Auto shredders are well established as important processing systems for the recycling of automobiles, large appliances and other obsolete metallic scrap.

Although the basic technology has now been around for several decades, recyclers and their equipment suppliers continue to examine new approaches to maximizing the amount of metal (and the extent of profits) that can be recovered from the shredder stream.
Equipment companies and shredder operators take different paths to try to maximize production and quality, although there are some points of agreement beginning to emerge.
EASY ON THE WATER. Shredder operators are well aware that dust suppression benefits them in many ways, by: 1) Avoiding nuisance complaints and unhealthy emissions; 2) Increasing operator visibility; and 3) keeping metallic dust in the stream of recovered and marketable materials.
As long as the first two points are accomplished, it is working in coordination with this third goal that can be a key variable in how much water is used, says Bobby Triesch of consulting firm Shredder Dynamics Inc., San Antonio.
Suppressing dust has taken many forms over the years, often involving varying amounts of water and the addition of foams and chemicals. "I can’t stress enough how every shredder plant is different," says Triesch. "I have operated systems that used as much as 150 gallons per minute during maximum continues shredding to as little as 30 gallons per minute during maximum continuous shredding."
He continues, "The difference comes down to what kind of separation system is being utilized in the downstream. The wet downstreams use more water while the damp shredders use less."
Jim Schwartz of Texas Shredder Inc., San Antonio, says his company is seeing overwhelming demand for damp shredding systems. "We’re selling the heck out of those; we’re retrofitting existing systems left and right," he remarks. These systems can use just 10 or 15 gallons per minute, or even no additional water during rainy or snowy weather.
Schwartz credits Trevor Masters, a U.K.-based shredder system designer who works in coordination with Texas Shredder Inc., for his development and upgrades of the SmartWater systems sold by Texas Shredder.
SmartWater may cost a little bit more up front, says Schwartz, but it can quickly save operators money in their cost-per-ton processed value. "You don’t use more water than you need to. Damp shredding puts just enough water in the shredder box to suppress the steam, to keep down the dust and to mitigate explosions, but then you don’t have to wring water out of the product," he comments.
A FULL ARRAY OF METALS. While securing a clean, marketable ferrous scrap grade is always a priority for shredder operators, attention paid to the nonferrous portion of the stream continues to escalate.
According to Javier Herrera, VP of business development and technology with Harris Waste Management Group Inc., Peachtree City, Ga., operators are using several techniques to maximize their return on the nonferrous portion of what they produce, including:
• A more consistent loading on the separation systems by properly sizing the
material before it arrives to the eddy current systems
• The use of newer eddy current systems designed to process the fines portion more efficiently by working at a higher frequency
• And using metal recognition systems that can further recuperate the stainless steel materials not affected by the eddy currents as well as any residual metal that has not been picked up by previous systems.
Says Denny Jennerjohn of Metso Minerals Metal Recycling, Brookhaven, Miss., "There is a definite trend toward adding screening/sizing equipment and multiple eddy currents. The reliability of modern eddy currents has made online installations more popular."
Systems such as the SSE Metal Recovery System marketed by Wendt Corp., Tonawanda, N.Y.; a system from SGM Magnetics, with U.S. offices in Sarasota, Fla.; and the Steinert ISS system offered by Resource Recycling LLC, St. Petersburg, Fla., are designed to pull metals out of the residue stream that used to require a heavy media plant to find.
"In many cases, adding this to your system allows you to reclaim costs out of what used to be landfilled," says Jim Stepanek, sales manager of the shredder division of Wendt Corp. "There’s a fairly quick payoff on our SSE system."
Schwartz of Texas Shredder, which helps market the Steinert ISS system, agrees about the rapid returns these advanced eddy current systems can bring. "These machines get all of the metals—ferrous, nonferrous or stainless—and do a fair job of getting insulated copper wire," he notes.
"This is an important final step," Schwartz continues. "The normal practice emerging is to put this system last, and it gets almost all of the metal left in what was the waste stream. Operators are realizing extra metal sales and they’re cutting down on the number of pickers."
Schwartz acknowledges that the upfront investment for such a process is expensive, but agrees with Wendt Corp.’s Stepanek that the payoff is quick. "Even at $300,000 or $400,000 for a system like this, it can be just a few months before operators have a positive return on their investment," he remarks. "These are being used by people who never imagined they were throwing out that kind of metal."
