Americans consume a great deal of soda, juice and bottled water, and in the hot, sticky Southeastern United
States soft drinks are especially in demand.
But even the thirsty residents of the U.S. Southeast have their limits, so not every beverage bottled or canned is consumed before its expiration date.
The leftover beverages present a business cost for bottling plants, which created an opportunity for Tony McCarthy and his company FMS Inc. of Clearwater, Fla.
FROM WATER TO PEPSI. Tony McCarthy learned the value of scrap commodities as a child growing up in Essex, England, where his father owned a trucking company.
FMS INC. AT A GLANCE |
Principal: Tony McCarthy, who founded FMS Inc. and The Drum Depot in 2002 Locations: Headquarters and plant in Clearwater, Fla.; custom beverage recycling systems set up in bottling plants throughout the Southeastern United States No. of Employees: 10 in Clearwater, plus others being hired for off-site locations Equipment: Custom expired and off-spec beverage recycling systems designed in cooperation with Sani-Tech Systems Inc., Duvall, Wash.; balers made by International Baler Corp., Jacksonville, Fla., and Harmony Enterprises, Harmony, Minn.; plastics grinders made by AEC Inc., Wood Dale, Ill. Services Provided: Recycling of off-spec and expired beverages, both the liquid and solid portions; paper, cardboard, glass, metal and plastic scrap recycling, including drums of all sizes |
On an adjacent property was a truck container fabricator, which often made containers with a combination of plywood, steel or aluminum as materials.
When it came time for those containers to be retired, young Tony’s grandfather showed him how to separate the metal, keeping a particular eye out for higher-value aluminum. "He took me to the scrap yard, and I got big-time money from that," recalls Tony.
The lesson stuck with Tony even after he immigrated to the United States in 1982, just after graduating from high school. In the United States, Tony worked in sales positions throughout the 1980s and 1990s, including three years working as sales manager for an engineering company, combining two of his favorite career aspects into one job.
The entrepreneurial urge was always present, however, as was the recollection of how recovering salvaged and scrap materials can be a lucrative business effort.
Founding Florida Marine Surplus (FMS) in Clearwater in 2002, Tony initially focused on selling aftermarket marine surplus parts and supplies. Before the year was out, he also started The Drum Depot, which concentrated on selling clean, empty 55-gallon drums as components for floating docks.
Activity in the drum business soon began outpacing that on the FMS side, "which led to transitioning to strictly the recycling end of the business," says Tony. The Drum Depot soon purchased two Nelmor-brand grinders made by AEC Inc., Schaumburg, Ill., so saleable secondary raw materials could also be produced from the stream of drums.
Working to expand the drum recycling business is what brought Tony into contact with bottling plants such as Tampa Pepsi, where drums of many different sizes-some full, some empty-were creating a disposal line item for the regional bottling plant.
At Tampa Pepsi, Tony helped set up a custom equipment line that required some upfront investment in processing capabilities, but ultimately is saving the company an estimated $10,000 per month in disposal costs.
GOOD TO THE LAST DROP. The processing, separation and recycling loop designed by Tony and FMS eliminates the landfill from the equation, finding a home for containers and expired product alike.
At the Tampa Pepsi facility, two processing lines have been set up-one for beverages in aluminum cans, the other for those in PET (polyethylene terephthalate) plastic bottles.
On both lines, forklift trucks bring pallets of expired or off-spec product to a staging area where a metal hopper is loaded with product. The hopper is then raised and tipped into an elevated hopper that leads to a conveyor that feeds the processing line.
The product first passes into what McCarthy calls a "bottle busting" machine that is equipped with an augur and made by Sani-Tech Systems Inc., Duvall, Wash. At this step, most of the liquid is separated from its container and is directed into a retaining system beneath and then near the processing line. The solid scrap proceeds through an augur which empties the fluid even more.
On the plastics line, empty containers then head for the baling chamber of a downstroke baler made by International Baler Corp., Jacksonville, Fla. For the aluminum can line, FMS has recently installed a baler made by Harmony Enterprises Inc., Harmony, Minn. According to Tony, the line is now producing dense 1,000-pound bales that have improved shipping profitability.
During the compression process, yet more liquid is separated from the marketable aluminum or plastic scrap and joins the rest of the liquid in the retaining system.
The overall FMS system not only captures the aluminum and plastic scrap, but also retains the mixed liquids and stores them for eventual shipment to end markets that Tony has helped discover.
It turns out thirsty humans are not the only ones who enjoy soft drinks. Cattle ranchers have reported that the sugary mix has been very well received as a cattle feed additive.
