It is interesting that the old discussion regarding the advantages of using a large shredder compared to those of using smaller shredders has found renewed vigor lately. At The Shredder Co., Canutillo, Texas, during the past year, we have taken orders for four small shredders and seven large shredders. That might indicate a preference for large machines, but the locations and the circumstances for each plant differ greatly and need to be examined for clues other companies should consider when deciding what size auto shredder to install.
Before discussing whether the new shredder should be large or small, it is probably a good idea to look at whether a new shredder is a good idea in any event.
MATERIAL SHORTAGE
The emergence of China and India as developing economic powers, fueled by their adoption of market economies, is creating huge consumer demand for material goods such as automobiles, appliances, cell phones and other electronic goods, housing, commercial buildings and highways and other infrastructure projects.
An excellent new book by Robyn Meredith titled The Elephant and the Dragon explores the reasons why India’s and China’s economies are developing in such robust but different ways. In addition to the Elephant’s (India’s) and the Dragon’s (China’s) economies, many other developing economies are scattered around the world, each of which is populated by people who want to join the consumer society. In the U.S. with about 5 percent of the world’s population, we have been consuming about 30 percent of the world’s nonrenewable resources. To understand the magnitude of this issue, please consider that according to a recent edition of the Economist magazine, the total consumer spending in the U.S. is double the total of consumer spending in China and India combined. It is fairly certain that this is going to change, and as a result the world economy will be material short for the foreseeable future.
FREE-MARKET ECONOMIES
There is a lot of truth to the economic saying, "There is no cure for high prices like high prices." This is the best way to allocate scarce resources. Another common sentiment is that in a free market there is no such thing as shortages, there are only high prices. With high prices, there will be more production, and with high prices, there will be attempts to use less product and to use what is being consumed in a more efficient manner.
As the need for scrap steel has increased during the past few years, the free market price being offered increased dramatically. Prices for a metric ton of shredded steel scrap delivered to a typical steel mill went from the mid-$150s to more than $600. The point here is that the free market is a very good way to allocate scarce materials. It is always going up and down to adjust the supply and demand.
Some say steel scrap will come down from these record high prices, but that prices will remain high enough to ensure that all of the economically recoverable scrap in the world will be recycled. As long as there is any semblance of a free market in the world, there will be enough of a margin between buying and selling prices to reward those who are the most efficient in the processing and recycling of scrap materials.
If the available scrap can be shredded, is it better to do the shredding in a big shredder or a smaller one?
WHICH SIZE?
Because the price of fuel is going up, transportation costs dictate that shredding the material close to the source is clearly the right thing to do. In my neighborhood, if I try to process only 3,000 to 5,000 tons per month by shredding, it will be possible to maintain a much larger margin, which should produce a better rate of return. Large shredding plants require so much investment that they become riskier than their smaller counterparts.
It is the experience of some entrepreneurs who are new to the business that they simply do not have enough investment capital for a very large plant, which can cost $10 million to $20 million when all of the land, buildings, cranes, loaders, rail, electrical and mechanical installation costs are considered. However, it is possible to install a smaller shredder for about $4 million to $5 million, and sometimes capital outlay is a strong factor in the decision-making process.
Larger shredders operate at a lower cost per ton, some say, so that it clearly is better to process material using a larger shredder. In response, often some variation of the following story is told: Two men are walking through the jungle when, all of a sudden, a tiger jumps out and starts to chase them. One man starts kicking off his big boots. The other man says, "Why are you doing that? You can’t outrun him anyway?" The first man says, "I don’t have to outrun him, I only have to outrun you!"
We know that in a stable market, the margin available to process scrap metal via shredding gradually shrinks to the break-even point for the least efficient producer. The trick is to be the most efficient producer, or at least not to be the least efficient producer.
Like so many other discussions in the scrap processing business, the truth is that there is no exact answer in determining shredder size. There are, however, a series of factors that when examined will give a better indication as to whether bigger is better or not.
The following is an attempt to identify some of the relevant factors that scrap processors should consider when deciding which size shredder to install at a particular yard.
THINK SMALL
There has been a movement to consolidate the scrap processing industry, with several worldwide firms buying other worldwide firms for many billions of dollars. We have also seen some steel makers acquire several billion dollars worth of scrap processing assets.
This consolidation in the scrap processing industry will have some unintended consequences. It is my opinion that there will not be enough efficiency gained by the consolidation in the scrap processing industry to pay for the high earnings multiples demanded by the stock markets.
