Those who feel iron and steel are invincible need only look at the fate of those who manufactured slide rules (remember those ruler-like tools that engineers and scientists carried around to make complex math computations?). They produced an excellent, quality product. However, their business was eclipsed by the invention of the pocket calculator. Could the same thing happen to ferrous?
For decades, steel has been the heavyweight champion of the industrial world. Aluminum and plastics have been dancing around the ring like featherweight contenders, jabbing at steel’s market share and falling back when the big palooka starts to throw its weight around.
But it’s way too early to write steel (and steel scrap) out of the picture. Just as a fighter can survive many bouts on experience alone, there are advantages to steel’s having been around for a long time. For one, notes Len Shaw, executive director of the Canadian Association of Recycling Industries (CARI), Ottawa, Canada, the steel industry has a well-established recycling infrastructure. That is something plastics can’t come close to matching today – or anytime soon.
In fact, if steel has a walloping, roundhouse punch to deliver to competitors in the market, it’s going to come from its recycling infrastructure. While certainly no industry segment is recycling all of the materials it possibly could, steel leads the industry with well defined industry-sponsored recycling programs. Gathering more scrap material will be a challenge in an industry that already recovers about 88% of its usable scrap. There is little question that there will be a continued, gradual increase in the amount of all materials recycled – whether ferrous or others.
Shaw confirms the importance of trends toward continued upward movement in all areas of recycling. “Scrap steel is still relatively high when compared to glass and plastics, which are young but coming of age,” Shaw says. He notes the influence of issues like greenhouse gasses across North America and Europe. “When you recycle metals, you are not creating as many of those gasses,” he says. Nor do producers have to exploit sources of new raw materials.
“Long term, any new steel production will have to derive its raw materials from scrap,” says William Heenan, president of the Steel Recycling Institute, Pittsburgh, Pa. He says the industry will not see any new coke or blast furnaces in the 21st century. Instead, the electric arc furnace – or some newer technology – will drive the industry.
“You will see demand for scrap increase over time, as well as demand for other materials like DRI (direct reduced iron),” he says. Noting how much steel is recycled today, Heenan admits, “There isn’t a lot of room to grow.” He says the answer to the riddle of increasing domestic iron scrap supplies will be the reduction of exports from the United States and more reliance on DRI or new processes.
“Nothing holds a candle to steel,” maintains Doug Brooks, chairman of the board of the Steel Shipping Container Institute, Washington, D.C.
Brooks, who is president of CP Louisiana, Inc., New Orleans, says the steel container industry produces 30-33 million new drums a year. However, it recycles about 40 million drums a year. “We recycle over 95% of our containers,” Brooks says. “This is an industry with a recycling base that is quite mature. It’s been in place for many years.” He says the quality of steel has improved vastly in the past five years, especially in areas like lightweighting of containers.
For the past 20 or even 40 years, steel materials have been made lighter and stronger. “We’ve seen substantial metallurgical changes,” Shaw notes. “Steel is not sitting by and letting other commodities take over its market.” However, there certainly is competition.
MEET THE COMPETITION
Remember the word that someone muttered in Dustin Hoffman’s ear in the movie The Graduate: “plastics.” Are the seers seeing the same thing some 30 years later?
Some firms are making major strides in their handling of plastics. Nortel, one of the largest telephone companies in the world, has designed what it calls an environmentally friendly phone. It is all plastic. It was designed without glue or inks on labels so the plastic parts are not contaminated with chemicals when they are recycled. Information is etched into the plastic. The phones snap together so there are no metal screws to contaminate the plastic waste stream.
Successful projects like that are required on a grand scale before plastic recycling becomes easier and is able to rival the iron and steel industry as a manufacturing threat. The simple fact is that the plastics recycling infrastructure is not as established as that for steel.
Brooks is not worried too much about plastics replacing steel containers. “Today steel commands 80% of the market,” he says. “It is the most recyclable material. It handles well.” By that he means that stacking plastic drums three or four high in a hot warehouse is inviting an avalanche of drums after a few weeks time.
