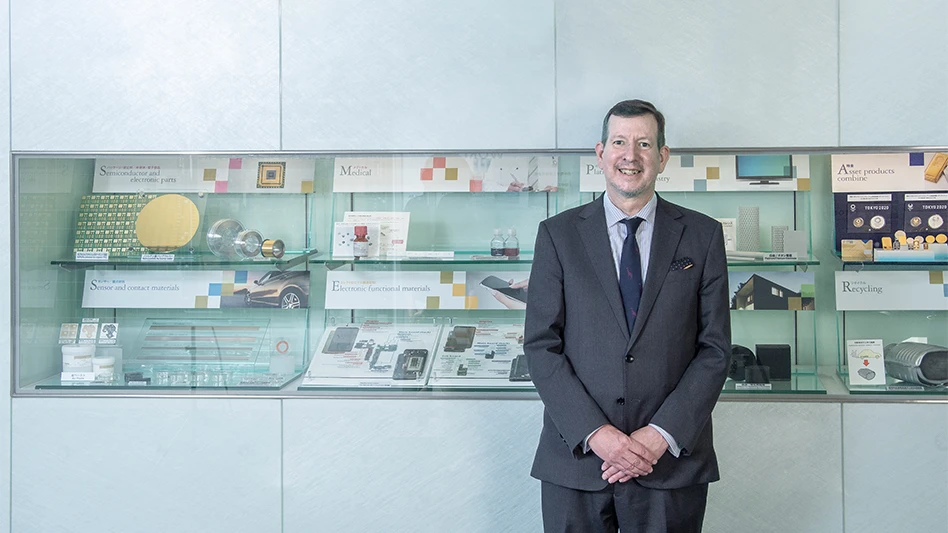

When it comes to the value per ton, pound or even ounce, no materials make more sense to recycle than precious metals. Tokyo-based Tanaka Precious Metals, which operates a smelter and refinery in Shonan, Japan, has been doing just that since 1976.
Although the company has an established presence in the recycling sector, the sustainability-driven tenor of the times has it calling more attention to its methods via its RE Series line of 100 percent-recycled-content gold, silver and platinum group metals (PGMs), as well as some minor metals.
The company’s General Manager of Business Strategy Andrew Farry says while its RE Series was launched in 2021, when it comes to recycling, Tanaka has “been doing this forever, basically.”
In an interview with Recycling Today, Farry talks about the greater awareness among electronics original equipment manufacturers (OEMs) and other precious metals users that their involvement in recycling is worth publicizing more than it might have 10 or 20 years ago.
Recycling Today (RT): When did the company begin planning for its RE Series product line, and to what extent has it involved investing in facilities and equipment?
Andrew Farry (AF): The RE Series concept is nothing new to us. It’s basically receiving material back from our sources, recycling them and putting them back into products we supply to our customers. It’s nothing new, but some customers [such as some in the semiconductor industry] are starting to focus on meeting sustainable development goals [SDGs].
What SDGs come down to is responsible refining, which is what we’ve done for years. The concept is to bring back as much from our customers and then tap into the urban mines. What we put out there, bring it back—cradle to grave.
This concept is being applied not only to precious metals, but [also] with the automotive industry there are initiatives to recycle almost every component. Batteries are one part of that.
Concerning electronics, it’s the same thing. Many electronics manufacturers have initiatives to ensure that anything that goes into their products has to be recycled back.
It’s also about consumer awareness. Instead of throwing these products away, people are learning there is value in these products—you’re bringing them back into the supply chain by recycling.
SDGs are helped by consumer awareness plus the responsibility of the manufacturers. The OEMs want to rely less on mines and more on recycled products to create a closed circle.

RT: To what extent has the RE Series effort provided Tanaka with a way to have some control over its own precious metals supply chain?
AF: What we’re trying to do is reduce the amount of our dependence on virgin material. We’ve reached 40 percent of recycled materials being used [as of the end of 2022].
