
Avantium, a renewable chemistry company based in the Netherlands, plans to open a plant later this year that will enable commercial-scale production of a plant-based plastic that can be incorporated into packaging and recycled in traditional polyethylene terephthalate (PET) recycling streams.
Avantium’s YXY plant-to-plastics technology catalytically converts plant-based sugars into a chemical building block that can be used in a variety of chemicals and plastics, including polyethylene furanoate (PEF), a polymer used either as a replacement for PET or as a high-barrier liner in PET bottles.
PEF’s oxygen barrier properties are 10-times greater than PET, and its carbon dioxide barrier properties are 16-times greater, according to the company. The improved barrier properties can lead to a longer shelf life for foods and beverages, and they maximize the taste and fizziness of soft drinks.
“PEF is a new polymer—it’s new to the world,” Avantium CEO Tom van Aken says. “It is something that has not been produced at commercial scale before. We have been working on this since 2005.”
The process
The company opened a pilot plant 10 years ago in Geleen, Netherlands, that produces small quantities of furandicarboxylic acid (FDCA), a monomer that is a key building block for PEF along with plant-based monoethylene glycol.
After producing FDCA, Avantium delivers it to an existing polyester polymer production facility in Portugal to convert it into PEF under a tolling agreement.
Upon opening the new commercial-scale FDCA plant, Avantium plans to continue working with the Portugal plant for the final step of the process before distributing the PEF polymer to its customers.
The amount of PEF produced at the current pilot plant has been sufficient for Avantium to validate the technology.
“For more than 10 years, we’ve been making bottles, films and fibers,” Van Aken says. “It’s [a] much smaller scale, but we’ve been able to do tests to show that people can use existing blow molding machines to blow these bottles, they can use existing filling lines to fill these bottles, etc.”
The commercial FDCA plant under construction in the Netherlands will be operational sometime in the second half of this year, he says. Bottles produced with the new bioplastic could be available in supermarkets and elsewhere at the start of next year.
The company already has 15 offtake agreements—pledges from prospective customers to buy FDCA and PEF that Avantium plans to produce. Many plan to use PEF in bottle and fiber production, Van Aken says. Additionally, PEF can be used in clothing.
While most of the initial customers are based in Europe, many are global brands. “Brands like Louis Vuitton [LVMH Group] and [Danish multinational brewer] Carlsberg are working globally,” he adds. “We think that American consumers are going to get their hands on PEF in the near future.”
In February 2023, Avantium also announced a partnership with Origin Materials Inc., a sustainable materials company based in the U.S., to accelerate mass production of FDCA and PEF for use in plastics. The partnership aims to bring the technology platforms of both companies together to produce FDCA from sustainable wood residues on an industrial scale.
The licensing agreement will allow Origin Materials access to Avantium’s process technology to design and build an FDCA facility in the U.S. with an annual capacity of about 110,000 tons. Avantium will supply Origin Materials with FDCA and PEF to accelerate market development, according to a news release.
So far in the Netherlands, Avantium has been using sugar from food crops, such as sugar cane, corn, wheat and sugar beets, to produce FDCA and PEF. In the long term, however, the company would like to use nonfood crops and forestry and agricultural byproducts for the process.
Advantages of PEF
While Avantium isn’t the first company to manufacture bioplastics, the major advantage PEF offers is its compatibility with the existing PET recycling stream.

“PEF looks similar to PET, but, of course, it’s a different polymer,” Van Aken says. “The benefit is that we have demonstrated by doing numerous trials with recycling companies that you can blend PEF with PET.”
PEF would be a relatively small volume of the PET recycling stream and would not be detrimental to the recycled plastics’ properties.
“I think PEF is one of the very few products that doesn’t interfere with the PET recycling process,” Van Aken says. “In fact, the recycled PET that results out of this is actually a fraction better than normal rPET [recycled PET] because it has higher barrier properties. ... That is giving us an opportunity to bring PEF to the market and make sure that we can recycle it from the start.”
However, as the amount of PEF in the market increases, Avantium believes it would make sense to create a separate PEF recycling stream. The benefit would be to preserve the gas-barrier properties of recycled PEF. “That’s going to be something for the future,” Van Aken says.
Because of its superior barrier properties compared with PET, PEF is suitable not only for replacing PET bottles but also for replacing glass bottles and aluminum cans, he adds.
Avantium’s PEF is more expensive to produce than PET. However, Van Aken says as the technology matures and production volumes increase, the cost gap should narrow.
“It is dependent on scale because you need the economy of scale in order to bring down the cost,” Van Aken says. “We’re bringing a new polymer to market. Our first asset that we’re building right now in the Netherlands is 5,000 [metric] tons per year, which is a small plant in comparison to the regular PET plants operated today. Therefore, we’re currently selling PEF at a significant premium. If you produce PEF at the same scale as PET, you come to the same ballpark of pricing.”
Multiple life cycle assessments have been done on PEF, and the most recent, conducted by a European institution, shows it has a 62 percent lower carbon footprint than PET when used in bottles, Van Aken says.
“I still think that there is significant room to further reduce the carbon footprint of PEF because it is still at the beginning of its life cycle and there is a learning curve,” he adds.
