T
o meet the scrap handling needs at Hutcherson Metals, President and Owner WileyHutcherson needed a machine that could do more than just one job.Hutcherson sees a combined 16 to 19 thousand tons of scrap come through his two facilities in Halls and Jackson, Tenn., per month. He’s employed a Fuchs material handler at each to help get the job done.
An MHL 350 makes its home at the Jackson facility, and an MHL 360 works at Halls. Both have been on the job for about a year and they’ve both proven useful and versatile additions to Hutcherson’s equipment line. "They do just about everything that needs to be done in processing scrap," he says.
The Fuchs 350 and 360 first caught Hutcherson’s eye at the ISRI Convention a few years ago. He says he watched the machines carefully for a few years before deciding to look into purchasing.
"I liked what I saw," he says, pointing out that the 350’s and 360’s hydraulically adjustable cabs eventually sold him on the machines. "I knew that would be a plus—to be able to see what you’re doing, especially when you’re loading," he says.
Loading trucks and barges is a big part of Hutcherson’s operations, in addition to general processing. The Fuchs machines have proven their mettle in all applications, he says, from feeding the shredder, shear and baler to loading the material onto various modes of transportation.
Hutcherson says while many of the machines he’s used in the past have been equipped with elevated cabs, none had the height he was after.
Height wasn’t a problem with the Fuchs machines—the adjustable cab of the 350 has a maximum eye level of more than 18 feet, while the 360 can reach 20 feet.
Another feature that drew Hutcherson to the Fuchs scrap handlers was the rubber tires, which he says are easier on his roads than the tracked equipment he also uses.
The 360 has particularly impressed Hutcherson by going beyond the call of duty for a typical scrap handler. In addition to its usual duties at the Halls yard loading and handling ferrous and nonferrous scrap, the machine has been working on a demolition job in Memphis, Hutcherson says, where it feeds brick and concrete into a trommel screen.
The machines have made a great impression on Hutcherson and his operators. "They think they’re great, especially when it comes to loading," he says. "We’re really proud of them."
The 350’s and 360’s overall versatility as workhorses have made them stand out at all Hutcherson’s facilities. "We don’t know of anything we like better on the yard," he says.
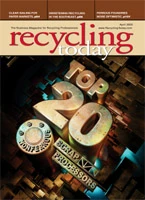
Explore the April 2005 Issue
Check out more from this issue and find your next story to read.
Latest from Recycling Today
- Fitch Ratings sees reasons for steel optimism in 2025
- P+PB adds new board members
- BlueScope, BHP & Rio Tinto select site for electric smelting furnace pilot plant
- Magnomer joins Canada Plastics Pact
- Out of touch with reality
- Electra names new CFO
- WM of Pennsylvania awarded RNG vehicle funding
- Nucor receives West Virginia funding assist