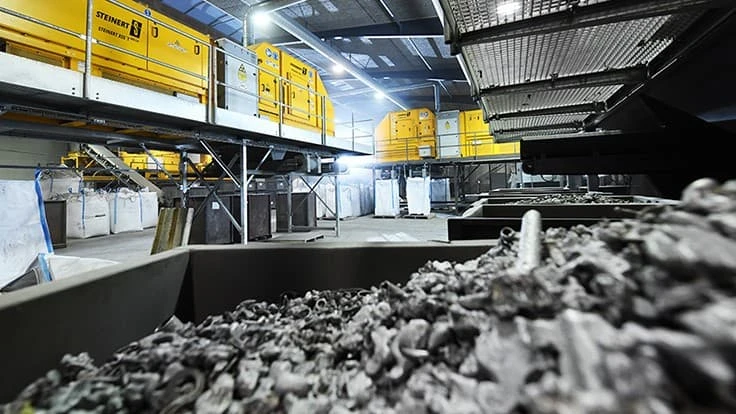
Photo provided by Steinert GmbH.
Global magnetics equipment provider Steinert GmbH, based in Cologne, Germany, has conducted an interview with Karl Hoffmann, the global sales director of its Metal Recycling Division.
In the interview, Hoffmann gives his thoughts on aluminum recycling, technological breakthroughs. the distinctive features of the aluminum market and his expectations for the future.
Steinert GmbH (SG): Mr. Hoffmann, how can so much energy be saved by recycling aluminum?
Karl Hoffmann (KH): Basically, you have to compare primary and secondary aluminum. In the case of primary aluminum, firstly bauxite has to be mined and then a complex process is undertaken to produce aluminum oxide from this. This is a very energy-intensive process, which causes a lot of environmental pollution.
By using scrap aluminum in smelting works, much less energy is used. What’s more, the aluminum can be used again and again – in theory, it can be recycled infinitely. And the figures involved are significant: around 75 percent of the aluminum ever produced is still in circulation. This is, firstly, because products made from aluminum have a long life and secondly because metal can be recycled with great ease.
SG: So how much less energy is needed to recycle aluminum compared with producing it from scratch?
KH: You can assume a saving of up to 95 percent. Of course, this is great news for climate protection. Recycling aluminum has the potential to produce 92 percent fewer CO2 emissions than new aluminum. In 2019, 20 million metric tons of aluminum was recycled globally, which is an equivalent saving of 300 million metric tons of greenhouse gases.
Processing 1 metric ton of aluminum scrap also saves 8 metric tons of bauxite from having to be mined. All things considered, it’s a saving of 14,000 kilowatt hours (kWh).
These days to be able to produce certain quality alloys, we still need primary aluminum, the manufacturing process for which is highly energy-intensive. Maintaining high quality levels for recycled aluminum requires intelligent cycles using highly efficient recycling technologies, such as sensor-based sorting technology. This can then compensate for the downgrading of material qualities experienced in the recycling cycle, which also enables secondary aluminum to be efficiently used in the production of what are known as aluminum wrought alloys.
SG: What is the importance of aluminum alloys?
KH: There are hundreds of different alloys and, depending on the requirements of the application in question, they provide various mechanical properties, such as strength or hardness. Developments in this field are highly dynamic. In the automotive sector, for example, it has long been standard to produce body parts from aluminum. And now, supporting parts, like suspensions are being manufactured out of recently developed aluminum alloys or even aluminum compounds. Of course, the engine itself is already mainly made from cast aluminum. Several automotive manufacturers have already honed in on aluminum as a material. Aluminum’s lower weight helps them comply with ever tighter CO2 emission requirements; the density of aluminum is 2.7 times less that of steel.
Aluminum will also be a key material for electric vehicles (EVs). The more steel is replaced with aluminum, the greater the range of an EV. Its potential for the future is huge too.
Alongside these large potential savings in CO2 emissions driven by lightweight design in the automotive sector, this potential will also be boosted by the efficient and specific use of recycled aluminum to reduce greenhouse gases.
Using recycled aluminum consumes around 95 percent less energy than primary aluminum. But precise sorting technology is essential for ensuring high-quality recycled goods.
SG: How do you ensure as high a grade of aluminum as possible from recycling?