Our refinery harvests recycled gold, silver, platinum, palladium, rhodium and a couple other high-value metals. We try to use as much as we can recycle and not rely [solely] on primary sources. There are still mines in South Africa, Russia, Canada, the U.S. and other places producing these metals, but we’re trying to reduce our footprint at those mines and increase it at the urban mines.
We still need mines and mineral resources from the ground, but what we and our customers are trying to do is reduce our dependence on them.
RT: To what extent will RE Series metals be available to outside buyers, or are they for in-house use only?
AF: It’s an industry initiative. Some of the big companies like Apple are trying to reduce their footprint on sourcing materials from mines. They’ve created initiatives that back the RE Series effort—it offers them what they’re looking for in terms of recycling. They are looking at their global footprint and trying to figure how they can reduce use of mined precious metals and base metals.
The semiconductor and electronics industries are trying to set initiatives to reduce the amount of material procured from mines. Our series is part of that whole process—what we put out we bring back. That’s the whole basis for this, and we’re doing what we can to support that initiative.

RT: How would you characterize the return on investment aspects of the RE Series effort?
AF: Recycling has been in our spectrum for years; it’s nothing new to us. Customers now request that more in what they receive from us. It’s not a big bottom-line issue. There is not a lot of extra capex on our refining side since we have a lot of refining capacity. For us, it’s not a big money winner on its own, but it’s something we’ve done forever.
The industry is changing a little. I don’t see enormous changes in our volume in refining, but specific customers are asking for re-refined materials. There is a shift, but we’ve not needed to invest further in those processes because we largely have them in place, although we are adding capacity in Taiwan. It’s more about responsibility and what the industry is expecting.
For us, we’ve been doing this forever, basically. We’ve updated our equipment on a regular basis, but it’s not something that is giving recycling-specific returns.
We’re not trying to make money off this, we’re trying to stay in line with industry standards.
RT: How do you think other companies can learn from the RE Series effort, and to what extent is Tanaka willing to share portions of what it has learned?
AF: It really is an industry initiative. We’ve been requested to maintain and grow our focus on recycling, and some of our sister companies around the world are being asked the same questions. They, too, have probably implemented initiatives to enhance their supply chains. There is no rivalry on that front; no one’s standing out in this respect. I think we’re all kind of absorbing it and responding to the request of our customer base.
RT: To what extent will maintaining and growing the RE Series line require the company to place an increased focus on collecting end-of-life materials?
Sponsored Content
Labor that Works
With 25 years of experience, Leadpoint delivers cost-effective workforce solutions tailored to your needs. We handle the recruiting, hiring, training, and onboarding to deliver stable, productive, and safety-focused teams. Our commitment to safety and quality ensures peace of mind with a reliable workforce that helps you achieve your goals.
AF: For our RE Series, on the procurement side, we’ve been involved in recycled materials for four decades, so this is nothing new to us. If you were dependent only on primary sources, you would be dependent on the mines. So, for four decades, we have been reducing that dependence via recycling.
Part of what we seek for our refinery is spent auto catalysts. And, in that sector, we get an enormous amount of our PGMs through recycling, so this is an extension of what we’ve been doing for years.
Mine locations can lead to problems from geopolitical considerations or strikes or floods. So, limiting one’s dependence on primary sources has always led to recycling.
The scarcer the material, the more you don’t want to be fully dependent on those primary sources, and this is especially true of PGMs. Therefore, urban mining is very important.
If you throw out a smartphone, you’ve thrown out a lot of money. There is value in those products, and it does not necessarily have to be precious metals but also the base metals, aluminum and copper. Obtaining more of those can be about educating the public and getting a little bit greater consumer awareness of phone recycling.
Get curated news on YOUR industry.
Enter your email to receive our newsletters.
