Selecting racking systems for a record storage business is not as easy as one, two, three. It’s a complicated process that must take a number of variables into consideration, including cost, product flexibility, facility parameters and fire codes, to name a few. But, with some advice from racking system suppliers and a records storage professional, the task may seem more manageable.
QUALITY AND COST
According to John McManaway of Archives Security Inc. (ASI), Birmingham, Ala., the company starts shopping for racking by identifying the quality products and suppliers, after which, cost is the main factor. "When you’re buying several hundred thousand box locations worth of rack, cost must be a driving factor after you weed out any inferior products, suppliers, etc.," McManaway says.
Lori Palmer, senior vice president of REB Storage Systems International, Chicago, advises record storage managers to "hunt out a reputable and knowledgeable company that can do everything for them. Racking people should automatically do a CADD drawing with layouts and box capacity." She also suggests that reputable suppliers encourage their customers to look into their local fire codes and regulations to be certain their facilities are in compliance. "We work with sprinkler and lighting contractors that are familiar with the records storage business, not just storage facilities," Palmer says.
Mark Mitchell of SpaceRak, Hendersonville, Tenn., also suggests taking advantage of a suppliers’ design skills. "Look for a rack system supplier that offers in-house design and engineering of the whole system," he says.
In addition to these considerations, when shopping for racking, Mitchell says record center managers should also consider the savings they could see from buying rack systems directly from the manufacturer. He says this could free up capital that can be used on other system components, such as lighting and fire suppression.
"After quality and cost, the flexibility of the product is important," McManaway continues. "We need to be able to configure the systems within the parameters of our facility as well as be able to reuse them if we relocate."
ASI also finds looks important, he says. "While we don’t expect our storage rack to be aesthetically perfect, we also don’t want it to look like a demolition derby is being held in our record center on a regular basis," McManaway says. "We are very concerned about the clean, orderly appearance of our record center when clients or prospective clients visit."
When it comes to aesthetics, used racking shouldn’t be immediately dismissed, but Palmer also stresses that it is not necessarily less expensive. She suggests asking about the previous application it was used in and whether it has been refurbished. "Always get a price on new and used," she says, "you might be surprised. Sometimes it makes more sense to buy new frames and utilize used beams or decking."
Once the racking supplier has been determined, facility layout is another important consideration.
THE DESIGN FACTOR
"Facility layout has a huge impact on storage system design," McManaway says. "Overall square footage is important, but the most important determining factor is ceiling height. The number of levels you can add to your system will of course be dictated by how high you can go." He adds, "How high you can go then dictates what strength of product you need as well as what type of installation will be required."
REB Steel’s Palmer says, "Clear, open buildings with few obstructions, such as heating/cooling units, plumbing and other utility lines and fewer building columns are an easier type of facility to design a system for and will usually help in getting increased storage capacity within the facility." She adds, "An open type warehouse usually works best when you have a clear height storage of 18 feet or more. Obviously, the higher you go, the more value for your real estate and the higher your profitability."
However, Palmer says that shorter buildings are not without their advantages, offering better operator efficiency without using catwalks.
Taller racking systems require stronger concrete slabs, as well. "When considering height, you must also consider the strength of the floor that the system will rest upon," McManaway says. "Thorough testing of the floor must be conducted by experienced engineering/geotechnical specialists, especially when buying a used facility."
Structural issues related to the building and the racking system also influence the placement of fire suppression equipment. "Local fire codes combined with the special NFPA (National Fire Protection Association) codes that our industry falls under completely dictate where fire protection devices must be installed," McManaway says. Generally, as height increases, so does the need for fire suppression equipment.
SpaceRak’s Mitchell says operators should also consider the placement of the system’s main aisle, or the record center’s "Main Street." He says, "Main Street should connect all major components of the facility with as little interference as possible. This aisle is typically used to carry the fire suppression trunk line with all service aisle branches feeding off of it. The cleaner the rack design, the least costly the fire suppression system should be."
Racking system height is not the only factor that affects record storage capacity; aisle width is also a factor.
While the main area of Archives Security Inc. (ASI), Birmingham, Ala., stores hard copy records with retention schedules attached to them, ASI’s John McManaway says the area is not truly climate controlled. For more sensitive information, the company employs a climate-controlled vault. "We have a state-of-the art climate controlled vault that is monitored 24 hours a day for strict t
Behind Closed Doors
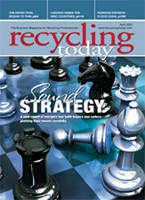
Explore the April 2007 Issue
Check out more from this issue and find your next story to read.
Latest from Recycling Today
- Nucor receives West Virginia funding assist
- Ferrous market ends 2024 in familiar rut
- Aqua Metals secures $1.5M loan, reports operational strides
- AF&PA urges veto of NY bill
- Aluminum Association includes recycling among 2025 policy priorities
- AISI applauds waterways spending bill
- Lux Research questions hydrogen’s transportation role
- Sonoco selling thermoformed, flexible packaging business to Toppan for $1.8B