Heavy media separation remains a viable last step, whether for a mixed residue/metals stream coming from a shredder with few downstream capabilities or for a mixed metals shipment coming from a facility with extensive separating systems.
"Individual operators still send their material out to these plants for further separation," says Herrera of Harris. He notes, though, that "some operators in countries with low labor costs are also purchasing this mixed material by container loads from U.S. operators for manual separation in their countries."
IN SEARCH OF CONSISTENCY. Another truism that seems to have been accepted is that shredders and downstream systems operate best when the flow of material is consistent, rather than coming in fits and starts.
This holds true throughout the process, from initial infeed to the shredder box through to maximizing eddy current productivity. Schwartz says there "is no downside to full-box shredding. If you keep the box full, you’re going to get more tons per hour and more life out of your wear parts."
A shredder mill that is consistently filled with material will extend wear parts life, says Schwartz, because "material will work against itself." These metal-on-metal collisions will then perform some of the work that would otherwise be performed by the hammers and walls. Autofeed systems are the only way to ensure full box shredding, says Schwartz.
Schwartz credits Jim Mosbach of the Metal Management Inc./NIMCO facility in Newark, N.J., as being an early pioneer in exploring the benefits of full box shredding. Texas Shredder now offers autofeed systems that Schwartz says involve "parameters and algorithms" to help maintain a carefully monitored, consistent feed.
The AutoPilot system created by Trevor Masters has been designed to make continuous full-box shredding possible, says Schwartz. Schwartz emphasizes that a crane or loader dedicated solely to feeding the shredder infeed conveyor is also critical for large-tonnage maxiumum production.
THE MAGIC OF MAGNETS |
Whether recycling materials from the metals shredding stream, curbside products, construction and demolition debris, composting or municipal solid waste (MSW), the recovery of metallic content can provide the economic justification for a recycling or MSW processing facility. The magnetic separation equipment industry can provide magnetic head pulleys, suspended separators, magnetic drums and an eddy current system for non-ferrous metallic removal. Magnetic head pulleys used as the head pulley of a conveyor system provide a simple solution to recovery of the ferrous content in waste and recycling streams. A magnet suspended above a picking line, or a conveyor carrying other material, is also selected on the basis of volume, belt speed and material type and size. These units will provide a cleaner ferrous product with minimal losses. A combination of a suspended magnet preceding a magnetic head pulley can provide maximum recovery and cleanliness of the finished product. Magnetic drums consist of a stationary magnet assembly, which rotates around a non-magnetic cylinder, with cleats to provide transportation of the material. Normally these units are used where the percentage of ferrous is high and the physical size of ferrous could cause damage to belts on suspended magnets. Finally with the ferrous metallics removed, eddy current separators can be utilized to recover non-magnetic metallics, such as aluminum, copper, brass, 300 series stainless steel, etc. These separators consist of a short conveyor system with an alternating pole rare earth magnet assembly contained in a non-metallic drum. The magnet assembly rotating at a high speed induces current flow in the non-metallic particle creating a magnetic field surrounding it, which causes the particle to be repelled by the field on the rotor. Unlike magnetic separation which attracts ferrous particles, the non-magnetic metallics are ejected forward of the material trajectory. Just as the mining industry has used this equipment for natural resources, magnetic units can provide an inherent advantage to mining our recycled products above ground. — Don Morgan, Walker Magnetics, Worcester, Mass. |
Stepanek of Wendt Corp. cites the cutter bar on that company’s shredder models as an ideal way to save wear and tear on wear parts, in addition to allowing "the grates to size the material" more efficiently. "A cutter bar machine will [offer] longer grate life and fewer grate changes," he says.
The benefits of keeping a steady stream of material extends all the way through to the eddy currents at the end of the system, many industry suppliers agree. Herrera of Harris cites "a more consistent loading on the separation systems" as a key to achieving high-quality end products.
SIZE AND SPEED. When super-sized shredders with 120-inch rotors began appearing on the scene, industry observers wondered whether these "monsters" would muscle out smaller shredders in the 66 to 80-inch rotor size range.
The answer is that they have not done so, although many operators have found succes with the giant machines, and some manufacturers continue to tout their advantages.
