Booming markets for secondary commodities have kept not only recyclers busy throughout the middle part of this decade, but also many of the equipment makers who supply them.
Makers of shredders and downstream sorting equipment in particular have seen an influx of orders stemming from scrap recyclers’ investments in installing powerful and finely tuned shredding plants to handle the obsolete scrap stream.
Scrap recyclers who have seen their revenue streams change because of
THIS JUST IN Even as the October issue of Recycling Today goes to press, additional investments in shredding capacity and technology are being announced. OmniSource Corp., Fort Wayne, Ind., has announced plans to invest approximately $9 million to replace its existing shredding operation at its Toledo scrap processing and metal shredding facility. The investment will use "the latest state-of-the-art technology to increase the recovery of recyclable metals [to] produce a high-quality shredded steel product used as feedstock for regional steel producers," the company announced in a news release. An elected official from Toledo’s home county has welcomed the investment by OmniSource. "On behalf of Lucas County, I’m happy to see that OmniSource will be keeping good-paying jobs here in our community and upgrading their facility to remain competitive in the long term," says Lucas County Commissioner Pete Gerken. "This commitment is a win for our residents and a win for economic development in our region." OmniSource notes that "the new shredder will position OmniSource to remain regionally competitive and retain approximately 50 union and salaried positions within the city of Toledo."
higher per-ton and per-pound pricing are almost uniformly taking measures to re-invest a healthy portion of their profits into equipment that can harvest the maximum amount of metal possible.
"Management is committed to technological upgrades to further improve metallic and plastics yields from our shredder waste streams," says the CEO of one of the world’s largest scrap recycling companies, Jeremy Sutcliffe of Sims Group Ltd., in remarks accompanying the firm’s more recent quarterly results.
LARGE OR SMALL. A review of shredder installation projects from the past two years demonstrates a range of investment decisions, with plants both large and small appearing across the recycling landscape.Super-sized shredders with rotors more than 100 inches wide have been a popular choice, especially by larger companies as well as mid-sized companies operating in larger metropolitan regions.
Installations of this magnitude include the placement of 130 Heavy Shredders offered by Wendt Corp. at scrap yards located in Indiana and New Jersey.
Wendt Corp. refers to the 130 Heavy Shredder as the largest shredder model on the market. The shredder now in place at Sturgis Iron & Metal in Elkhart, Ind., features an 8,000-hp motor and can process 400 tons of material per hour, according to Tom Wendt, executive vice president of Wendt Corp, Tonawanda, N.Y.
Metal Management Inc., based in Chicago, has selected the 130 Heavy Shredder as the replacement model it’s having installed at its Newark, N.J., location. The mammoth shredder will be powered by a 9,000-hp motor.
At the Institute of Scrap Recycling Industries Inc. (ISRI) 2007 Convention & Exhibition, Metal Management’s Matthew Parker, a director of ferrous trading based at the company’s Newark location, noted that by his company’s count there were now as many as 39 super-sized shredders with larger rotors and the ability to shred through as much as 60,000 tons per month of scrap. "We’re going to produce more shredded scrap, and we are going to be able to sell it," he said of his own company’s position on shredding capacity.
Other shredder manufacturers are also selling plants from the upper end of their model range, such as Canutillo, Texas-based The Shredder Co.’s sale of a 120 SHD shredder to Chaparral Steel in Midlothian, Texas, or the sale of large units from Harris Waste Management, Peachtree City, Ga., to recyclers located in North Carolina and Alabama.
Not all new shredders are at the upper end of the size range, however. Many companies dipping their toes into the shredding waters for the first time are selecting smaller models, either to accommodate the level of investment they can afford or to better match the requirements of a less densely populated geographic market.
American Pulverizer Co., St. Louis, is a shredder manufacturer that has had particular success selling plants with 60-to-80-inch rotors to small and medium-sized scrap recyclers often located in small and medium-sized markets.
