_fmt.png)
Like many recyclers at the beginning of the pandemic, SteelCoast, a recycler of military and civilian ships, was unsure how its operations and profitability would be affected. Despite the uncertainty last year, the company pressed on, making changes to its operations and staffing.
In 2020, SteelCoast processed about 44,000 tons of ferrous scrap and other metals, which it shipped to mills from its yard at the Port of Brownsville in Texas. This year, the company projects it will increase production to more than 70,000 tons and will triple its workforce from 77 employees in 2020 to 240.
“The SteelCoast team recognized that 2020 was going to provide challenges in every aspect of our industry,” says Mark Hodgson, president of the company. “We turned adversity into opportunity and focused on the details of the business and the employees that support it.”
In the last six months, SteelCoast has processed and shipped more than 25,000 tons of steel and other metals, Hodgson adds. The company also received the 2020 Excellence in Safety Award from American Equity Underwriters Inc. (AEU). AEU, Mobile, Alabama, provides workers’ compensation for waterfront employers, according to a news release issued by SteelCoast.
Now, with the wind in its sails, SteelCoast’s leadership says the company has set its sights on dismantling the U.S.S. Nassau, a former Tarawa-class amphibious assault ship that has the capacity to transport more than 3,000 United States Navy and Marine Corps personnel. The project is expected to take 12 months to complete, Hodgson says.
Setting sail
SteelCoast was founded in 2017 as a joint venture between Hilco Redevelopment Partners of Illinois and MCM Marine Services of Michigan, which was acquired by Callidus USA in 2020. The company operates a complex at the Port of Brownsville, which recently celebrated its 85th anniversary.
“We’re a fairly new company to an old industry in this port,” Hodgson says. “We operate on a vessel recycling facility that’s been here since the mid-’60s.”
SteelCoast purchased the assets from a previous ship recycling and scrapping operation, ESCO Marine, which were sold following a Chapter 11 bankruptcy proceeding that was filed in late 2015. Financial details and the purchase price were not disclosed.
The Brownsville facility already had undergone more than $1 million in renovations and improvements prior to SteelCoast’s purchase of the facility.
It recycles oceangoing vessels (military and nonmilitary) from around the world, in addition to dismantling decommissioned, idled or underutilized oil rigs, train locomotives, rail cars and other industrial and commercial sources of recyclable metals. Additionally, SteelCoast operates a 4,500-horsepower shredder.
The Port of Brownsville opened in 1936 and consists of a 17-mile-long ship channel. It is the only deepwater seaport located directly on the U.S.-Mexico border, according to port officials.
Today, the Port of Brownsville’s ship recycling operations capture more than 85 percent of the U.S. Navy and U.S. Maritime Administration (MARAD) ship recycling business.
The port is home to ship recycling companies like SteelCoast, All Star Metals and International Shipbreaking Ltd., which recently received the European Union Ship Recycling Accreditation, becoming the first company in the U.S. to receive that accreditation, according to the Port of Brownsville.
Activity at the port provides $3 billion in support to the Texas economy, creating about 51,500 jobs statewide, according to Eduardo A. Campirano, port director and chief executive officer.
Under the hull
SteelCoast operates an 80-acre complex with about 4,000 feet of water frontage on the main Brownsville channel. In addition, the company is expanding its operations with a new 13.5-acre facility nearby that will act as a feeder yard for the business’ main facility.
Today, SteelCoast employs 160 workers and serves as one of the primary contractors for the U.S. Navy and MARAD. While the company has only been around for four years, Hodgson says everyone on its management team has at least 20 years of industry experience.
The company specializes in ship abatement and remediation, including removing hazardous materials, such as mercury and asbestos, from ships and separating the scrap metal. Hodgson says SteelCoast processes about 6,000 tons of ferrous material and 300 tons of nonferrous material per month.
_fmt.png)
To do this, the company operates five large crawler cranes that feature 250- to 330-ton lifting capacities, large material handlers and heavy hauling trucks. The company breaks each ship down using two excavators equipped with shears, says Alberto Garcia, chief financial officer of SteelCoast.
“There are more than 50 pieces of moving equipment in the facility every day,” Hodgson adds.
Navigating uneasy waters
While the company has positioned itself to double its scrap output, SteelCoast’s executives were not always clear what the company’s future would be at the start of the pandemic. Hodgson says his management team needed to examine every aspect of SteelCoast’s operations to figure out how to maintain profitability.
“We got granular and looked at every aspect of our business, including our team and operations,” Hodgson says.