The lower carbon footprint is logical, he says, because PEF starts from renewable sources.
About 10 percent of plastic used in manufacturing bottles and films ends up in nature, Van Aken says.
“We have evaluated with a third party what happens if PEF ends up in nature,” he says. “It demonstrates that PEF degrades significantly faster than PET. We don’t see this as an end-of-life solution, and we are focused on recycling of PEF.”

Van Aken says the company is not trying to market PEF as a biodegradable solution, however, it will not accumulate in nature as PET does.
Avantium hopes to build additional plants in Europe and Asia to serve markets across the world with its new resin.
Interested brands
Avantium has negotiated offtake agreements with a number of companies that include:
- Carlsberg Group – The Danish brewing company has signed a conditional offtake agreement with Avantium to purchase a fixed volume of PEF resin for various packaging applications, including its Fibre Bottle, a bio-based and recyclable beer bottle that contains an inner layer of PEF produced in Avantium’s current pilot plant. The outer shell of the bottle, produced by packaging company Paboco, consists of sustainably sourced wood fiber. The shell has the added benefit of insulation properties, which help keep beer colder for longer. The brewer has been sampling the bottles in pilot markets in Western Europe.
- Albert Heijn – The largest grocery chain in the Netherlands will be the first supermarket chain in the world to introduce PEF packaging for its store-brand products, Avantium says. Refresco, a global beverages bottler, will produce Albert Heijn’s new fruit juice bottle made from PEF once Avantium’s commercial plant is operational.
- AmBev – The Brazilian brewing company, part of the Anheuser-Busch InBev Group, the largest beer company in the world, will purchase PEF to make bottles for its soft drinks. AmBev and Avantium worked together to develop multilayer bottles for AmBev soft drinks, using PEF as a high-barrier liner in PET bottles.
- LVMH Perfumes & Cosmetics Houses – This global producer of perfume and cosmetics brands, including Parfums Christian Dior, Givenchy Parfums and Guerlain, signed an agreement to introduce PEF to the cosmetics market.
Avantium is on the verge of transitioning from a firm focused on research and development to a large-scale producer of PEF resin.
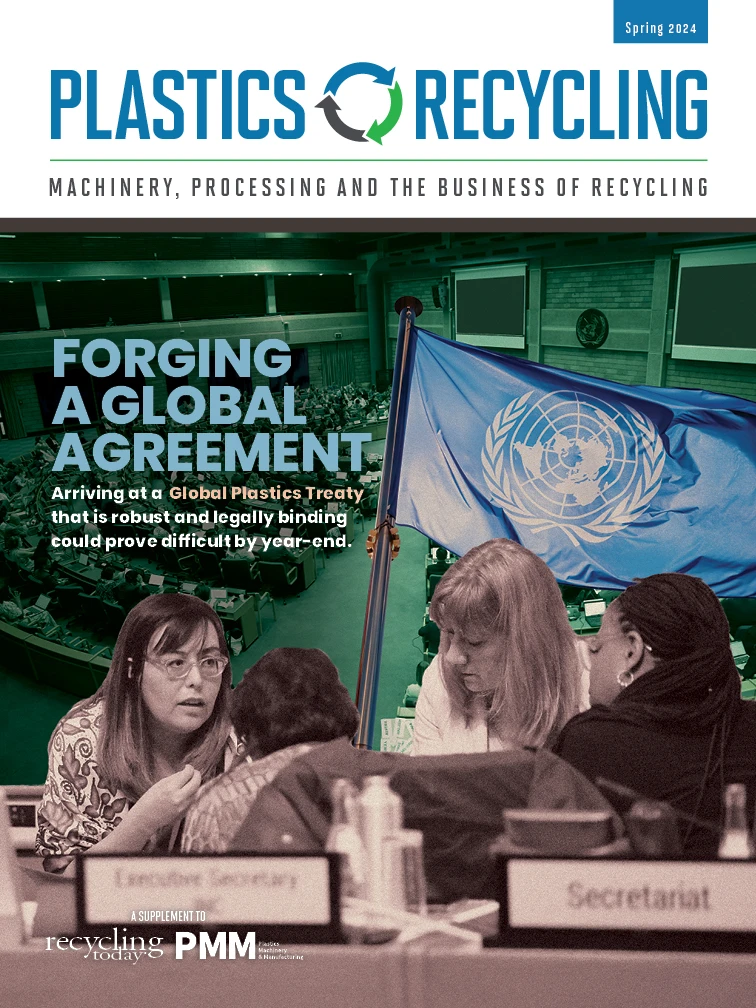
Explore the Spring 2024 Plastics Recycling Issue
Check out more from this issue and find your next story to read.
Latest from Recycling Today
- NWRA announces 2025 Driver of the Year, Operator of the Year winners
- The Scrap Show: Nanci Schuld of FE Trading Group LLC
- Call2Recycle Canada partners with RLG to advance battery collection
- Report delves into recovery opportunities for food-grade polypropylene
- Reimagining Supplier Payments in Metal Recycling: A Digital Leap Forward
- STEINERT Lithium Battery Detection and Removal from Waste Streams
- Driving the Future: Innovations in Waste & Recycling Technology
- Robin Wiener recognized for recycling leadership