
The world is paying increasing attention to the broad concepts of sustainability and circulatory economics. This focus will certainly affect plastics recycling in the near future. In particular, discarded plastics that are accumulating in the world’s oceans and waterways are clearly evident and negatively viewed.
An estimated 8.8 million tons of plastics reach the oceans per year. Areas of plastic waste twice the size of Texas (known as the Great Pacific Garbage Patch) are in the Pacific Ocean between the West Coast and Hawaii. Piles of discarded plastics have accumulated in harbors and on beaches. Additionally, in India, eight brands of sea salts marketed as being from the Mumbai region were found to contain microplastics, according to an article in the September 2018 issue of Chemical & Engineering News.
Many initiatives have been introduced to prevent this tide of plastic waste. Canada, for instance, has an active national program designed to keep beaches free of plastic debris.
Other efforts are dedicated to collecting litter. During World Cleanup Day, which took place Sept. 15, 2018, plastics and other waste materials were collected and disposed of properly.
The Ocean Cleanup, founded by Boyan Slat, a Dutch innovator, involves more than 80 engineers, researchers, scientists and computational modelers working to rid the world’s oceans of plastic. The organization is evaluating a device consisting of a 2,000-foot-long floating boom made of plastic with a tapered 10-foot-deep screen designed to trap some of the 1.8 trillion pieces of plastic in the Great Pacific Garbage Patch. The collected plastics will be retrieved periodically and taken to recyclers. (The system was being brought back to Hawaii for repairs and upgrades as of the start of this year.)
Of course, not all discarded plastics end up in the oceans. A larger quantity, in the form of household, commercial and industrial refuse, is collected by hauling companies and landfilled. All of this discarded plastic should be recycled; however, figuring out how to do this most effectively is a formidable challenge.

Defining end-of-life plastics
First, what exactly are end-of-life plastics? One definition is that they are meltable, extrudable plastics that have been used once for their original purposes.
Resin identification codes were designed for some of the most abundant plastics:
- PET, polyethylene terephthalate (No. 1);
- HDPE, high-density polyethylene (No. 2);
- PVC, polyvinyl chloride (No. 3);
- LDPE, low-density polyethylene (No. 4);
- PP, polypropylene (No. 5);
- PS, polystyrene (No. 6); and
- Others (No. 7).
These plastics, with the exception of PET, have long linear chains of carbon atoms in common. The chains in PET also contain a multitude of oxygen atoms. In the process of manufacturing, the chains of all plastics are induced to lie closely together so interchain forces are created. Although these forces are individually tiny, when the chains are sufficiently long, the sum of the energy of these tiny interchain forces acting together can equal or exceed the energy of a single carbon-carbon linkage. That is why plastics must be composed of long molecules.
During recycling, any system is confronted by the very strong linkages of the carbon-carbon chains and the weak but multitudinous interchain bonds holding these strong main chains together in a complex aggregate.
One apparently straightforward approach to recycling is to simply melt the plastic scrap for subsequent pelletization. The resulting pellets can then be sold as a lower quality substitute for virgin plastics. Melting distorts the parallel alignment of the long chains so the tiny interchain forces no longer hold the aggregate together to provide strength to the plastic. This mechanical approach also requires sorting the plastic scrap because different plastics, when molten, might not be truly compatible with one another to develop cohesive interchain forces again at a later stage. Other components of the plastic scrap, such as colorants and plasticizers, might also play an adverse role, interfering with chain alignment.
An alternative recycling approach is to cut these long chains into smaller pieces by applying heat to the dry plastic scrap in the absence of oxygen in a batch process called pyrolysis. This method often uses multiple large, double-walled metal tanks within which the plastic scrap mixture is slowly stirred, maintaining contact with the inner heated wall of the tank to achieve adequate heat transfer. The wall can be heated by burning the gaseous lowest molecular weight pyrolysis products generated within the tank. Pyrolysis of a batch of plastic scrap takes several hours, after which residues and char in the tank must be removed for disposal before the next batch can be treated.
The amount of supercritical water employed can be minimized so the cost of heating the water to a state of supercriticality is as low as possible.
As some of the carbon-carbon bonds in the plastics are broken by the dry heat inside the tank, each of the separated carbon atoms on either side of a broken bond carries a single electron: a free radical. These free radicals are highly reactive and can combine with other particles to form a black char.
