
Electronics recycler and asset management company Sunnking, headquartered in Brockport, New York, has an ambitious tagline: “We rule electronics recycling.” To ensure the company delivers on this promise, it recently has taken steps to expand its processing capabilities.
From resale to recycling
Duane Beckett founded Sunnking in 2000 as an electronic equipment reseller, but the company quickly began accumulating devices that had no resale value. “We began as an asset management company always looking to find value in material,” he says. “Over time, we have expanded our focus to recycling material.”
Beckett called upon his 10-year history in the scrap metal industry, having worked as a plant manager for Integrated Recycling Services, Lancaster, New York, and began recycling the devices Sunnking had accumulated.
While Sunnking resells whole units primarily, Vice President Adam Shine says the company recently began component recovery initiatives. For instance, Sunnking employees harvest parts from LCD displays and from laptops to create kits to service these devices.
“As a processor, everything that enters the facility is processed or refurbished,” Beckett says of the company’s Brockport plant. The 204,000-square-foot facility houses Sunnking’s resale and recycling operations, which include a semiautomated dismantling line and sorting capabilities. In 2016, nearly 25 million pounds of electronics passed through the facility, he says.
In addition to its Brockport location, the company operates transfer facilities in the New York cities of Buffalo and Syracuse where employees perform initial sorting and consolidation of incoming electronics.
“We receive material from throughout the northeast United States through three channels,” Shine says. These channels include business-to-business clients seeking asset disposition and recycling services; sites run by municipalities throughout New York state to collect devices from residents; and large recycling collection events that Sunnking hosts to collect residential material.
Shine says initially Sunnking’s business focused solely on corporate and institutional accounts; but, when New York state enacted its electronics recycling law in 2011, Sunnking began targeting residential electronics collected throughout the state. Today, Shine says 40 percent of Sunnking’s business is from the business-to-business sector, while residential devices collected under New York law or at the company’s own collection events comprise 60 percent of its business.
In addition to handling these traditional devices, Sunnking manages industrial, medical and commercial equipment, Shine says. “Our motto is that we specialize in anything with a cord or a circuit board.”
The company sells its refurbished devices internationally via online channels, including its eBay store, http://stores.ebay.com/sunnking, and locally at its retail store in Brockport.
“We began as a reseller of electronics and still heavily focus on the reuse side of recycling,” Beckett says.
However, Shine says recycling has grown to account for a significant portion of the company’s business. “Currently, our business is 10 to 12 percent reuse and 88 to 90 percent recycling,” he says.
That’s not to say that resale is no longer a priority because, as Shine says, it offers more value for the company than recycling does. However, technology is progressing at such a rate that 3-year-old products essentially are obsolete, he says. “They no longer have reuse or resale value, and you have to recycle them.”
Sunnking’s combination of resale and recycling helped to minimize the effect of the downturn in the commodities market that began in 2015. Having withstood the trials of the last two years, Sunnking is focusing much of its energy on producing cleaner streams of recyclables.
Expanding its processing capabilities
Earlier this year, Sunnking added equipment at its Brockport location to shred and separate electronic devices to maximize material recovery and to produce cleaner streams of recyclables. Sunnking refers to this process as “semiautomated dismantling and sortation.”
Prior to the company’s move to its new Brockport facility and the installation of this semiautomated processing line, Shine says Sunnking sent some material out to be shredded by another area processor.
“We wanted to control our own destiny and better market the end material,” he says of the company’s expansion of its processing capabilities. “We got the added benefit of speed.”
Sunnking uses this equipment to process low-value devices, which are manually presorted to remove hazardous items that should not be shredded.
The new machinery includes a shredder from Shred-Tech, Cambridge, Ontario; a
_fmt.png)
Shine says the company is considering various options for automatically separating this shredded material further. In addition to manual sorting, he says Sunnking has sent material for toll processing to a company with optical sorting capabilities to increase material recovery and purity.
“We would like to add that technology if there is an economic payback,” Shine says.However, he says, Sunnking presently is focused on adjusting its recently installed equipment as it learns the intricacies of the different materials it is processing.
As part of this learning process, Shine says Sunnking is batching like devices together for processing. “We are cleaning the machines out thoroughly between each run,” he says. “That may not be the way we run in the future, but we are trying to get a sense of end markets and values.”
Sponsored Content
Labor that Works
With 25 years of experience, Leadpoint delivers cost-effective workforce solutions tailored to your needs. We handle the recruiting, hiring, training, and onboarding to deliver stable, productive, and safety-focused teams. Our commitment to safety and quality ensures peace of mind with a reliable workforce that helps you achieve your goals.
Shine continues, “We need to walk before we run. When we are comfortable and have markets, we will add processing capabilities.”
The installation of its semiautomated processing line has reduced the time needed to disassemble material, resulted in higher processing volumes and increased profits, the company says.
Sunnking uses a manual dismantling process for higher-value devices so as not to degrade the value of the components.
Looking toward the future
Shine says Sunnking’s management strategy is focused on continual improvement. “We are constantly looking for new innovations, processing methodologies, markets and sales channels to stay ahead of the curve,” he says.
Sunnking plans to maximize its Brockport processing plant, Shine says. “In the future, we will continue to add automation to our process as new technology emerges.”
Shine and Beckett also say they will be on the lookout for merger and acquisition and organic growth opportunities that are aligned with the business.
“One of the things I feel strongly about is that if you are not changing, you’re dying,” Shine says. “We are looking for growth opportunities—either further processing or geographic expansion.”
Get curated news on YOUR industry.
Enter your email to receive our newsletters.
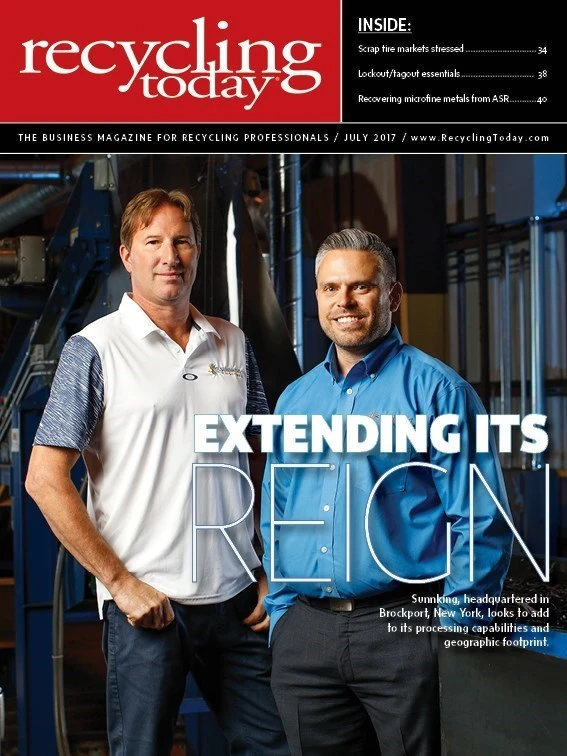
Explore the July 2017 Issue
Check out more from this issue and find your next story to read.
Latest from Recycling Today
- CP Group announces new senior vice president
- APR publishes Design Guide in French
- AmSty recorded first sales of PolyRenew Styrene in 2024
- PRE says EU’s plastic recycling industry at a breaking point
- Call2Recycle Canada, Staples Professional expand partnership
- Circular Services breaks ground on north Texas MRF
- Tariff uncertainty results in choppy nonferrous scrap flows
- CATL, Ellen MacArthur Foundation establish battery partnership