SECOND CHANCES |
Recyclers in many parts of the country have had a familiar lament throughout this decade with its tight labor market: Filling positions with reliable people has been tough to do. Tony McCarthy of recycler FMS Inc., Clearwater, Fla., acknowledges the same problem. “It can be difficult to find people who really want to work,” he comments. One employee has been with Tony almost since 2002, but many other employees have come and gone, he admits. One labor source Tony has tapped into is prison inmates who are part of a work program. “The workers I have through the state work release program are good,” says Tony. He notes that part of the reason is mandatory: “They’re not allowed to be disrespectful on the job.” But Tony is also hopeful that such employees can take advantage of a second chance that he is ready to offer. “There is at least one employee who is looking forward to going full-steam with me; it’s a neat thing to watch,” says Tony. “I treat anybody like I would like to be treated. When any of the work release employees want to continue to work for me, I hope I can make it happen.” |
"Cattle love it; they can drink a 6,000-gallon shipment in about two days," says Tony. Donating the sweet byproduct to cattle ranches does not yield a sale price, but it does save on disposal and avoids any environmental hazards of too much sugar entering the water supply.
The cattle feed market is just one of several that FMS has discovered or helped cultivate. It turns out that bees are fond of excess cola syrup product, providing a nectar that can be purchased by honey producers for their beekeeping swarms.
Additionally, a local company has the ability to filter the beverage output into clean water, a commodity for which there is a ready market during the summer when Tampa Bay area businesses and home owners are striving to keep their lawns green.
The success of the system has not been kept under wraps and is spreading beyond the Tampa Bay region. Since the 2005 Tampa Pepsi installation, Tony has been in contact with bottlers in several other regional markets, including in Orlando, where Tony and FMS are hard at work replicating and building on the services they provide for Tampa Pepsi.
The Orlando contract has prompted FMS to purchase a new truck so it can service the five distribution centers operated by the Orlando Pepsi bottler. The centers, which will be equipped with their own balers, are located in Orlando as well as in Atlantic coast markets to the east.
Bottlers in Jacksonville, the Carolinas and Georgia are also showing interest in identical or similar systems. "The people at Tampa Pepsi love the system they have, that’s why they have urged bottlers in other cities to do the same thing," he remarks.
In Clearwater, FMS recently moved to a larger 23,500-square-foot facility to make room for its in-house beverage processing systems, nearly doubling its working space. Product is brought to the plant in 53-foot containers that are dropped off at a variety of customer sites.
"In my old plant, visitors were pretty amazed with what we could do with 12,500 square feet," says Tony. "We often had three semi-trailers coming in per day."
MORE VALUE ADDED. Although the canned and bottled beverage systems have been the leading niche for FMS, Tony says the company is not a one-trick pony.
It continues to handle a wide variety of drums and other types of packaging or scrap generated at bottling plants and by other customers. The company takes in small plastic pallets (such as the ones that hold four or six two-liter bottles), some plastic "skeleton" scrap generated by a nearby medical device manufacturer, as well as cardboard and other more common materials.
Another niche venture involves recycling stainless steel CO2 and beverage syrup canisters (used in retail applications). The canisters have molded rubber parts that are firmly affixed to them, presenting a separation challenge. But, working with an equipment supplier, Tony says he has helped design a machine to remove the rubber tops, and will soon start in on recycling two trailers full of the canisters.
Customers who handle bottled coffee drinks and other products packaged in glass are providing one more recycling stream for FMS. The company will soon take delivery on glass processing equipment that will allow it to produce clean cullet that can be marketed to bottle makers.
The effort will result in new marketable materials, but finding end markets has not been a foremost challenge. In his company’s brief but fast-growing history, Tony has struck up good relationships with Chinese buyers of scrap materials, he says, as well as buyers representing other overseas and domestic consuming facilities.
As his volume of material has grown, so has the FMS transportation network, which now includes drivers, trucks and trailers that coordinate making other shipments with the pickup of scrap materials, which usually represents the backhaul opportunity.
The company’s reputation as a recycling problem-solver has attracted the attention of municipalities such as Dunedin, Fla. Tony is working with such communities to design and place compactor/containers at drop-off sites that can maximize the efficiency of drop-off programs by maximizing the weight of commodities that can be placed in a 53-foot trailer. "If you maximize the weights, it can make it worthwhile to pick a container up some 200 miles away," he comments.
The opportunities are many, to the point that a challenge for Tony and FMS lately has been to find the time and talent to take advantage of all the opportunities.
As the FMS beverage recycling system has caught on in new cities, Tony’s days are filled with travel, purchasing decisions and making sure the new FMS facility and new on-site installations are outfitted correctly.
"I’m actually shocked at how well it has gone," states Tony. "It’s hard to know exactly where I’m going because things are happening so fast."
The author is editor of Recycling Today and can be contacted at btaylor@gie.net.
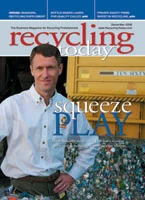
Explore the December 2006 Issue
Check out more from this issue and find your next story to read.
Latest from Recycling Today
- Nextek, Coveris to recycle food-grade plastic film
- Recyclekaro expands recycling capacity
- USTR hears comments on port fee proposal
- C&D World 2025 hits record attendance and exhibitor numbers
- Denali now offers mobile depackaging service
- Hyundai confirms Louisiana as EAF mill site
- ASCE sees infrastructure progress, but more to be done
- Global steel output tapers downward