
Since it became known that littered plastic can find its way into the food chain in the form of microplastics, the general public has realized that improperly disposing of or recycling plastic packaging poses risks to the environment. For other materials, recycling mechanisms have long been established. Packaging steel has been at the forefront of recycling for years, even compared with glass, aluminum or cardboard.
Packaging steel reached new highs in recent years. In 2015, packaging steel achieved a recycling rate of 77.5 percent in Europe (EU plus Norway and Switzerland), an increase of 1.5 percent from the previous year. As a result, 2.7 million tons of steel were returned to the production process.
Beverage cans in particular are becoming increasingly popular because of their popularity among young adults and teenagers and the convenience they offer: Cans can be opened easily and ensure a long shelf life. They also are lightweight, practical in handling, easy to stack and, because of their stability, are resistant to damage.
Counting the benefits
According to research undertaken for Andernach, Rhineland-Palatinate, Germany-based Thyssenkrupp by Aachen, Germany-based Cyclos HTP, a 0.5-liter beverage can made from tinplate is 91 percent recyclable. Cyclos HTP is a company that specializes in the classification, assessment and certification of package and product recyclability as well as in research and development in this area.
A number of other features, developments and achievements ensure that packaging steel is at the forefront of sustainability. The packaging processes and the material itself provide optimum product protection and preservation, which means cans do not need to be cooled during production or transportation to end customers.
When it comes to recycling, packaging steel has been outperforming other materials for years. In North America, steel is cited as the No. 1 recycled material, and each year more steel is recycled in the U.S. than paper, plastic, aluminum and glass combined.

“Among other things, this has to do with its magnetic properties, which enable the material to be separated from other waste easily—whether in household waste or other waste cycles,” Christian Puerschel, head of communications and market development at Thyssenkrupp, says. “Steel is also a ‘permanent’ material that can be recycled almost indefinitely without any loss of quality.”
Each newly manufactured steel product thus contains an increasing percentage of recycled steel. Recycling tin products reduces emissions as it saves up to 76 percent of the energy that is used to make them. The objective is to establish a closed material loop worldwide, which has been achieved in many other countries to a large extent.
Of course, this only works if any gaps between the functional links within the value chain are closed to ensure that as little material as possible leaves the cycle.
“In Germany, for example, we have assumed responsibility in this area for many years and actively close and maintain the recycling loop with our subsidiary DWR and involvement in the nonprofit company KBS,” Puerschel says.
Deutsche Gesellschaft für Weißblechrecycling mbH (DWR, or German Society for Tinplate Recycling) is a wholly owned subsidiary of Thyssenkrupp and ensures collected steel packaging is gathered, sorted and returned to the market.

Kreislaufsystem Blechverpackungen Stahl GmbH (KBS, a metal packaging recycling system operator) is a nonprofit company that ensures that large quantities of packaging steel for commercial use (from cafeterias, hospitals, etc.) are returned to steel production correctly.
Another sustainability aspect is steel cans’ capacity to preserve food and beverages. Today, it is hard to imagine just how difficult it once was for humans to store perishable foods such as meat or fish for a prolonged time. Even though we may have lost sight of this achievement in light of the passage of time, one fact remains: A higher share of tinplate packaging in food consumption means less food is wasted as a result of spoilage, whether actual or supposed. Incidentally, this also applies to beverage cans, which can be stored for extended periods of time.
Getting better
As a leader in packaging steel technology, Thyssenkrupp continues to research new material properties and manufacturing processes.
For example, since 1985, the weight of the two-piece standard 0.33-liter beverage can has been reduced by more than one-third to 22 grams. The weight savings for three-piece food cans are even greater: Reducing the wall thickness to a fraction of a millimeter since the 1970s has reduced the weight of the cans by half, making them significantly more material-efficient.
With new additions to the Rasselstein packaging steel brand, such as Solidflex, High Formabilit, or Ultra-Low-Earing steel, Thyssenkrupp believes it is at the forefront of a development that enables packaging steel with very specific properties to be configured exactly to each customer’s requirements. Thyssenkrupp can provide its customers with more than 6,000 specifications. The company’s portfolio includes maximum-strength packaging steels with high ductility; innovative, highly malleable steels for demanding can geometries; and extremely homogeneous and isotropic tinplates for closures and multistage deep-drawn DRD (drawn and redrawn) cans, which are printed in distortion.
Ahead of its time
These efforts and innovations ensure the future viability of packaging steel across the globe while also securing a collective approach to tighter recycling regulations.
“As a pioneer in the closed-loop economy, we naturally support these regulations and consider ourselves well-positioned to address these upcoming challenges—and more—in terms of sustainability,” Puerschel adds.
Thyssenkrupp is developing packaging steels that feature improved material properties as well as steel types that reduce resource consumption to an even greater degree. These innovations will help packaging steel to continue to expand its role as an environmentally friendly and efficient product in the future—not just as a supplement but increasingly as an alternative to packaging materials with a higher environmental footprint.
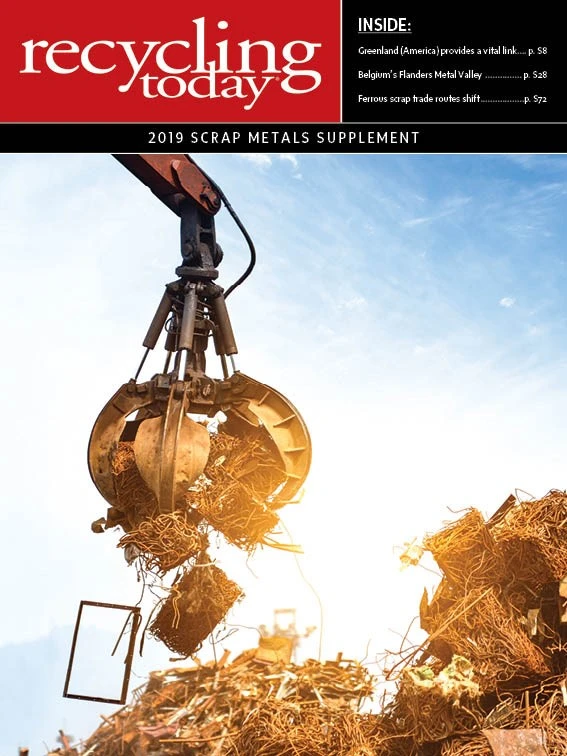
Explore the January 2019 Scrap Metals Supplement Issue
Check out more from this issue and find your next story to read.
Latest from Recycling Today
- Two factors raise ferrous export questions in April
- Analyst: Scrap imbalance lost amid copper’s critical status
- AF&PA report shows decrease in packaging paper shipments
- GreenMantra names new CEO
- Agilyx says Styrenyx technology reduces carbon footprint in styrene production
- SABIC’s Trucircle PE used for greenhouse roofing
- Hydro to add wire rod casthouse in Norway
- Hindalco to invest in copper, aluminum business in India