Organization is a powerful component of the success of any business. While one pile of scrap metal might look the same as any other to the untrained eye, for scrap dealers trying to manage an inventory of dozens of grades, keeping everything straight can be a challenge.
Sometimes even a well-trained eye isn’t enough to differentiate between various grades. In today’s market, particularly concerning nonferrous materials, a nearly invisible difference in chemistry can translate into big differences in price. The industry has turned to sophisticated tools like inventory management software to help maintain an accurate, organized catalogue of what recyclers have at their facilities.
MAKING THE GRADE. Properly grading materials is among the top priorities for most recyclers, particularly with today’s market prices.
"From the moment material is received at the recycler’s yard, it is important that the material be properly graded," according to Larry Smith of Holland, Ohio-based software provider the Shared Logic Group Inc. "This does not always happen immediately. Often times, material is graded or adjusted at a later time before it is settled with the supplier."
Accurate grading is especially important with the current high value of nonferrous materials, says Jerry Martz of software provider Systems Alternatives Inc. (SAI), based in Maumee, Ohio. Today’s market conditions place additional emphasis on a recycler’s ability to accurately grade material at the point of purchase and to be diligent in recording weight and quality adjustments, Martz says.
Cougle’s Recycling is a full-service recycling center for paper, OCC, plastic, glass and nonferrous metals. From its location in Hamburg, Pa., it serves thousands of customers, from small stores to complete communities. When Cougle’s identified that its weighing operation was slowing down production efficiency and affecting data accuracy, it was quick to consider an alternative system solution. Company Chief Operating Officer Matthew Cougle contacted his local Avery Weigh-Tronix distributor, Precision Solutions, for help. The answer to the problem was simple. Precision Solutions retrofitted Avery Weigh-Tronix Forklift Truck Scales to seven of the company’s lift trucks, and after just two months, productivity had increased significantly. Cougle expects a total productivity increase of more than 30 percent in the following months. Cougle’s weighs and grades material as it arrives at the facility and after it is baled. Before the installation, drivers were weighing the loads on one of two floor scales, requiring the driver to leave the lift truck to record the weight. Operators would then send the handwritten paperwork to the office for processing of the transport and billing documents. The new lift truck scales have enabled Cougle’s to integrate weighing and data management seamlessly into the operation. The scale unit is installed onto each truck’s fork carriage, so that drivers can lift, weigh, move and record the load in just one operation, without leaving the cab. Precision Solutions also supplied onboard wireless PCs that transmit the weight data to a central computer for analysis. The new system also prevents operators from lifting overweight loads, reducing excessive wear and tear to the forklifts. The scales are useful for weighing a wide variety of recycled material. Because some of the materials, such as paper, may be different densities, the system provides legal-for-trade accuracy, allowing Cougle’s to grade the material appropriately and secure its full value. The scales’ patented one-piece construction offers longer life, with no parts to break under strain, according to Avery Weigh-Tronix. The plates are coupled with Avery Weigh-Tronix’ patented Weigh Bar sensor technology. Regarding another benefit, the scales are bolted rather than welded to the fork carriage, avoiding damage to the truck, and making it easy to reinstall the scale onto a different lift truck when the equipment lease expires. The Avery Weigh-Tronix truck scale allows Cougle’s to weigh gross vehicle weights of up to 270,000 pounds and dual-tandem axle loads of up to 80,000 pounds. The scale is integrated with Avery Weigh-Tronix’s patented Weigh Bar technology at each section of the scale. When a truck drives onto the scale, the Weigh Bars measure the load on the platform. The Weigh Bars are made of high-strength alloy steel to ensure repeatability and long-term durability, according to the company. "The truck scale allows us to verify that the trucks are loaded correctly. In our business it’s important to make sure the trucks are under the allowed gross weight, but filled enough to meet customer requirements," Cougle says. "We are happy with the Avery Weigh-Tronix truck scale and the amount of time it saves us over our previous truck platform scale." – This sidebar was submitted on behalf of Avery Weigh-Tronix
Smith adds that if material is purchased by weight and by unit, it can lose its source identity when it is mixed with other like commodities. But if the material is tagged when purchased, it will retain its source identity and can have other attributes associated with it, such as chemistry or the person responsible for inspection, included on the tag. "If the material is properly received, it can be tracked throughout the system from that point on," Smith says.
