Fuel tanks and fuel systems will fuel the next round in the market war over the physical makeup of new vehicles on the road. Environmentally, plastic has the early upper hand when it comes to designing for light weight and flexible molding. Steel comes to the fore later in a vehicle’s life cycle, when recyclability becomes a key concern for obsolete autos and light trucks.
The fuel tank has become a steel industry focus for regaining and retaining its market share in auto parts. When it comes to fuel tanks, steel has lost a considerable part of its traditional market to plastics. Look for the steel industry to bend over backwards-as well as twist around axle housings and curve past wheel wells-in its effort to remain a mainstay of fuel tank technology.
The steel industry’s ultimate success will be one more factor in determining how much recoverable metal enters the scrap yard when a vehicle hits the end of the road.
IN THE TANK
As recently as 1999, about 58% of global production of fuel tanks was steel. Market analysts project steel’s market share will drop to around 41% by 2004. The Steel Recycling Institute (SRI), Pittsburgh, and the American Iron & Steel Institute (AISI), Washington, gasped at the projection, then sat up and took action. The trade groups formed the Strategic Alliance for Steel Fuel Tanks (SASFT), headed by Peter Mould, Brighton, Mich. He is the principal of Automotive Steel Technologies, a steel consulting practice, and is program manager for SASFT.
The plastics industry’s numbers show an even more dramatic picture of the demise of steel fuel tanks. According to Bruce Cundiff, Troy, Mich.-based director of automotive for the American Plastics Council (APC), five years ago, 26% of the fuel tanks in new North American cars and light trucks were plastic. Today that figure is 72% in North America and roughly 50% worldwide. The plastics industry expects to do all it can to keep those figures growing.
Yet steel’s proponents see some rough spots for the plastics industry to overcome-spots where metals might have an advantage. The steel industry also expects to play a major role in the increasingly popular propane-fueled vehicle market, as fleet vehicles are outfitted with propane tanks that eventually will need to be recycled (see sidebar).
“The key now is that the OEMs are trying to meet the partial-zero emissions standards,” Mould says. Those standards go into effect in 2004. “We believe that steel has the best chance of doing this for the manufacturers right now.”
Automakers have rushed to lightweight vehicles to make them more fuel-efficient. Lighter vehicles get better gas mileage. However, the end-of-life disposal of those vehicles and their components also is a major concern for manufacturers, faced with tougher recyclability in Europe and possibly in the U.S.
Handling Propane |
Another fueling sector increasingly visible in dismantlers’ yards is the propane tank. Propane fuel vehicles are fairly commonplace in taxi and truck fleets. Not only do they offer an alternative to gasoline power, but they have some advantages in cold weather areas over the traditional gasoline engine. Soon their fuel systems will be hitting the dismantlers, and there is some question about handling the tanks and other parts of the system. “There has to be infrastructure out there to handle those propane systems,” says Doris Hill, senior staff engineer in General Motors’ Designing for the Environment group, Flint, Mich. “It is just that we haven’t needed it yet.” The steel industry, however, has checked out the handling of propane systems. Greg Crawford, vice president of operations at the Steel Recycling Institute (SRI), Pittsburgh, emphasizes that the tanks are recyclable . . . although he, too, is unaware of any ongoing, coordinated recycling activities for automotive liquid propane (LP) tanks. But he warns that no scrap dealer should accept whole, unprocessed propane tanks from a dismantler or anyone else — for basic safety reasons. “A qualified person must prepare the tanks,” he states. Preparation includes removal and capture of any residual fuel in the container. Next comes removal of the fittings, which typically are brass or bronze. “The empty vessel needs to be further modified, including mechanically crushing the tank or mechanically shearing the tank,” Crawford says. Under no circumstances should acetylene torches or any other sparking tool be used to cut the tank open. Since most propane vehicles today are fleet vehicles, the fleet owner should have qualified people on site to empty and crush the tanks. At that point, the recycler can be sure the tank is ready for processing. “Crushing or shearing validates that the tank is empty,” Crawford says, and it can go to scrap facilities and be processed like other steel. |
APC’s Cundiff notes that plastics have four big advantages going into the auto battle: first, plastics cost less, both for the material itself and in operating costs later in the vehicle’s life; it is light, giving it advantages for fuel economy; it can be molded into complex shapes; and it offers chemical resistance to the new blends and additives put in fuel today.
But if a material won’t recycle when the car is retired in five to 10 years, it may not be a long-term option for OEMs facing recycling mandates.
The toughest regulations auto manufacturers face are the European laws that require the filing of disassembly information on every vehicle. The laws require 85% recyclability of vehicle components, with that percentage increasing over the next decade. In the U.S., California leads the way for tougher requirements, especially in the fuel tank and fuel line area.
Another of plastic’s big intangible advantages is the one-stop, full-service purchasing offered to OEMs. Traditionally, the plastics industry offered a full-service fuel-tank operation, participating in the design of the tank, building of the tank, and sending it to the car manufacturer. The steel industry basically provided steel to the OEMs who built what they needed.
CARB STANDARDS
In North America, there is another bump in plastic’s road. The evaporative emissions standards became more critical. To meet those requirements, plastic fuel tank designers went to more complicated, multi-layer tanks with barriers in the middle. This added expense, making the multi-layer tanks roughly the same price as steel.
“In 2000, AISI decided to look at the issues and reclaim the market for steel,” Mould says.
“Automakers told us that they are searching for alternatives to plastic fuel tanks,” says Darryl C. Martin, senior director for automotive applications at AISI. He says this is because plastic designs currently are unable to meet the stricter requirements of the California Air Resources Board (CARB), which take effect in 2004.