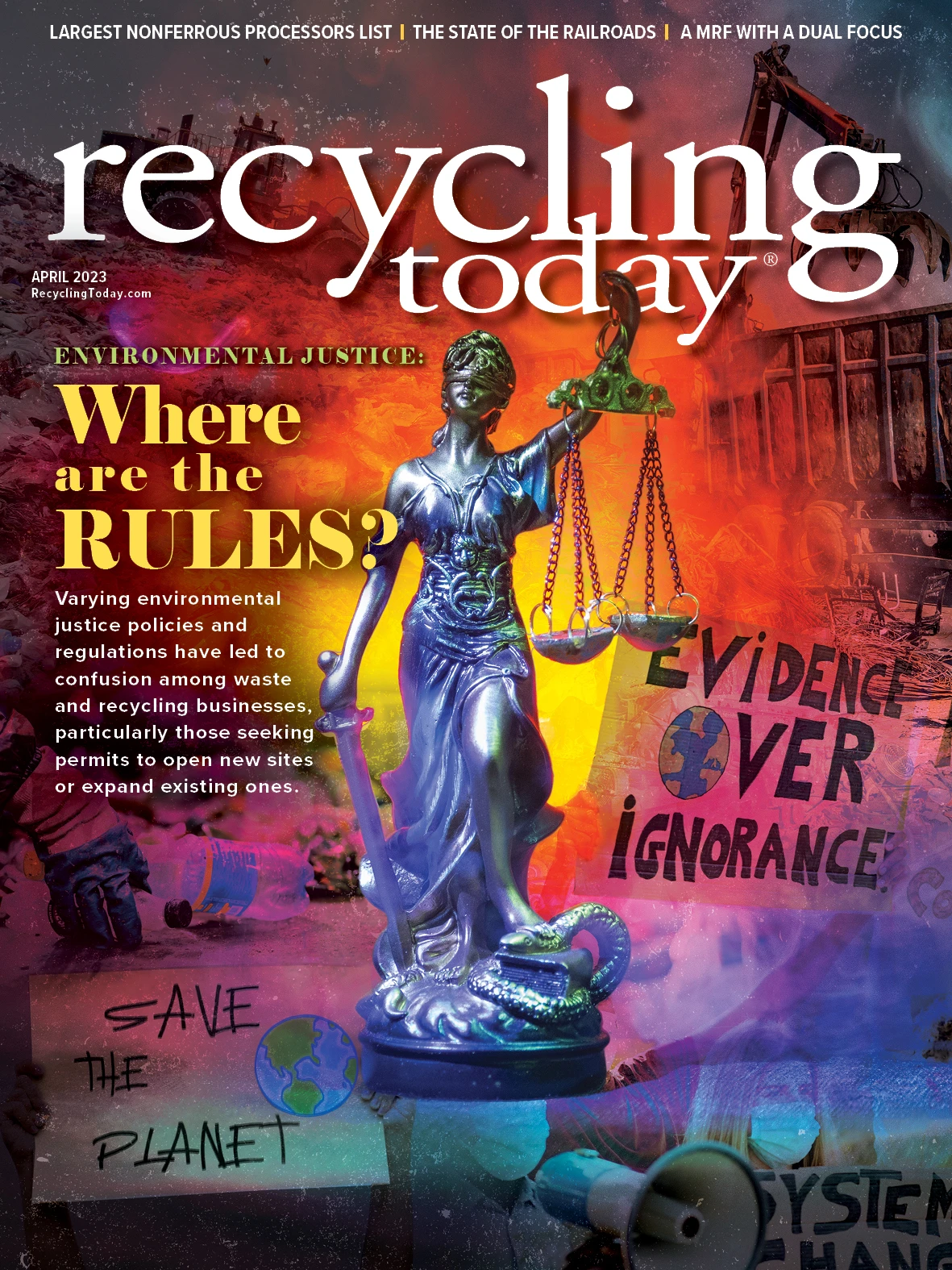
Explore the April 2023 Issue
Check out more from this issue and find your next story to read.
Latest from Recycling Today
- Nucor expects slimmer profits in early 2025
- CP Group announces new senior vice president
- APR publishes Design Guide in French
- AmSty recorded first sales of PolyRenew Styrene in 2024
- PRE says EU’s plastic recycling industry at a breaking point
- Call2Recycle Canada, Staples Professional expand partnership
- Circular Services breaks ground on north Texas MRF
- Tariff uncertainty results in choppy nonferrous scrap flows