The company’s Skip Anthony says "We listened to the mid-sized scrap dealers express a need to shred and developed these machines to process from 2,500 to 5,000 tons per month of automobiles and scrap just like the big boys."
American Pulverizer has sold smaller shredders to customers such as Clayton County Recycling in Iowa and Rubino Brothers in Stamford, Conn., that are suitable for these companies either because of their rural location, in the case of Clayton County Recycling, or because of the small footprint of an urban scrap yard, in the case of Rubino Brothers.
Mid-sized shredding plants, with rotors in the 80-inch range, are also being sold, with one recent example being the decision by Industrial Services of America Inc. (ISA), Louisville, Ky., to purchase a mid-sized shredder.
In June, ISA announced its decision to purchase a TSC 80 SXS shredding plant from The Shredder Co. "to process many types of heavy grades that it is presently processing with a shear and to make specialty shredder grades for specific consumers," according to a company news release.
Whether purchasing replacement units or setting up a greenfield shredding site, the demand from scrap recyclers for shredders has challenged equipment makers to continue producing sturdy machines to chew through the nation’s scrap.
Increasingly, these same recyclers are paying attention not just to the volume of scrap they can shred each day, but also to maximizing their recovery rates so that metal does not slip through as residue.
CHASING EVERY OUNCE. The dollars being invested in shredding capacity are being doubled up by many recyclers on sorting equipment and systems for the back portion of the shredding system.The economics of $3-per-pound copper and at times dizzying prices for nickel, aluminum and other nonferrous metals, as well, has changed the economics of investing in nonferrous sorting and separating technology.
Just as shredding equipment makers have successfully convinced scrap recyclers to invest in newer and better models, so too have makers of drum magnets, eddy currents, induction sorters and innovative new machines being deployed for the first time.
SGM Magnetics has notched several high-profile sales in 2007, including units to Metal Management Inc., Sims Group, PSC Metals, Carolinas Recycling Group, Atlantic Iron & Metal, Joseph Behr & Sons, Gershow Recycling, Newell Recycling of El Paso and Rensselaer Iron & Metal.
Other downstream equipment providers have also announced sales, often of multiple units. One such example involves the placement of three Steinert eddy currents and an induction sorting system at the Shredded Products LLC yard in Rocky Mount, Va.
Calculations by scrap recyclers are showing that money invested in equipment that can capture even tiny pieces of metal and even a low single-digit percentage of the total shredded stream can quickly pay for itself.
"The whole goal in our business is to recover metal units," says one recycler in the southern United States. "If 1 percent of your metal goes to the landfill, that’s material that you’ve paid for [across the scale] that you’re not able to sell."
In recent markets, that ability to harvest and sell has involved a different set of numbers, as nonferrous scrap consumers are willing to pay more per pound, and overseas consumers, in particular, are willing to purchase grades extracted from the post-shredder stream.
A news release from Wendt Corp. announcing two recent downstream equipment sales notes that scrap recycler E. Kingsford Iron & Metal in Michigan "chose Wendt Corp. to assist with designing and implementing a nonferrous recovery plant to increase revenue as well as reduce landfill costs."
Similarly, Bayside Recycling, based in Duluth, Minn., selected its Wendt equipment "to assist with designing and implementing a nonferrous recovery plant that will significantly increase revenue as well as reduce landfill costs," according to a Wendt Corp. release.
Recyclers have demonstrated a willingness to respond quickly to changing markets, with shredder operators in particular willing to put their money behind the concept of capturing as much metal as technology allows.
DUSTING OFF. With shredding plants humming along throughout North America, another set of suppliers to the industry is asking plant operators to consider one of the side effects of the shredding process.Dust Control Technologies, Peoria, Ill., has recently worked with Adams Steel in California to examine and address the dust control aspects of the company’s shredding plants.
