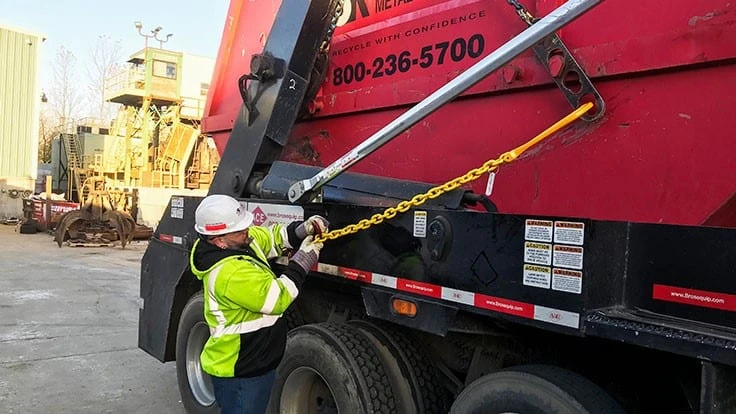
Photo courtesy of Sadoff Iron & Metal Co.

Industry groups including the Institute of Scrap Recycling Industries (ISRI), Washington, and the National Waste & Recycling Association, Arlington, Virginia, as well as lugger manufacturers and other organizations, have been meeting for years to develop a set of standards for lugger container securement that could be accepted by the Commercial Vehicle Safety Alliance (CVSA). The CVSA, based in Greenbelt, Maryland, seeks “to achieve uniformity, compatibility and reciprocity of commercial motor vehicle (CMV) inspections and enforcement by certified inspectors dedicated to driver and vehicle safety,” according to a description on its website.
The standards are the first of their kind to meet the Federal Motor Carrier Safety Administration’s (FMCSA) 49CFR 393.102(c) regulations regarding the minimum performance criteria for cargo securement devices and systems.
ISRI says the standards will simplify cargo securement procedures for CMV drivers and provide equivalent means to other standards for lugger truck cargo securement.
The new standards
The new cargo securement standards require operators to chain or strap the lugger container to the body of the CMV. In some cases, as many as eight winch straps are needed per container.
According to the CVSA Inspection Bulletin dated Sept. 28, 2020, the requirements only apply when the CMV isn’t equipped with an integral securement system, which is a system on certain roll-on/roll-off and hooklift containers and their related transport vehicles that mates compatible front and rear hold-down devices to secure the complete vehicle and its cargo. Lugger container vehicles do not have these integrated securement systems.
Because the United States and Canada did not specify in their standards how that securement needed to be done, the industry created several different types of securement to prevent forward, rearward and upward movement. Without an integral securement system, other ways of securement are needed for lugger container vehicles, according to the CVSA bulletin.
Put to the test
Industry tests helped to determine the equivalent methods for securing lugger boxes.
In August 2020, Cleveland-based roll-off trailer and lugger hoist manufacturer Ace Brother’s Equipment Inc.; ISRI; Fond du Lac, Wisconsin-based Sadoff Iron & Metal Co.; Fond du Lac-based Whealon Towing & Service Inc.; and the Wisconsin State Patrol worked together to test securement methods for lugger trucks that would be approved by CVSA.
“Our initial testing was done in July, and it passed two of the three tasks,” Andy Coates, fleet operations manager at Sadoff Iron & Metal Co., says. “The third one had failed, so I had to go back and come up with a couple of different ideas to look at the forward acceleration of the container. We tested those, and we were able to get positive results.”
Coates says the change to this standard was important because it made the process more efficient and saved money, but it also improved safety. The old method of securement took around 10 minutes, while with the new standard it can be completed in about 90 seconds to two minutes.
“Our initial testing was done in July, and it passed two of the three tasks.” – Andy Coates, fleet operations manager, Sadoff Iron & Metal Co.
So far, he says, the feedback from his drivers has been good.
“Most of the guys have embraced it and actually had some positive comments,” he says of the new standards. “Previously, the containers would kind of wiggle around on the trucks, and now they don’t anymore. Not that they were in danger of going anywhere, but they keep it a bit more steady on the truck,” he says of the new securement method.
Coates adds that his company’s trucks are black and red. When searching for new chains to meet the securement regulations, he found bright yellow ones, which, while unintentional, have been helpful.
“My contact with the state patrol actually texted me in the last week, and he saw one of our trucks going down the other side of the highway,” Coates says in early December 2020. “He saw that yellow chain, and it just leaves no doubt that it’s secure, it’s visible,” he adds.
Know your options
Two different options prevent forward movement when securing the lugger box through equivalent means.
Option 1: With this option, the pin must be extended within 4 inches of the channel on the lugger box (if so designed) to prevent forward movement, CVSA’s Inspection Bulletin notes. (The channel on the box must be placed on the rear side of the pin.)

Option 2: With the second option, at least two securement devices are required, each with a minimum working load limit (WLL) of 9,200 pounds (4,173 kilograms), according to the CVSA. A minimum of one tiedown on each side going directly from the power unit hoist body to the container lift lugs or lifting keys is required. (Half-inch grade 80 chain is required, with a WLL of 12,000 pounds.)
Only one option is provided when it comes to securing against rearward and lateral movement.
With rearward movement, the pin must be extended, and the dump hook or dump key must be forward of the pin and attached to the container.
With lateral movement, the pin must be extended, and a space of up to 4 inches (10 centimeters) can be between the pin and the container on either side of the box.
