More and more, producers and contractors are entering the recycling market. Lack of landfill space, transportation and handling costs, raw material shortages and compatibility for reuse with virgin aggregates all make recycled aggregate material attractive to produce. Recycled feed material is often cheaper than natural aggregate, especially if there is a tipping fee involved. By recycling material, the producer/contractor can usually increase profit while reducing cost. And many producers want to act on a desire to extend existing aggregate reserves. Accompanied by the increase in oil prices over the last two years, the use of recycled asphalt pavement (RAP) in hot-mix asphalt has contributed to substantial operating cost savings. Current market trends and industry practices prove that contractors can produce top quality RAP at top-value prices, thus keeping asphalt and concrete rubble out of landfills. Additional savings realized by contractors and municipalities will further increase the market size and demand for recycle crushing equipment. The time for contractors and producers to look at the recycling market as a viable extension of their business is now. But how can contractors know if recycling is the proper niche for their operation? Initially, there are several questions contractors and producers can ask themselves as criteria for getting into aggregate recycling. These include: • Is there a market for the end product? • Will recycle reduce the cost of doing business? • Does recycling provide a valuable service to the current or prospective customer base? A Natural Evolution Vern and Kirk Young, father and son owners of Young Contracting in Niceville, Fla., pride themselves on being a single-source solution for the developer, providing site development solutions for shopping centers, subdivisions and condominiums. It is a benefit to their customers that Young can provide all of the following from a single management and bidding perspective: • Site modifications, with necessary building demolition, dirt and existing pavement removal, and overburden removal. • Site preparation including adding fill or base, trenching and installing water and sewer lines, flat work (concrete paving, sidewalks, curbs and gutter) and asphalt paving. • Land clearing, including mulching stumps and branches for pulp wood and larger logs to the sawmill. “We’re unique in that we try to use everything from a job site,” notes Kirk Young. “Some of our competitors still dump, and even burn. Our efforts toward recycling ensure that almost nothing goes to a landfill. It was a natural progression for the Youngs to venture into asphalt recycling. “We’ve always tried to be the area leaders in our field,” says Young. “We originally started pavement recycling by utilizing millings from a local asphalt contractor. We were one of the first in this area to realize a use for this material as a viable fill product. Early on, the pavement contractor gave us the millings in return for hauling them away. Then the price went to $1 per yard. From there, the prices have escalated to a competitive nature.” Young Contracting is a good example of an ideal recycle contractor. They understand that concrete, asphalt and C&D material are resources that are readily available at virtually all demolition sites. Instead of thinking of this material as waste, contractors like Vern Young realize the economic benefits of turning this material into revenue and keeping it out of landfills. Operating their own portable equipment enables them to use recycled material not only for their own projects, but also to provide an added service to the local asphalt contractors in their area. Kirk Young says getting into the crushing business was an extension of the family’s work ethic. “We have always tried to do as much of the project as possible with in-house equipment, labor and know-how,” he says. In the early days, the Youngs stockpiled asphalt and concrete, hiring a contract crusher as the stockpiles became excessive. They recognized this was not an efficient use of their storage yard, equipment or labor. “We eventually realized by having our own crusher onsite, we can process the material as we accumulate it and immediately use it on the next project. Also, we keep the money we were paying out to the crushing contractor. “With the volume of recycle we process, it is a competitive advantage for us to offer alternatives. Our customers have the option of using virgin aggregate, or a lower cost material. The savings can be significant for them,” he continues. “We have a history of satisfied customers, and acceptance of recycled materials has not been an issue.” Making the Call Once the Youngs decided to enter the recycleing market, there was a decision that remained: What type crusher to purchase, and from whom. “The Youngs have been good customers of ours for a long time,” says Jerry