China’s hunger for copper scrap throughout this decade has caused U.S. companies operating wire chopping lines to compete much harder to secure material to run through their processing lines.
In the wire chopping market, the intense global competition for copper feedstock can run in contrast with what is often a nearly non-existent market for the PVC or other types of plastic cable used to coat the wire scrap.
Throw into this mix a demand for aluminum scrap that is stable but not as global or volatile as what has been occurring with copper, and operators of wire chopping lines are presented with several considerations before deciding how (or whether) to make the investment to purchase copper wire and aluminum cable and the automated equipment used to produce high-grade copper and aluminum chops.
MONEY IN METAL
Since starting up its wire chopping operations in 1968, Mallin Brothers Co. Inc., Kansas City, Mo., has seen China become a more consistent competitor in search of material. "The market dynamics have become more global, and the Far East markets are a much more consistent competitor," says Jeffrey Mallin, president of Mallin Brothers.
"When the Chinese first entered the market, they were not consistent buyers," he comments. "They would buy and then leave the market for lengths of time. We had a competitive advantage because we were always buying, no matter what the market conditions." Adds Mallin, "Foreign [buyers] are now very much in the market and have created new challenges and opportunities for domestic wire processors."
Mallin Brothers also makes an effort to keep its finished copper chops within the domestic market. "We feel it is very important to support the manufacturing base in this country," Mallin says. "That is where most of our scrap is generated."
Mallin Brothers sources its incoming wire from wire manufacturers, utilities, electrical contractors and domestic scrap dealers, processing No. 1 and No. 2 insulated copper wire, insulated aluminum wire, ACSR (steel reinforced) and URD (concentric cable) wire.
American Electronics Recycling (AER), Sarasota, Fla., installed a wire chopping line at its facility to maximize the value of the wire it receives with the electronic scrap the company processes, according to AER President Trip Alford.
AER produces a No. 2 copper chop, primarily, from its stream of electronic devices, though the company also sources additional wire to process that can result in a No. 1 chop, Alford says.
"We are always looking for insulated copper wire to run through the machine to augment what we are doing," he says. "It allows us to move loads more quickly."
AER also prefers to sell its finished copper to the domestic market, Alford says.
The company runs all of its copper wire though its shredding system first before sending it onto the wire chopping line. "People that don’t have a shredder would handle it a lot differently," Alford says.
At Mallin Brothers, where wire chopping makes up 80 percent of the company’s business, the company employs three wire chopping lines made up of equipment from several manufacturers. "We have had great success with Triple S Dynamics granulators, MTB equipment and various other equipment," Mallin says.
Recently, Mallin Brothers added expanded capacity to one of its lines that was scheduled to come online in September. The company is also engineering additional capacity for a second line, according to Mallin.
Copper and aluminum chops have enjoyed healthy demand, though demand for copper has been somewhat inconsistent compared to that of aluminum, Mallin says. "Copper demand is good, not great." He adds that it is more challenging to find domestic markets that give the company an advantage over global markets.
"Demand for aluminum choppings has been solid and steady all year," he adds.
Mallin says he is optimistic that demand will remain strong into 2009. "We are fortunate that our product has a market more diversified than most scrap streams," he adds.
The strength of markets going forward rests on the strength of the U.S. dollar, Alford says, noting that the weaker dollar works in favor of U.S. industry. He predicts the market will be weaker through the balance of 2008 and into the first quarter of 2009.
"I hope things get better, but hope doesn’t always float the ship," Alford says.
AND THEN THERE’S PLASTIC
SPEAKING THE LANGUAGE |
Dealers, traders and recyclers who ship and process scrap cable and wire have a number of terms to get to know in the course of doing business. The 2007 version of the Scrap Specifications Circular managed by the Institute of Scrap Recycling Industries Inc. (ISRI) contains several such terms, including: • Barley and Berry - Forms of No. 1 copper wire; • Birch – No. 2 copper wire; • Druid – Insulated copper wire; • Talon – New pure aluminum wire and cable; • Tann – New mixed aluminum wire and cable; • Tassel – Old mixed aluminum wire and cable; and • Twang – Insulated aluminum wire scrap. Other wire-related terms include Clove, Cobra and Cocoa, which are all forms of copper wire nodules. Each of the grades is defined more fully in the ISRI Circular, often with pertinent information as to the size and purity of the material if it is to be traded under the suggested name. Those seeking a copy of the full ISRI Scrap Specifications Circular can go to www.isri.org and click on the "Specs and Markets" button on the menu on the left-hand side of the home page. |
The value proposition for wire choppers in North America has always rested upon securing the copper and aluminum within.
Recyclers by nature, however, hate to send anything to the landfill, and even before plastic started climbing in value attempts to find end markets had been consistent.
One source of hope for insulated wire processors lies with IntegriCo Composites of Temple, Texas.
According to Chris Brough, vice president of engineering and product development with the company, IntegriCo has developed a composite railroad tie that is able to use aluminum and copper wire chop residue as a feedstock.
Speaking at the Institute of Scrap Recycling Industries Inc. (ISRI) Commodities Roundtable Forum in mid-September, Brough described how his company’s composite railroad ties are making headway in a market that consumes some 20 million such pieces of lumber each year.
IntegriCo has targeted what Brough calls "landfill-bound plastic waste streams" as a feedstock, using a manufacturing process that can handle mixed plastics even with their different melt temperatures and other chemistry differences. "Yes, we can take your cross-linked polyethylene," Brough told scrap recyclers in attendance.
Although IntegriCo’s process can handle such scrap in theory, Brough acknowledged that the company’s current hunger for such material is not large enough to absorb what wire choppers produce. "We’ve got more than we can use right now," he commented. "Our demand is filled."
But should IntegriCo either gain greater railroad market share or begin manufacturing other products, such as shipping pallets, using this same process, it will provide a needed outlet for wire chopping line operators who wish to help develop an end market.
"Our technology is fairly flexible, and we can take materials that others can’t handle," Brough says. He noted that many of the consuming markets for recycled plastic require material that is free not only of metal, paint or other non-plastic contaminants, but that must also be uniform in its chemistry and even its color.
Even the IntegriCo buyers like a certain amount of consistency, however, and they’ve been disappointed when a recycler ships a load that is a drastically different mix of chopped coatings compared to what arrived from that same recycler the month before.
IntegriCo, just like scrap recyclers themselves, prefers to see wire chopping systems that thoroughly separate metal from plastic. Scrap recyclers wish to capture the valuable metal, and IntegriCo would rather not have the metal in its plastic as a contaminant. "We’re all on the same page," Brough says.
Should IntegriCo continue to accept plastic chops (and Brough acknowledged that scrap recyclers "have heard this before" when it comes to an end market for this plastic), the inroad into this end market is likely to be welcomed by wire chopping line operators.
The authors are editor in chief and managing editor of Recycling Today and can be contacted at btaylor@gie.net and dtoto@gie.net.
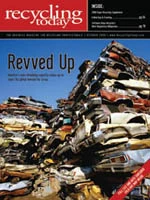
Explore the October 2008 Issue
Check out more from this issue and find your next story to read.
Latest from Recycling Today
- CP Group announces new senior vice president
- APR publishes Design Guide in French
- AmSty recorded first sales of PolyRenew Styrene in 2024
- PRE says EU’s plastic recycling industry at a breaking point
- Call2Recycle Canada, Staples Professional expand partnership
- Circular Services breaks ground on north Texas MRF
- Tariff uncertainty results in choppy nonferrous scrap flows
- CATL, Ellen MacArthur Foundation establish battery partnership