After nearly 30 years in the business, George Adams has developed first-hand experience regarding what it takes to be an environmentally responsible partner in the community. His company is now operating as SA Recycling LLC, a joint venture between Adams Steel and the Sims Group Ltd., offering metal recycling services from a network of 27 locations that serve California, Arizona, Nevada and Mexico.
"All of our operations are designed to use the latest control technologies to help us meet the highest standards of environmental health and safety," says Adams. "That includes protecting the ecology as well as our employees."
The company’s Anaheim location includes one of the super-sized shredders in the market, the 124 SXS from The Shredder Co. The plant features a double feed roller system weighing more than 70,000 pounds and driven by a 7,000-hp motor. With programmable logic controllers, touch-screen monitors and real-time data feedback, the "smart" shredder is designed for rapid, consistent decision making and one of the lowest per-unit costs of any comparable equipment.
Like many of the new shredder plants on the market, the 124 SXS uses a computer-controlled water-injection system for initial dust control, which also helps eliminate excess heat and reduce any possibility of explosion. "Damp shredding is part of the dust-control equation," says Adams. "But we’ve found that the outflow dries fairly quickly, especially in hot weather. So we needed something more to keep the particulates down, especially when we are loading the shredder [residue] into trucks." The giant shredder can process about 230 tons of scrap per hour, or more than three rail cars or trucks per minute.
After reviewing several available options, Adams decided on a high-volume system from Dust Control Technologies, Peoria, Ill. "We run the Dust Boss whenever we’re loading or moving material," says Adams. "There’s one at the Anaheim facility and another at our Terminal Island location."
The Dust Boss DB-60 is a high-volume, ducted fan dust suppressor mounted on a movable carriage. The design generates 30,000 CFM (cubic feet per minute) of forced air, using a 25-hp fan motor rated at a service factor of 1.3 for reliability and longevity. The oscillating unit blankets as much as 21,000 square feet with a fine mist of water droplets that are atomized to 50-200 microns in size. With an adjustable throw angle from 0 to 50 degrees elevation and 40 degrees of oscillation, the unit has a range of up to 210 feet, providing SA Recycling operators with significant coverage of the loading area.
"The droplet size is critical to effective suppression," explains Dust Control Technologies President Edwin Peterson. "Fugitive dust particles tend to be quite small, so the water should be atomized to droplets near that same size for maximum attraction. The nozzles and fan must be designed to work together for optimum flow, spray angle and delivery pressure to achieve the droplet size, velocity and distribution needed."
The DB-60 also incorporates a 10-hp booster pump for extending water pressure by as much as 150 psi. Fed by a 1.5-inch quick-disconnect hose, the unit requires just 10 psi of constant pressure to supply 30 specially designed brass nozzles. At a boosted pressure of 200 psi, it uses about 15-30 gpm (global precipitation measurement). The manufacturer offers an optional dosing pump that can be used to meter in surfactants for superior particle capture or odor control additives. The DB-60 and the smaller DB-30 can be outfitted for potable or non-potable water sources.
"These units have been a great help in trapping dust which might otherwise make its way into the air," Adams concludes. "In fact, we’ve ordered two more machines to be delivered this year for other facilities."
The author is editor in chief of Recycling Today and can be contacted at btaylor@gie.net. Additional reporting was also done by Rick Felde on behalf of Dust Control Technology for the last portion of the feature.
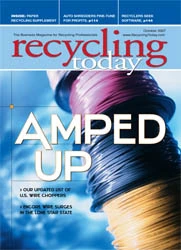
Explore the October 2007 Issue
Check out more from this issue and find your next story to read.
Latest from Recycling Today
- Sortera Technologies ‘owning and operating’ aluminum sorting solutions
- IDTechEx sees electric-powered construction equipment growth
- Global steel output recedes in November
- Fitch Ratings sees reasons for steel optimism in 2025
- P+PB adds new board members
- BlueScope, BHP & Rio Tinto select site for electric smelting furnace pilot plant
- Magnomer joins Canada Plastics Pact
- Out of touch with reality