Raising the Bar
Another perk offered by using inventory management software is the ability to grade and tag material at the point of receipt—even at the scale itself.
George Kane of software provider 21st Century Programming, Long Beach, Calif., says this capability is extremely helpful in getting data organized before it has time to get lost in the shuffle of day-to-day business. "Some companies, particularly in the paper business, have forklift-based scales, with tablet PCs mounted on the forklift," Kane says. "They can pick up the box, weigh it right then and [the software] adds it directly into their inventory. The inventory is really live—as soon as it hits the scale, your position is updated."
This kind of accuracy in grading helps with another inventory-related priority for recyclers—the ability to track material throughout its stay at any given facility and beyond.
For instance, inventory management software gives recyclers the capability to follow the chain of custody for a given load of scrap as it makes its way through the facility, according to Kane. Work in progress (WIP) capability tracks material as it is assigned to different processing centers throughout the facility. This feature is particularly useful to companies with more than one yard or those that might send material out to subsidiaries for processing, he says. According to Kane, with some systems recyclers can create a flow chart for their customers detailing how the material was handled and by whom.
However, even the most sophisticated software is not immune to problems related to operator error.
PROBLEM SOLVING. Human error—both intentional and unintentional—can cause problems for even the most well-designed systems. "Improper grading or adjusting of the received material will cause any inventory system to have problems," says Smith.
Entering the wrong information into the system will throw things off automatically, Kane agrees. "If a person knows it’s copper No. 1 but he puts it in as copper No. 2, the computer has no way to manage that," he says.
Limited physical space can challenge the best software programs. Martz says many systems fail when operators are unable to reliably determine a material’s source weight and grade before it is sorted and processed. "This is often due to a lack of space to segregate each grade and operator controls to ensure grades are not commingled," he says.
Many times, entering the wrong information is a simple operator mistake, but sometimes, an employee’s error isn’t so innocent. In either case, having a system that takes photographs is helpful in overcoming operator error. "If you’re weighing something on the scale and know there’s photographic proof, you’re less likely to mis-grade," Kane says. He also recommends that recyclers limit the number of employees who are allowed to edit and void items on the system. The inventory challenge specific to handlers of scrap is that material often comes in as one thing and ends up stored as another. "Once it’s cleaned and stored, tracking it is the hardest thing for any scrap yard," says Kane. "With scrap metal, paper or plastic, you buy as one thing one time, but it turns into several other items. You may buy copper plumbing scrap from a plumber, but you may end up with several grades of scrap."
To find everyday mistakes, Kane recommends taking physical inventory occasionally to check the information on the computer. "It’s important to take proactive control of your inventory—walking around your facility, checking loose bales, checking against the computer," says Kane.
Martz agrees. "Periodic physical inventory tallies or estimates proactively serve to validate book [inventory] against the actual inventory," he says. When outbound loads are short on grades that still show up in the book inventory or when the book shows negative values, "these are clear signs of an inventory system that is not being maintained," says Martz. "Unrealistic inventory values by grade also point to a potential problem," he adds.
No system is completely infallible, so by checking the physical inventory with the computer as standard procedure, recyclers can spot and fix any discrepancies early and help keep the system running smoothly. Additional capabilities like stock pile controls and the ability to re-cost inventory values at month end are valuable management tools, adds Martz.
The capabilities of inventory management software have grown considerably since recyclers first began using it, and Kane expects the systems to become increasingly more sophisticated as technology improves. Kane sees RFID tags in particular playing a large roll in the future of inventory control. "That’s the future—it’s not quite there yet, but it’s close," he says.
The author is associate editor of Recycling Today and can be contacted at jgubeno@gie.net.
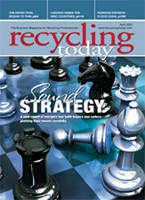
Explore the April 2007 Issue
Check out more from this issue and find your next story to read.
Latest from Recycling Today
- Nucor receives West Virginia funding assist
- Ferrous market ends 2024 in familiar rut
- Aqua Metals secures $1.5M loan, reports operational strides
- AF&PA urges veto of NY bill
- Aluminum Association includes recycling among 2025 policy priorities
- AISI applauds waterways spending bill
- Lux Research questions hydrogen’s transportation role
- Sonoco selling thermoformed, flexible packaging business to Toppan for $1.8B