
Steel is the most widely traded metal in the world and, unfortunately, also a large contributor of greenhouse gas (GHG) emissions, accounting for 7 percent to 9 percent of global emissions annually.
Commitments to reduce GHG emissions are being woven into environmental, social and governance (ESG) statutes at companies around the world, and conversations about lower emissions, fair labor practices, water conservation, pollution reduction and diversity are occurring throughout the supply chain and are no longer in the shadows.
Steel consumption plays an important role in the transition to a net-zero economy. The material is an integral part of energy solutions, transportation systems and new buildings, and as developing countries expand their water treatment plants, public infrastructure, bridges and railways, all those projects will need steel.
The case for responsible sourcing
Steelmaking needs to achieve low emissions with responsibly sourced raw materials while balancing social interests. But how do we achieve this mammoth task? What road map and metrics across companies and technologies should we use globally?
In the Winter 2023 issue of Scrap Recycling, we dissected some of the elements of ResponsibleSteel from the context of U.S. green steel production, more than 70 percent of which is made via electric arc furnace (EAF) technology using ferrous scrap. EAFs can produce 78 percent to 85 percent less carbon dioxide than blast furnaces, but the world produces more than 70 percent of its steel via blast furnaces and has much progress to make. U.S. firms, however, have invested and continue to invest in reducing Scopes 1, 2 and 3 emissions.
The wrong certification could erroneously categorize all steel as equally green, and Phillip Bell, president of the Washington-based Steel Manufacturers Association, warns against allowing some steel producers to classify their products as green when they have significantly more carbon emissions.

Why certification makes sense
ResponsibleSteel CEO Annie Heaton expands the conversation and gives insight into why her organization views the new Standard 2.0, released late last year, as the global solution to move steel toward decarbonization. The nonprofit has diverse leadership, including two steelmakers, a nongovernmental organization, a biodiversity advocacy group, an international trade union and three independents, and has members with blast furnace and EAF assets.
“Green is about progress as well as absolute embodied emissions,” Heaton says. “The transition will take 30 years. ResponsibleSteel is a solution to the common objective. Green is not simple, and it is too complex a topic to boil down to one word.”
ResponsibleSteel has 13 principles, not only covering the environmental aspect of sustainability but also the human one. “The ResponsibleSteel certification is a standard and assurance program with an external, independent evaluation,” Heaton says. “The sliding scale allows any steelmaker worldwide to show progress toward decarbonization. All who produce steel need to be incentivized and rewarded for progress.”
The ResponsibleSteel certification reassures stakeholders a site has a decarbonization plan, as well as an environmental improvement plan and safety management systems in place, each of which are checked independently.
Heaton acknowledges ferrous scrap use is the leading solution to lower GHG emissions to date. The sliding scale, which has four levels, differentiates emissions by accounting for scrap use alongside the reality of limited material.
Scrap feedstocks are confined to the amount of scrap made from steel produced before. Scrap production is estimated at 900 million metric tons annually by 2050 against 2 billion to 2.5 billion metric tons of steel demand. Therefore, iron ore-based steel production will continue playing a large role and is the source of the lion’s share of emissions, Heaton says.
She notes the U.S. is in a fortunate position of being one of the more mature global economies and a net exporter of ferrous scrap. Still, decarbonization will require global advances and collaboration, and many companies and countries are at different stages. Heaton adds that all steelmakers can incorporate more downstream and upstream emissions savings through carbon capture utilization and storage systems and preparation for hydrogen, for example.
“We have an enormous challenge at hand to decarbonize an industry largely made of primary iron-based steel, which makes up about 70 percent of global production,” Heaton says. “ResponsibleSteel is a tool to accelerate and drive progress toward a net-zero steel industry.”
Steelmakers are heterogeneous regarding technology, resources, methods, economic context, policies and the technology road map while facing different environmental and social impacts, hence, Heaton was informed by the organization’s agnostic principle toward decarbonization. The broad standards will give the guiding principles over the next 30 to 40 years.
