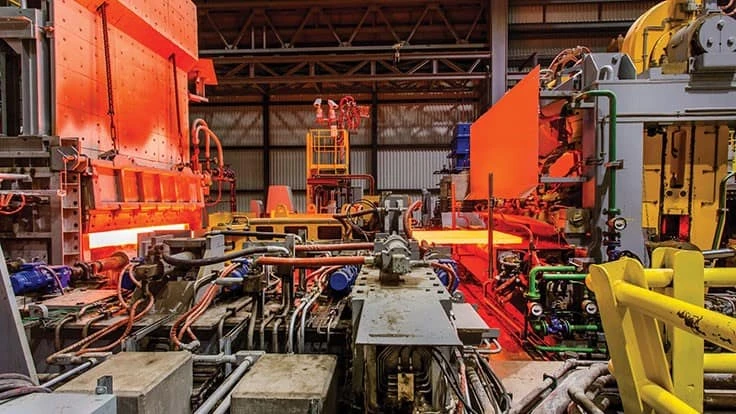
Photo courtesy of Big River Steel.
San Francisco-based Global Energy Monitor (GEM), in a 36-page June 2021 report, says global steel overcapacity means “many older and polluting steel plants can be closed without disrupting global supply.” The think tank identifies basic oxygen furnace (BOF) mills with blast furnaces as those that should be closed in an era when “the global iron and steel sector faces a reckoning with climate change.”
Separately, global consultancy EY (formerly Ernst & Young) has issued two reports focusing on ways steelmakers in India can take part in a “financially and environmentally relevant” post-COVID-19 recovery effort, in part by replacing BOF capacity with scrap-fed electric arc furnace (EAF) capacity.
GEM says its research indicates more than 60 percent of global steelmaking capacity remains tied to blast furnace-BOF (BF-BOF) production methods, which it calls “the most carbon-intensive conventional method of producing steel, with limited, difficult, and high-cost decarbonization options.”
The report, co-authored by Caitlin Swalec and Christine Shearer, says steelmakers in Asia, in particular, are “doubling down” on what it calls “old technology.” This, GEM says, “could lock in carbon emissions for the lifetime of each plant (40 or more years) without intervention in investment cycles.”
Considering emissions targets tied to the Paris Accord and decreed by several national governments, “If innovative low-emissions technologies reach commercial scale at the projected pace, the steel industry faces $47 billion to $70 billion in stranded asset risk for carbon-intensive steel plants currently under development,” writes GEM. Most of this “stranded asset risk” is in China, GEM says.
In addition to the wider adoption of existing EAF technology, the GEM report points to hydrogen-based direct-reduced iron and carbon capture and storage techniques as methods that can help the steel industry reduce its carbon footprint.
Focusing on India, a September 2020 24-page report by EY found many of the same problems and potential solutions. That document, co-authored by V.R. Sharma, Paresh Vaish and Saurabh Bhatnagar, states in part, “Several economically viable options [are] being tested as a replacement of the carbon route, and some of them are being considered for scale-up.”
Among the problems in India, according to EY: “Developing economies that depend primarily on the BF-BOF route due to the scarce availability of scrap have higher total energy consumption and material consumption per ton of steel” produced.
At the same time, the consultancy notes, “The government of India had released draft environment guidelines that are quite stringent and may further become rigorous in the future. This shall affect many inefficient and small steel producers, as they may find it unviable to produce steel while complying with increasingly strict environment norms.”
In a June 2021 follow-up report by EY, titled “Towards Greener Steel - Steering the Transition”, the authors find that “reducing the energy intensity and environmental impact of the industry will require a significant effort across the life cycle of steel.”
A “greater move to EAF production and investment in a robust recycled steel supply for steelmaking” is listed as one of the emissions-reductions strategies for Indian steelmakers. States the new EY report in part, “As demand for green steel increases, countries with more sustainable steelmaking industries are likely to reap a competitive advantage.”
The complete GEM report can be found on its website, while the June 2021 24-page EY report on India’s steel sector can be found on this web page.
Latest from Recycling Today
- Aqua Metals secures $1.5M loan, reports operational strides
- AF&PA urges veto of NY bill
- Aluminum Association includes recycling among 2025 policy priorities
- AISI applauds waterways spending bill
- Lux Research questions hydrogen’s transportation role
- Sonoco selling thermoformed, flexible packaging business to Toppan for $1.8B
- ReMA offers Superfund informational reports
- Hyster-Yale commits to US production