Brooks says plastic has major recyclability problems that steel does not have to deal with. “Don’t confuse the steel drum with what was in it,” he says, referring to the common skull-and-bones logo on steel cans. “Steel is just iron. Even if left to decompose, it does not pollute. It deteriorates to nothing more than a natural product.”
On the other hand, he says, plastic has contamination problems. Reground must be added to virgin material. “You have to make two more plastic containers just to get rid of the one you made in the first place,” Brooks says. Recycled plastics have permeability problems which steel does not have.
There is a lot of talk about plastic wood, but it has not found widespread acceptance in construction. Meanwhile, steel producers are making great inroads in the residential and the office building markets with their steel studs. Steel poles are becoming more common in high-tension and phone wiring applications. Construction remains a key market for steel. Heenan says the appliance market, too, will stick with steel.
The plastics industry also has to deal with the fact that most plastic products headed for the recycler have a lot of air in them. This makes shipping tough. Some mechanism for crushing or shredding the material closer to the point of collection (much the way cardboard is baled at many sites) would take a bit of the onus away from plastics. Steel products, on the other hand, tend to be pretty solid and more efficient to transport.
Still, plastics will remain a competitor and will have to be considered in any discussion of steel’s future.
Glass recycling is doing well, too. Beer remains the mainstay of the glass packaging business, constituting 48% of the market. Steel has little hope of taking back market share in the bottle or can business.
“Nothing major has changed (in glass packaging),” says Joe Cattaneo, vice president of the Glass Packaging Institute, Washington, D.C. “There is a trend to thinner-walled containers in beer, so you are looking at a lot more light-weighting. That means a reduction in tonnage.”
Glass beer bottle shipments through September, 1999 were 196,131 thousand gross. That is up somewhat from 1998’s figure of 195,241 thousand gross. Production also was up, at 197,504 as of this past September. Last year’s figure was 194,611. That also shows some inventory building in beer containers.
Continued improvements in the process of making glass will assure that it remains a competitor for the steel industry. Owens-Illinois, Inc., Toledo, Ohio, owns much of the technology used in the glass packaging industry. In August, the company announced a new process that substantially reduces the amount of glass needed to manufacture a typical glass bottle. Called Duraglas XLT, it lightweights the glass, but increases its strength when compared to traditional materials.
“By dramatically reducing the amount of raw material and energy required in the manufacturing process and increasing the rate of production, Duraglas XLT containers help make glass one of the most cost-effective and environmentally friendly, 100% recyclable choices in packaging,” says Joseph Lemieux, CEO of Owens-Illinois. He points to a 10-20% reduction in raw materials in the production of a typical 12-ounce beer bottle.
While not offering specifics, the company does project additional savings will be possible as research improves the technology. Miller Brewing Co.’s Milwaukee, Wisc., operations are using XLT bottles produced at Owens-Illinois’ Streator, Ill., plant. So, glass is not sitting on what laurels it has.
Glass has several continuing advantages over steel in the consumer arena. It is microwavable. It is transparent, so it showcases products well. Most consumers agree that it preserves the taste of what is in the bottle. On the commercial side, it does not deteriorate, corrode, stain or fade. It needs no internal protective coating. It is autoclavable, so it is appropriate of special lines like pharmaceuticals.
Like a fighter with a glass jaw, there are weaknesses in the overall glass recycling business. One is the relative availability of the material glass is made from. Glass is pretty simple stuff: silica, sand and soda. While a lot of glass is recycled – the recycling rate has hovered around 35% for the past few years – it still is not an extraordinarily high-value item. So, it is expensive to ship collected material to bottle makers. There are problems sorting colors. Bottle makers may end up using only 30% recycled cullet when they could use 50%, if only a supply were handy.
OTHER METALS
Other materials, like aluminum, are often mentioned as competitors to steel. Recycled aluminum is a sizable component of the U.S. aluminum supply. According to the Aluminum Association, Washington, D.C., recycled aluminum was 33% of supply in 1998. The transportation market, which consumes over seven billion pounds of aluminum, is the largest sector of the aluminum industry, two billion pounds ahead of the container market.