Dry pyrolysis processes generate about 20 percent char by weight, which is a considerable economic negative. The amount of char generated by any published pyrolysis procedure can be roughly estimated by simply subtracting the weight of the oil produced by the process from the weight of the plastic feedstock.
Applying supercritical water
The disadvantages of dry pyrolysis systems for recycling plastics can be avoided by including a small amount of water. In 1822, a French engineer showed in an experiment that ordinary water is transformed into a new substance called supercritical water when heated above 705 F. The remarkable properties of this new form of water are now conveniently accessible, according to a 2012 book by Yizhak Marcus titled Supercritical Water: A Green Solvent: Properties and Uses.
The temperature at which supercritical water can exist is well above the melting or softening point of all plastics. This means the reaction with supercritical water involves the facile mixing of two fluids rather than a solid plastic and a liquid. Additionally, at such temperatures, supercritical water carries more energy than is necessary to cleave the most common carbon-carbon bonds in the plastics within seconds. That means the costly, hours-long reaction times needed to reduce the size of the plastic molecules in dry processes are not necessary. Finally, supercritical water is capable of donating hydrogen atoms to combine with and stabilize the duo of reactive short chain ends resulting from the carbon-carbon bond separation, which otherwise form char.
Using supercritical water to convert solid plastics into liquid fuels requires sophisticated, computer-controlled, continuous engineering if the most attractive economics are to be attained. For example, the plastic must be shredded and melted so it can be passed through a conventional commercial extruder. The continuous molten stream of plastic that emerges from the extruder then encounters a shower of supercritical water within a small pressured reactor zone of adjustable volume for just a few seconds.
Sponsored Content
Labor that Works
With 25 years of experience, Leadpoint delivers cost-effective workforce solutions tailored to your needs. We handle the recruiting, hiring, training, and onboarding to deliver stable, productive, and safety-focused teams. Our commitment to safety and quality ensures peace of mind with a reliable workforce that helps you achieve your goals.
The amount of supercritical water employed can be minimized so the cost of heating the water to a state of supercriticality is as low as possible. Ratios of 25 percent water to 75 percent solid plastics are practical and are in contrast to the highly diluted slurries of plastics needed in other water-based systems where pumpability is essential.
From all of the foregoing chemical engineering fundamentals, it should be clear that continuous, chain-disruptive reactions with supercritical water will play a key role in the transformation of all types of plastics, sorted or mixed, into easy-to-handle liquids.
Get curated news on YOUR industry.
Enter your email to receive our newsletters.
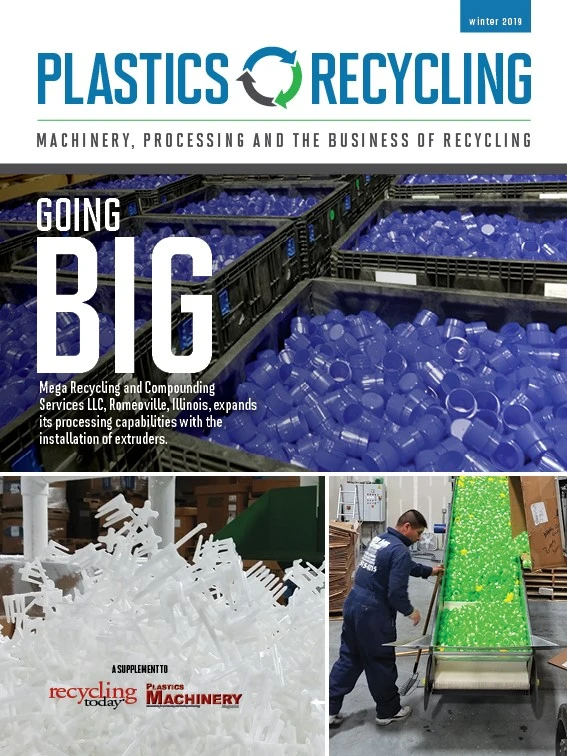
Explore the February 2019 Plastics Recycling Issue
Check out more from this issue and find your next story to read.
Latest from Recycling Today
- Toppoint Holdings expands chassis fleet
- Lego creates miniature tire recycling market
- Lux Research webinar examines chemical recycling timetables
- Plastics producer tracks pulse of wire recycling market
- Republic Services, Blue Polymers open Indianapolis recycling complex
- Altilium produces EV battery cells using recycled materials
- Brightmark enters subsidiaries of Indiana recycling facility into Chapter 11
- Freepoint Eco-Systems receives $50M loan for plastics recycling facility