Throughout the years, professionals in the secondary plastics industry have made huge strides to separate themselves from the competition by becoming more innovative.
"There are hundreds in the plastics recycling industry who just grind or pelletize, so to be competitive they have to ask themselves, ‘How can I differentiate myself from the crowd?’" says Scott Melton, president of ACI Plastics, an American Commodities Co. in Flint, Mich.
Professionals have responded to this question in a number of ways, including exploring new processing technology, investigating new end markets and, in some cases, forming joint ventures, which can help to put them ahead of the rest when it comes to plastics recycling.
TECHNOLOGICAL ADVANCEMENTSProfessionals are constantly working on ideas that will help them stick out in the plastics industry. ACI’s idea was to become more innovative by forming partnerships that have helped the company create new products and processes for its plastics.
ACI offers size reduction (grinding and shredding), paint and coating removal, compounding, pelletizing and full
laboratory and logistic services.
MBA Polymers' Austria plant processes approximately 40,000 tons of feedstock per year.
In 1999 ACI formed a joint venture with the European company WIPAG to install a line that separates automotive instrument and door panels.
"The nice part is the by-products are 100 percent recycled, with all three components being used in an application and nothing going to a landfill," Melton says.
ACI sells the skin separated from the door and instrument panels to a company that makes the inside of garden hoses, the polyethylene foam is sold to a company in Ohio that uses it for carpet backing and the substrate, the most valuable component, is used back in the original applications (door or instrument panels).
"In the past seven years we have diverted 70 million pounds that were going to the landfill that now are going back into applications," Melton says.
Maine Plastics has also been looking into new technology to improve its grinding, baling, shearing and shredding processes. The company uses separation technology to take general material and remove contaminants.
"Where we are most innovative is in identifying material," says Robert Render, president of Maine Plastics in Zion, Ill. "When we get material, we properly identify all the properties, find where the problems are going to be and then determine the right application, market and process for it," Render says.
He says he is always looking for new ideas and technology at trade shows that he can apply to Maine Plastics’ processes. Render is currently pursuing a new way to clean agricultural film and dirty materials that doesn’t require any water.
"I think you constantly have to be innovative in terms of your equipment, lab testing capability and training of people," Render says.
MBA Polymers Inc., well known for recycling plastics from highly mixed complex streams, such as those created by the shredding of end-of-life computers, appliances, electronics and automobiles, is also continuing to improve its processes.
"Our innovation is the ability to extract and purify many different types and grades of plastics from complex mixtures," says Dr. Mike Biddle, president and founder of MBA Polymers Inc., Richmond, Calif. "This is important because the vast majority of plastics end their lives attached to and mixed with many other types of materials, and it’s extremely difficult to separate them, as most traditional separation methods don’t work for plastics."
MBA’s process involves more than 20 different unit operations, including particle size reduction, materials liberation, removal of non-plastics and aggressive washing and sorting of the plastics not only by type but also by grade, Biddle explains. After the final purification, the sorted plastic flakes are then compounded and upgraded to meet customer specifications, he adds.
Biddle says MBA Polymers is also innovative in its business model by
building a global network of collection and processing facilities in North America, Europe and Asia and the company is looking to build more facilities.
Online Sidebar - Cost Concerns
Click here to view online only sidebar
"We have built an international team of professionals from the plastics, recycling, mining and manufacturing industries," Biddle says. "We view ourselves as a plastics supplier rather than a plastics recycler—we simply use innovative technology and business design to lower our cost basis compared to traditional plastics companies," he adds.
BUSINESS EXPANSIONSInnovations in plastics recycling are not only seen in technology, but also in professionals’ business models.
Plastic Nation started in the late ’80s as a broker of plastic scrap and has evolved into a processor over the years.
The company’s innovation lies in its merger and acquisition activity, according to Mark Christopher Graziadei, VP of business development for the Boca Raton, Fla.-based company.
"In addition, setting up national programs with suppliers by providing processing equipment allows Plastic Nation to secure material and establish long-term relationships with its vendors," he says.
"Merging and partnering with other companies increases our range as to what we can do," Graziadei adds.
The company’s facilities take commingled plastics from the curbside and separate, grind, wash and upgrade the material before marketing it to manufacturers.
FUTURE INNOVATIONSMaintaining a competitive edge requires continued innovation.
Melton is expanding ACI to two new locations. But, before making a definite decision, Melton says he wants to make sure the company will have enough material coming in and enough customers in the area to supply.
"We’ll be giving our molders their scrap back, but we’ll also supply them raw material from recycled resin, which comes from 25 to 50 percent recycled material," Melton adds.
Plastic Nation will continue looking for businesses that complement its processes as well as looking for new opportunities, such as a current plan involving alternative energy, Graziadei says.
Professionals say to be successful in the plastics industry, a company must have a quality program, people who know what they are doing, competitive prices and, most importantly, new ideas. As professionals look toward the future, they will continue to build upon these principles to remain in the competition.
The author is assistant editor of Recycling Today and can be contacted at kmorris@gie.net.
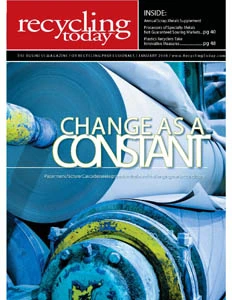
Explore the January 2008 Issue
Check out more from this issue and find your next story to read.
Latest from Recycling Today
- Nucor receives West Virginia funding assist
- Ferrous market ends 2024 in familiar rut
- Aqua Metals secures $1.5M loan, reports operational strides
- AF&PA urges veto of NY bill
- Aluminum Association includes recycling among 2025 policy priorities
- AISI applauds waterways spending bill
- Lux Research questions hydrogen’s transportation role
- Sonoco selling thermoformed, flexible packaging business to Toppan for $1.8B