But aluminum has its own problems – enough that it might think about looking over its shoulder for a challenger. Some observers maintain that magnesium will replace aluminum. They say the magnesium market is about the same place that aluminum was after World War II . . . a light, strong metal that has a host of applications for industry. It simply needs to spend a bit more time in the research and development stage, finding its spot in the industrial arena. Autos are most frequently mentioned as the prime target for lightweighting.
There is little doubt that cars will be lighter in the coming decades than they are today. CARI’s Shaw says that transfer of materials alone will not change the makeup of the car of the future, although improvements in materials and new materials will be part of the picture. However, the ability to recycle components may be even more important in the 21st century than the weight of the components, some observers believe.
“Remember that it is life-cycle management, not just fuel consumption, that is driving the recycling of automobiles,” Shaw says.
For that reason, Heenan maintains that steel will have the inside track in the auto industry for some time to come. “In real estate they talk location, location, location. In the auto industry, it comes down to three things: cost, cost, cost,” he says. “If a material can not be as safe as steel and as cost-effective as steel, it won’t even make it into the ballpark with auto makers.”
Rest assured that recycling old vehicles is becoming a major cost factor in auto manufacturers’ budgets. Until the plastics industry gets its own recycling issues ironed out, it won’t be a severe threat to iron and steel. “Products of the future will have to be managed to the ends of their lives,” Shaw maintains. In Europe, the future starts in just two years when automakers must demonstrate an 85% materials recycling rate for their end-of-life (ELV) vehicles.
And Heenan adds that the existing infrastructure of auto shops with trained workers who know how to repair and bend steel and replace it economically if it is damaged, bodes well for steel’s long-term viability with auto makers.
That will make it tough for plastics, or any other materials, to make big inroads on steel in Detroit. Several different types of plastics, often from dozens of producers, go into a typical car. A first step toward more easily separating and recycling automotive plastics is the work being done on labeling the kinds of plastic used for plastic parts in cars.
BET ON STEEL
In short, the smart money will place a bet on steel and steel recycling. “Continued growth in the economy requires growth in the primary material. But there will be growth in recycling, too,” says Shaw.
If you are over 40 years of age and in the ferrous scrap business, most of these arguments will not have any effect whatsoever on your income. Even if other commodities do take a chunk out of the iron market, steel will continue to be a basic industry for decades to come. Steel scrap will continue to be recycled and demand should remain strong.
However, if you are the equivalent of The Graduate 2001, you may want to consider mixing a few of those other commodities in with your portfolio. Look beyond today’s contenders to rising stars like magnesium, which is only a twinkle in most recyclers’ eyes. Make market contacts now while the emerging sectors are young. If a market like magnesium flops, you will not have lost a lot. However, if it takes off your operation will be in on the ground floor and will be an experienced hand in recycling the commodity. But don’t dump your magnet cranes and bet the whole operation on an emerging market.
“You’re going to need old steel to make new,” Heenan states. “It’s a good looking situation for steel recyclers.”
In the final analysis, even the most ardent of anti-iron people do not predict the permanent retirement of either the primary or the recycling portions of the steel business. It’ll be around and punching for years to come.
The author is an environmental writer and Recycling Today contributing editor based in Strongsville, Ohio.
Get curated news on YOUR industry.
Enter your email to receive our newsletters.
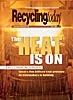
Explore the July 2001 Issue
Check out more from this issue and find your next story to read.
Latest from Recycling Today
- SABIC’s Trucircle PE used for greenhouse roofing
- Hydro to add wire rod casthouse in Norway
- Hindalco to invest in copper, aluminum business in India
- Recycled steel price crosses $500 per ton threshold
- Smithers report looks at PCR plastic’s near-term prospects
- Plastics association quantifies US-EU trade dispute impacts
- Nucor expects slimmer profits in early 2025
- CP Group announces new senior vice president