Because efficiency gains might not pay for these investments or meet the price to earnings ratios demanded by the equity markets, the consolidated companies will attempt to increase their margins. This desire for larger margins will encourage new investments in smaller shredding plants. This trend is already at work. In several areas where major competitors have consolidated, the margin to process scrap has increased. This has resulted in a number of processors taking a "neighborhood" approach to their scrap gathering efforts. While the very large shredder investments need 30,000 tons, 50,000 tons or even more per month to process economically, a "neighborhood" shredding plant, which represents a much lower investment, with better margins, can make money processing 2,000 to 5,000 tons per month.
The fee to enter the scrap processing business is not as high when investing in a smaller auto shredding plant as the fee to enter the business with a large shredding plant. Therefore, when good processing margins appear to be available, I think that new smaller plants will be established.
The smallest shredder that we supplied this year is our 60 SXS shredder, with 1,500 horsepower, for a total investment of about $4 million. It is producing about 2,000 to 3,000 tons per month of shredded steel scrap. This plant is located about 60 miles from one of the largest shredder operations in the United States.
Under our free-market system, consolidations tend to create wider margins because of lower levels of competition, and wider margins tend to encourage new companies to enter into the economic competition. There is always pressure to find balance.
THINK BIG
Sponsored Content
Labor that Works
With 25 years of experience, Leadpoint delivers cost-effective workforce solutions tailored to your needs. We handle the recruiting, hiring, training, and onboarding to deliver stable, productive, and safety-focused teams. Our commitment to safety and quality ensures peace of mind with a reliable workforce that helps you achieve your goals.
Large shredding plants operate at a lower cost per ton. Companies invest less per ton of annual capacity. For example, assume that a $5 million investment will purchase and install a shredding plant that will process 50,000 tons per year. This means that the investment for 1 ton of capacity annually is $100. Assume that for a $10 million investment, the plant will process 500,000 tons. This means that the investment for 1 ton of capacity annually is $20. This is a significant factor in amortizing the investment. This indicates that the amortization costs for the smaller machine will be as much as five times higher per ton.
Other operating cost efficiencies can be found in the reduction of power costs per ton of finished material. For example, a smaller shredder will consume about 20 kilowatt hours per ton at the shredder alone and another 20 to 30 kilowatt hours per ton for the downstream and associated equipment. A large shredder will consume about 12 kilowatt hours at the shredder and perhaps another 18 kilowatt hours for the downstream and associated equipment. If the cost of one kilowatt hour is 10 cents, then there will be several dollars per ton difference in power costs.
Labor costs also are considerably lower per ton for the larger shredders because the size of the team operating the shredder is perhaps the difference between eight to 10 men for the smaller shredder compared to 12 to 20 men for the larger shredder. Assume that the number of man hours is double, but the production of shredded scrap is a factor of 10, and it is easy to see that the cost per ton for labor will be about five-times higher for the small shredder compared to the large shredder.
Interestingly, the amount of wear parts consumed is comparable between the shredders. Assuming that the same density of scrap is being prepared, the cost for replacement parts will be about $3 to $4 per ton for either size machine. There will be some further labor savings, as the larger machine with larger castings has significantly higher tons produced before wear parts need to be replaced. This reduces the man hours required for maintenance on a per-ton basis for the larger shredder.
Direct expenses, such as the cost for the landfilling of raw material, the amount of nonferrous metal value recovered, etc., are comparable between the small and large shredder.
If sufficient quantities of shreddable scrap are available and if sufficient capital is available, the most efficient shredder operation can be accomplished with the larger shredder.
If smaller amounts of scrap are available with larger margins, then it may be wise to invest in one or more smaller shredders.
If freight costs to market are being considered, the freight savings need to outweigh the operational savings to be the determining factor.
Scott Newell is the chairman of The Shredder Co. LLC and Newell Recycling Co. of El Paso, Texas. He can be contacted at scotnewell@aol.com.
Get curated news on YOUR industry.
Enter your email to receive our newsletters.
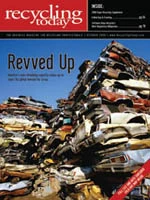
Explore the October 2008 Issue
Check out more from this issue and find your next story to read.
Latest from Recycling Today
- CP Group announces new senior vice president
- APR publishes Design Guide in French
- AmSty recorded first sales of PolyRenew Styrene in 2024
- PRE says EU’s plastic recycling industry at a breaking point
- Call2Recycle Canada, Staples Professional expand partnership
- Circular Services breaks ground on north Texas MRF
- Tariff uncertainty results in choppy nonferrous scrap flows
- CATL, Ellen MacArthur Foundation establish battery partnership