The ResponsibleSteel standard does not say any one steel plant design is the right one, she says, and also can accommodate new technologies, such as direct electrolysis, as they evolve. Companies also are adopting different permutations with metallics beyond the blast furnace by using direct-reduced iron, hot-briquetted iron and pig iron made with charcoal. Along with ferrous scrap, EAFs also use these improved forms of iron.
Scrap is an important component in the sliding scale. Some blast furnaces today include 15 percent ferrous scrap, but some are pushing boundaries at 20 percent to 25 percent, which could increase over time. Scrap to iron ratios at EAFs can be 70/30, 80/20 or 90/10. The various proportions are represented on the scale and provide a view of how a plant performs in relation to its competitors, Heaton says.
The sliding scale graph (Page 37) represents the distribution of steel plants worldwide depending on the level of scrap available. The four levels are assessments of the transition they likely will undergo. By 2050, all plants must be at the lower level to reflect progress.
Heaton says scrap traceability, as with iron ore and semifinished feedstock, also will be important. This element only will be possible with the knowledge of the recycling industry.
The 2.0 version introduces additional requirements for a site to be evaluated, including input materials sourcing. At increasing levels, raw materials are being certified against an ESG scheme and will become part of producers’ overall ESG guidance. By Level 4, the new standard includes 80 percent coverage of certification of raw materials.
Heaton assures data will be publicly disclosed, including emissions of crude steel and where it sits in the sliding scale, which represents decarbonization progress and the assurance of the broader elements in ESG progress.

The big picture
Taking a step back from the positive contributions of ResponsibleSteel’s certification, the reality remains that a blanket certification can mislead a consumer, even without intent. Steel from a Level 4-certified plant will have eight times the emissions when produced by a blast furnace than steel from an EAF. Thus, the Global Steel Climate Council categorized the sliding scale as greenwashing.
ResponsibleSteel says it is committed to pushing back against greenwashing, and Heaton echoes that commitment while noting the reality of limited scrap sources, heterogeneous steelmaking starting points, iron-based production dependence and the immediate need to include all players in a well-designed, inclusive solution today.
She advocates that procurement should look at the progress toward goals, not only the absolutes in decision-making, adding that steel producers should be incentivized and rewarded for their progress and that we must think globally since the certification includes more than emissions metrics.
ResponsibleSteel looks like a strong road map toward each entity’s ESG goals, which include decarbonization. Every company should have a verifiable road map that mandates practices to improve auditing, planning and public disclosure in accordance with its stated values. The certification acknowledges benefits of scrap use but within the context of its limited supply.
Regarding carbon emissions, specifically, the blanket designation to the public as a ResponsibleSteel member, without an evident level (1-4) following the term along with the homogeneous Level 4 designation defined as “near zero,” despite varied emissions contributions, is of concern to some. Some steelmakers that primarily use scrap feedstock today have a different vantage point than those steelmakers producing using mixed or wholly blast furnace technologies. They prefer a more easily comparable and measurable emissions-focused standard, with several standards surfacing.
Steelmaking members of ResponsibleSteel must commit to starting their certification process within one year, Heaton says. She also highlights that claiming green only on emissions without regard to internationally agreed standards on labor, human rights and biodiversity can be a precarious position.
Fortunately, the search for progress has room for diverse methodologies in pursuit of an improved industry with players at different points. Collaboration and cooperation will be essential in seeking to achieve low GHG by 2050.
Get curated news on YOUR industry.