Avery, an aggregate specialist for Beard Equipment, which has offices in Mobile, Ala., and the panhandle of Florida. “They are good contractors, too; very picky about their equipment and the appearance of their yard and office, and so on. “They had experience already with grinding trees and stumps, prior to their decision to crush asphalt and concrete,” Avery continues. “And they had worked with a contract crusher, as well. So the concept was not new to them. When we began our conversations about a recycling crusher, I told them right off I felt the Kolberg-Pioneer 4233 Recycler was a good choice for them.” The low 9 feet, 5 inch feed height is ideal for the contractor who moves often and doesn’t wish to build a ramp for loading. The angle of the 36 inches by 15 feet variable speed belt feeder provides the operator with easy visibility over the receiving hopper to manage the feed rate. A large 36 inches by 33 inches feed opening handles slabby materials. Recommended maximum recycle feed sizes are 24 inches by 24 inches by 12 inches. The unit is also suitable for aggregate applications, with a maximum feed size of six inches to eight inches in hard rock and eight inches to 10 inches in softer limestone. The grizzly bypass between the feed belt and the impactor separates fines and undersized product from material to be crushed, increasing overall tons-per-hour, while reducing wear costs on the blow bars. Depending on feed material, feed rate and material gradations, the crushing system is capable of producing up to 140 tons per hour. Both primary and secondary aprons are adjustable for gradation control and provide relief for uncrushables. Fabricated with four-inch abrasive resistant steel, they feature replaceable wear tips at the high wear trailing edge. The crushing system Young uses has a three-bar rotor design that is said to combine the mass and strength of a solid rotor with the penetration of an open rotor. The three bars have a wedge-locking system and are reversible. The 42 inches in diameter by 33 inches wide rotor is also stress relieved. In addition, the housing opens hydraulically past center, exposing the rotor and side wear plates for easy access. Another feature for portability is the standard 30 inches by 29 feet discharge conveyor, which provides an 11 feet, three inch discharge height for direct loading into a truck or maximum stockpiling without additional conveyors. With a plant weight of 54,500 pounds, the recycling crusher is portable without special permits. Travel height is 13 feet, 5 inches and width is 9 feet, 1-1/4 inches. An optional tire arrangement is available to accommodate an 8 feet, 6 inches travel width, if required. No special trailer or tractor is required when it’s time to move. At 44 feet, 6 inches in length, the resulting small footprint is ideal for tight job spaces and maximum material storage. Standard onboard power is provided by a 165 horsepower diesel engine (Cummins or John Deere are available), which powers the impactor, variable speed belt feeder, discharge conveyor and magnet. Young had two large jobs that involved crushing concrete and more than 100,000 tons of asphalt to recycle. According to Vern Young, the first two jobs saved him several thousand dollars and provided him with base material he could use onsite. “The crusher did everything Jerry and the factory said it would,” says Kirk Young. “And we’ve had virtually no problems with the crusher. The low feed height allows the operator to watch the feed material for optimum production rates. And the ample discharge conveyor height gives us good stockpiling capability for efficient loader use. We're getting more than 400 hours on a set of blow bars, and our gradation is easily maintained,” he adds. This article was supplied by Kolberg-Pioneer, Inc., Yankton, S.D.
When a contractor like Young Contracting decides to buy recycling equipment, the company must ask itself several questions. The following criteria can help with manufacturer and equipment choice: • Is portability a factor? • What are the volume and production requirements? • What is the product size desired? • Do site conditions cause limitations? • What will be the capital investment? • What will operating costs be, including labor, wear, maintenance? • What is the material to be processed - and will there be contamination?
Important Questions
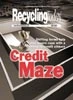
Explore the May 2001 Issue
Check out more from this issue and find your next story to read.
Latest from Recycling Today
- Magnomer joins Canada Plastics Pact
- Electra names new CFO
- WM of Pennsylvania awarded RNG vehicle funding
- Nucor receives West Virginia funding assist
- Ferrous market ends 2024 in familiar rut
- Aqua Metals secures $1.5M loan, reports operational strides
- AF&PA urges veto of NY bill
- Aluminum Association includes recycling among 2025 policy priorities