When securing front and rear lifting chains, the lift chains can be loose during transit. This is not a violation, according to the bulletin, as the chains are not considered tiedowns for the purposes of cargo securement. Rear lift chains can be used during transit/roadside inspection.
If the equivalent means cannot be used, general commodity requirements would apply.
The lugger box must be secured for length and weight and requires a number of tiedowns to satisfy both requirements (e.g., one tiedown for every 10 feet or portion thereof plus an additional tiedown in the first 10 feet if not against a front-end structure; the aggregate WLL of the tiedowns must meet half the weight of the container and load), the CVSA says. Lugger box securement should be at the fixed longitudinal midsection between the lugs on the side of the lugger container. Any method is acceptable, but this can be achieved by using a tightening device (chains or straps) connected directly to the sides or top of the container. The tightening device must be anchored to the vehicle on the other end, according to CVSA.
Coates says the next step in this process is to get these standards written into regulation. “Currently, this only exists as an inspection bullet with CVSA. It’s not in regulation yet. So, the next step would be to take it to the FMCSA,” he says.
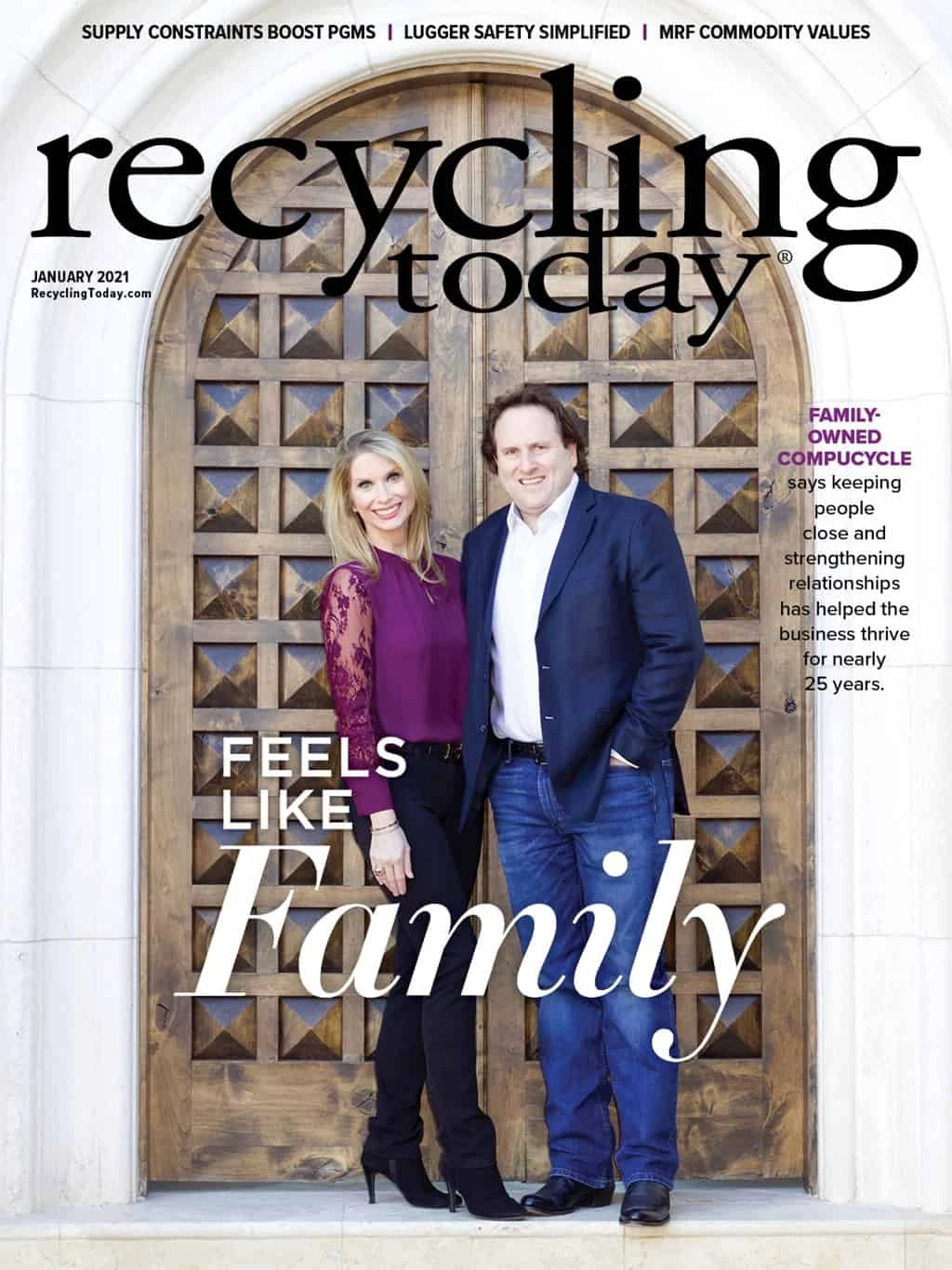
Explore the January 2021 Issue
Check out more from this issue and find your next story to read.
Latest from Recycling Today
- Toppoint Holdings expands chassis fleet
- Lego creates miniature tire recycling market
- Lux Research webinar examines chemical recycling timetables
- Plastics producer tracks pulse of wire recycling market
- Republic Services, Blue Polymers open Indianapolis recycling complex
- Altilium produces EV battery cells using recycled materials
- Brightmark enters subsidiaries of Indiana recycling facility into Chapter 11
- Freepoint Eco-Systems receives $50M loan for plastics recycling facility