Enter your email to receive our newsletters.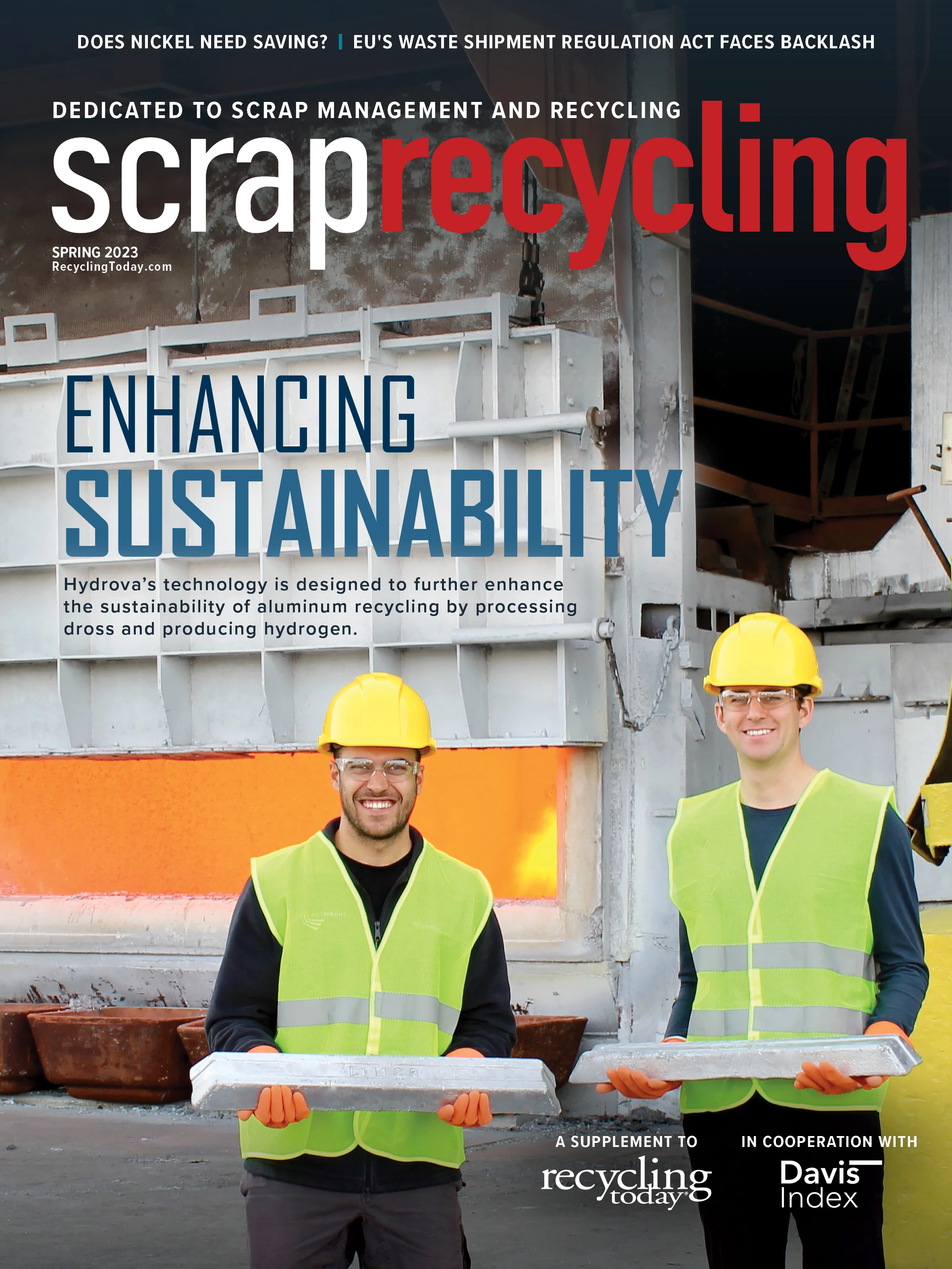
Explore the Spring 2023 Scrap Recycling Issue
Check out more from this issue and find your next story to read.
Latest from Recycling Today
- Athens Services terminates contract with San Marino, California
- Partners develop specialty response vehicles for LIB fires
- Sonoco cites OCC shortage for price hike in Europe
- British Steel mill’s future up in the air
- Tomra applies GAINnext AI technology to upgrade wrought aluminum scrap
- Redwood Materials partners with Isuzu Commercial Truck
- The push for more supply
- ReMA PSI Chapter adds 7 members