Squaring belt ends with precision can lenghten the service life of conveyor belts and fasteners.
When splicing conveyor belts with mechanical fasteners, it is important to remember that accurate squaring of the belt ends before installing the splice is essential to belt performance. A squared splice contributes to longer service life for both belt and fasteners by helping the belt run or "track" in a smooth and straight manner.
Although a variety of causes contribute to off-tracking, one of the most common reasons for this problem -- and a major factor in premature splice failure -- is that the spliced belt ends were not cut straight or square to begin with. When installed on improperly squared belt ends, the splice creates an uneven tension along the joint, causing the belt to move or jerk laterally.
Signs of this condition can include ragged, stringy, chewed-up belt edges or ripped belting resulting from the belt edges scraping against skirtboards and ironwork. In severe cases, fastener pullout or uneven top-plate wear can result from uneven tension distribution along the splice. Poor belt tracking can cause loads to shift from belt center to belt edge, resulting in spillage.
Belt-end squaring is easy, excellent preventive maintenance. Two methods explained here -- the first, currently recommended by the National Industrial Belting Association -- can provide accurate results.
STANDARD METHOD
Before doing anything else, lock off the power line switch to the conveyor. Never attempt to work on the belt or splice without doing this first.
If the work involves new belting with smooth, straight edges, it may be sufficient to simply reference one end of a steel carpenter’s square along the belt edge. With worn belting, however, edge wear and damage usually make this method inaccurate.
To avoid faulty measurements caused by worn belt edges, it is best to establish the average centerline of the belt and use this line as the reference for squaring. Note that unless the belt is already on the ground, measuring and marking on flat belts are best done while the belt is still taut and under tension, before clamping and slacking the section to be spliced. If the section to be spliced is troughed, the belt should be slackened and supported from underneath with boards or plywood to allow it to lie flat during the measuring steps.
To establish the average centerline (Fig. 1), measure across the belt, edge to edge, using chalk or pencil to mark a number of center points -- or close clusters of two or three points each -- at intervals of three to five feet along the belt, extending back as much as 15 to 20 feet if possible from each
belt end. Shorter distances may lessen the accuracy of this squaring procedure.
Laying a straight-edge or chalkline along these points, determine and mark an average centerline (Fig. 2). If working alone, you can tie one of the chalklines to a nail driven through the belt. Just remember to remove the nail afterwards.
With your steel square referenced against this centerline at the point where the belt is to be cut (Fig. 3), draw two lines, one out to each belt edge from the centerline. These naturally join at the center to form a single line across the belt.
Before cutting, sight along the line from either belt edge to confirm that the combined lines appear straight as they cross the belt. Sighted from a low angle, even a slight misalignment will be clearly visible as a bend occurring at the center of the belt.
GEOMETRIC APPROACH
Even without a square, you can produce accurate results with simple geometry. This method actually is more precise than the square method above, but may require more time to perform.
First, find and mark the centerline as described above (Figs. 1-2). At the point where you want the belt end to be cut (Fig. 4), measure out from the centerline towards both belt edges and mark a short line (two or three inches long) parallel to the centerline, close to each edge; make sure these lines (Lines B and C) are equal distances from the centerline.
At a distance from the belt and equal to at least three times the belt width, drive a small nail into the belt on the centerline (Fig. 5). Using this nail as a pivot for holding the end of a steel tape, string or chalk line, swing an arc across Lines B and C, marking the belt where this arc cuts across
Lines B and C. These marks then will be equal distances from the centerline.
Align a steel rule between these intersecting points (Fig. 6); this line will be precisely square with the centerline. Cut the belt along this line to create a squared belt end.
Thus squared, the newly-cut belt end should make it easy to install a straight, properly-aligned splice. Be aware, however, that belting can be difficult — even dagerous — to cut. Several cutting tools are available to make the work easier and considerably safer.
For the quickest, easiest and most accurate results, advanced chain-drive belt cutters permit one-pass cutting with virtually no resistance and enable safe, reliable operation even with rubber and PVC belts up to 60 inches wide and 3/4 inches thick. After proper end-squaring procedures, the user simply lifts the tool’s lock-down bar, inserts the belt across the cutter-blade track, aligns the belt and clamps it in place by lowering the lock-down bar. Turning a double-handled crank draws a twin-edge blade through the conveyor belt. Chain-drive crank sys-tems significantly reduce the effort and time required to make a cut, allowing it to be done in one easy pass.
For added safety, some belt cutters feature a hold-down bar that can be secured in an open position to eliminate the need to manually hold it while aligning the belt over the cutter-blade track. For greater convenience, some hold-down bars can be completely detached in order to position the tool around continuous belts -- either new stock or belts already strung around conveyors -- before re-assembling and cutting.
Heavier-duty belts, those as large as 1 9/16-inch thick, can be accurately and safely cut with hand-drawn cutters that feature adjustable double-edged blades. The tool’s base is securely interlocked with a stainless steel track, along which the user slides the cutter head across the belt width. After each pass, the blade is progressively lowered until the belt is completely severed. For belts up to 1 9/16-inch thick, extra long blades may be installed in this type of cutter.
With squared and straight-cut ends, mechanically spliced belts run more smoothly, which increases splice and belt life and reduces maintenance problems that can result from off-tracking.
Consider this additional splice maintenance tip: after completing the splice installation, carve the date into the belt cover alongside the splice (special tools are available for this). Next time this splice needs a replacement, you’ll know how long that splice lasted. Over time, you’ll establish an average lifespan for your splices. Then, if you notice that splices on a particular belt are failing prematurely, it probably is a signal that something else -- such as pulleys or bearings -- needs checking or maintenance.
The author is product manager for Flexible Steel Lacing Co., Downer’s Grove, Ill.
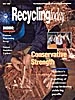
Explore the May 1995 Issue
Check out more from this issue and find your next story to read.
Latest from Recycling Today
- ReMA board to consider changes to residential dual-, single-stream MRF specifications
- Trump’s ‘liberation day’ results in retaliatory tariffs
- Commentary: Waste, CPG industries must lean into data to make sustainable packaging a reality
- DPI acquires Concept Plastics Co.
- Stadler develops second Republic Services Polymer Center
- Japanese scrap can feed its EAF sector, study finds
- IRG cancels plans for Pennsylvania PRF
- WIH Resource Group celebrates 20th anniversary