“Automakers understand that CARB requirements influence auto regulations not only in California, but in many other states and other countries,” Martin says.
Mould says that even with the multi-layer plastic tanks, the plastics industry will still have problems meeting emissions standards. “We think steel is now going to get a second look by users,” he continues.
To help steel’s cause along, SASFT called on a diverse lot of companies. There are U.S., Canadian, Mexican, Japanese and European steel manufacturers; welding companies, and other steel-related firms involved.
“These companies came together and are trying to evaluate the competitive issues between steel and plastics,” Mould says.
He knows that the plastics industry will not give up without a fight and is working on plastics technology that will meet those same emissions requirements.
He’s right about that. “The beauty of plastics is that they offer a number of options,” says Don Little, chairman of the APC’s automotive work group. An employee of Dow Automotive, he is on top of efforts to manufacture more sophisticated and thinner plastics that will meet design needs at lower costs.
“We are confident we will be able to produce plastics to meet CARB requirements,” he says.
A HORSE RACE
In fact, it could be a real horse race: plastics manufacturers have light weight and product flexibility on their side. Steelmakers have a less permeable product and a simpler product to recycle, one with a well-established recycling infrastructure.
While the plastics industry is striving to meet the permeability standards, steelmakers are working on the flexibility of the material in auto design.
A project is underway right now to duplicate in steel the saddle-shaped plastic tanks being used on today’s vehicles.
Are any of the OEMs buying? “Not yet,” Mould acknowledges. “But we know every OEM is looking at every alternative, including steel.”
Mould expects the break for steel to come in the 2004 design year.
“The issue really hasn’t come to a serious point yet,” he remarks. Mould notes that the recycling industry has yet to see large numbers of vehicles with plastic fuel tanks come to end-of-life yet. In fact, that could be as much as five to 10 years out.
“Recycling is a problem with plastic tanks unless there is some radical new technology developed,” Mould says. Even then, he questions the economic feasibility of such processing.
Dismantlers in many locations must remove any fuel tank-plastic or steel- from the hulk before sending it to the shredder. Separating multiple plastics from one another is usually an unwelcome task.
The Europeans are mandating recovery. There is government legislation in place and fees are exacted to cover the cost of scrap processing. The U.S., generally, relies on more of a free-market approach. Here, the questions revolve more around good engineering and product responsibility.
“Competitive plastic fuel tanks will be available to meet CARB standards,” says APC’s Cundiff. The industry is looking at alternative technologies, like thermoforming, to provide further design flexibility.
Cundiff notes that auto designers look at all aspects of vehicle design-not just end-of-life-when choosing materials. Flexibility in fuel tank design means flexibility in all the other underbody components.
In addition, APC director of technology Mike Fisher says that the plastics industry’s development horizon goes a lot further than four or five years. Already, they are developing polymers to work in combination with steel and aluminum to meet alternative designs.
Plastic’s proponents note that a lighter car not only reduces fuel consumption, but also requires a smaller engine producing less pollutants.
TODAY VS. TOMORROW
Plastic clearly has a value in lightweighting vehicles. The problem comes with recovery. The plastic recycling industry is built around HDPE and PET. Unfortunately, engineers have not designed a car built around the same plastics as are used in milk or soda bottles (HDPE and PET are the most commonly recycled plastics and a good recycling infrastructure exists for both types of plastics-but for few others, and especially not mixed plastics).
Further complicating matters, there are over two dozen different chemistries of plastics in cars. Despite plastic’s plans for the future, Greg Crawford, vice president of operations at SRI, says the opportunities to recycle that assortment of plastics today is “nil.” He adds, “Plastic tanks have no scrap value. The dismantler is still obligated to remove the tank. And there is a disposal cost to landfill it.”
Martin adds that steel fuel tanks not only can meet durability and emissions requirements for fuel tanks, they also are fully recyclable. “That is an advantage of particular importance as governments continue to tighten requirements for end-of-life vehicles,” Martin says.
To make plastic fuel tanks meet stricter requirements for permeability likely will mean making them heavier. This would eliminate their lightweighting advantage and would go a long way toward mitigating the price advantage lighter plastics enjoy. And when it gets to the recycling stream, such plastics are considered contaminated, limiting their reusability.
STEEL NOT HOME FREE
Steel faces its own problems. It is not the most pliable material to form into the odd configurations often required on the vehicle’s underbody.
Martin says that problem is a thing of the past, thanks to the advances in materials, such as highly formable steels that allow for greater flexibility in forming complex shapes. In addition, steelmakers have come out with improved corrosion-resistance techniques that make steel more attractive for fuel tanks.
Both plastic fabricators and steel manufacturers claim the inside track. Like coaches before a big game, both are aware of their side’s strengths and the other side’s weaknesses.
For the recycler, one point remains paramount: both sides are fully convinced that recycling cars and fuel tanks-whether steel or plastic-is an absolute “must” for the future. That bodes well for recycling advocates, though in the U.S. that recycling is much more likely to occur if there is a paying end market for the material.
The author is an environmental writer and Recycling Today contributing editor based in Strongsville, Ohio.
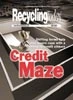
Explore the May 2001 Issue
Check out more from this issue and find your next story to read.
Latest from Recycling Today
- Magnomer joins Canada Plastics Pact
- Electra names new CFO
- WM of Pennsylvania awarded RNG vehicle funding
- Nucor receives West Virginia funding assist
- Ferrous market ends 2024 in familiar rut
- Aqua Metals secures $1.5M loan, reports operational strides
- AF&PA urges veto of NY bill
- Aluminum Association includes recycling among 2025 policy priorities