
Three companies received the inaugural Re|focus Sustainability Innovation Awards from the Plastics Industry Association (PLASTICS), Washington, for their design and materials innovations.
Circular Polymers and Broadview Group International (BGI), Brook Park, Ohio, were honored in the end-of-life category for a rotary impact separator, which separates postconsumer carpet into clean fiber and a limestone calcium carbonate granulate.

Paris-based Tarkett was recognized in the design category for its Ethos modular carpet tile with Omnicoat Technology that was created using recycled windshields and safety glass.
Dell, Round Rock, Texas, was awarded in the materials category for its Latitude 5000 Notebook, which contains a structural material for the notebook computer housing made from 50 percent recycled content by weight.
The association received 39 entries from 11 industry sectors in nine countries.
“The submissions received were creative, and these particular innovations display real promise in commercial applications that show how we can scale these new technologies,” says Kim Holmes, the association’s vice president of sustainability.
Judges included association members and members of the Society of Plastics Engineers Sustainability Division.

End-of-Life
The rotary impact separator is a patented machine BGI developed that separates postconsumer carpet into clean face fiber, clean backing fiber and calcium carbonate. The process uses mechanical force to separate face fiber, backing fiber and calcium carbonate from backing material. No washing, chemicals or high heat are needed.
The separated carpet fibers are used as feedstock for chemical recycling to produce virgin-like resin. The fiber also can be pelletized or densified and used in injection molding. The calcium carbonate is used in road construction and as a filler in rubber and plastic products.
Circular Polymers licensed the exclusive rights in North America from BGI to use the rotary impact separator. Circular Polymers opened a plant in Lincoln, California, in 2018 to process 30 million pounds of carpet per year using the separator. An estimated 5 billion pounds of carpet are sent to landfills every year in the U.S. and Canada.
“We plan to open additional plants in the U.S.,” Circular Polymers CEO David Bender says. “But incentives are important to make this economically feasible. Outside of California, only 1 to 2 percent of carpet is being recycled in the U.S.”

The company opened its first plant in California because it is the only state in the U.S. that charges an assessment on all carpet sold or shipped in the state. The Carpet America Recovery Effort (CARE) raised its assessment fee, which was established in January 2017 at 25 cents per square yard, to 35 cents per square yard effective Jan. 1. The assessment is collected by retailers from consumers and is remitted to CARE. Subsidies are paid in the form of grants to carpet recyclers, such as Circular Polymers.
While Bender declines to reveal his company’s investment in licensing the technology and building the plant, he says Circular Polymers received a $500,000 grant from CARE. It also received a $2 million loan from California’s Department of Resources Recycling and Recovery (CalRecycle) for new equipment.
BGI spent more than $3 million to develop the technology.
“Our technology processes all carpet types: nylon 6, nylon 66, PET and polypropylene,” BGI President Joe Bork says. “Carpet recycling is done by product type because nobody wants to buy a mixed polymer product.”
The rotary impact separator shreds the carpet, and rotating paddles inside the machine beat it into pieces, removing 80 percent of the calcium carbonate. Another part of the machine further removes the calcium carbonate and adhesive. The machine separates the carpet’s face fiber from the backing fiber and cleans each fiber type independently. The machine discharges clean face fiber, clean backing fiber and calcium carbonate.
Chicago-based PureCycle Technologies, a partner of Circular Polymers, is commercializing a patented recycling process that transforms plastic feedstock into virgin-like resin. “What Circular Polymers has done with processing postconsumer carpet back into raw materials for chemical recyclers is not only revolutionary but [also] an incredible model for us all, considering the large volumes of feedstock that are being landfilled today,” says David Brenner, PureCycle chief integration officer.
Design
Tarkett, a leading manufacturer of commercial floor coverings, used a previously untapped material stream—windshields and safety glass—to develop Ethos, a high-performance polymer made of polyvinyl butyral (PVB). Combined with the company’s Omnicoat Technology, the material is used to make modular tile that is an alternative to polyvinyl chloride (PVC) soft-surface tiles. Omnicoat Technology is a proprietary coating that creates a chemical barrier that works to overcome problems with flooring substrate, such as unevenness. It is used in conjunction with Tarkett Tape to install Ethos modular carpet tile over flooring substrates that previously required time-consuming and costly testing and floor preparation.
The Ethos modular carpet tile is Cradle to Cradle Certified Silver (v3), the first U.S. modular carpet tile to achieve this level of certification. Since Ethos is designed with recycled materials and can be recycled through Tarkett’s ReStart Program, it is an example of a circular-economy product.
“The Ethos product line was an exciting development, created in response to an important customer partnership,” says Paul Evans, Tarkett vice president of research and development.
“Our development provided the performance and economics requested by the client while diverting millions of pounds of previously unusable material from landfills,” Evans says.
Materials
Dell worked with suppliers to create a structural material for its notebook computer housing made from 50 percent recycled content by weight. Dell used 20 percent postindustrial recycled carbon fiber combined with 30 percent postconsumer recycled content resin. That material is molded into a notebook computer top cover for the company’s Latitude 5000 series notebooks, which are used commercially and must meet tough durability requirements.
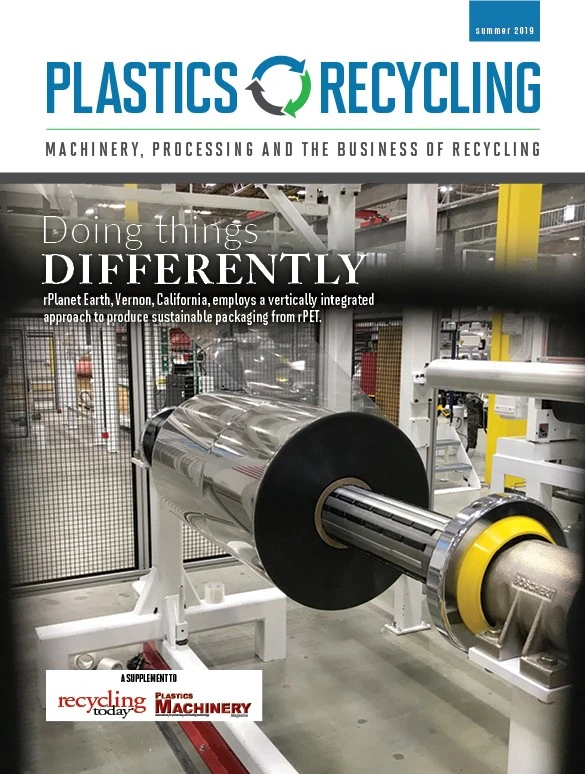
Explore the June 2019 Plastics Recycling Issue
Check out more from this issue and find your next story to read.
Latest from Recycling Today
- GFL opens new MRF in Edmonton, Alberta
- MTM Critical Metals secures supply agreement with Dynamic Lifecycle Innovations
- McClung-Logan Equipment Company joins Tana’s authorized dealer network
- Grede to close Alabama foundry
- Plastics Recycling Conference 2025: Working toward their targets
- SWACO rolls out new commercial recycling and food waste programming
- Updated: Matalco to close Canton, Ohio, plant
- Metso launches electric Anode Weighing and Casting Machine