Ultimately, the company scaled back the size of its workforce and reinvested the money it saved into the remaining employees. Some investments include an increased focus on training and education, which helped to create a stronger team mentality to keep the business running efficiently, he says.
“Our business philosophy is ‘Team First,’” Hodgson says. “We’re a very labor-intensive business, and our focus is primarily on our time. Continuous education and communication of our teams at all levels is key to the productivity of our business.”
SteelCoast also spent time examining how it operated and developing best practices to keep its operations running smoothly. Paring down staffing helped save money, but Hodgson also says his team began working on a new staggered schedule that allowed the facility to run effectively with fewer employees.
“All of these things have allowed us to emerge in 2021 as a much stronger and formidable business,” he says. “Our team sets this company apart from the competitors. We’re always looking for innovations, and we listen to our team to find what will let us stay ahead of the game.”
As the company continued to grow, it eventually brought back workers it let go at the height of the pandemic, Hodgson says. Now, he says, the scrap metal market is the strongest he has seen in a long time. Surveyed pricing from Fastmarkets AMM shows No. 1 busheling sold for $564.07 per ton, No. 1 heavy-melting scrap sold for $402.50 per ton and shredded sold for $447.30 per ton in May. These prices compare with $310.01, $216.67 and $264.30, respectively, in May of last year.
Hodgson also says that the Biden administration has plans to move quickly over the next three years to improve recycling nationally, which he says could mean more job opportunities and strong commodity prices.
Sailing the horizon
With strong scrap markets and plenty of projects in place, Hodgson says getting enough workers to meet the growing demands will be one of the biggest obstacles the company faces moving forward.
In terms of what is next for the company’s operations, SteelCoast is currently awaiting the U.S. Navy’s award of two aircraft carriers, including the Kitty Hawk and the JFK.
The business also is planning to expand its capabilities to dismantle the Navy’s nuclear ships when they start getting decommissioned in the near future.
“We’re not just looking toward tomorrow, we’re looking two or three years down the line to make sure we’re prepared for the future,” Hodgson says.
However, Garcia says that whatever happens next, SteelCoast is prepared to collaborate internally to address both challenges and opportunities. “We realized that one person doesn’t have all of the answers,” Garcia says. “The only way to improve is to discuss every issue with our team. This includes when we’re looking to innovate and do things differently.”
“We’ve empowered everyone to have a voice,” Hodgson adds. “It’s through communication and understanding that sets us apart.”
Get curated news on YOUR industry.
Enter your email to receive our newsletters.
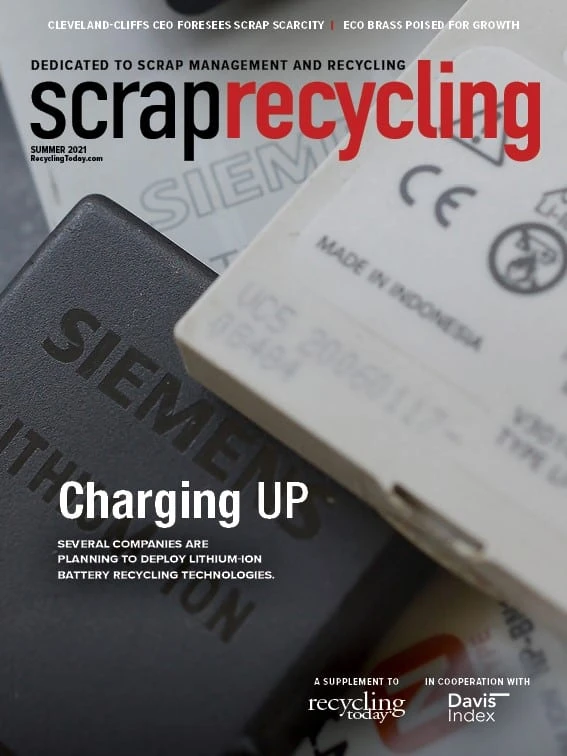
Explore the Summer 2021 Scrap Recycling Issue
Check out more from this issue and find your next story to read.
Latest from Recycling Today
- Athens Services terminates contract with San Marino, California
- Partners develop specialty response vehicles for LIB fires
- Sonoco cites OCC shortage for price hike in Europe
- British Steel mill’s future up in the air
- Tomra applies GAINnext AI technology to upgrade wrought aluminum scrap
- Redwood Materials partners with Isuzu Commercial Truck
- The push for more supply
- ReMA PSI Chapter adds 7 members