
Photo courtesy of T.J. Rosario, Metalico-Girard

To hear T.J. Rosario tell it, the decision was a relatively simple one to make.
When the time came for Cranford, New Jersey-based scrap processor Metalico to find a replacement for the Sennebogen electric pedestal-mounted material handler at its Girard, Ohio, yard after 15 years of service, the company chose to stick with a Sennebogen electric offering. It upgraded from an 835 E model that was installed in 2007 to an 840 E model that was put in place May 2022.
After nearly a year of runtime, Rosario, Metalico-Girard maintenance manager, says the 840 E has been a strong addition to the yard as it places scrap onto the infeed conveyor to the shredder.
“It’s been doing well,” Rosario says of the new machine. “The operator loves it. It’s been trouble-free; we haven’t had any issues with it.”
Each day, the scrap handler operates for about 10 hours and handles between 800 pounds and 1,000 pounds of ferrous and nonferrous scrap.
Looking back at the installation, Rosario says the transition from the old scrap handler to the new one was smooth but required collaboration between Metalico, Oakwood, Ohio-based sales partner Alta Equipment and Sennebogen LLC, the Stanley, North Carolina-based subsidiary of Germany-based Sennebogen GmbH.
Necessary equipment

Rosario says Metalico’s Sennebogen 835 electric handler had run for about 30,000 hours before it was replaced last year. He was instrumental in the machine’s purchase in 2007 when the Girard yard was then owned and operated by Liberty Iron & Metal.
Metalico, which boasts 27 locations in eight states and has more than 450 employees, acquired the Girard yard in 2020.
The company recycles scrap iron and steel, which it sells to domestic mills and furnaces. Additionally, it recycles nonferrous metals, such as aluminum, copper, lead, stainless steel and high-temp alloys that it sells to domestic manufacturers and to some export markets. Metalico also buys catalytic converters and recovers platinum group metals, including platinum, palladium and rhodium. According to the company’s website, it operates two catalytic converter sites and three automobile shredders.
Metalico purchases scrap from manufacturers, small scrap dealers, demolition contractors and through retail. The metals are sorted and prepared for sale to mills, furnaces and foundries.
At the Girard location, Rosario says the material handler primarily grabs automobile scrap, various types of sheet scrap, white goods, some structural materials and other similar items. But 15 years of use had led to increased downtime needed for repairs on the machine.
“[The material handler] is pretty vital to the operation [of the scrap yard],” Rosario says. “You could do without it, but it makes it tough. On the older one, it started getting tougher because it began breaking down more. We learned to do without it [during downtime], but it does hurt the production.”
Everett Zoog is a material handler and paving specialist at Alta and sells machinery throughout Ohio. He brokered the sale of the new 840 E model to Metalico-Girard and says the company’s biggest concern when contemplating the upgrade was not whether to continue using an electric material handler but ensuring machine uptime.
“All these machines are going to break because it’s a tough environment,” Zoog says. “But it’s just how quick you can get them up and running after the fact. It comes down to parts availability and the relationship [with the seller].”
Staying electric
The material handler’s uptime is of the utmost importance to Metalico, and using a machine with an electric motor has been a difference-maker.
Rosario points to ease of maintenance as a big factor in the company choosing electric over diesel. Additionally, because the Girard yard already had an electric scrap handler in use, the new one could be attached directly to the existing power grid, making for a smoother installation.
“[Performing] service is a lot easier because there’s no diesel motor,” he says. “All you have is the hydraulics. The electric motors are trouble-free; even the one we took out, it had 30,000 hours on it, and we had zero problems with the motor.”
Zoog adds that while there isn’t enough data on electric motors to gauge exactly how long they can last, their lifespans have the potential to be much longer than diesel models, which he says can last 12,000 hours to 15,000 hours before wear takes a major toll.