The current market seems to have room for shreddres throughout the size spectrum, as manufacturers such as American Pulverizer Co., St. Louis, remain busy selling and upgrading shredders well under the super shredder size.
"We are talking with people around the country inquiring about plans for everything from the smallest shredders (60 by 60) to the largest shredders (120 by 104)," says Triesch of Shredder Dynamics. "The difference comes down to what type of market they are in. If they are in a major metropolitan area, most are talking about 98 or 120-inch machines, while in smaller markets, people are thinking about 60 or 80-inch machines."
Among manufacturers, Wendt Corp.’s Stepanek argues for the merits of larger machines beyond their potential output advantages. "Bigger is better," he remarks. "A key to successful shredding is the force of the hammers. A 1,200-pound hammer with good rotor speed can shred heavier material, including some demolition scrap and plate and structural forms of steel."
Even smaller shredders produced by Wendt Corp. feature a rotor configuration that "gives operators the ability to use a larger hammer and shred heavier material," says Stepanek.
Jennerhohn of Metso Corp. says, "Of course size matters, especially considering the inertia increase with the larger rotors." He remarks, though, that "a heavy-duty 80-inch model will shred anything that should be allowed in any shredder."
Schwartz says Texas Shredder customers are showing a preference for "bigger shredders, without a doubt." He continues, "If a company had a 60/80, it is going to an 80-inch class shredder. Those with 80-inch models are going into 98-inch class shredders. Some of those folks even want 120-inch models."
Schwartz believes these upgrades usually make sense. "Larger models cost more to buy, but they cost no more to run; in fact, generally operators are finding them less expensive to run," he says. "There may or may not be a lower electrical cost (per kilowatt hour), but you can run the same amount of scrap in less time. If you are running fewer hours, this can give you increased flexibility to run within the off-peak electrical hours that some utility companies offer at lower rates."
Stepanek also cites reduced operating hours as a cost savings key with larger shredders, also noting that this then saves wear and tear on castings. "A bigger shredder with larger hammers and other castings should result in fewer operating hours and a lower cost per ton during production. Also, these larger castings can absorb the impact and last longer, creating less of a need to bring in the maintenance crews to change parts."
MATCHING THE MARKET. If there is, in fact, a move toward larger shredders occurring in North America, is this causing shredder capacity to match or to exceed the expected demand for scrap shredding?
Forecasting is always a tricky business, and recyclers and manufacturers can consider several factors.
On the one hand, the percentage of obsolete scrap as part the overall scrap stream seems to be increasing. This is due in part to overall industrial production in North America either declining or leveling off and also to scrap-generating factories become increasingly efficient in their materials usage (thus producing less scrap).
Household consumers, meanwhile, continue to buy and cast off old vehicles, washers and driers, keeping the stream of obsolete scrap steady or growing.
"By analyzing the trends, we can see that while the U.S. consumption [of durable goods] increases consistently, even during slower economic times, the generation of recyclable scrap will continue to increase," says Herrera.
But the boom in shredders installed in the previous decades—and now in some cases being upgraded—may have already anticipated this ongoing flow of scrap.
Most shredder operators believe their field is a competitive one, implying that existing shredder operators are waging a battle to obtain sufficient feedstock for their machines.
Triesch sums it up this way: "The name plate capacity of all of the shredders in the U.S., if operated correctly to the maximum potential of the shredder and the motor, would far exceed the available amount of tons of obsolete scrap being generated."
Considering the level of competition, the quest for greater efficiency, cost savings and marketable metallics yield is likely to continue.
The author is editor of Recycling Today and can be contacted via e-mail at btaylor@RecyclingToday.com.
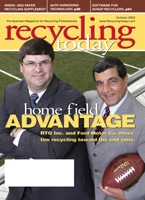
Explore the October 2003 Issue
Check out more from this issue and find your next story to read.
Latest from Recycling Today
- Nucor receives West Virginia funding assist
- Ferrous market ends 2024 in familiar rut
- Aqua Metals secures $1.5M loan, reports operational strides
- AF&PA urges veto of NY bill
- Aluminum Association includes recycling among 2025 policy priorities
- AISI applauds waterways spending bill
- Lux Research questions hydrogen’s transportation role
- Sonoco selling thermoformed, flexible packaging business to Toppan for $1.8B