Purchasing a shredding plant has been a major move for the Bianculli brothers and Ocala Recycling of Ocala, Fla.
But the additional investment of downstream sorting equipment manufactured by Steinert is helping the company receive a return on its investment in the form of clean, upgraded streams of both ferrous and nonferrous shredded scrap.
Ocala installed a Harris Shredder in the fall of 2007 and invested in a full complement of Steinert downstream equipment with three important components:
• An MTE Q 150 Electromagnetic Drum Magnet;
• Two NES 200 5009 Eddy Current Separators; and
• An ISS 200 All Metal Separator.
According to Rich Bianculli of Ocala Recycling, "The separation system was designed to yield high-quality metal products while losing a minimal amount of metal units in the waste stream."
Bianculli says Ocala Recycling chose equipment made by Steinert for several reasons, including its heavy-duty design. "Steinert equipment is designed to be more durable, reliable and survivable," says Bianculli.
The installation process also helped Bianculli confirm that he had made the right decision going with Steinert. "Steinert US provides good support for their equipment," he remarks.
Aside from safety, the maximum recovery of clean shredded metal products is Ocala Recycling’s number one goal. "High quality ferrous and nonferrous metal streams are being made," says Bianculli. "And the All Metal Separator recovers any stubborn nonferrous plus the stainless steel."
In the Ocala setup, "Shredded materials are first introduced to the main electromagnetic drum, where ferrous metal is removed," says Bianculli. "Nonferrous metals that don’t react to the magnet are conveyed to the sizing screens, which present the large and small nonferrous to two different Eddy Current Separators set for that size material, thus maximizing metal recovery. The waste from the ECS units then gets a final separation to remove any stainless and missed metals."
The end result: "The waste is ready for the landfill with less than 1 percent metal by weight," he declares.
Bianculli’s satisfaction with the Steinert equipment is certainly related to bottom-line results. "It’s a little early to determine the precise recoveries we are achieving, but, suffice it to say, they are at the high end of what we thought we might achieve. We are very happy with the return-on-assets we are presently enjoying with the Steinert equipment."
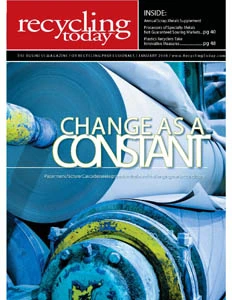
Explore the January 2008 Issue
Check out more from this issue and find your next story to read.
Latest from Recycling Today
- Nucor receives West Virginia funding assist
- Ferrous market ends 2024 in familiar rut
- Aqua Metals secures $1.5M loan, reports operational strides
- AF&PA urges veto of NY bill
- Aluminum Association includes recycling among 2025 policy priorities
- AISI applauds waterways spending bill
- Lux Research questions hydrogen’s transportation role
- Sonoco selling thermoformed, flexible packaging business to Toppan for $1.8B