“You don’t have any real maintenance besides hydraulics, and there’s a lot less vibration because it’s electric,” Zoog says of electric scrap handlers versus diesel. “So, a lot of your typical wear is nonexistent. Your oils, all the engine oil, the filters—the cost of ownership is less.”
Zoog says that although a customer might pay a premium price upfront for an electric scrap handler, a model that feeds a shredder every day is going to provide a quick return on investment.
“Something that will feed a shredder, it’s your beast,” Zoog says. “If you use it every day, you’re getting that money back pretty quickly,” he adds.
The installation

Metalico’s new 840 E handler was a size upgrade from its previous 835 E, adding 10 more feet of reach for a total of 65 feet, 6 inches. After a nine-month wait, the machine was shipped from the Port of Charleston, South Carolina, in 19 pieces then hauled to Girard on five trucks.
When the machine arrived, Metalico was ready. The company had four technicians, including two from Alta and one from Sennebogen, as well as two cranes to help put the pieces in place and electricians to aid in connecting the handler to the power grid.
Sponsored Content
Labor that Works
With 25 years of experience, Leadpoint delivers cost-effective workforce solutions tailored to your needs. We handle the recruiting, hiring, training, and onboarding to deliver stable, productive, and safety-focused teams. Our commitment to safety and quality ensures peace of mind with a reliable workforce that helps you achieve your goals.
In advance of the delivery, Rosario says Metalico upgraded from a 450-amp breaker to 600 amps. Because the location already was using an electric handler, additional changes weren’t necessary. The pedestal-mounted material handler sits on a 30-foot-by-30-foot pad of 12-inch-thick concrete.
“We have a big [electrical] panel that has a lot of excess capability that we weren’t using,” Rosario adds. “It wasn’t a big deal to upgrade it. Plus, there was already a spot there for it.”
The installation took five days to complete. According to an installation timeline provided by Zoog:
- On the first day, smaller parts were unpacked and moved closer to the installation area via forklift. Two trucks and two cranes hauled heavier equipment closer to where the machine was being erected near the shredder. Mechanics then put together the four-point base of the pedestal, and cranes were used to place the pedestal base over the electric hookup.
- On the second day, electricians updated the wires connecting the machine to the generator. Counterweights were installed and the pedestal was added. Catwalks were installed around the upper carriage as it laid on the ground, and wires were fed through the pedestal to connect the upper carriage.
- The upper carriage was placed on the pedestal on the third day.
- The fourth day consisted of placing the machine’s stick onto its boom, then connecting its hoses.
- The final day included fine-tuning and checking pressures. The grapple was installed and the operators were trained on the machine.
“The install took a while,” Zoog says. “The freight was five trucks, 19 pieces. Then you have to have a crane there waiting to take them off the trucks.”
Before the new electric scrap handler could be installed, “we had to take the old machine apart at the far end of the yard,” he says. “Then, a week later, [we] had to hire a crane again and another truck to haul all the pieces from the yard down to the shredder and had to plan for the shredder to be down for that long. There were a lot of logistics.”
Working in the yard’s favor was its 15 years of experience using an electric pedestal handler that had prepared the facility for an eventual upgrade.
“They had all their infrastructure in place,” Zoog says. “That’s really the hardest thing when you’re installing one of these machines. It’s having the transmitter, having the concrete pad, putting the wires underground to feed up and plug it in; that’s really the hardest part. Luckily, [Metalico] had all that in place.”
Get curated news on YOUR industry.
Enter your email to receive our newsletters.