KH: It goes without saying that this depends a great deal on the input material. The quality needed of course also depends on its intended use. Course impurities, like plastics or wood, can be removed with relatively simple technology, involving eddy current separators.
Sensors can sort to a much finer degree. X-ray transmission technology is basically the same as that used in the medical profession where the absorption of X-ray radiation makes different material densities visible. When sorting metal, this means that pieces of metal on a conveyor belt can be radiated and classified into materials and purity levels to a high degree of accuracy.
The huge advances made in detection, software and the processing of signals deliver a combination of very accurate sorting and high speed. Compressed air is then used to separate good parts out from not-so-good ones.
SG: What happens then with the sorted material?
KH: Smelting plants buy the metal to process it further. But there is also an option of further sorting the aluminum into alloys. The more precisely this is done, the more specifically the material can be used. We then inch ever closer to the goal of a closed cycle, in other words, a circular economy.
SG: What technological advances have been made recently at Steinert?
KH: Not long ago, we updated our system with X-ray transmission technology. We call the system XSS, which stands for X-ray and sensor sorting, the latest innovation bears the add-on EVO. This embodies developments made over the last five years. For example, we are now able to detect various material characteristics much more precisely than was previously the case. This is mainly thanks to enhanced signal processing. Nowadays, the systems are able to better separate out certain alloys. What’s more, we are also now able to separate free magnesium, a metal that is frequently found in aluminum scrap and if not detected causes considerable extra work in aluminum smelting works. This is challenging because, like aluminum, magnesium is a light metal and its absorption coefficients for X-ray radiation are therefore very similar.
SG: Have you made any other breakthroughs?
KH: Yes, we have made the components in our systems even more resistant. The X-ray source, a key and costly component, for example, now comes with a four-year warranty, which is unique in the sector.
SG: What is happening in the markets right now?
KH: Light metals allow weight and therefore CO2 to be saved in the mobility sector. The statutory requirements in this area are getting more and more stringent all the time so there is growing pressure on OEMs to implement lightweight solutions. At the same time, there is more and more interest from society in sustainable economies. Aluminum recyclers are therefore increasingly stating the share of recycled aluminum used. It can be assumed that demand for aluminum over the next few decades will increase by another 50 percent. An above-average amount of this will have to come from recycled material. Around 5 million tons of aluminum scrap is currently recycled a year in Europe. The figure globally is 20 million tons. Experts estimate that this figure will double over the next 10 years.
SG: What trends do you see emerging for aluminum recycling?
KH: Most of the material we sort today comes from vehicles or other products that were manufactured 10 or more years ago. The number of alloys used has increased since then. So, in the future, it will be important to be able to distinguish between alloys more accurately than we can today.
SG: Are there also any technological solutions that would simplify the recycling of all these alloys?
KH: Yes, and we have already developed them: laser-induced breakdown spectroscopy, or LIBS for short. This involves firing at aluminum with a high-energy laser. When the laser hits the metal, it turns into a metal vapor known as plasma. As it cools, it implodes and emits a measurable energy radiation, which is specific to that atom structure. This allows the various aluminum alloys to be determined with great accuracy.
If this technology is introduced across the board, we will be able to separate the alloys from one another so precisely that a circular economy is possible. The smelter facilities know what they need for their alloys. If a company can determine exactly what kind of material they have, then they can also establish what needs to be added to achieve the specified material properties.
SG: Steinert uses the term “greener aluminum,” what does this mean?
KH: Greener Aluminum highlights the opportunities that this metal and its unique possibilities offer us in recycling. This does require intelligent recycling cycles and sorting technology, but it is already allowing us to produce closed material cycles for this important material.
Here at Steinert we are delighted that we are able to play a key role here through the work of our development teams and our specialist advisers in the field. The future that intelligently reusing this metal offers us is driving us to achieve even more and develop even smarter solutions.
Latest from Recycling Today
- Aqua Metals secures $1.5M loan, reports operational strides
- AF&PA urges veto of NY bill
- Aluminum Association includes recycling among 2025 policy priorities
- AISI applauds waterways spending bill
- Lux Research questions hydrogen’s transportation role
- Sonoco selling thermoformed, flexible packaging business to Toppan for $1.8B
- ReMA offers Superfund informational reports
- Hyster-Yale commits to US production