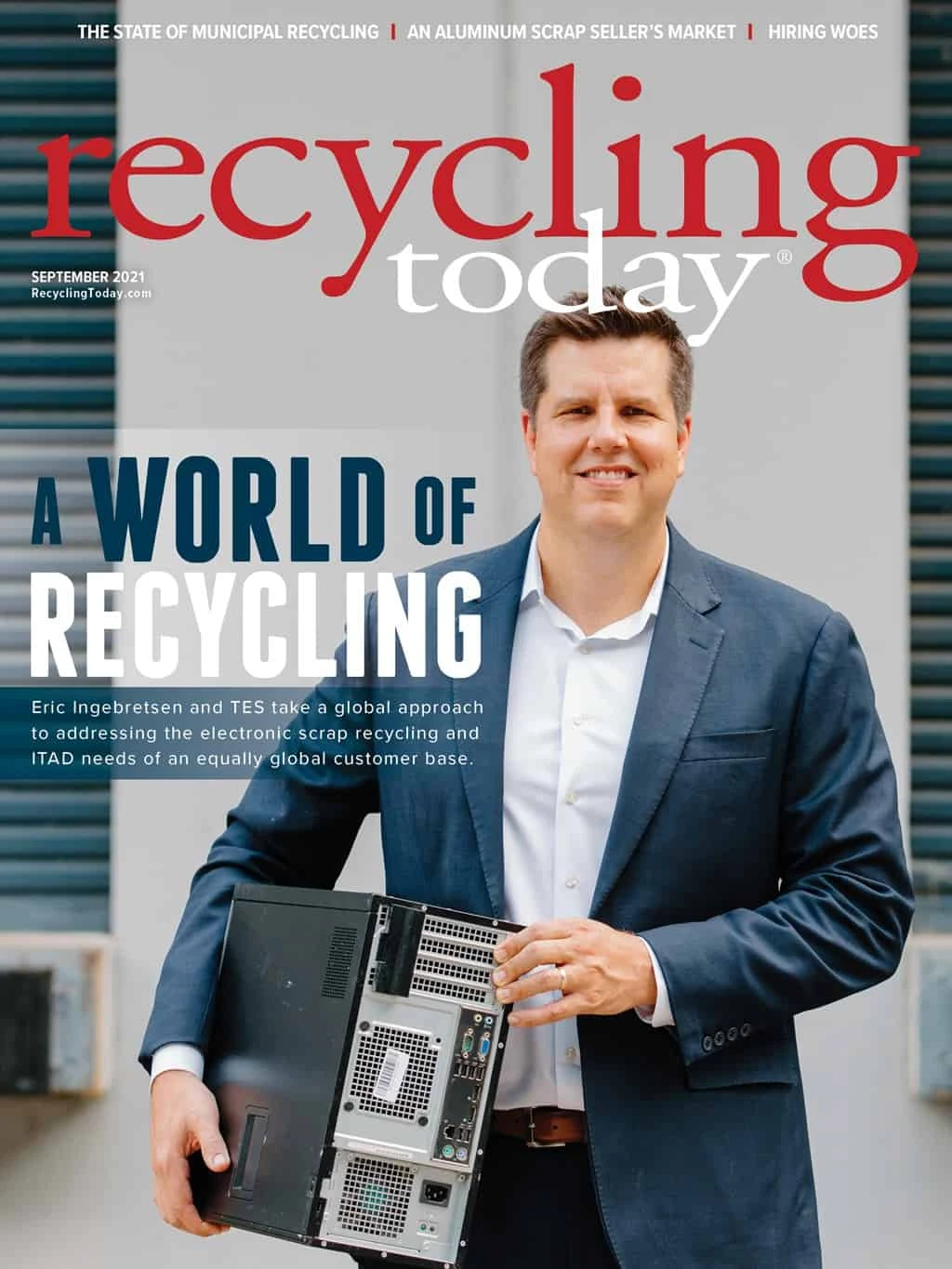
Explore the September 2021 Issue
Check out more from this issue and find your next story to read.
Latest from Recycling Today
- Aqua Metals secures $1.5M loan, reports operational strides
- AF&PA urges veto of NY bill
- Aluminum Association includes recycling among 2025 policy priorities
- AISI applauds waterways spending bill
- Lux Research questions hydrogen’s transportation role
- Sonoco selling thermoformed, flexible packaging business to Toppan for $1.8B
- ReMA offers Superfund informational reports
- Hyster-Yale commits to US production