
Plastic grocery bags are among the most despised disposable plastic products, inspiring a multitude of bans across the nation. And current market conditions make recycling them economically challenging.
Prime Plastic Products Inc., Vista, California, aims to boost high-density polyethylene (HDPE) grocery bag recycling and is working to overcome the technical challenges that come with it. The company has two primary operations: grinding postindustrial plastics in Vista and sorting various types of used polyethylene (PE) film for resale at its Prime Recycling Solutions division, located in Norwalk, Ohio.
The company is considering adding an extruder to turn PE grocery bags into pellets. It also may purchase equipment to sort and clean the film, says President Vince Gupta, who co-owns the company along with his wife, Radhika.
“Based on current market supply and market demand, we are seeing it has become clear that the old model of ‘buy, aggregate and sell’ is not going to be sufficient,” Gupta says. “We are looking to see where we can add the most value to the material for the right targeted end markets. I am looking for the equipment to produce a clean-enough feedstock.”
Manual sorting is part of the process. Prime Recycling has a 40-foot sorting line where two or three workers on each side can pull out contaminants that ultimately compromise the quality of the end product.
But Gupta is searching for the most efficient means to boost the quality of the PE. He’s considered a wash system but is hesitant to go that route. “Wash systems, in my understanding, are expensive,” he says. “And the jury is still out as to if the wash step is necessary for a variety of potential end markets. So, the more practical choice would be to send the material through a densifier, and then the densified material goes into the extruder.
“I’ve been thinking I’m not looking to do a wash-system cleaning,” Gupta says. “So, that’s why we came to terms with the fact that our [recycled pellets] are going to go into applications which are B and C grade rather than A grade—particularly considering the glut of virgin PE that is coming online that could economically fill those A-grade applications. The question becomes, ‘Should we compete with those A-grade applications?’”
He thinks that a densifier-extrusion system will be economically feasible for the company.
The Norwalk facility covers 82,000 square feet on a 5.5-acre site. Prime Recycling has more than 2 million pounds of film there waiting to be sorted and baled or processed into pellets.
“We have to [reprocess it] because the film doesn’t have much value in today’s market,” Gupta says. Ideally, he would like to process 1,000 pounds of grocery bags per hour.
Gupta says German, Austrian and Italian manufacturers are offering recycling systems for film that cost anywhere from $750,000 to $1.2 million, which is not economically feasible for Prime. “We need to get strategic and innovative in how we look at vertically integrating our processes,” he says.
But the industry’s standards for the cleanliness of film bales have declined, especially after many years of shipping to China, so they come into Prime Recycling’s facility with lots of contamination, Gupta says. And now, China’s Operation Green Fence policy takes a hard line on importing contaminated recyclables, which has made it even harder to sell bales of recyclable film.
“What I’m learning is that unless I do value addition to the stream of scrap, it’s just not going to work,” he says.
An additional factor that has complicated the plastics recycling landscape has been the falling price of virgin resin. Now processors are buying off-spec virgin resin instead of recycled plastic because it has become price-competitive.
If Prime Recycling doesn’t extrude its material, the only option might be to sell it for fuel. “So, in one way, I’m a candidate which has a lot at stake to find a solution to this problem,” Gupta says. “As an industry, we need to explore new end-market opportunities for PE film products, including nonfilm applications.”
Gupta says he is fairly certain that he can easily and cost-effectively densify and pelletize bubble wrap, gaylord liners, stretch wrap, clean store- returned grocery bags and laundry, mattress and furniture bags. The trick is finding the right formula for handling grocery bags from curbside collection programs, which are dirtier. Prime has applied for grants from the state of Ohio to help it tackle grocery bags collected curbside.
Gupta wants to come up with a solid plan for bag sortation for both economic and environmental reasons. “I would just like to see some solution to this nationwide problem,” he says. “There are so many sources of film beyond return-to-retail, and if we don’t find a robust solution for all film, we do run the risk of being faced with more government intervention.”
For more information: Prime Plastic Products Inc., 760-734-3900, www.primeplastic.com, Prime Recycling Solutions, 419-577-8959, www.primeplastic.com
Get curated news on YOUR industry.
Enter your email to receive our newsletters.
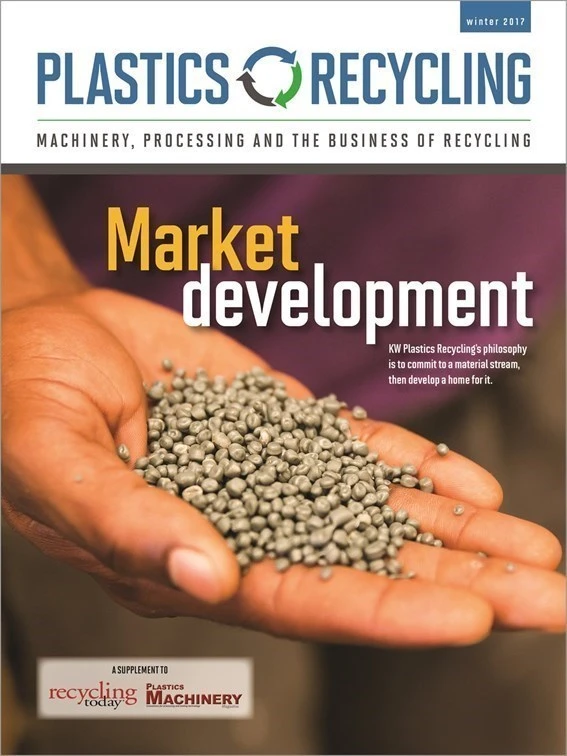
Explore the February 2017 Plastics Recycling Issue
Check out more from this issue and find your next story to read.
Latest from Recycling Today
- Toppoint Holdings expands chassis fleet
- Lego creates miniature tire recycling market
- Lux Research webinar examines chemical recycling timetables
- Plastics producer tracks pulse of wire recycling market
- Republic Services, Blue Polymers open Indianapolis recycling complex
- Altilium produces EV battery cells using recycled materials
- Brightmark enters subsidiaries of Indiana recycling facility into Chapter 11
- Freepoint Eco-Systems receives $50M loan for plastics recycling facility