
Two Australian companies are working together to commercialize a technology that converts low-quality plastic scrap, such as the plastic found in automotive shredder residue, into road-ready diesel fuel. Construction is scheduled to start this year in Camden, Indiana, on the first plant using the technology.
In the proprietary catalytic restructuring process, plastic scrap is heated to more than 750 degrees Fahrenheit in the absence of oxygen. The heat breaks down the material into polymers and then into even smaller oil and gas molecules. When a catalyst is introduced, those molecules re-form into fuel precursors.
The technologies used in the process are owned by Integrated Green Energy Ltd., which has entered a strategic partnership with Foy Group Ltd.; both companies are based in Chatswood, Australia.
Foy has the rights to commercialize the technology in the U.S. and elsewhere.
“In relation to plastics reuse and fuel generation, Foy has the capability to produce road-ready fuels from end-of-life nonrecyclable plastics that are otherwise destined for landfill or other dumping,” says David McIntosh, Foy’s finance director. “Because our technology produces an end product that is immediately marketable, in a scalable design, in a continuous rather than batch process, Foy has a silver bullet that no other player in the industry has managed to bring to the market.”
“Because our technology produces an end product that is immediately marketable, in a scalable design, in a continuous rather than batch process, Foy has a silver bullet that no other player in the industry has managed to bring to the market.” – David McIntosh, Foy Group Ltd.
McIntosh says the cost of diesel fuel made by the process is significantly lower than conventionally produced fuel and has a smaller carbon footprint. In addition, technology is under development to further reduce the costs of production. Instead of buying crude oil, the Foy plant will recycle shredded plastics delivered to the site via road or rail by waste haulers.

Foy is partnering with GEP Fuel & Energy LLC of Port Arthur, Texas, to build the $200 million plant in Indiana. Under the companies’ agreement, GEP has the right to construct an additional four plastic-to-fuel facilities throughout the U.S.
The core technology is described in Australian patents AU2015904828, AU2016901654 and AU2016902869, which now all are encapsulated in a single patent application.
Australian Patent Application PCT/AU2016/051144; filed Nov. 23, 2016
Crushing tool. A new tool is designed to improve the crushing of blown films, cast films, small ribbons or fibers made from polyolefins and plastics such as polylactic acid (PLA), polystyrene (PS) and acrylonitrile butadiene styrene (ABS). Such crushing tools are used particularly in cutter compactors for the processing and crushing of plastic materials. In one aspect of the invention, a deflector is used to push material into the cutting zone. The patent states that the material to be crushed behaves like a fluid and is fed rapidly and efficiently to the cutting tools. The invention is assigned to Erema Engineering Recycling Maschinen und Anlagen GmbH, Ansfelden, Austria.
Patent Application 20160339443; Nov. 24, 2016
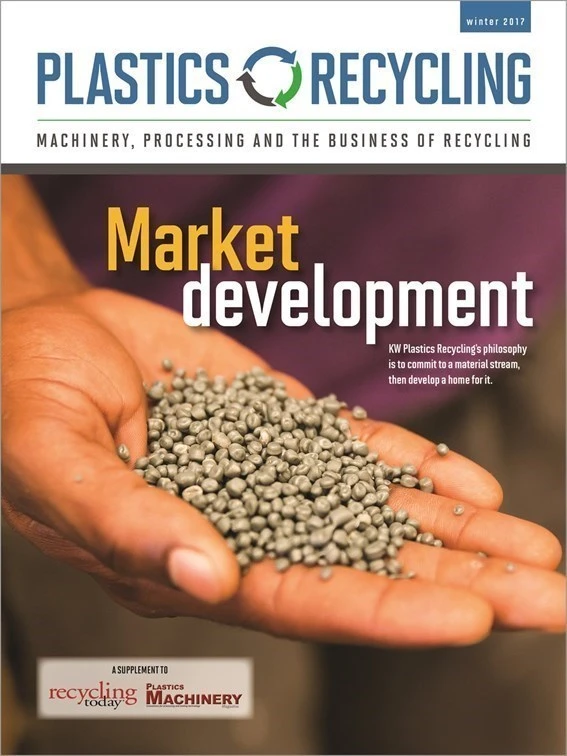
Explore the February 2017 Plastics Recycling Issue
Check out more from this issue and find your next story to read.
Latest from Recycling Today
- Smithers report looks at PCR plastic’s near-term prospects
- Plastics association quantifies US-EU trade dispute impacts
- Nucor expects slimmer profits in early 2025
- CP Group announces new senior vice president
- APR publishes Design Guide in French
- AmSty recorded first sales of PolyRenew Styrene in 2024
- PRE says EU’s plastic recycling industry at a breaking point
- Call2Recycle Canada, Staples Professional expand partnership