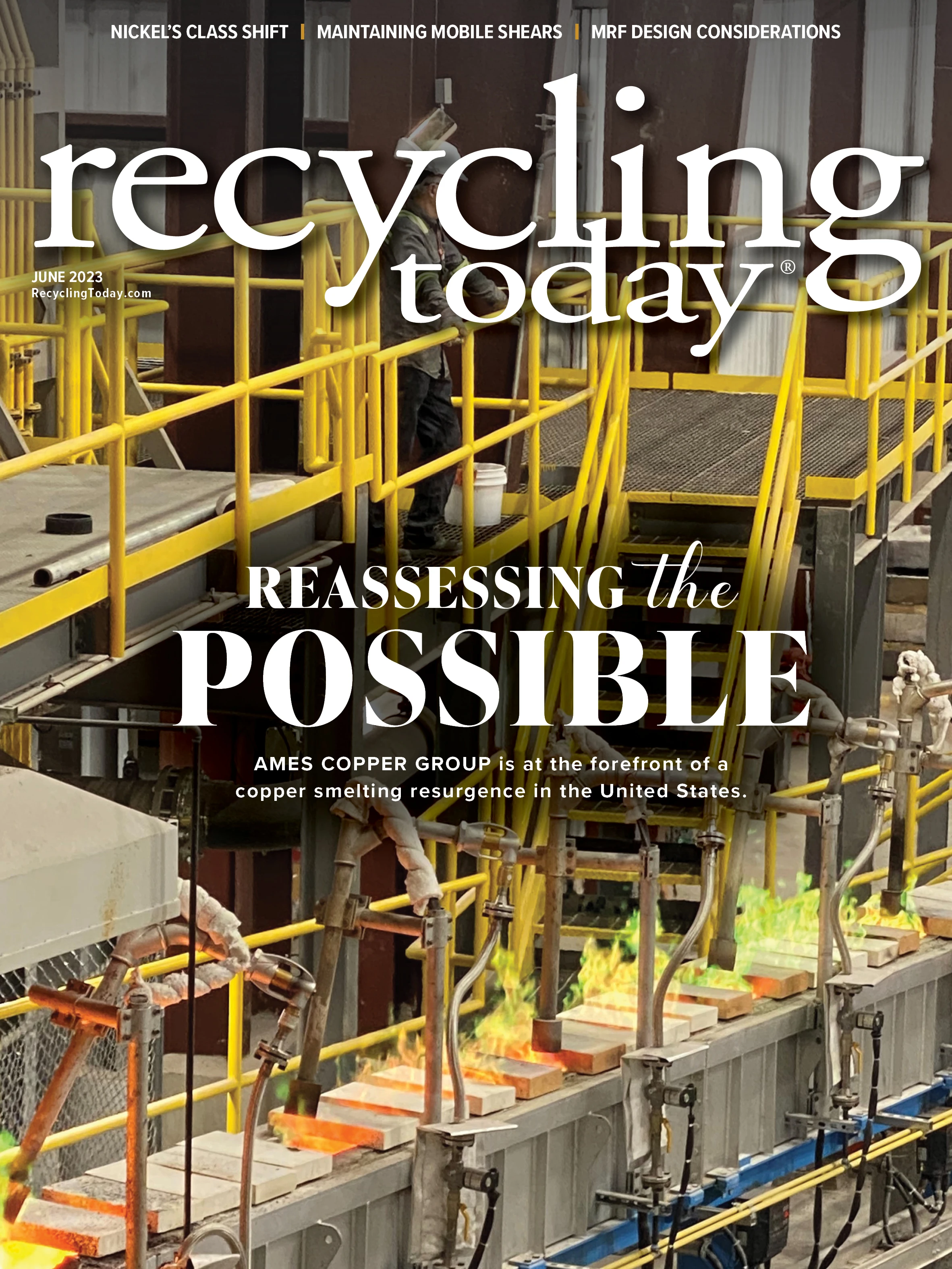
Explore the June 2023 Issue
Check out more from this issue and find your next story to read.
Latest from Recycling Today
- Athens Services terminates contract with San Marino, California
- Partners develop specialty response vehicles for LIB fires
- Sonoco cites OCC shortage for price hike in Europe
- British Steel mill’s future up in the air
- Tomra applies GAINnext AI technology to upgrade wrought aluminum scrap
- Redwood Materials partners with Isuzu Commercial Truck
- The push for more supply
- ReMA PSI Chapter adds 7 members